Case Study: BP’s Procurement and Supply Chain Management 1) 4-5 pages written response* outlining the results of their analysis of the case questions. Any data (e.g. academic articles,
Case Study: BP's Procurement and Supply Chain Management
1) 4-5 pages written response* outlining the results of their analysis of the case questions. Any data (e.g. academic articles, case, industry journals, periodicals, videos, or other sources of relevant information) relevant to the case and/or question response should be included.
2) Power Point Slides
Case Study Questions
Do you recommend the consolidation effort of PSCM? Why or Why not? Justify the answer and include a plan of action if you decide to consolidate the pipe inventory. The plan should include the following points:
1. A breakdown of current inventory carrying costs on an annual basis using the information provided in the case study. What information is missing that would be helpful? Include any assumptions you make such as fill rate and inventory holding costs.
2. Develop a strategy for consolidation or standardization that includes which pipe specifications will be kept and which specifications will be excluded and justify your reasoning. The plan should include expected annual cost savings, improvements to inventory management, and a plan to phase out or dispose of obsolete inventory if applicable.
3. There are two groups that will likely oppose such an effort: BP engineers working on the various projects and joint-interest partners that help fund each project. Describe how you would approach the different groups to obtain approval for your consolidation plan. Describe the drivers that each group faces and identify potential points of conflict and how you would overcome such opposition if challenged
The Southern Inspection master service contract expires in four months. Make a recommendation for or against the Louisiana relocation effort. This recommendation should include the following:
1. Propose an evaluation process and scorecard, along with any performance metrics that may apply. Perform a financial health analysis on all the suppliers using the available information in the case. When financial statements are not provided, what other methods can be used to better understand supplier health? How does this information or lack thereof, weigh in to supplier selection?
2. Identify the locations that would be suitable. Justify why the site or sites were selected.
3. Identify the switching costs from the incumbent supplier. What risks are involved when switching suppliers? How will these risks be mitigated?
4. How does the pipe inventory consolidation agenda play into the relocation effort? Would the outcome of one action affect the outcome of the other? Why or why not? If relocation is recommended, should both inventory consolidation and relocation efforts take place concurrently? If not, which should take precedence and why?
Due 4th March 2023
Council of Supply Chain Management Professionals 333 East Butterfield Road, Suite 140 Lombard, Illinois 60148 USA +1 630.574.0985 | [email protected] | cscmp.org
CSCMP ACADEMIC CASE STUDY SERIES
Case studies can supplement a course and be used to teach application of supply chain
management concepts to real-world situations. Others can use the case studies to learn
about supply chain challenges and to analyze the situation to develop solutions.
BP’s Procurement and Supply Chain Management
An Academic Learning Case Study written for the Council of Supply Chain Management Professionals
Written by: Arunachalam Narayanan, Texas A&M University, College Station, Texas Malini Natarajarathinam, Texas A&M University, College Station, Texas Brandon Winn, Procurement & Supply Chain Management, BPs
Jeffrey Kirkpatrick / Dallas Baptist University Order # 82146 / Order Date: 1/5/2023 Copyright
This document is available from our site and provided for your personal use only and may not be retransmitted or redistribute d without written permission from the Council of Supply Chain Management Professionals (CSCMP). You may not upload any of this site’s material to any public server, online service, network, or bulletin board without written permission from CSCMP.
BP’s Procurement and Supply Chain Management
2
This case was developed solely for the purpose of classroom discussion. Some details of
the case have been disguised. This case is not intended to serve as endorsements, sources of
academic or business data, or illustrations of effective or ineffective management of the
personnel or company.
OVERVIEW OF BP
BP p.l.c. is one of the world’s largest energy providers of fuel for transportation, energy
for heat and light and petrochemical products for everyday items. BP has interests in both
upstream and downstream segments in over 100 countries worldwide making it a fully
integrated energy company. Upstream refers to finding and extracting crude oil and natural
gas from deep underground reservoirs. Downstream operations consist of refining and
marketing oil and gas into usable consumer products.
The United States subsidiary of BP p.l.c., BP America Inc., is one of the nation's largest
producer of oil and gas. They own and operate oil and natural gas fields, refineries, chemical
plants and lubricant processing facilities in 22 states that are worth over $40 billion in fixed
assets. BP America has both onshore and offshore drilling operations in the United States.
This case focuses on upstream procurement activities in the Gulf of Mexico. Figure 1
depicts BP’s offshore platforms. Assets in the development stage have project teams and
robust drilling programs to bring newly discovered oil and gas to the market. Once "first oil" is
achieved and the asset is fully commissioned, it transitions to the production group that
operates the newly drilled wells. Overall demand for drilling products and services decreases in
the production stage. A typical oil field in the Gulf of Mexico can produce for up to twenty
years or more before the reservoir is fully depleted and the asset is decommissioned.
Jeffrey Kirkpatrick / Dallas Baptist University Order # 82146 / Order Date: 1/5/2023 Copyright
This document is available from our site and provided for your personal use only and may not be retransmitted or redistribute d without written permission from the Council of Supply Chain Management Professionals (CSCMP). You may not upload any of this site’s material to any public server, online service, network, or bulletin board without written permission from CSCMP.
BP’s Procurement and Supply Chain Management
3
Figure 1. BP assets in the Gulf of Mexico
BP’S PROCUREMENT AND SUPPLY CHAIN MANAGEMENT
The Procurement and Supply Chain Management (PSCM) group of BP America is a
partially decentralized organization. Their function is to develop plans for the management of
third party spend and to motivate and engage the broader BP workforce to achieve maximum
value from suppliers and contractors. Within their Gulf of Mexico operations, BP spends about
$3-$3.5 billion on third party suppliers.
The goal of PSCM is to achieve maximum value from third party spend while mastering
the associated risks. To deliver this goal the group must leverage BP's scope and scale by
developing foundational and strategic PSCM capabilities such as standardization, aggregating
demand, building strategic relationships, and developing supply chains in emerging economies.
The PSCM group is responsible for sourcing all goods and services required for drilling and
producing hydrocarbons.
Jeffrey Kirkpatrick / Dallas Baptist University Order # 82146 / Order Date: 1/5/2023 Copyright
This document is available from our site and provided for your personal use only and may not be retransmitted or redistribute d without written permission from the Council of Supply Chain Management Professionals (CSCMP). You may not upload any of this site’s material to any public server, online service, network, or bulletin board without written permission from CSCMP.
BP’s Procurement and Supply Chain Management
4
Figure 2. Pipe placement in the wellbore
A key product category for BP's business is steel pipe that is cemented into the drilled
well to protect and isolate geological formations from collapse and contamination. The other
purpose of the pipe is to allow hydrocarbons to flow from the reservoir to the wellhead. Well
depths in the Deepwater Gulf of Mexico region are often 25,000 feet from the ocean floor
down to the reservoir. This product category is known in the industry as Oil Country Tubular
Goods (OCTG). The terms OCTG and pipe are used interchangeably throughout this case. Figure
2 illustrates pipe placement in the well and the corresponding name of each pipe section.
There are three general classifications of OCTG material: carbon, alloy, and chromium.
Carbon pipe is of a lower grade and strength, and is often used in onshore wells of low criticality.
Wells in the Deepwater Gulf of Mexico have high pressures and aggressive corrosion conditions
requiring more expensive high grade alloy and chromium pipe for corrosion resistance.
Jeffrey Kirkpatrick / Dallas Baptist University Order # 82146 / Order Date: 1/5/2023 Copyright
This document is available from our site and provided for your personal use only and may not be retransmitted or redistribute d without written permission from the Council of Supply Chain Management Professionals (CSCMP). You may not upload any of this site’s material to any public server, online service, network, or bulletin board without written permission from CSCMP.
BP’s Procurement and Supply Chain Management
5
Wellbore placement is noted in Figure 2. Each joint of pipe is mated together via male
and female threaded connections machined onto each end. When a section of the well is
drilled and ready for pipe placement, workers on the drilling rig vertically stack the pipe and
lower it into the well one by one by twisting each connection together with large iron tongs.
After being lowered and set into the well, cement is pumped through the pipe and then
pushed out the bottom and up the sides between the outside of the pipe and the rock. After
the cement is dry, the next hole section is drilled.
DOMESTIC OIL AND GAS INDUSTRY
Since 2003, there has been an increase in drilling activities both in the US and around
the world. As the selling price of oil and natural gas increases, more capital were available for
drilling projects. According to the America Petroleum Institute (API), completion of US oil and
gas wells have consecutively increased since 2003, and in 2014 reached the highest levels in
nearly 35 years. The following figure shows the number of US oil drills versus the West Texas
Intermediate (WTI) crude oil price.
Figure 3. US oil drilling rig count versus WTI crude oil price
Jeffrey Kirkpatrick / Dallas Baptist University Order # 82146 / Order Date: 1/5/2023 Copyright
This document is available from our site and provided for your personal use only and may not be retransmitted or redistribute d without written permission from the Council of Supply Chain Management Professionals (CSCMP). You may not upload any of this site’s material to any public server, online service, network, or bulletin board without written permission from CSCMP.
BP’s Procurement and Supply Chain Management
6
The upward trend in drilling has put a strain on the OCTG supply chain. According to
one supplier of pipe, the total US OCTG inventories were relatively low at about four months'
supply (or 1.2 million tons) at one point of time. Wary of fluctuating steel costs, pipe
distributors have also kept inventory fairly lean in case of a price drop. These developments,
coupled with the capacity limits in the OCTG supply chain, results in long lead times for the end
user and forces energy companies such as BP to carry large amounts of inventory to meet the
drilling demand.
SOURCING PIPE AT BP
Since OCTG accounts for only one percent of the global steel market, the manufacture
of pipe for the oil industry is scheduled at the steel mills' convenience. The recent economic
boom in China and India caused steel producers to focus on metal goods used in building
construction and the automotive industry (the two largest users of steel). This bias toward
other industries and the scarcity of raw materials result in 2 to 24-month lead teams for
certain OCTG, making demand planning at BP especially difficult.
While steel pipe may sound like a commodity, metallurgy and manufacturing quality is
paramount. BP carefully selects steel mills located in the United States, Europe, and Japan
capable of manufacturing API standard pipe grades with the engineering ability to develop
unique metal alloys set by BP's own standards. Only a handful of steel mills meet this criterion.
To help ease the inventory burden to BP, a single domestic distributor that represents
most of the selected steel mills is utilized. The distributor will only carry products manufactured
to API specifications; any custom pipe made for BP is purchased directly from the mill. The
agreement with the distributor allows for unused or defective products to be returned,
preferred pricing, and consignment-based inventory. When custom pipe is ordered, BP owns it
at the time of manufacture. These direct mill orders are non-cancelable and non-returnable.
Jeffrey Kirkpatrick / Dallas Baptist University Order # 82146 / Order Date: 1/5/2023 Copyright
This document is available from our site and provided for your personal use only and may not be retransmitted or redistribute d without written permission from the Council of Supply Chain Management Professionals (CSCMP). You may not upload any of this site’s material to any public server, online service, network, or bulletin board without written permission from CSCMP.
BP’s Procurement and Supply Chain Management
7
A further complication to the purchase of pipe used in the Gulf of Mexico is the
threaded connection itself. Premium threads are proprietary thread designs manufactured by
select companies. These proprietary thread designs achieve a gastight metal-to-metal seal that
standard API threads cannot. BP has standardized on two brands of premium threads for pipe
used in offshore wells. These premium threading companies, Seal Tight and Interlock, have
strategic relationships with either the steel mill or distributor. Most pipe orders specify the
thread type so the threading operation is performed at the mill. However, there are some
instances (less than 15 percent) where the pipe is received plain-ended, and BP is responsible
for having the pipe threaded at a local Seal Tight or Interlock facility.
ORDER PLACEMENT PROCESS
The order placement process of pipe for drilling operations involves the following steps:
First, the engineer defines the pipe specifications after analyzing the drilling location.
The specification includes size, weight, length, grade, and connection types based on the
pressure, corrosion requirements, and well depth. Most of the pipe specifications are based on
API standard grades carried by the distributor. However, exploratory wells present a high level
of uncertainty and sometimes require engineered solutions beyond any standard grade of
pipe. In these instances, BP must work directly with the mill to develop a solution.
The engineer provides these specifications to the materials coordinator (buyer) through
an internal requisition process. The materials coordinator then places the order with the
distributor based on pre-agreed terms and pricing in the master contract. In most cases, BP
would receive staggered shipments of its pipes. For example, if the project requires 100,000
feet of a specific pipe, they would receive 20-40% of it in the first shipment based on lead time
and rate of consumption and accept the remaining quantities in subsequent shipments. In
cases of unique purchases, the approved mills will submit proposals and a purchase order will
be awarded to the selected bidder.
Jeffrey Kirkpatrick / Dallas Baptist University Order # 82146 / Order Date: 1/5/2023 Copyright
This document is available from our site and provided for your personal use only and may not be retransmitted or redistribute d without written permission from the Council of Supply Chain Management Professionals (CSCMP). You may not upload any of this site’s material to any public server, online service, network, or bulletin board without written permission from CSCMP.
BP’s Procurement and Supply Chain Management
8
Once the order is placed, the domestic distributors schedules the production in steel
mills based on pipe specifications, availability of capacity in the steel mill, and its threading
capability. The pipes are mostly ordered on the basis of consignment, while in some cases BP
owns the inventory. The steel mill after receiving the order from the distributor, places it in the
long production queue based on the priority of the request. After production, the pipe is
shipped to storage yards in Houston. If a domestic mill manufactures the pipe, it is shipped via
rail car to Houston and unloaded directly into the yard, or placed on a truck that delivers to the
yard location. Pipe ordered from foreign mills is shipped into the Port of Houston where it is
then trucked to the storage facility. In one case, airfreight was used to transport a very urgent
order at a cost of $1 million. Approximately 60% of all OCTG is ordered from foreign mills.
STORAGE, INSPECTION, AND SHIPMENT TO DRILLING RIGS
BP stores their inventory in a third-party facility located in Houston that specializes in
pipe maintenance and inspection. At the storage facility, pipe is inspected using EMI
(Electromagnetic Inspection) and FLUT (Full Length Ultrasonic Testing) techniques to identify
the presence of any manufacturing or stress induced flaws. Pipe inspection must be performed
at this stage of the supply chain because steel mills will not inspect pipe to the standards
required by BP because the process is too time consuming.
Although the storage facilities are not owned or operated by BP, safety of the workers
is the number one priority. BP pays a premium to have its own segregated section of the pipe
yard with specially trained contract personnel to handle the movement of pipe inventory to
and from the inspection facilities. Since pipe is kept in storage for extended periods of time,
corrosion prevention becomes quite important. To maintain the integrity of the pipe, they are
stored at least 18 inches above the ground and stacked up to no more than six feet. The six-
foot height restriction is due to an industry safety code that requires personnel to be tethered
in a safety harness. Pipe can be stacked up to ten feet if a tie-off is available. Recycled plastic
Jeffrey Kirkpatrick / Dallas Baptist University Order # 82146 / Order Date: 1/5/2023 Copyright
This document is available from our site and provided for your personal use only and may not be retransmitted or redistribute d without written permission from the Council of Supply Chain Management Professionals (CSCMP). You may not upload any of this site’s material to any public server, online service, network, or bulletin board without written permission from CSCMP.
BP’s Procurement and Supply Chain Management
9
timbers are placed between each stack and the threaded portions of the pipe (most
susceptible to corrosion) are protected by composite thread protectors. The racks are
constructed so that the pipe is slightly slanted to allow for water runoff. Such racks cost
approximately $1,500 to $2,000 to construct.
When the operator from the drilling rig requests the pipe, the yard crew prepares it for
the drilling rig, which includes a full-length drift, addition of pipe accessories such as float
equipment and centralizers, and bolstering for offshore platforms. They are stacked on trucks
with 44,000 lbs load limits using a forklift with a loading cost of about $200 per truck and
shipped to Port Fourchon in Louisiana at a cost ranging from $3 to $5 per mile per truckload.
The pipe is then loaded and shipped on a vessel to the drilling rig.
PIPE PURCHASE: SHOULD THEY CONSOLIDATE?
BP's inventory consists of 35 different pipe specifications. Specifications refer to outer
diameter, measured in inches, weight, measured in pounds per foot (refers to thickness of
pipe), and grade, which refers to the metal composition. Most pipe specifications are standard
API, except for those used in exploratory wells, which are typically proprietary grades.
Appendix "A" shows the 35 different pipe specifications stored in Houston. The grades
of the pipe increase in material strength and corrosion resistance as you read down the table.
When HC is denoted in the grade, it refers to high collapse which means the pipe has higher
yield strength and can withstand high pressure wells. 13Cr110 grade pipe provides carbon
dioxide corrosion resistance, but cannot be used in sour gas (hydrogen sulfide) producing
wells. 25Cr125 can be used in both sour gas and carbon dioxide producing wells, but is only
utilized by one project. Outer diameter and weight increase when read from left to right. The
table provides information on the average annual usage of each type of pipe in thousands of
feet as well as the standard deviation of demand. There is a large variability in usage due to
project specific orders.
Jeffrey Kirkpatrick / Dallas Baptist University Order # 82146 / Order Date: 1/5/2023 Copyright
This document is available from our site and provided for your personal use only and may not be retransmitted or redistribute d without written permission from the Council of Supply Chain Management Professionals (CSCMP). You may not upload any of this site’s material to any public server, online service, network, or bulletin board without written permission from CSCMP.
BP’s Procurement and Supply Chain Management
10
Appendix "B" provides the price per foot of each pipe specification and the associated
lead time in weeks. Generally, there is a premium price paid for the higher grade pipe and in
most cases, they have longer lead times. Pipe of lower grade can be substituted with pipe of
higher grade if it is within the same outer diameter and weight range. Also, the price per foot will
decrease with increase in annual usage. The pricing chart provided is associated with the annual
usage in Appendix "A". A forty-foot length should be assumed for all pipe identified in the table.
Project economics are determined by the price of oil. Exploratory and appraisal wells
are typically the first to be canceled or delayed when oil futures trade low. These types of
projects also require custom engineered pipe that remains in inventory, sometimes for years, if
the project is canceled. Even for sanctioned commercial projects, individual teams often work
in silos and develop different solutions for the same problems. Also, factors such as weather
and lead time may affect project schedule, making demand forecasting even more unreliable.
Lack of standardization and a fragmented project approach leads to excess inventory that
cannot be shared between different projects. When considering inventory carrying costs,
which include the cost of capital, opportunity costs, material handling costs, and inventory
control costs, it is not economically feasible to store the pipe for long durations. In most cases,
the pipes that are left in the pipe yard would probably be written off as scrap, unless an
engineer requests the same grade.
PSCM is looking for ways to coordinate the purchase of pipe to avoid excess inventory
in the system. The plan is to buy a common specification of pipe, which is acceptable to most
locations in the Gulf of Mexico, so that inventory consolidation is possible. Two likely sources
of resistance to this initiative are the engineers and joint-interest accounting. Engineers on the
project teams want their pipe optimized for each individual well. Joint-interest partners have
trouble justifying the cost difference between the grades of the pipe. For example, a pipe
designed for high-pressure environments can be used in locations where the pressure is low,
but at a greater unit cost thereby increasing the cost of the drill rig.
Jeffrey Kirkpatrick / Dallas Baptist University Order # 82146 / Order Date: 1/5/2023 Copyright
This document is available from our site and provided for your personal use only and may not be retransmitted or redistribute d without written permission from the Council of Supply Chain Management Professionals (CSCMP). You may not upload any of this site’s material to any public server, online service, network, or bulletin board without written permission from CSCMP.
BP’s Procurement and Supply Chain Management
11
A leaner inventory can be troublesome if pipe cannot be expedited. If the pipe is not
available when needed, BP is still obligated to pay for all costs of the drilling rig even when idle.
Non-productive time costs the same as productive time, which can be anywhere from $400,000
to $1,000,000 per day. The drilling rig costs alone often justify a fully stocked pipe yard.
STORAGE AND INSPECTION FACILITIES: CURRENT SITUATION
The supply market for OCTG storage and inspection has seen significant consolidation.
In years prior, BP utilized four pipe yards in the Houston area. Currently, Southern Inspection,
a subsidiary of a large oilfield supply conglomerate, acquired all four of these facilities. Each
service contract was transferred to Southern Inspection, and the pricing was honored until their
expiry in the following year. When a new contract was negotiated, unprecedented price
increases ensued. The average price of inspections rose by 15% and pipe movement costs
increased by 25%. Southern Inspection cited increased demand for storage space and
investments in new inspection equipment as the primary drivers. BP found itself in a weak buyer
position, and accepted the new pricing. The negotiated price list is provided in Appendix "C".
Soon after the new contract was signed, a study was conducted by the BP Logistics
group to evaluate the possible relocation of the present storage facility for OCTG in Houston
to a site or sites in Louisiana. The study looked at the cost of handling, taxes and logistics
capability in the region. The findings of this study indicated potential savings in dollars and time
through such a move, provided comparable facilities and services were available in Louisiana.
Because this study was limited to transportation and tax issues, additional information as it
pertains to the other services required for OCTG storage and inspection is necessary.
BP currently occupies approximately fifty acres of storage space at the Southern
Inspection yard and expects to increase this space requirement by five percent annually for
the next three years. A compelling reason for moving inventory to Louisiana is the fact that
Jeffrey Kirkpatrick / Dallas Baptist University Order # 82146 / Order Date: 1/5/2023 Copyright
This document is available from our site and provided for your personal use only and may not be retransmitted or redistribute d without written permission from the Council of Supply Chain Management Professionals (CSCMP). You may not upload any of this site’s material to any public server, online service, network, or bulletin board without written permission from CSCMP.
BP’s Procurement and Supply Chain Management
12
Collepals.com Plagiarism Free Papers
Are you looking for custom essay writing service or even dissertation writing services? Just request for our write my paper service, and we'll match you with the best essay writer in your subject! With an exceptional team of professional academic experts in a wide range of subjects, we can guarantee you an unrivaled quality of custom-written papers.
Get ZERO PLAGIARISM, HUMAN WRITTEN ESSAYS
Why Hire Collepals.com writers to do your paper?
Quality- We are experienced and have access to ample research materials.
We write plagiarism Free Content
Confidential- We never share or sell your personal information to third parties.
Support-Chat with us today! We are always waiting to answer all your questions.
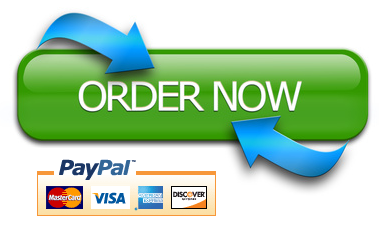