Why do Manufacturing Companies focus on Lean Thinking? What is meant by the term overproduction? Why do you think this has been described as the biggest waste of all?
Learning Outcome:
1. Demonstrate a deep understanding of the logistic function concepts and theories as well as supply chain management strategies. (Lo.1.1)
2. Demonstrate the ability to understand complex issues pertaining to supply chain integration and strategic supply chain partnership (Lo 1.2).
3. Apply essential elements of core logistic and supply chain management principles. (Lo 2.1)
Critical Thinking
The purpose of this assignment is to identify and apply Logistics and Supply Chain Management concepts/tools to suggest logistics performance priorities.
Use the Saudi digital Library (SDL) search engine.
Search Title: THE BENEFITS OF LEAN MANUFACTURING what lean thinking offers the process Industries
Authors Name: Melton,T
Source: In 7th World Congress of Chemical Engineering, Chemical Engineering Research and Design June 2005 83(6):662-673
Read out the research paper carefully and based on your understanding you should answer the following questions.
Questions:
1. Why do Manufacturing Companies focus on Lean Thinking? (500 words)- (5Marks)
2. What is meant by the term overproduction? Why do you think this has been described as the biggest waste of all? (500 words)- (5Marks)
3. Assess the reasons for using lean thinking. What are the benefits of using lean thinking from Suppliers to end users? (500 words) -(5Marks)
· Reference should be included.
THE BENEFITS OF LEAN MANUFACTURING What Lean Thinking has to Offer the Process Industries
T. MELTON�
MIME Solutions Ltd, Chester, UK
H ow many people in the manufacturing industry can truly say that they have not heard of LEAN? Not many. Yet how many of these believe in lean, have implemented lean, are the passionate change agents who have convinced senior stakeholders
than lean is the way forward for their company? Less. Much Less. Lean is a revolution—it isn’t just about using tools, or changing a few steps in our manufacturing processes—it’s about the complete change of our businesses—how the supply chain operates, how the direc- tors direct, how the managers manage, how employees—people—go about their daily work. Everything. So what is this revolution, and how is it impacting the process industries? The background of lean thinking is based in the history of Japanese manufacturing techniques which have now been applied world-wide within many types of industry.
Keywords: lean manufacturing; waste; value; flow; value stream; bottleneck.
A BRIEF HISTORY OF ‘LEAN’
Mention ‘lean’ and most ‘lean thinkers’ will know that this is a reference to the lean production approach pioneered by Toyota but also the subject of The Machine that Changed the World (Womack et al., 1990); a book which first high- lighted Japanese production methods as compared to tra- ditional Western mass production systems; it also highlighted the superior performance of the former. The follow-on book, Lean Thinking: Banish Waste and Create Wealth in your Organisation (Womack and Jones, 1996), is equally a key step in the history of lean as it summarizes the lean principles which ‘guide action’. It also coined the phrase ‘Lean Production’.
But let’s go back to the beginning—the birth of lean was in Japan within Toyota in the 1940s: The Toyota Pro- duction System was based around the desire to produce in a continuous flow which did not rely on long production runs to be efficient; it was based around the recognition that only a small fraction of the total time and effort to process a product added value to the end customer. This was clearly the opposite of what the Western world was doing—here mass production based around materials resource planning (MRP) and complex computerized systems was developing alongside the mass production philosophies originally developed by Henry Ford, i.e., large high volume pro- duction of standardized products with minimal product changeovers.
Taiichi Ohno had started work on the Toyota Production system in the 1940s and continued it’s development into the late 1980s unhindered by the advancements in computers which had allowed mass production to be further ‘enhanced’ by MRP Systems. By the 1970s Toyota’s own supply base was ‘lean’; by the 1980s their distribution base was also ‘lean’.
Key tools and techniques within the ‘lean’ system, included:
. Kanban—a visual signal to support flow by ‘pulling’ pro- duct through the manufacturing process as required by the customer.
. 5 S’s—a visual housekeeping technique which devolved control to the shopfloor.
. Visual control—a method of measuring performance at the ‘shop floor’ which was visual and owned by the oper- ator team.
. Poke yoke—an ‘error-proofing’ technique.
. SMED (single minute exchange of dies)—a changeover reduction technique.
However let us return to the 1990s and the two landmark works discussed at the start of this section.
The Machine that Changed the World (Womack et al., 1990) compared and contrasted the Mass Production System seen in the US and Europe, with the Lean Production System, seen in Japan, within the automotive industry.
Table 1 is a summary of some of the comparisons high- lighted by Womack et al. (1990).
. The mass producers were able to maintain long pro- duction runs using standard designs which ensured that the customer got a lower cost; they also got less variety
�Correspondence to: Dr T. Melton, MIME Solutions Ltd, Gable Cottage, Childwall Farm, Kelsall Road, Kelsall, Chester, CH3 8NR, UK. E-mail: [email protected]
662
0263–8762/05/$30.00+0.00 # 2005 Institution of Chemical Engineers
www.icheme.org/journals Trans IChemE, Part A, June 2005 doi: 10.1205/cherd.04351 Chemical Engineering Research and Design, 83(A6): 662–673
as did the workforce who found this mode of operation tedious.
. In comparison, the term ‘lean’ comes from the ‘upside’ of the production method which requires ‘half the human effort, half the manufacturing space, half the investment and half the engineering hours to develop a new product in half the time’.
However, it is not difficult to see that the world of car-parts and conveyor belt production lines did not immediately grab the interest and excitement of the process industries. Apart from the packaging lines the analogies seemed hard to find.
However, Lean Thinking (Womack and Jones, 1996) helped us to understand the principles of lean:
. The identification of value.
. The elimination of waste.
. The generation of flow (of value to the customer).
It clearly demonstrated that this was not a philosophy or technique which was only applicable to the automotive industry.
THE BENEFITS OF BEING ‘LEAN’
The benefits seen within non-process industries (see Figure 1), such as the automotive industry, are well documented:
. decreased lead times for customers;
. reduced inventories for manufacturers;
. improved knowledge management;
. more robust processes (as measured by less errors and therefore less rework).
This makes lean a very real and physical concept— especially for manufacturing.
Lean production has now expanded and lean thinking has been applied to all aspects of the supply chain. There are many well documented examples of the application of ‘lean thinking’ to business processes such as project man- agement (Melton, 2003); construction, design, and so on.
Lean can be applied to all aspects of the supply chain and should be if the maximum benefits within the organization are to be sustainably realized. The two biggest problems with the application of lean to business processes are the perceived lack of tangible benefits and the view that many business processes are already efficient. Both assumptions can be challenged (Melton, 2004):
. There are many tangible benefits associated with lean business processes. A lean business process will be faster, e.g. the speed of response to a request for the business process will be faster, and as most business pro- cesses are linked to organizational supply chains, then this can deliver significant financial benefits to a company.
. The perception that a business process is already efficient is all too often an illusion. Functionally, many business processes may appear very efficient, however the appli- cation of Lean Thinking forces us to review the whole supply chain in which the business process sits, and this frequently reveals bottlenecks and pockets of inefficiency.
But for now let us return to the world of manufacturing within the process industries.
WHAT’S STOPPING US?
With the benefits so apparently obvious the question has to be—what’s stopping us?
For some in the process industries the answer is simple— nothing! There are good examples of the implementation of lean philosophies across the process industries. For example, PICME (Process Industries Centre for Manufac- turing Excellence), an organization part funded by the DTI to specifically help manufacturing in the process industries to become more efficient and more competitive, quote estimated projected savings of over £75 million over their first 5 years of operation (PICME, 2004).
Table 1. Production Systems Compared.
Mass production Lean production
Basis † Henry Ford † Toyota
People–design † Narrowly skilled professionals † Teams of multi-skilled workers at all levels in the organization
People–production † Unskilled or semi-skilled workers † Teams of multi-skilled workers at all levels in the organization
Equipment † Expensive, single-purpose machines † Manual and automated systems which can produce large volumes with large product variety
Production methods † Make high volumes of standardized products † Make products which the customer has ordered
Organizational philosophy † Hierarchical—management take responsibility † Value streams using appropriate levels of empowerment— pushing responsibility further down the organization
Philosophy † Aim for ‘good enough’ † Aim for perfection
Figure 1. The benefits of ‘lean’.
Trans IChemE, Part A, Chemical Engineering Research and Design, 2005, 83(A6): 662–673
THE BENEFITS OF LEAN MANUFACTURING 663
But for some the ‘case for change’ cannot be as compel- ling as it would appear to be. Figure 2 is a force field dia- gram which shows some of the drivers and resistors within the manufacturing sector of the process industries; it is only when the specific driving forces for an organization are greater than the opposing forces that the change will occur. The ultimate sustainability then requires additional supporting forces to further reduce and eliminate opposition.
Within the process industries specific sectors have been under increasing pressure:
. Chemical Industry—the continuing pressure on the cost base.
. Pharmaceutical manufacturing—the pressure on the supply chain has increased as there are more external competitive pressures for manufacturers to deliver new, safe efficacious drugs quicker than ever before.
But—lean manufacturing has now been applied within the pharmaceutical sector both within primary and secondary operations and the use within the wider process indus- tries is increasingly likely as the breadth of benefits are demonstrated and the driving forces for change increase.
Lean thinkers would probably want an additional driving force for change: lean is easy to implement! But although the principles and tools associated with lean thinking may appear at face value an easy concept to use within an apparently willing industry they present huge ‘change’ challenges to any business truly wishing to become lean.
Perhaps the biggest resisting force for the process industries will be the huge inertia that must be overcome: the resist- ance to change.
Lean thinking involves a serious challenge to the status quo and for many this level of challenge to the ‘way we do things round here’ is a sufficient deterrent to appli- cation—particularly after the surge of business changes implemented following initiatives seemingly aiming for a similar goal—greater business effectiveness and therefore profit! However it can be demonstrated that the forces supporting the application of lean are greater than those resisting it.
WHAT IS LEAN THINKING?
Lean Thinking starts with the customer and the definition of value. Therefore, as a manufacturing process is a vehicle to deliver value (a product) to a customer, the principles of lean thinking should be applicable to the Process Industries and the specific manufacturing processes within that industry.
We can remove waste from many steps of our manufac- turing processes, from how we develop the initial product and process design, how we assure compliance, to how we design to operate a completed facility. However, to be truly lean we have to link all these elements within a robust supply chain—we need to ensure the flow of value. This leads to what many are calling a ‘lean enterprise’ (LERC, 2004).
Figure 2. The forces opposing and driving a change to ‘lean’.
Trans IChemE, Part A, Chemical Engineering Research and Design, 2005, 83(A6): 662–673
664 MELTON
The Lean Enterprise Research Centre (LERC, 2004) at Cardiff Business School highlighted that for most pro- duction operations:
. 5% of activities add value;
. 35% are necessary non-value activities;
. 60% add no value at all.
Therefore, there is no doubt that the elimination of waste represents a huge potential in terms of manufacturing improvements—the key is to:
. identify both waste and value;
. develop our knowledge management base;
. realize that sustainable improvement requires the buy in of the people operating the processes and managing the business, and therefore a culture of continuous improvement.
Value
The identification of value and the definition of value propositions for specific customers is the starting point. Without a robust understanding of what the customer values you cannot move forwards (see Table 2). Outside of the process industries there are many examples of what we mean by a ‘value proposition’—as a consumer buying a washing machine what we value may be the abil- ity to wash our clothes at home; for others the value may be related to cost or specific design features or even the colour. The challenge for the manufacturer is to develop a product portfolio based on these value propositions.
Table 2 gives some examples of value propositions which manufacturers in the process industries have developed as related to their specific customer group, their product portfolio and their potential capabilities.
For customer A, development of the process they hand- over to the toll manufacturer is a value added activity; for customer B this would be considered waste.
Waste
Any activity in a process which does not add value to the customer is called ‘waste’. Sometimes the waste is a necessary part of the process and adds value to the com- pany and this cannot be eliminated, e.g., financial controls.
Otherwise all ‘Muda’, as the Japanese call waste, should be eliminated.
There are seven main types of waste as outlined in Figure 3 and further detailed in Table 3.
Initially, waste can be easily identified in all processes and early changes can reap huge savings. As the processes continually improve, the waste reduction will be more incremental as the company strives to achieve a waste- free process. Continuous improvement is at the core of lean thinking.
The data in Table 3 is only the tip of the iceberg in terms of the amount and types of waste which will be within our manufacturing processes and overall supply chains. The key is to identify it, i.e., to ensure that the root cause— the real waste—is eliminated, not just the symptom.
Flow
Flow is probably the hardest lean concept to understand. It is the concept which most obviously contradicts with mass production systems; the comparison of one piece flow versus batch and queue processes.
It is a lack of flow in our manufacturing processes which accounts for the huge warehouses which house the mass of inventory which consumes the working capital of the business.
To understand flow you need to understand the concept of the value stream—that linkage of events or activities which ultimately delivers value to a customer. A value stream crosses functional and, usually, organizational boundaries.
Figure 4 shows a simple value stream which would be typical for a toll manufacturer. The value stream does not show all the supporting activities, only the main value adding stages and the key multi-functional teams involved.
Flow is concerned with processes, people and culture and it is appropriate at this stage to mention the work of Goldratt and Cox (1993) who’s book The Goal introduced
Figure 3. The seven types of waste.
Table 2. Examples of value propositions within the process industries.
Customer type Value proposition Manufacturer type
A. Major pharmaceutical manufacturer of drug products
† Robust process and product development at fast track speed ensuring regulatory compliance
† Toll manufacturer of pharmaceutical intermediates
B. Other manufacturer in a low cost base industry
† Correct specification, low cost and delivered on time in the volumes specified
† Bulk chemicals manufacturer
C. The patient (via the companies who distribute the drugs)
† High quality, safe drugs that ‘work’ at an appropriate price
† Major pharmaceutical manufacturer of drug products
Trans IChemE, Part A, Chemical Engineering Research and Design, 2005, 83(A6): 662–673
THE BENEFITS OF LEAN MANUFACTURING 665
the Theory of Constraints. This theory aligns with lean thinking in the way it considers an organization as a system consisting of resources which are connected by pro- cesses which ultimately make product which can be sold.
It effectively talks about a value stream and the main causes for the lack of flow—constraints in the system.
Godratt and Cox (1993) introduced some development of operational rules to guide how a production plant should be operated based on three measurements:
. Throughput: the rate at which the system generates money through sales (use sales not production—if you produce something, but do not sell it, it is not through- put)—this links into the lean philosophy of producing product when the customer ‘pulls’ for it.
. Inventory: all the money that the system has invested in purchasing things which it intends to sell.
. Operational expense: all the money the system spends in order to turn inventory into throughput.
They then define the goal of that production operation as increasing throughput while simultaneously reducing both inventory and operating expense and that any plant improvement must be challenged against this, i.e.,
. as a result of this improvement will we: — Sell any more products? (Did Throughput go up?) — Reduce the amount of raw materials or overtime?
(Did Operating Expense go down?) — Reduce the plant Inventory?
Table 3. The seven types of waste.
Type of waste Description Within the process industry Example symptom
1. Over production
† Product made for no specific customer
† Development of a product, a process or a manufacturing facility for no additional value
† Large campaign—large batch and continuous large-scale manufacturing processes
† Development of alternative process routes which are not used or the development of processes which do not support the bottleneck
† Redesign of parts of the manufacturing facility which are ‘standard’, e.g., reactors
† The extent of warehouse space needed and used
† Development and production organization imbalance
† An ever changing process (tweaked) † Large engineering costs/time
associated with facility modifications
2. Waiting † As people, equipment or product waits to be processed it is not adding any value to the customer
† Storage tanks acting as product buffers in the manufacturing process—waiting to be processed by the next step
† Intermediate product which cannot leave site until lab tests and paperwork are complete
† The large amount of ‘work in progress’ held up in the manufacturing process—often seen on the balance sheet and as ‘piles of inventory’ around the site
3. Transport † Moving the product to several locations
† Whilst the product is in motion it is not being processed and therefore not adding value to the customer
† Raw materials are made in several locations and transported to one site where a bulk intermediate is made. This is then transported to another site for final product processing
† Packaging for customer use may be at a separate site
† Movement of pallets of intermediate product around a site or between sites
† Large warehousing and continual movement of intermediate material on and off site rather than final product
4. Inventory † Storage of products, intermediates, raw materials, and so on, all costs money
† Economically large batches of raw material are purchased for large campaigns and sit in the warehouse for extended periods
† Queued batches of intermediate material may require specific warehousing or segregation especially if the lab analysis is yet to be completed or confirmed
† Large buffer stocks within a manufacturing facility and also large warehousing on the site; financially seen as a huge use of working capital
5. Over processing
† When a particular process step does not add value to the product
† A cautious approach to the design of unit operations can extend processing times and can include steps, such as hold or testing, which add no value
† The duplication of any steps related to the supply chain process, e.g., sampling, checking
† The reaction stage is typically complete within minutes yet we continue to process for hours or days
† We have in process controls which never show a failure
† The delay of documents to accompany finished product
6. Motion † The excessive movement of the people who operate the manufacturing facility is wasteful. Whilst they are in motion they cannot support the processing of the product
† Excessive movement of data, decisions and information
† People transporting samples or documentation
† People required to move work in progress to and from the warehouse
† People required to meet with other people to confirm key decisions in the supply chain process
† People entering key data into MRP systems
† Large teams of operators moving to and from the manufacturing unit but less activity actually within the unit
† Data entry being seen as a problem within MRP systems
7. Defects † Errors during the process— either requiring re-work or additional work
† Material out of specification; batch documentation incomplete
† Data and data entry errors † General miscommunication
† Missed or late orders † Excessive overtime † Increased operating costs
Trans IChemE, Part A, Chemical Engineering Research and Design, 2005, 83(A6): 662–673
666 MELTON
The final concept they introduce is that of the bottleneck—that step in a process which determines the throughput of the whole process. This also aligns with lean ‘pull’ production which tells production that it’s OK to stop production! (if there is no customer ‘pull’).
Within the process industries we do strive for pro- duction efficiencies, however, ‘a value stream perspective means working on the big picture, not just individual processes, and improving the whole, not just optimising the parts’ (Rother and Shook, 1999). In other words we need to improve the efficiency and effectiveness of the whole supply chain not just improve one part of it and we need to operate the supply chain not the pro- duction unit.
Figure 5 summarizes the above discussion on flow by demonstrating how a part of a supply chain could operate
if ‘pulled’ rather than ‘pushed’. In a ‘push’ system pro- duction works as much as it can to fill a warehouse; In a ‘pull’ system production works only when it needs to at the pull of customer orders.
Figure 5 demonstrates that the process (the grey boxes) only operates when an appropriate ‘signal’ is seen:
. The packaging operation only operates when it is packa- ging for a customer order (it’s ‘signal to pack’). It takes product from a final product silo (kanban).
. When the level in the silo falls past the red line this is a signal for the final product manufacture to commence. Once the silo is at the green level this is a signal for the manufacture to stop. This operation takes its material from the raw materials kanban and the intermediate kanban.
Figure 4. A simple value stream.
Figure 5. ‘Pull’ production example—using kanbans.
Trans IChemE, Part A, Chemical Engineering Research and Design, 2005, 83(A6): 662–673
THE BENEFITS OF LEAN MANUFACTURING 667
. Both of these are storage areas. Specific kegs are placed on a coloured floor. When enough kegs have been used so that the red area of the floor can be seen—this is a signal for the preceding operation to commence, i.e., intermediate manufacture or purchasing of raw materials.
The sizing of the kanbans and their operation to ensure FIFO (first in-first out) has to be thought through but this can be an effective method of:
. Implementing a ‘pull’ production system.
. Reducing lead-time to the customer.
. Reducing inventory at all stages in a process.
Knowledge Management
The knowledge we have in our systems and more impor- tantly, our people, is fundamental to the implementation of lean.
The success of lean in some manufacturing organizations has been in part due to the reorganization of the teams at both operational and management level.
Example changes are:
. reorganization of all resources around value streams;
. multi-skilled or cross-functional teams with more responsibility for the day to day operation of a manufac- turing unit.
Additionally, formally capturing knowledge of processes is necessary especially within a work environment where cor- porate knowledge is no longer defined by the large numbers of employees who have worked there all their lives. Some
companies have used some form of IT solution to capture knowledge formally; for others a process of knowledge sharing spreads the knowledge wider than previously. A well-managed knowledge base is critical to the sustainabil- ity of change.
Continuous Improvement
Lean thinkers are aiming for ‘perfection’ and in doing so the improvement cycle is never ending. For many in the process industries this culture change is the hardest change of all.
However, for assured sustainability the organizations who are truly lean will invest the time and effort to support a change in culture—the way we do things around here. The case study attempts to highlight some of the ways in which culture can be impacted.
HOW TO START ‘LEAN THINKING’
A data-rational, structured approach is needed if the key principles of value, waste and flow are to be rigorously applied along the supply chain.
The process of ‘how to lean’ (Figure 6) can be summar- ized as:
. Document current process performance—how do we do it now.
. Define value and then eliminate waste.
. Identify undesirable effects and determine their root cause in order to find the real problem.
Figure 6. How to ‘lean’.
Trans IChemE, Part A, Chemical Engineering Research and Design, 2005, 83(A6): 662–673
668 MELTON
. Solve the problem and re-design the process.
. Test and demonstrate that value is now flowing to the customer of that process.
There are many tools and techniques to support each step in the above process—they support implementation of the principles.
Table 4 shows a sample of the tools a ‘lean thinker’ would have in their toolkit. What surprises many skeptics is that the lean principles can be put into action using tools which are very familiar to those who have been involved in performance improvements.
What is different is the fact t
Collepals.com Plagiarism Free Papers
Are you looking for custom essay writing service or even dissertation writing services? Just request for our write my paper service, and we'll match you with the best essay writer in your subject! With an exceptional team of professional academic experts in a wide range of subjects, we can guarantee you an unrivaled quality of custom-written papers.
Get ZERO PLAGIARISM, HUMAN WRITTEN ESSAYS
Why Hire Collepals.com writers to do your paper?
Quality- We are experienced and have access to ample research materials.
We write plagiarism Free Content
Confidential- We never share or sell your personal information to third parties.
Support-Chat with us today! We are always waiting to answer all your questions.
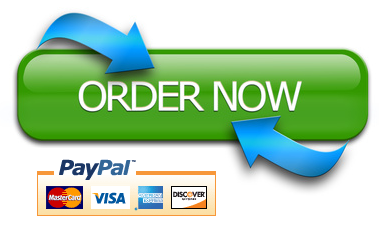