Applying Methods of Process Improvement to Improve Productivity
Applying Methods of Process Improvement to Improve Productivity Applying Methods of Process Improvement to Improve Productivity Consider the following scenario: Terry is a senior histology lab technician at a large urban hospital. He is responsible for overseeing a team of six junior technicians to process samples for testing. Recently, the hospital has introduced a new process whereby the senior histology lab technician must visually accept and approve the findings of the junior technicians in order for samples to be cleared and entered into the electronic health record for disease diagnosis. Terry has been able to meet this new need for the past few months. However, as more cases are entering the histology lab, cases have started to become backlogged. Additionally, the histology lab hours are restricted to business hours; this has severely impacted the processing of histology samples. Terry is worried that the approval process is not efficient and that perhaps a second senior histology lab technician should be hired to meet around-the-clock demand. As a current or future health care administrator, how might you address the productivity lag in the histology lab in the scenario? ORDER INSTRUCTIONS-COMPLIANT NURSING PAPERS For this Assignment, review Case 2, ?Noninvasive Cardiovascular Laboratory? in Chapter 8 of the text, Managing Health Services Organizations and Systems. Reflect on how you, as a current or future health care administrator, might be required to identify opportunities to improve productivity in an HSO. What types of information might you need to gather? How might you identify whether a process improvement opportunity exists? Then, review the Week 3 Case Questions document in this weeks Learning Resources to complete the Assignment. The Assignment (3-5 pages): ? Complete the case questions presented. ? Create a fish bone diagram and a flow diagram that represent an analysis of the processes for improvement and implementation approaches to support your answers to the case questions. ? Be sure to support your answers with support from the literature. Submit the Assignment by Day 7. ? BrainMass Inc. brainmass.com March 22, 2019, 3:41 am ad1c9bdddf https://brainmass.com/health-sciences/health-care-management/process-improvement-627605 Attachments Week 3 Assignment.docx Solution Preview Applying Methods of Process Improvement to Improve Productivity Consider the following scenario: Terry is a senior histology lab technician at a large urban hospital. He is responsible for overseeing a team of six junior technicians to process samples for testing. Recently, the hospital has introduced a new process whereby the senior histology lab technician must visually accept and approve the findings of the junior technicians in order for samples to be cleared and entered into the electronic health record for disease diagnosis. Terry has been able to meet this new need for the past few months. However, as more cases are entering the histology lab, cases have started to become backlogged. Additionally, the histology lab hours are restricted to business hours; this has severely impacted the processing of histology samples. Terry is worried that the approval process is not efficient and that perhaps a second senior histology lab technician should be hired to meet around-the-clock demand. As a current or future health care administrator, how might you address the productivity lag in the histology lab in the scenario? To address the productivity lag, the healthcare administrator must facilitate a flexible workflow process that is capable of ensuring that a smooth operation is conducted throughout the entire healthcare organization. The first question to ascertain by the healthcare administrator is whether the current process at the organization is in accordance with the healthcare needs and operational functions within the healthcare organization. There are several workflow processes that need to be understood, which require continuous information flows wherein the healthcare administrator needs to determine how the ? Applying Methods of Process Improvement to Improve Productivity Order Now
ADDITIONAL DETAILS
Methods of Process Improvement
Introduction
The methods of process improvement are a way for an organization to improve its processes so that it can create a better product. Each method has strengths and weaknesses, but together they can make your company be more efficient and responsive to customer needs.
Process analysis to identify bottlenecks and provide solutions for design problems
Process analysis is the process of identifying and analyzing a problem. It’s also the step before designing solutions for problems, which can be done in several ways.
-
Identify the problem: What’s going wrong? How bad is it?
-
Determine root cause: Why is there a problem at hand? Why does this specific thing happen so frequently? Is there something else that could be causing these issues, or are they all related to one overarching reason (e.g., customer service)?
-
Define scope and scope boundaries: What are we trying to improve here—the entire process or just part of it—and what will we need from you when working on those changes (e.g., data collection)?
Design of experiments to find the best combination of factors for a given application.
Design of experiments to find the best combination of factors for a given application.
The design of an experiment is a process that helps determine how many factors (or variables) are involved and what level of each factor should be used in the experiment. Factors can be anything from product features to customer demographics, so it’s important to determine which ones are most important for your particular application before running any experiments. Once you have decided on these factors, you can then select levels for each one by choosing whether or not you’d like them at different levels from high impact (e.g., low-price products) down through average impacts (e.g., high-price products). The next step is determining how much variation there will be between different combinations within each level—for example if one factor has three possible options while another has only two possible options with no overlap between them then it may make sense not try all three combinations but instead pick just two out of those three because they’ll have less variability among themselves than if we had done everything at once instead! Finally after deciding upon our level choices and sampling plan we need then run this new data set against existing knowledge about cost effectiveness in order to see what sort of conclusions we might draw from our findings.”
Lean manufacturing, which reduces inventory and increases efficiency
Lean manufacturing, which reduces inventory and increases efficiency, can help your business save money by reducing waste. Your customers will be happier with a product that arrives quickly and without hassle, so they’ll likely be willing to pay more for it.
This method also improves quality by eliminating wasteful steps in the production process. For example, if there’s no need to make two different types of widgets at once because they’re identical except for color or size (and therefore don’t need different tooling), then there’s less chance that one will go unproduced because of some oversight during assembly or testing—and thus less likelihood that you’ll end up with one extra widget sitting around in a warehouse somewhere as useless “inventory.”
Six Sigma, which is a discipline that uses statistical methods to eliminate defects and improve processes.
Six Sigma, which is a discipline that uses statistical methods to eliminate defects and improve processes.
Six Sigma uses a set of quality management principles and techniques. It also uses statistical methods to eliminate defects in products or services (such as product design), increase the accuracy of data collection, reduce variation in operations (including manufacturing), improve customer satisfaction by detecting problems before they occur and increasing efficiency by utilizing resources more effectively; it also helps organizations meet their strategic goals by reducing costs while meeting customer requirements
Total quality management, which builds quality into every aspect of operations, from product design to customer service.
Total quality management, which builds quality into every aspect of operations, from product design to customer service.
This philosophy emphasizes the importance of continuous improvement and personal involvement in decision making. TQM takes a systems approach to improving processes through teamwork and employee participation. It requires that employees are fully involved in all phases of production; they should be able to see where changes need to be made, why they’re needed, who makes them happen (i.e., management), who has responsibility for implementing those changes (i.e., leadership), how long it will take before implementation is complete (i.e., schedule), how much money it will cost per unit produced during this time period (i.e., cost), how many units will actually be produced during this time period once something goes wrong with one part or another…
Each method works individually or in combination with others.
Each method works individually or in combination with others. Some methods are more suitable for certain industries than others, but all methods have their strengths and weaknesses. It’s important to consider the context of your problem before deciding which method(s) you should use.
For example: If you’re working on a manufacturing plant that produces one product, then using Lean Six Sigma might be a good choice because it helps identify problems in your production process while they’re still small enough to fix. However, if you need help improving customer service from sales associates who aren’t trained well enough yet (and thus aren’t able to solve problems), then something like PDCA would probably work better for this type of situation by helping them improve over time rather than just fix one thing at once (which could lead back into bad habits).
Conclusion
The methods described above are just some of the ways that companies can improve processes. At the end of the day, it all depends on what you want to achieve and how much time and money you’re willing to invest in process improvement. You may want to try one method at first, then see if it works for your business before moving on to another type of technique.
Collepals.com Plagiarism Free Papers
Are you looking for custom essay writing service or even dissertation writing services? Just request for our write my paper service, and we'll match you with the best essay writer in your subject! With an exceptional team of professional academic experts in a wide range of subjects, we can guarantee you an unrivaled quality of custom-written papers.
Get ZERO PLAGIARISM, HUMAN WRITTEN ESSAYS
Why Hire Collepals.com writers to do your paper?
Quality- We are experienced and have access to ample research materials.
We write plagiarism Free Content
Confidential- We never share or sell your personal information to third parties.
Support-Chat with us today! We are always waiting to answer all your questions.
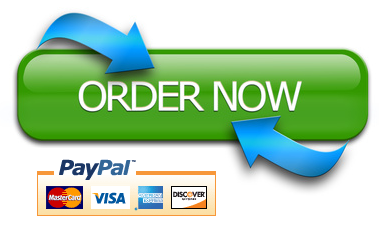