Structure, Organization, Ease of reading, Grammar: 3 Points This Assignment had a very, very specific structure.? Identify 2-4 issues.? Come up with solutions for those issues and summa
Structure, Organization, Ease of reading, Grammar: 3 Points
- This Assignment had a very, very specific structure. Identify 2-4 issues. Come up with solutions for those issues and summarize them briefly. Provide a table with Pros and Cons for each, use a weighted table to rank the solutions and select the best to implment, and wrap it all up with an overall (but brief) recommendation – what could have been done to help prevent this disaster from a PM perspective. DID YOU FOLLOW THIS STRUCTURE?
- Did you follow the advice given in the lectures and From Your Instructor about the format?
- Did you follow rules of English grammar, spelling, and syntax? Did you fix errors pointed out via Word’s editing capabilities (e.g. squiggly blue or red underlined text)?
Content: 10 Points
- Is it clear from reading your assignment that you read the case and understood what happened that led up to the mistakes that were made and that yielded the fires and explosions?
- Did you ‘dig deeper’? Some people identify very technical issues – did you find the underlying reasoning – the project-level thinking that may have driven decisions to go a certain way technically?
- Did you keep your writing concise and to the point? Part of the intent of this assignment is an exercise in expressing important ideas in as efficient a way as possible.
- Was there a logical flow from your Issue Identification to your Proposed Solutions, to your Pros and Cons and to your conclusion?
- Did you create a weighted table (see example) to compare the proposed the solutions in terms of ease of implmentation and effectiveness?
- If you did have ‘extra’ information to exhibit, did you put it in an Appendix rather than in the body of the text? Again, the focus is on a concise, crisp presentation of your arguments.
References and resources: 2 Points
- Did you provide several relevant references that helped make your points? Of course you can use the main Case as a reference, but did you reach out and find out more about the Columbia Gas incident from other sources? You really should at least investigate the references pointed to at the bottom of this Case at a minimum.
Other things to consider:
- Did you add value from your own professional and/or personal experience?
- Did you make appropriate use of figures and tables in an appendix? Don't substitute quantity for quality here – one good, relevant, and meaningful small table is worth 100 randomly inserted graphs and charts.
- Did you really take on the viewpoint of a project leader here, and consider the way the team was motivated, the way the different stakeholders communicated (or didn’t), the culture of the different companies?
- Did you consider the different stakeholder interests?
Merrimack Valley Gas Explosions Case Study
(REDACTED)
Executive Summary
On September 13, 2018, excessive pressure in natural gas lines owned by Columbia Gas
caused a series of explosions and fires in Massachusetts's Merrimack Valley region. The system
over-pressure ultimately damaged 131 structures, hospitalized 21 individuals, and killed one
person. (National Transportation Safety Board, 2019) Columbia Gas of Massachusetts did not
offer any advisories, and police and firefighters were doing a better job evacuating people from
their homes. It ultimately left thousands of households displaced without heat or the ability to
cook for months and bankrupted Columbia Gas of Massachusetts.
Although the accident can be attributed – on face value – to technical errors, these errors
shine a light on more profound organizational complacency within Columbia Gas, not the least
of which involve a gap in good project management practice and responsibility. A thorough
investigation conducted by the NTSB provided many technical recommendations to Columbia
Gas. To protect against future disasters, however, changes must be made from the project
management perspective. The three top identified top issues are cost-cutting in safety efforts,
lack of coordination internally and with local governments, and a culture of complacency.
I will discuss how these three major issues led to the subsequent disaster, solutions, pros
and cons, and these two overall recommendations: adding safety to the performance criterion
for project managers and developing a precise emergency plan with routine drills.
Background
On September 13, 2018, excessive pressure in natural gas lines owned by Columbia Gas
caused a series of explosions and fires in Massachusetts's Merrimack Valley region. The system
over-pressure ultimately damaged 131 structures, hospitalized 21 individuals, and killed one
person. (National Transportation Safety Board, 2019) Columbia Gas of Massachusetts failed to
proactively communicate with the local population. The people of Merrimack Valley were
getting their news instead from the local law enforcement agencies. This disaster ultimately left
thousands of households displaced without heat or the ability to cook for months and bankrupted
Columbia Gas of Massachusetts.
The disaster's technical causes could be traced back to replacing aging cast iron gas pipes
with polyethylene pipes. Contractors followed the work package that Columbia gas developed
and approved. The contractors removed a length of pipe without the very important step of
disconnecting a pressure sensor that was still attached to the removed pipe section. The pressure
sensor began reading a pressure drop that opened valves in the gas network until they were open
completely. Alarms were triggered at NiSource, Columbia's parent company, in Ohio. However,
they had no remote control of the valves and could only respond in person, and by the time the
valves were shut and brought back in control, the damage had already been done. (Maltzman,
2020)
Although seemingly technical in nature, this disaster points to multiple systemic issues
linked to project managers' failures and top management at Columbia Gas. The three issues
discussed in this paper are cost-cutting in safety efforts, lack of coordination internally and
with local governments, and a culture of complacency.
Issues Identification
Issue 1 – Cost Cutting in Safety Efforts
Ironically, the modernization project that set off the disaster was to replace the old pipes
with newer, safer, polyethylene pipes. However, the mitigation of risk through this
modernization created a secondary risk that revealed cost-cutting measures that made the process
unsafe. As it is cheaper to hire a contractor to replace the pipes, Columbia Gas outsourced labor
on this project. (Penn, 2019) By engaging a third party, Columbia Gas would have less oversight
over the project with contractors working on an unfamiliar system. Furthermore, Columbia Gas
typically had a technician from the Meter and Regulation Department assigned to the site to
manage the pressure readings. This practice was ended four years ago. (Penn, 2019) Columbia
Gas did not provide any reasons for ending the procedure, but it seems evident that it is a cost-
cutting measure, undertaken (in the author’s opinion) without proper consideration of the
downside.
However, even if Columbia Gas were directly working on the project, the accident may
have still happened. The NTSB investigation revealed the work package was signed off by an
engineer-in-training, not a licensed professional engineer. The office working on the project only
had two licensed engineers, and they only dealt with signing off on more extensive projects,
which this pipeline replacement was not (National Transportation Safety Board, 2019). This
seems to be a workflow process problem – something a project manager should consider.
Finally, there was a lack of documentation of the sensors resulting in them being
excluded from the work package. Had the engineers had the resources to review and provide that
information to the construction workers diligently, they would have accounted for the regulator
sensing lines.
Issue 2 – lack of coordination
Had the significant increase in gas pressure been detected and promptly acted upon, the
damage would have been significantly reduced. The first alarm that warned of high pressure
went off at 3:57 pm. It was not until 4:30 pm that technicians arrived at the first regulator station
to cut off the high-pressure gas flow – and not until 7 pm later that evening that the high gas
pressure was brought back in control. The NTSB investigation showed that Columbia Gas was
not prepared to respond to the emergency. Their emergency documents did not provide clear and
actionable steps for responding to this large-scale emergency event. (National Transportation
Safety Board, 2019). Although not per se related to this particular project, the project manager
could ‘step up’ and question why a particular project does not have these emergency steps.
Furthermore, information was not provided to municipal governments and emergency
first responders. The NiSource Emergency Manual states that when an over-pressurization of the
system occurs, there "may be a need" to communicate with local government officials and
emergency management agencies as well as fire and police departments. Had firefighters and
police been given the actionable information in a timely fashion, evacuations and precautions
could have begun. This communication could have potentially prevented multiple injuries and
the single death that occurred. Further, better communications could have prevented the
embarrassing situation of leaving the Twitter feed posting the company receiving a safety award
rather than providing the local population with vital, urgent information about the disaster as it
unfolded.
Issue 3 – lack of safety culture
Massachusetts Department of Public Utilities provided documentation on enforcement
action against Columbia gas for the preceding five years. Many of the incidents show a history of
improper maintenance, documentation, and inspection of their gas lines.
In Columbia Gas' pursuit of higher profit, minimum resources were placed into making
sure the gas lines they operated could be as safe as possible. A lack of safety culture also reveals
a culture of complacency. This culture can be seen in their lack of thorough risk assessment and
planning for emergency events. Investment into classes and exercises for their on-site engineers
would have also made the response less hectic and more unified.
Furthermore, had safety been a higher priority, the planning process would have included
a thorough check for safety issues. At the time, Massachusetts' state did not require a
professional engineer to sign off on the project plans. Columbia gas, therefore, did the bare
minimum to be following regulatory guidelines. Had also safety been taken into account during
their review and planning process for modernizing their gas lines, the potentially deadly issue of
over-pressure would have come up and been a more significant part of the review process for the
construction plans. Again, although this is not the specific role of the PM, the PM can and
should be the person to highlight these issues to management.
Proposed Solutions Table
Issues # – Solution # Solution
1-1 Re-invest in safety heavily. Create an executive-level office to
advocate for safety across the entire company's operation. Use this new
people's power to conduct a thorough review of engineering and
planning processes to refocus on safety.
1-2 Add safety as a performance target criterion to protect against
sacrificing quality over budget and time constraints.
1-3 Modify company policy concerning project planning and review so that
it goes above and beyond the regulatory requirements set forth by the
government.
2-1 Develop a precise and thorough emergency action plan that includes
Columbia Gas, local governments, and emergency first responders.
Make sure different monitoring stations are adequately staffed so that
no one person is entirely swamped when an emergency incident occurs.
2-2 Plan routine drills that practice potential emergencies. Make sure that
emergency first responders are included. Conduct reviews of these
drills to see if there are any improvements to be made
2-3 Conduct a review of how different departments and regional offices
communicate with each other. Create a communications plan that
allows information, especially in an emergency, to be communicated
timely.
3-1 Create a company-wide safety program that educates people on safety
practices and standards that must be respected. Also, put in place a
mechanism to make sure violations are dealt with transparently and
timely.
3-2 Make training classes for new hires, especially in the technical
department, mandatory.
3-3 Bring in new board members, executive-level hires with extensive
experience working in organizations that focus on safety. Such as the
NTSB or OSHA.
Pros and Cons Matrix
Solution Pros Cons
1-1: Create
executive-level
office overseeing
safety
Does not add to current
employee's responsibilities.
Dedicated teams can dig deeper
and provide more unbiased
recommendations.
It will take time to set
up.
Without strong
backing from board
members, may not
have enough influence
to provide long-
lasting change
1-2: Add safety as a
performance
criterion
Limit the pressure for project
managers to meet budget and
time constraints at the cost of
safety
Quality over cost constraints
There is a subjectivity
to how safety factors
in and can be
confusing for project
managers
1-3: Modify
company policy to
exceed regulatory
requirements
Columbia Gas becomes a leader
over a follower regarding safety
regulations.
Reduces the possibility that
Columbia Gas will be fined.
Increased margins
required may turn the
company to be less
competitive with other
companies that follow
the bare minimum
Takes increased time
before project start
2-1: develop a
precise emergency
plan
Reduces the need for the on-site
managers to make high-pressure
decisions in the moment
The plan could be too
rigid, leading to
secondary risks
2-2: Conduct
routine drills Make sure employees practice
the emergency plan.
Practice coordination with local
emergency first responders
Expensive and time-
consuming
May inadvertently
create more
complacency by
allowing people to
feel too comfortable
2-3: Review how
departments
communicate
within the company
Create pathways for company-
wide improvement that will
have long-term benefits for
safety and productivity
Would require drastic
changes to
communications
systems that could be
expensive or time-
consuming to
implement
3-1: Create a
safety-program Invests in future profits by
reducing costs for disaster
events
Will take time to
translate into
employees' attitude
3-2: Create training
classes for new
hires
Improve technical qualifications
within the team
Provide another perk for
employment
Costly and time
consuming to create
and complete
3-3: Bring on board
safety-oriented
board members and
executives
Enables new exchange of
information and practices
Changes may take
time to trickle down
to the whole company
Solutions Ranking Table (Top Solutions in green)
Solution Likelihood of
Success
Difficulty
Implementing
Solution
Score
Solution
Rank 1-5, 5 highest 1-5, 5 least difficult Likelihood of
success times
difficulty
Asdfad sdfasdaafa 4 2 8 3
Adfadfaafadfdfafadsfadsfasdf 5 5 25 1
Adfadsfasdfadfa 3 4 12 2
Adfafddfadfaf adfadsfadf asfasdf 5 5 25 1
Asdfafdadfadsfadf 5 5 25 1
adfadfa 3 1 3 6
Adffdaasdfaddadfaasdfadsfadsfasdf 5 1 5 5
asdfafd 4 2 8 3
adfafdadf 2 3 6 4
Recommendations
From the solutions ranking table above, we can see two stand-out solutions. They have a
high likelihood of success with low difficulty: adding safety to the performance criterion for
project managers and developing a precise emergency plan with routine drills. These are
incredibly urgent as there is no good emergency plan currently in place, and Columbia Gas
cannot sustain another mismanaged emergency, and of course the people of the Merrimack
Valley have had enough in terms of fires and explosions in and around their homes.
These aren’t the only changes – there are also more long-term changes, these changes
will be useful but will require significant resources and time before positive results appear. These
changes are necessary to reinstate their customers' trust in the company as one that safely
manages their natural gas. These changes include creating long term safety programs, more
comprehensive technical training, and making an executive-level office overseeing safety within
the company.
Lastly, a review of the company's communication and corporate culture will shed light on
where Columbia Gas has become complacent. This review is a massive undertaking but will
reveal safety downfalls and inefficient and redundant parts of the company to reorganize to bring
this ancient company forward into the more competitive landscape. These changes, prioritized
and implemented immediately, will significantly reduce any potential future disasters and
mismanagement.
References
Maltzman, R. (2020). Columbia Gas of Massachusetts – Project Issue Analysis – AD642
Individual Assignment 2. Boston.
National Transportation Safety Board. (2019). Overpressurization of Natural Gas Distribution
System, Explosions, and Fires in Merrimack Valley, Massachusetts, September 13, 2018.
Washington, DC: Pipeline Accident Report NTSB/PAR-19/02.
NiSource Inc. (2020, December 1). Home – NiSource. Retrieved from Nisource:
https://www.nisource.com/home
Penn, N. (2019, June 3). The Day the Town Blew Up – Andover Masssachusetts Gass Explosion.
Retrieved from Popular Mechanics:
https://www.popularmechanics.com/technology/infrastructure/a27309627/andover-gas-
explosion/
dfadsfafd adfadfadfafdadfadsfdfdsffds
dflkadsfjlasdfjlafdjldfjladsflasdfasdfasdfasdfasdfasdfdsafadsfdsafadsfadsfadsfadsfasfd
asdfadsfasdfadsfasdfafd
,
Columbia Gas of Massachusetts – Project Issue Analysis – AD642 Individual Assignment 2 ©2020 Richard Maltzman, Master Lecturer, Boston University Metropolitan College It was late in the afternoon of September 13, 2018. Professor Rich Maltzman looked up, startled, as three sharp raps on his car window interrupted the online course he was teaching from his car. Why from his car? Everyone in the town of Andover (Massachusetts, USA) had already been told to get out of their their homes, and they awaited word from the police – should they leave the town altogether? Yes! The three raps were from the Professor’s wife, and she was animatedly and urgently conveying the message: “we have to LEAVE TOWN. NOW!” The urgency was coming from the breaking story so well-summarized by the podcast series, “Fire in the Valley”. Fires and explosions were occurring in over 100 structures in the Merrimack Valley region of Massachusetts, north of Boston, in particular in the City of Lawrence and the towns of North Andover and Andover, Massachusetts, where the Professor and his family reside.
It was hard for residents to get the important details. Local news stations were covering the story, but the information was scattered and hard to decipher meaningfully. The Twitter feed from Columbia Gas of Massachusetts, the utility that operates the natural gas lines that were involved had this post on their web page for hours during the incident:
This was of little help – and if it wasn’t so sad, it would actually be funny. The local police were doing a better job posting advice and making announcements and sending out reverse 911 calls to residents. This is what triggered the raps on the windows and yielded the decision for Professor Maltzman to prematurely end his class, which ironically was about qualitative decision making. This tweet from the authorities made things much more clear:
So, the Professor and his family headed to Cape Cod to stay with relatives – they were very lucky to have this option available. Others were not so lucky. See this video from Rabbi Howard Mandell who tells his story, which starts with a 6- foot flame emanating from his boiler’s gas supply.
What happened here?
A tremendous write-up of the story comes from an article from the June, 2019 issue of Popular Mechanics – an article entitled, “The Day the Town Blew Up”.
Here the key extract:
…On the Salem Street side of the O’Connell South Common (in Lawrence, Massachusetts), a public park, a contractor removes a length of cast-iron pipe, caps it, and sets it aside.
Feeney Brothers Utility Services (“Providing Underground Utility Services since 1988”) has a permit to open up a two-foot-wide, 340-foot-long stretch of Salem Street, for the purpose of “completing gas main tie-ins and retirement of dual cast-iron gas mains.” Feeney Brothers is a family-owned operation with seven hundred employees. They’ve worked extensively not only for Columbia Gas but also for the region’s other major natural-gas supplier, Eversource. In recent years, gas utilities in Massachusetts have increasingly relied on contractors to carry out projects like this.
It’s usually cheaper.
The job today is to install new polyethylene pipeline and tie it into a new distribution main, also plastic. The Feeney Brothers contractor may or may not be aware that a regulator sensing line— a gauge that measures gas pressure—is attached to the pipe he had discarded. But it’s important to note that he and his crew are performing their duties as directed, under Columbia Gas supervision, and correctly following the steps in the work package Columbia Gas developed and approved. Columbia Gas’s work order doesn’t mention the sensor and was not prepared by a professional engineer. Until four years ago, a technician from the Meter and Regulation Department would have been assigned to the site to monitor pressure readings on the affected section of gas main, but Columbia Gas, for undisclosed reasons, has ended this practice.
The sensor on the discarded length of pipe thinks it’s still measuring the gas pressure in a vast underground network. In fact, it is measuring nothing: The pipe has been disconnected from the network. The sensor might as well be attached to a hot dog. But the sensor doesn’t know any of that, and there is no other sensor in this segment of the network to contradict it.
The sensor sends a message to the regulator valves in this segment of the network: Boost the pressure! Which they do. But the sensor, because it’s still attached to the dead piece of pipe,
doesn’t detect any of that. Instead, it registers a pressure drop, all the way down to 0.01 psi. More pressure, it tells the valves, until they have opened completely, and two distribution systems that were supposed to be segregated, cordoned off from each other, are instead tied directly into each other for twenty-six minutes.
A wave of high-pressure gas rushes into the regional gas-main system that serves Lawrence, Andover, and North Andover. In the older cast-iron segments of the network, the pressure rises to at least 6 psi, twelve times what the pipes are capable of handling.
At 4:04 p.m., the first high-pressure alarm is received by the NiSource monitoring station—in Columbus, Ohio. A second alarm is received at 4:05 p.m.
In the control room in Ohio, the NiSource employees have no capacity to control, let alone shut down, the gas flow. They can only contact the Meters and Regulations Group at Columbia Gas, which at 4:06 p.m. dispatches its entire team of inspectors to investigate—a total of two people, or approximately one per 2,494.75 miles of pipe.
The result of this over-pressurization: 141 fires, 5 explosions, 21 serious injuries, 1 death, many people displaced and/or without heat or the ability to cook – for months, and the bankruptcy of Columbia Gas of Massachusetts.
This was the incident. How about the cause?
The NTSB incident report summarized the case in the following way:
NTSB investigators learned that, until about 4 years ago, Columbia Gas required that a technician monitor any gas main revision work which required depressurizing the main. The technician—typically from the Meter and Regulation department—would use a gauge to monitor the pressure readings on the impacted main and would communicate directly with the crew making the change. If a pressure anomaly occurred, the technician could quickly act to prevent an overpressurization action. Columbia Gas offered no explanation as to why this procedure was phased out.
Although the Columbia Gas monitoring center in Columbus, Ohio, received high-pressure alarms and reported the event to the Meters and Regulations department two minutes after receiving the first alarm, there were no technicians prestaged or positioned to immediately close valves when the overpressurization occurred. Had Columbia Gas adequately performed MOC (Management of Change) and placed personnel at critical points along the system, Columbia Gas could have immediately addressed the issue and mitigated the consequences of the event. Therefore, the NTSB recommends that NiSource apply MOC processes to all changes to adequately identify system threats that could result in a common mode failure. Additionally, the NTSB recommends that NiSource develop and implement control procedures during modifications to gas mains to mitigate the risks identified during MOC operations. Gas main pressures should be continually monitored during these modifications and assets should be placed at critical locations to immediately shut down the system if abnormal operations are detected.
NTSB Recommendations In November 2018, the NTSB issued a series of “urgent” safety recommendations. The report contained four recommendations for NiSource, the parent company of Columbia Gas, and one for the state, seeking elimination of the professional engineer licensure exemption for public utility work and a requirement for a professional engineer’s seal on public utility engineering drawings.
The NTSB report recommends NiSource do the following:
• revise the engineering plan and constructibility review process across all subsidiaries; • review
Collepals.com Plagiarism Free Papers
Are you looking for custom essay writing service or even dissertation writing services? Just request for our write my paper service, and we'll match you with the best essay writer in your subject! With an exceptional team of professional academic experts in a wide range of subjects, we can guarantee you an unrivaled quality of custom-written papers.
Get ZERO PLAGIARISM, HUMAN WRITTEN ESSAYS
Why Hire Collepals.com writers to do your paper?
Quality- We are experienced and have access to ample research materials.
We write plagiarism Free Content
Confidential- We never share or sell your personal information to third parties.
Support-Chat with us today! We are always waiting to answer all your questions.
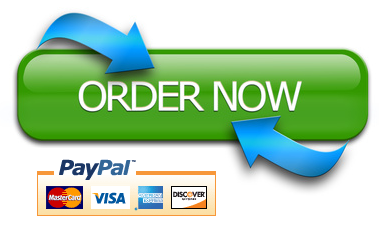