As the vice president of operations, you have noticed that your organization’s current operations strategy is not supporting the challenges that the organization is presently facing. In
Overview
Scenario
As the vice president of operations, you have noticed that your organization's current operations strategy is not supporting the challenges that the organization is presently facing. In order to maintain a competitive edge, you must address these challenges with your chief executive officer immediately.
Select an existing production organization. Analyze the organization's current vision, mission, business strategy, operation strategy, supply chain, total quality management, just-in-time philosophy, forecasting method, statistical technique, facility location, work design, project life cycle, and project management.
Note: As you collect the information for the first and second assignments, keep in mind that in the third assignment, you must prepare a presentation for your chief executive officer.
Instructions
Using the production organization you selected, write a 6-8 page paper in which you:
- Evaluate 2-4 weaknesses that are evident in the selected organization's product life cycle. Generate a new product design and product selection, and then determine three strategies that the organization needs in order to strengthen the operation. Provide support for the rationale.
- Determine the key components of supply chain management for the company you have selected. Determine three major issues that could affect the structuring, sourcing, purchasing, and supply chain of your organization. Provide a solution to each issue.
- Develop a total quality management tool that identifies and analyzes any future issues. Provide a rationale for developing the selected tool.
- Analyze three advantages of employing the just-in-time philosophy in your organization. Evaluate 3-5 potential impacts the philosophy will have on quality assurance. Provide specific examples to support your response.
- Determine a qualitative and quantitative forecasting method for your operation. Next, create a table in which you identify the characteristics of the operation that relate to each method. Evaluate the strengths and weaknesses of each method.
- Use three sources to support your writing. Choose sources that are credible, relevant, and appropriate. Cite each source listed on your source slide at least one time within your assignment. For help with research, writing, and citation, access the library or review library guides.
This course requires the use of Strayer Writing Standards (SWS). The library is your home for SWS assistance, including citations and formatting. Please refer to the Library site for all support. Check with your professor for any additional instructions.
The specific course learning outcome associated with this assignment is:
- Create a strategic plan that strengthens the operation's product life cycle and considers supply chain management, total quality management, the just-in-time philosophy, and includes a forecasting method.
Assignment 1: Vice President of Operations, Part 1
Courtney Nelson
BUS 515
Professor David Kimble
Toyota Motor Corporation is a well-known global leader in the automotive sector, recognized for its creative production tactics and exceptional operational performance. Nevertheless, it is clear from a deeper examination that not all of Toyota's activities are in line with its operational plan. The control of inventory levels is one area where there is a clear discrepancy. Although Toyota's Just-In-Time (JIT) concept aims to minimize inventory to cut costs and prevent waste, there are times when the corporation keeps more inventory than is necessary (Pinto et al., 2018). This might be the result of changes in the supply chain, production hold-ups, or even demand forecasting. Nevertheless, it wastes money and produces inefficiencies when it could be spent elsewhere. Toyota must rectify this mismatched task by optimizing inventory management by JIT principles to improve cost-effectiveness and operational efficiency.
The unpredictability of production processes is another area where there is a misalignment (Östlund, 2020). Toyota's operating strategy places a high priority on quality and dependability, yet variances in production might affect the performance and quality of the products. When variations in the production process are not quickly found and fixed, the misalignment becomes especially apparent. To preserve Toyota's reputation for producing high-quality automobiles, a uniform and standardized approach to manufacturing is necessary. Additionally, Toyota's capacity to sustain the required degree of efficiency and quick production is jeopardized when supply chain problems lead to extended lead times for specific components. To address these problems, Toyota may need to work more closely with its suppliers and create backup plans to reduce supply chain interruptions. These measures are more in line with Toyota's values of JIT and TQM. s
Weaknesses in the Misaligned Tasks
The main drawback that comes with Toyota's overstock management is the higher carrying expenses that the company bears. The need for warehousing, security, and insurance due to this surplus inventory results in additional costs that take away from funds that could be used for innovation and expansion. Moreover, keeping too much inventory can cause obsolescence, which can cost money when things become out-of-date or unsellable (Prakash et al., 2018). Toyota's operational efficiency is compromised by this misalignment with lean concepts and the just-in-time (JIT) philosophy, which indicates inefficient resource allocation and a failure to capitalize on the cost-saving benefits of JIT.
The irregularities and fluctuations observed in Toyota's manufacturing procedures expose deficiencies in quality assurance, potentially leading to extensive consequences (Liker, 2021). Such discrepancies in the dependability and quality of the goods can undermine customer confidence and harm the brand's reputation. Any flaws or irregularities could result in expensive recalls, warranty claims, and even legal trouble, all of which could have a negative effect on the company's bottom line. Furthermore, unpredictability in manufacturing processes can result in rework or the discarding of defective items, which reduces cost efficiency and jeopardizes the company's capacity to maintain profit margins and competitive pricing. To ensure that manufacturing processes are in line with Toyota's operational strategy of producing dependable and high-quality automobiles, a greater emphasis must be placed on standardizing and continuously improving them.
Operations Strategy
Based on the four competitive priorities, Toyota Motor Corporation can create a new operations plan that prioritizes cost, quality, time, and flexibility (Liker, 2021). Toyota should keep focusing on cost-effectiveness by implementing its well-known lean manufacturing concepts and streamlining its supply chain to save costs and waste to strengthen its competitive edge. Regarding quality, the company should continue to uphold its steadfast commitment to manufacturing dependable, high-quality cars by putting in place strict quality assurance guidelines, continuous improvement procedures, and strict quality control methods. Time-wise, Toyota may take advantage of its just-in-time (JIT) production system to further cut lead times, allowing it to quickly adapt to changing consumer needs and maintain its competitive edge in the quick-paced automotive sector. Finally, to ensure that Toyota stays competitive and flexible in the rapidly changing automotive industry, it may improve its flexibility by expanding the range of products it offers, adjusting to changing consumer tastes, and investigating cutting-edge technologies like electric and driverless cars. To sustain its leadership in the global automobile industry, Toyota has aligned its operational strategy with the competitive priorities of cost, quality, time, and flexibility through the use of an integrated approach.
Competitive Priorities and Infrastructure Analysis
The competitive priorities of cost, quality, time, and flexibility are essential to Toyota's operations within the framework of its renowned production system. The just-in-time (JIT), lean manufacturing, and total quality management (TQM) frameworks that Toyota has painstakingly developed are fundamental to these goals (Achikanu, 2022). Toyota can achieve unmatched operational efficiency by utilizing artificial intelligence (AI) and advanced data analytics, which will secure its long-term competitiveness. Predictive analytics and real-time insights help streamline manufacturing procedures, quality control, and inventory management, resulting in significant cost savings and higher productivity. But considerations like the initial outlay, the requirement for strong data security protocols, and potential employee resistance to technology change all need to be carefully considered.
Toyota can take advantage of the revolutionary movement in the automobile industry towards sustainability and become a leader in environmentally friendly production (Achikanu, 2022). This means making investments in the manufacturing of electric vehicles, using renewable energy sources, and utilizing eco-friendly materials. Long-term advantages include alignment with worldwide sustainability trends, a competitive advantage in a more environmentally sensitive market, and a sustainable brand image. However, there's a chance that making the switch to sustainability may need upfront expenses and big infrastructural adjustments.
Cobots, or collaborative robots, have the potential to completely transform Toyota's operations by increasing productivity and adaptability (Dossou et al., 2022). These flexible robots can operate alongside human workers, helping with precise and repetitive jobs, lowering human mistake rates, and quickly adjusting to changing production needs. Enhanced operational flexibility and adaptation to changing market needs are among the benefits. Cobot adoption, however, can need significant upfront costs and encounter opposition from the current staff, necessitating careful planning and change management techniques.
References
Achikanu, A. O. (2022). The indicators for the effectiveness of business process improvement (Master's thesis, Sumy State University).
Dossou, P. E., Verdier, V., & Ogor, A. (2022). Production Systems Performance Optimization through Human/Machine Collaboration. In Supply Chain-Recent Advances and New Perspectives in the Industry 4.0 Era. IntechOpen.
Liker, J. K. (2021). Toyota Way: 14 management principles from the world's greatest manufacturer. McGraw-Hill Education.
Östlund, P. (2020). Improving Materials Supply Processes to Assembly Lines through the Toyota Production System and Lean Manufacturing.
Pinto, J. L. Q., Matias, J. C. O., Pimentel, C., Azevedo, S. G., & Govindan, K. (2018). Just in Time factory. Management for Professionals.
Prakash, I., Prakash, A., & Prakash, H. (2018). Romancing with inventory management. Blue Diamond Publishing.
er and be on the same page with each other.
Collepals.com Plagiarism Free Papers
Are you looking for custom essay writing service or even dissertation writing services? Just request for our write my paper service, and we'll match you with the best essay writer in your subject! With an exceptional team of professional academic experts in a wide range of subjects, we can guarantee you an unrivaled quality of custom-written papers.
Get ZERO PLAGIARISM, HUMAN WRITTEN ESSAYS
Why Hire Collepals.com writers to do your paper?
Quality- We are experienced and have access to ample research materials.
We write plagiarism Free Content
Confidential- We never share or sell your personal information to third parties.
Support-Chat with us today! We are always waiting to answer all your questions.
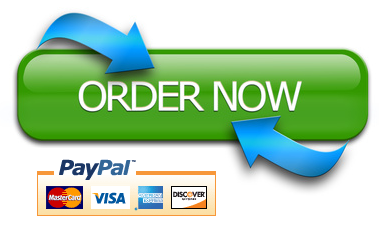