Read carefully the case study entitled Wilkerson Company and answer the following questions.? How does Wilkersons existing cost system o
Read carefully the case study entitled Wilkerson Company and answer the following questions.
- How does Wilkerson’s existing cost system operate? Develop a diagram to show how costs flow from factory expense accounts to products.
- Develop and diagram an activity-based cost model using the information in the case. Provide your best estimates about the cost and profitability of Wilkerson’s three product lines. What difference does your cost assign- ment have on reported product costs and profitability? What causes any shifts in cost and profitability?
- Based on your analysis for question 2, what actions might Wilkerson’s management team consider to improve the company’s profitability?
Assignment for the case study
Wilkerson Company
Prof. Mario Milone
Read carefully the case study entitled Wilkerson Company and answer the following questions.
1. How does Wilkerson’s existing cost system operate? Develop a diagram to show how costs flow from factory expense accounts to products.
2. Develop and diagram an activity-based cost model using the information in the case. Provide your best estimates about the cost and profitability of Wilkerson’s three product lines. What difference does your cost assign- ment have on reported product costs and profitability? What causes any shifts in cost and profitability?
3. Based on your analysis for question 2, what actions might Wilkerson’s management team consider to improve the company’s profitability?
1
,
Copyright
Wilkerson Co. |
Harvard Business School Case #101-092 |
Case Software #XLS007 |
Copyright © 2010 President and Fellows of Harvard College. No part of this product may be reproduced, stored in a retrieval system or transmitted in any form or by any means—electronic, mechanical, photocopying, recording or otherwise—without the permission of Harvard Business School. |
Exhibit 1
Exhibit 1 Wilkerson Company: Operating Results (March 2000) | ||||
Sales | $2,152,500 | 100% | ||
Direct Labor Expense | 271,250 | |||
Direct Materials Expense | 458,000 | |||
Manufacturing overhead | ||||
Machine-related expenses | $336,000 | |||
Setup labor | 40,000 | |||
Receiving and production control | 180,000 | |||
Engineering | 100,000 | |||
Packaging and shipping | 150,000 | |||
Total Manufacturing Overhead | 806,000 | |||
Gross Margin | $617,250 | 29% | ||
General, Selling & Admin. Expense | 559,650 | |||
Operating Income (pre-tax) | $57,600 | 3% |
Exhibit 2
Exhibit 2 Product Profitability Analysis (March 2000) | |||
Valves | Pumps | Flow Controllers | |
Direct labor cost | $10.00 | $12.50 | $10.00 |
Direct material cost | 16.00 | 20.00 | 22.00 |
Manufacturing overhead (@300%) | 30.00 | 37.50 | 30.00 |
Standard unit costs | $56.00 | $70.00 | $62.00 |
Target selling price | $86.15 | $107.69 | $95.38 |
Planned gross margin (%) | 35% | 35% | 35% |
Actual selling price | $86.00 | $87.00 | $105.00 |
Actual gross margin (%) | 34.90% | 19.50% | 41.00% |
Exhibit 3
Exhibit 3 Product Data | |||
Product Lines | Valves | Pumps | Flow Controllers |
Materials per unit | 4 components | 5 components | 10 components |
2 @ $2 = $ 4 | 3 @ $2 = $ 6 | 4 @ $1 = $ 4 | |
2 @ 6 = 12 | 2 @ 7 = 14 | 5 @ 2 = 10 | |
1 @ 8 = 8 | |||
Materials cost per unit | $16 | $20 | $22 |
Direct labor per unit | .40 DL hours | .50 DL hours | .40 DL hours |
Direct labor $/unit @ $25/DL hour | $10 | $12.50 | $10.00 |
(including employee benefits) | |||
Machine hours per unit | 0.5 | 0.5 | 0.3 |
Exhibit 4
Exhibit 4 Monthly Production and Operating Statistics (March 2000) | ||||
Valves | Pumps | Flow Controllers | Total | |
Production (units) | 7,500 | 12,500 | 4,000 | 24,000 |
Machine hours | 3,750 | 6,250 | 1,200 | 11,200 |
Production runs | 10 | 50 | 100 | 160 |
Number of shipments | 10 | 70 | 220 | 300 |
Hours of engineering work | 250 | 375 | 625 | 1,250 |
,
9 – 1 0 1 – 0 9 2 R E V : A U G U S T 5 , 2 0 0 3
________________________________________________________________________________________________________________ Professor Robert S. Kaplan wrote this updated version of “Destin Brass Products Co.,” HBS No. 190-089, prepared by Professor William J. Bruns, Jr. HBS cases are developed solely as the basis for class discussion. Cases are not intended to serve as endorsements, sources of primary data, or illustrations of effective or ineffective management. Copyright © 2001 President and Fellows of Harvard College. To order copies or request permission to reproduce materials, call 1-800-545-7685, write Harvard Business School Publishing, Boston, MA 02163, or go to http://www.hbsp.harvard.edu. No part of this publication may be reproduced, stored in a retrieval system, used in a spreadsheet, or transmitted in any form or by any means—electronic, mechanical, photocopying, recording, or otherwise—without the permission of Harvard Business School.
R O B E R T S . K A P L A N
Wilkerson Company
The decline in our profits has become intolerable. The severe price cutting in pumps has dropped our pre-tax margin to less than 3%, far below our historical 10% margins. Fortunately, our competitors are overlooking the opportunities for profit in flow controllers. Our recent 10% price increase in that line has been implemented without losing any business.
Robert Parker, president of the Wilkerson Company, was discussing operating results in the latest month with Peggy Knight, his controller, and John Scott, his manufacturing manager. The meeting among the three was taking place in an atmosphere tinged with apprehension because competitors had been reducing prices on pumps, Wilkerson’s major product line. Since pumps were a commodity product, Parker had seen no alternative but to match the reduced prices to maintain volume. But the price cuts had led to declining company profits, especially in the pump line (summary operating results for the previous month, March 2000, are shown in Exhibits 1 and 2).
Wilkerson supplied products to manufacturers of water purification equipment. The company had started with a unique design for valves that it could produce to tolerances that were better than any in the industry. Parker quickly established a loyal customer base because of the high quality of its manufactured valves. He and Scott realized that Wilkerson’s existing labor skills and machining equipment could also be used to produce pumps and flow controllers, products that were also purchased by its customers. They soon established a major presence in the high-volume pump product line and the more customized flow controller line.
Wilkerson’s production process started with the purchase of semi-finished components from several suppliers. It machined these parts to the required tolerances and assembled them in the company's modern manufacturing facility. The same equipment and labor were used for all three product lines, and production runs were scheduled to match customer shipping requirements. Suppliers and customers had agreed to just-in-time deliveries, and products were packed and shipped as completed.
Valves were produced by assembling four different machined components. Scott had designed machines that held components in fixtures so that they could be machined automatically. The valves were standard products and could be produced and shipped in large lots. Although Scott felt several competitors could now match Parker's quality in valves, none had tried to gain market share by cutting price, and gross margins had been maintained at a standard 35%.
This document is authorized for use by Yize Yuan, from 03/14/2022 to 06/10/2022 in the course: SP22 MGTF495-76905: Special Topic in Accounting: Strategic Cost Management & New Technologies (Milone) – MF22, University of California, San Diego
Any unauthorized use or reproduction of this document is strictly prohibited.
101-092 Wilkerson Company
2
The manufacturing process for pumps was practically identical to that for valves. Five components were machined and then assembled into the final product. The pumps were shipped to industrial product distributors after assembly. Recently, it seemed as if each month brought new reports of reduced prices for pumps. Wilkerson had matched the lower prices so that it would not give up its place as a major pump supplier. Gross margins on pump sales in the latest month had fallen below 20%, well below the company's planned gross margin of 35%.
Flow controllers were devices that controlled the rate and direction of flow of chemicals. They required more components and more labor, than pumps or valves, for each finished unit. Also, there was much more variety in the types of flow controllers used in industry, so many more production runs and shipments were performed for this product line than for valves. Wilkerson had recently raised flow controller prices by more than 10% with no apparent effect on demand.
Wilkerson had always used a simple cost accounting system. Each unit of product was charged for direct material and labor cost. Material cost was based on the prices paid for components under annual purchasing agreements. Labor rates, including fringe benefits, were $25 per hour, and were charged to products based on the standard run times for each product (see Exhibit 3). The company had only one producing department, in which components were both machined and assembled into finished products. The overhead costs in this department were allocated to products as a percentage of production-run direct labor cost. Currently, the rate was 300%. Since direct labor cost had to be recorded anyway to prepare factory payroll, this was an inexpensive way to allocate overhead costs to products.
Knight noted that some companies didn’t allocate any overhead costs to products, treating them as period, not product, expenses. For these companies, product profitability was measured at the contribution margin level ! price less all variable costs. Wilkerson’s variable costs were only its direct material and direct labor costs. On that basis, all products, including pumps, would be generating substantial contribution to overhead and profits. She thought that perhaps some of Wilkerson’s competitors were following this procedure and pricing to cover variable costs.
Knight had recently led a small task force to study Wilkerson’s overhead costs since they had now become much larger than the direct labor expenses. The study had revealed the following information:
1. Workers often operated several of the machines simultaneously once they were set up. For other operations, however, workers could operate only one machine. Thus machine-related expenses might relate more to the machine hours of a product than to its production-run labor hours.
2. A set-up had to be performed each time a batch of components had to be machined in a production run. Each component in a product required a separate production run to machine the raw materials or purchased part to the specifications for the product.
3. People in the receiving and production control departments ordered, processed, inspected, and moved each batch of components for a production run. This work required about the same amount of time whether the components were for a long or a short production run, or whether the components were expensive or inexpensive.
4. The work in the packaging and shipping area had increased during the past couple of years as Wilkerson increased the number of customers it served. Each time products were packaged and shipped, about the same amount of work was required, regardless of the number of items in the shipment.
This document is authorized for use by Yize Yuan, from 03/14/2022 to 06/10/2022 in the course: SP22 MGTF495-76905: Special Topic in Accounting: Strategic Cost Management & New Technologies (Milone) – MF22, University of California, San Diego
Any unauthorized use or reproduction of this document is strictly prohibited.
Wilkerson Company 101-092
3
Knight’s team had collected the data shown in Exhibit 4 based on operations in March 2000. The team felt that this month was typical of ongoing operations. Some people recalled, however, that when demand was really heavy last year, the machines had worked 12,000 hours in a month and the factory handled up to 180 production runs and 400 shipments without experiencing any production delays or use of overtime.
Exhibit 1 Wilkerson Company: Operating Results (March 2000)
Sales $2,152,500 100% Direct Labor Expense 271,250 Direct Materials Expense 458,000 Manufacturing overhead
Machine-related expenses $336,000 Setup labor 40,000 Receiving and production control 180,000 Engineering 100,000 Packaging and shipping 150,000
Total Manufacturing Overhead 806,000 Gross Margin $617,250 29% General, Selling & Admin. Expense 559,650 Operating Income (pre-tax) $ 57,600 3%
This document is authorized for use by Yize Yuan, from 03/14/2022 to 06/10/2022 in the course: SP22 MGTF495-76905: Special Topic in Accounting: Strategic Cost Management & New Technologies (Milone) – MF22, University of California, San Diego
Any unauthorized use or reproduction of this document is strictly prohibited.
101-092 Wilkerson Company
4
Exhibit 2 Product Profitability Analysis (March 2000)
Valves Pumps Flow Controllers Direct labor cost Direct material cost Manufacturing overhead (@300%) Standard unit costs
$10.00 16.00 30.00
$56.00
$12.50 20.00 37.50
$ 70.00
$10.00 22.00 30.00
$ 62.00
Target selling price $86.15 $107.69 $95.38 Planned gross margin (%) 35% 35% 35%
Actual selling price $86.00 $87.00 $105.00 Actual gross margin (%) 34.9% 19.5% 41.0%
Exhibit 3 Product Data
Product Lines Valves Pumps Flow Controllers Materials per unit 4 components
2 @ $2 = $ 4 2 @ 6 = 12 __________
5 components 3 @ $2 = $ 6 2 @ 7 = 14 __________
10 components 4 @ $1 = $ 4 5 @ 2 = 10 1 @ 8 = 8
Materials cost per unit $16 $20 $22 Direct labor per unit .40 DL hours .50 DL hours .40 DL hours Direct labor $/unit @ $25/DL hour (including employee benefits)
$10 $12.50 $10.00
Machine hours per unit 0.5 0.5 0.3
Exhibit 4 Monthly Production and Operating Statistics (March 2000)
Flow Valves Pumps Controllers Total Production (units) 7,500 12,500 4,000 24,000 Machine hours 3,750 6,250 1,200 11,200 Production runs 10 50 100 160 Number of shipments 10 70 220 300 Hours of engineering work 250 375 625 1,250
This document is authorized for use by Yize Yuan, from 03/14/2022 to 06/10/2022 in the course: SP22 MGTF495-76905: Special Topic in Accounting: Strategic Cost Management & New Technologies (Milone) – MF22, University of California, San Diego
Any unauthorized use or reproduction of this document is strictly prohibited.
Collepals.com Plagiarism Free Papers
Are you looking for custom essay writing service or even dissertation writing services? Just request for our write my paper service, and we'll match you with the best essay writer in your subject! With an exceptional team of professional academic experts in a wide range of subjects, we can guarantee you an unrivaled quality of custom-written papers.
Get ZERO PLAGIARISM, HUMAN WRITTEN ESSAYS
Why Hire Collepals.com writers to do your paper?
Quality- We are experienced and have access to ample research materials.
We write plagiarism Free Content
Confidential- We never share or sell your personal information to third parties.
Support-Chat with us today! We are always waiting to answer all your questions.
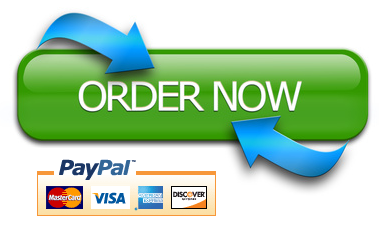