The annual demand for the Savonera bar soap, one of the luxury brands manufactured by Mellow Cosmetics Company, is 50,000 soap bars. The cost of a single soap bar is $2.5
QUESTION 1:
The information in this paragraph applies to this question and the 5 questions that follow (so, questions 1-6).
The annual demand for the Savonera bar soap, one of the luxury brands manufactured by Mellow Cosmetics Company, is 50,000 soap bars.
The cost of a single soap bar is $2.50.
The rate of holding cost per unit per year, which includes opportunity cost of investment and deterioration of a soap bar when in storage, is 10% of the cost of the soap bar.
The cost of setting up machinery for making a batch of the Savonera soap bar, which includes changing the materials and tools, and wastage of initial test quantities, is $40 per setup.
The company currently uses an arbitrary batch size of 6,000 for making Savonera bars of soap. Based on this batch size and the information provided earlier, please calculate and report the annual inventory holding (carrying) cost for Mellow Cosmetics Company.
Remember to show your work including any formula you use.
Round your final answer to two spaces (if needed) after the decimal.
Bold your final answer.
QUESTION 2:
Based on the arbitrary batch size of 6,000 bars of Savonera soap and the information provided earlier, please calculate and report the total annual cost of setups for Mellow Cosmetics Company.
Remember to show your work including any formula you use.
Round your final answer to two spaces (if needed) after the decimal.
Bold your final answer.
QUESTION 3:
The management of Mellow Cosmetics Company has requested your help for systematically figuring out the batch size for Savonera soap to replace their arbitrary batch size. Based on the demand and costs information provided earlier, please help by calculating and reporting the Economic Order Quantity (EOQ) for the batch size that you would recommend for manufacturing Savonera soap bars.
Remember to show your work including any formula you use.
Round your final answer to two spaces (if needed) after the decimal.
Bold your final answer.
QUESTION 4
Using the EOQ batch size that you calculated for Savonera bars of soap, please calculate and report the annual inventory holding (carrying) cost for Mellow Cosmetics Company.
Remember to show your work including any formula you use.
Round your final answer to two spaces (if needed) after the decimal.
Bold your final answer.
QUESTION 5
Using the EOQ batch size that you calculated for Savonera bars of soap, please calculate and report the total annual cost of setups for Mellow Cosmetics Company.
Remember to show your work including any formula you use.
Round your final answer to two spaces (if needed) after the decimal.
Bold your final answer.
QUESTION 6
Compare the total cost of inventory management (holding + setup cost) for the two quantities (6,000 and the EOQ you calculated), i.e., calculate and report the difference in the total costs of inventory management using the two different quantities.
Bold your final answer for the difference amount.
Based on your knowledge of the idea behind EOQ, please explain the reason for the difference (in words in two or three sentences – not in terms of reconciling the differences mathematically).
QUESTION 7
The information in this paragraph applies to this question and the three questions that follow (so, questions 7-10).
Workshop manager Shinji Suzuki has noted that the daily demand for the StoryKore bibimbap pots (dolsots) produced and sold by his business, Pandamonium International Cookware, located in southwest Champaign, is 24 pots.
The workshop operates 365 days a year.
The lead time for producing the pots is 4 days.
Shinji Suzuki would like your help in figuring out a few selected questions about managing inventory.
Based on the information provided, please calculate and report the reorder point under the assumption of no uncertainty. and therefore, no need for any safety stock.
Remember to show your work including any formula you use.
Round your final answer to the nearest whole number.
Bold your final answer.
QUESTION 8
Closer scrutiny of past data reveals that the standard deviation for daily sales is 9 pots. Adding this new information to that provided earlier, please calculate and report the number of pots you recommend as safety stock for a 99% service level (the z score for which, using the function =NORM.S.INV(0.99) in Microsoft Excel, is 2.33).
Remember to show your work including any formula you use.
Round your final answer to the nearest whole number.
Bold your final answer.
QUESTION 9
The StoryKore bibimbap pots are currently produced at Shinji’s workshop in batches of 120 at a time. Adding this new information to that provided earlier, and ignoring the uncertainty in demand and therefore the standard deviation of demand, please calculate and report every how many days on average does another batch of pots need to be produced.
Remember to show your work including any formula you use.
Round your final answer to the nearest whole number.
Bold your final answer.
QUESTION 10.
Shinji decides to increase the batch size from 120 noted in the previous question to 146 pots. Based on this new batch size, and ignoring the uncertainty in demand and therefore the standard deviation of demand, please calculate and report how many batches of size 146 need to be produced on average every year to fulfill demand.
Remember to show your work including any formula you use.
Round your final answer to the nearest whole number.
Bold your final answer.
Operations and Supply Chain Decisions and Metrics Professor Gopesh Anand
1
Module 3: Inventory Management
Table of Contents Module 3: Inventory Management …………………………………………………………………………….. 1
Lesson 3-1: Types of Inventory …………………………………………………………………………………………… 2 Module 3.1.1 Reasons for Inventory …………………………………………………………………………………………………….. 2 Module 3.2.1 Classifications of Inventory ……………………………………………………………………………………………… 6
Lesson 3-2: Inventory Decision – How much? ……………………………………………………………………… 16 Module 3.2.1 How Much and When …………………………………………………………………………………………………… 16 Module 3.2.2 Economic Order Quantity ……………………………………………………………………………………………… 22 Module 3.2.3 Calculating How Much to Order …………………………………………………………………………………….. 32
Lesson 3-3: Inventory Decision – When? …………………………………………………………………………….. 39 Module 3.3.1 Reorder Point for Continuous Replenishment or Review …………………………………………………… 39 Module 3.3.2 Calculating When to Order ……………………………………………………………………………………………. 45 Module 3.3.3 Other Inventory Management Systems …………………………………………………………………………… 51
Operations and Supply Chain Decisions and Metrics Professor Gopesh Anand
2
Lesson 3-1: Types of Inventory
Module 3.1.1 Reasons for Inventory
In this lesson, we're going to look at classifications of inventory. We're going to look at different types of inventory, and we're going to see how we can classify them based on importance as well as some other things. First, if you think about what is inventory, simple definition is it's whatever is kept in stock. Goods in stock is what we define as inventory. A lot of times we use the word stocks to denote inventory. The reason we, organizations keep inventory, or even as individuals, we keep inventory at home in our pantries and our refrigerators is to match supply with demand. You want to match the timing of when the demand occurs versus when you can get the supplies, and that's why you keep inventory. When we talk about organizations keeping inventory, you want to focus on internal as well as external customers. Within an organization, there may be sub- processes and the inventory might be for a customer that is within the organization for a sub-process. It can be internal customers, or it can be external customers and external customers are customers whose demand, there might be more uncertainty about when you compare that to internal customers. You have to think about it differently when you're talking about management of inventory. Finally, you want to think about businesses and individual customers, both, when you're talking about inventory, because a lot of companies have business to business relationships so they are making products to sell to a different business. Companies are outsourcing a lot of their
Operations and Supply Chain Decisions and Metrics Professor Gopesh Anand
3
production. A lot of components coming from different businesses, and you want to talk about inventory of that as well.
If you think about inventory and the idea of matching demand with supply, you can think about it from a perspective of a lake. The capacity of this lake is how much inventory you can store in your warehouse. The capacity of the warehouse in which you can store inventory. The level of the lake is the current level of inventory that you have. The rainfall is a supply, and the consumption of water is your demand. Put it this way. When the rainfall exceeds the consumption, the level of inventory is going to increase and it's going to get closer and closer to the capacity of your Warehouse, and when the consumption is more than the supply, the lake level is going to decrease. Inventory acts as the matching of demand and supply in this way, and we think about water consumption in a very similar fashion when we store water for our consumption in our households.
Operations and Supply Chain Decisions and Metrics Professor Gopesh Anand
4
Let's take a look at why organizations have inventory, why they build inventory. The first reason you can think of is a lead time for supply. For example, if there is a supplier that is at a certain distance from the purchaser, from the buyer, it's going to take a long time or it's going to take some model time for the supplies to get there. There's transportation time, but there will also be lead time that the supplier might quote in terms of we're busy with other things, we'll take so much time to make your particular order, and that's going to get added to the lead time of the transportation time. As a buyer, you are going to have to plan for that lead time during which that it's going to take for your order to get to you so you're going to store some inventory for that lead time. Within a process, within a multi-activity process, you might have activities that are at different processing times. In fact, most times you're going to have activities that have unmatched processing times. For example, one activity could be running at the rate of 10 units an hour, and another activity might be running at the rate of 15 units an hour so one is faster than the other. Now, you're not going to run both of them at 100 percent, but what you're going to do is run the faster one and build up inventory, and pause until the slower one catches up. Different processing times will mean that you will need to have some inventory based on the different processing times of different activities. Economies of scale. You might have a setup time involved with doing changeovers from one type of product to another. In which case you're going to say, well, I'm going to make a large batch of this inventory before I change over to the next item that I make. In which case, you are going to build some inventory. Now, this reason is basically because you want to take your cost of that setup time and spread it over a larger quantity, and that's why you have a batch size. You're going after economies of scale. You could think of a similar reason for
Operations and Supply Chain Decisions and Metrics Professor Gopesh Anand
5
economies of scale when you're talking about getting supplies from an external supplier, in which case, you might be thinking about well, I want to get a full truckload in order to take the cost of all items and spread it over lesser number of deliveries. In that case, you're going for economies of scale for an external supplier that you're purchasing from and you are building inventory based on that. You get a big order and you build up inventory until that gets exhausted and then you get another big order. Seasonality. If you're making lawnmowers, they're not going to be sold at the same rate throughout the year. In order to build up inventory for the spring and summer seasons, you'll continue to run your manufacturing plant at a certain rate during the winter months in order to build up inventory for that season. Similarly, with other seasonal items, such as the festive items for Christmas or other festivals that you might build up. Variations of products. When you have many different types of products, you are not going to keep making all of them all the time simply because it may not be cost-effective so you'll make certain items and keep them in stock while you're running other items on your line. Sometimes you'll be keeping inventory on the basis of speculation of prices. You'll say, well, here's a discount that I'm able to get or I know that the price of oil is going to go up in the near future. If I'm an airline, I'm stocking up on how much fuel I'm purchasing, and that might be inventory. That comes in my name, even though it may not be delivered to me, I may be buying those future contracts, and that's inventory that's effectively being held by me. Availability might be an issue if you're expecting a shortage, you're trying to speculate and hold that item so that you have it available when you need it. That might be a reason for you to hold inventory. Finally, talk about uncertainties. Uncertainties in terms of demand, uncertainties in terms of supply, and uncertainties even in terms of the way your process is being run. If it's not running at 100 percent yield rate, you might keep excess inventory for what if it breaks down or what if I have a quality issue or what if I have a strike and my plant has to shut down. I might keep inventory for those purposes to cover for those uncertainties. That's why organizations keep inventory.
Operations and Supply Chain Decisions and Metrics Professor Gopesh Anand
6
Module 3.2.1 Classifications of Inventory
Now, you can think of inventory and classify it based on the reasons that organizations keep inventory. Now keep in mind that this classification is not something that you can directly apply to a piece of inventory that you might see. You might not be able to say that this piece of inventory is pipeline or cycle, or anticipation. These are reasons on the basis of which you can classify inventory. Pipeline inventory is the time that inventory is in transit in any process. You order from a supplier that's distant from you during the time that it's in the pipeline to get to you, it's pipeline inventory. Cycle inventory is based on batch sizes. Let's say I run a batch of 10,000 units of one type of product, product X before I move to product Y? That cycle, when I'm making those 10,000 units, is going to start from zero and build up all the way to 10,000 units and I'll have 10,000 units of inventory before I send it off to the next task or to my customer, and that's going to be my cycle inventory. I'm building up that inventory during that production cycle. Anticipation inventory is something that we referred to earlier. You are overproducing when you do have the time or you're overproducing in anticipation of demand that you're expecting in the future. Then safety stock inventory is inventory that you hold for any kind of uncertainty. It might be uncertainty to do with production rates. It might be uncertainty to do with demand. It might be uncertainty to do with lead times. It may take five days for this product to get to me, or it might take eight days. I have to keep some buffer in order to allow for that uncertainty. That's what is classified as safety stock inventory. These are the main reasons that organizations keep inventory.
Operations and Supply Chain Decisions and Metrics Professor Gopesh Anand
7
Now here's a classification that you can actually point out and say, this inventory is raw material inventory or work in process inventory or finished goods. In any organization, you'll be able to say raw material inventory is whatever has been purchased from outside. Whatever has been purchased from an external party is going to be raw material inventory. The work in process inventory is inventory that is being worked on. Whether it's waiting to be worked on within the process boundaries, or whether it's actually being worked on in the process. Whether it's in the machine, whether it's bread that's being baked in the oven, or it's in a machine that requires a certain amount of time for something to get cured. It's going to be work-in-process inventory. Finally, finished goods inventory is anything that's ready from that organization's perspective, that's ready to go to the customer to get delivered to the customer. It's at the loading dock waiting to get on that truck to go to the customer, that's going to be your finished goods inventory.
Operations and Supply Chain Decisions and Metrics Professor Gopesh Anand
8
Now that we have this classification of inventory, what I'd like you to do is apply this classification to two simple kinds of businesses. The first business is a bakery, and the second business is in the same stream of products. It's a grocery store or a sandwich shop. It's a sandwich shop that uses the bread to make sandwiches. You have a bakery and a sandwich shop. What I'd like you to think about is, what are the raw materials? What is the work in process that would be the case for the bakery or the sandwich shop. Finally, what are the finished goods that these two types of businesses would have? Give that a minute and think about it, and then we'll come back and talk about the implications of this classification for these two different types of businesses.
Operations and Supply Chain Decisions and Metrics Professor Gopesh Anand
9
We were classifying the raw materials, the work in process, and the finished goods for bakeries and sandwich shops. For a bakery, you may have thought of flour, you may have thought of water, yeast. Those are the things that go into making bread. Those would be raw materials that they would be purchasing from outside, that they would be acquiring from outside. The work in process is going to be anything that's kept, that is in the process. If it's baking for a certain amount of time, it's working process inventory. If it's dough that's kept to mature before they start baking the bread from it, that's going to be work-in process inventory. Finally, the finished goods are going to be the loaves of bread that come out, that get on the truck to get delivered to customers. Raw material, work in process and finished goods for a bakery. For a sandwich shop, their raw material would include the bread that they're going to buy from that bakery. The raw material for them is going to be the finished goods for the bakery. Then they're work in process inventory is going to be some of the probably the sliced bread that they keep or they might be able to do some processing of sandwiches and keep them ready for customers. Then the finished goods are going to be the ready sandwiches that are being delivered to customers. What you can see from here is that what is one organization's finished goods is going to be raw materials from a different organization's perspective. Even though we have this classification, it'll be based on the usage and the position of that organization in this whole chain that is making products for the ultimate customer.
Operations and Supply Chain Decisions and Metrics Professor Gopesh Anand
10
When we think about inventory, we normally think about manufacturing businesses. We say, well, in services, you can't hold inventory. It's something that you make for a customer and you cannot really keep that in stock. We think about capacity of the service as being the inventory that we hold. But if you think about it, even services such as hospitals, restaurants, and hotels have to keep inventory. They have to keep inventory of different things that are needed for them to do their business correctly. Hospitals need drugs, they need surgical instruments. Restaurants need different things to serve their food. They need different things to manufacture their food. Hotels are going to need different things that they need to stock in the rooms. They're going to need different linens to be able to use them in the different rooms. Even their inventory is going to be important and to give you an interesting fact about inventory in services.
Operations and Supply Chain Decisions and Metrics Professor Gopesh Anand
11
In healthcare, inventory costs can be up to 40 percent of the total operating cost. The cost of holding, and using inventory is about 40 percent of total cost. This cost, by the way, is second only to labor costs, which is obviously not surprisingly, the highest proportion of cost for a healthcare business. Inventory is pretty important even for services.
Now let's look at a different way of classifying inventory. This is based on which items in inventory need more attention versus which items need less attention. This is called an ABC analysis. It's based on what you may be familiar with as the 80/20 rule. You have 20 percent of
Operations and Supply Chain Decisions and Metrics Professor Gopesh Anand
12
your items that account for 80 percent of the value. That's the idea between the ABC analysis is that you want to focus on those really important A items in terms of controlling the inventory, you want to keep a close eye on them. Then the C items, you may not follow as closely. You may not care as much about them in terms of keeping a close eye on them, and spending your resources keeping a close eye on them.
The idea is simple. You have 20 percent of your items are responsible for 60 percent of the dollar value. The next 30 percent of the items are responsible for 30 percent of your monetary value. Then the next 50 percent of the items are responsible for the top 10 percent of your dollar value. You have the A, B, and C that is telling you which are the more important items to keep an eye on.
Operations and Supply Chain Decisions and Metrics Professor Gopesh Anand
13
Let's take this ABC classification, and apply it to an example. Here's an example of a company that is making automobile parts and we have data on their annual unit sales that you're going to see in the next couple of slides. They want help in identifying the A, B, and C items.
Here you have the numbers to do the ABC analysis for local plane automotive parts. What you can see is the first column is just the identifier, the second column gives you the annual sales in units, and the third column is giving you the unit price. Take a minute, digest this information, and think about how you would go about converting this into an ABC analysis telling you which
Operations and Supply Chain Decisions and Metrics Professor Gopesh Anand
14
items you should be focusing on, spending more time on in terms of inventory control, which item's next, in terms of an ABC analysis.
Here you see the result of this analysis. We've run through the numbers here. What we've simply done is converted the annual sales quantities into annual sales monetary values here, dollars, and we see that we have annual sales, a total of 169,000. Once you have that, you can convert into percentage of total sales. That's what we've done. In the next column we have the percentage of sales. What you can see right from there is item Number 2, which is responsible for 80 percent of the monetary value of the sales. That would be obviously an item to focus on. It's one out of seven items that is responsible for 80 percent of their sales and that's going to be the prime item to focus on. This analysis can give you a sense of which items to focus on next, and which items to focus on the least.
Operations and Supply Chain Decisions and Metrics Professor Gopesh Anand
15
As a result, what you can see is you have this classification of one out of seven products accounting for 80 percent of the sales. That one item that we saw earlier, the next in line, the next in sequence in terms of percentage of dollar value are two items that account for 50 percent of the total monetary value of sales. Then out of the total of seven items, the last four account for only five percent of the total value of sales. What we've seen from this is that you can classify inventory based on many different ways. ABC classification is one of them which focuses on the importance of inventory management for different items in inventory. Earlier we saw a classification of raw material work in process and finished goods. Then earlier than that we saw why do different companies store inventory, and we saw classification based on that.
Operations and Supply Chain Decisions and Metrics Professor Gopesh Anand
16
Lesson 3-2: Inventory Decision – How much?
Module 3.2.1 How Much and When
In this lesson, you're going to learn how to determine how much quantity of inventory to order based on some different costs of ordering and holding inventory. But before we get to the idea of calculating how much you need to order, let's look at inventory from two different perspectives. These two perspectives are dependent demand inventory and independent demand inventory. Now what do we mean by dependent demand inventory? A dependent demand inventory basically means, it's the inventory for the parts that you are going to make in-house. Here, for example, you see a recipe for making a certain bread. Now, once you know how much quantity of bread you would like to make, the dependent demand inventory is going to be determined by the recipe. It tells you how many eggs are needed, how much salt is needed, how much flour is needed, how much water is needed. It's going to be determined by the demand for that finished product. That's going to tell you how much of the dependent demand inventory you need to take care of. Another example you can think of is, once you decide how many cars are going to get manufactured, you can look at the recipe, the bill of material that you have for making that car, and you can see what are the different parts that will be needed. To give a very basic idea, you're going to need four of the tires, four wheels for the main ones, and then one for the spare. That's going to get determined by the independent demand inventory. Dependent demand inventory, you manage it using
Operations and Supply Chain Decisions and Metrics Professor Gopesh Anand
17
manufacturing resource planning systems, which take your parent item demand, and divide it up into its different components and tell you how much is needed. That's what you see mainly in ERP systems, Enterprise Resource Planning systems, and Manufacturing Resource Planning system. What those systems do, is they take your parent item demand and convert it into the dependent demand for all the parts that you're going to use.
What we're going to focus on in this lesson is going to be your independent demand inventory. It's the inventory of items that you sell to customers. It's the inventory that is coming from outside the organization. This could be a B2B customers so you could be selling parts to a car manufacturer or you could be selling cars as a dealership to ultimate customers. You could be selling bread to many different stores. It's a B2B relationship, or it could be a store that's selling bread to ultimate customers. The independent demand item is going to be different based on where you are in that big supply chain.
Operations and Supply Chain Decisions and Metrics Professor Gopesh Anand
18
Before we get into the calculation of how much you should order, what I'd like you to do is think about the things that you consider when you go out and get groceries. Take any one regular item that you purchase and I say milk over here, for example. What are some of the considerations that you have when you decide how much quantity you're going to buy during this trip to the grocery store? Whether you're going to buy a gallon, two gallons, how much you're going to get from the grocery store? What are some of the things that go through your mind, when making that particular decision.
Operations and Supply Chain Decisions and Metrics Professor Gopesh Anand
19
We're talking about going to the grocery store and getting milk. Some of the things that would have gone through your mind would have been things like, how much do you have in your refrigerator, how much do you have at home, and how much do you consume on average? Your average demand rate of your household for that item. Here we said milk, but you could be thinking about any grocery item, and how much you consume on a daily basis. The other thing that might go through your mind is, how much does it cost from the perspective of, if you have to think about the investment that you're going to make. It might not be much for milk, but if it's a more expensive item, you're thinking, should I be investing so much of my money in purchasing milk for future consumption? You might think about a price discount and you might be tempted to buy more, if there's a price discount available, or if you anticipate a price discount that's coming up, you might purchase less based on that upcoming price discount that you're expecting. Storage space is going to be a huge consideration, whether you have a spare refrigerator or you don't, and how much space do you have in your refrigerator for storing the milk that you're purchasing. Expiration date on the milk and how much you use versus when it's going to get spoilt, is another thing that you might consider. Finally, you're going to think about when you're going to go to the store next. If you're planning to not go for a couple of weeks and you're thinking, I need to get enough for a couple of weeks, and then there might be some uncertainty involved in how much you consume in that couple of weeks, so you might get a little bit extra based on what if guests come or what if your family consumes more than they normally do in that particular period of time when you're planning to go to the store next. These are the things that you think about, when you decide how much to purchase in terms of groceries for your household. Companies, organizations go through very similar decision-making when they are deciding how much to purchase.
Operations and Supply Chain Decisions and Metrics Professor Gopesh Anand
20
The things that they're thinking about is, how much capital investment there's going to be, how much storage space is going to be required, whether it's an item that's going to need handling, it's going to have to be stored in different places and moved around, whether there's going to be refrigeration needed, if there's some cost involved with that. They're also thinking about spoilage. Is there going to be something that expires over time? If it's something in which there might be a fluctuation in demand, it might get obsolete. People might not want that particular product. If you're thinking about a fashion goods store, you are concerned about the items going out of style and not being able to be sold and that's when you would have to discount them. Those are the things that companies are thinking about when they're thinking about how much inventory they want to purchase.
Operations and Supply Chain Decisions and Metrics Professor Gopesh Anand
21
When you think about inventory management decisions, there are two basic decisions that companies are making. One is, how much to order and the other one is, when to order. When should they place the order? These are going to be based on different considerations of the things that we talked about a little bit earlier.
Operations and Supply Chain Decisions and Metrics Professor Gopesh Anand
22
Module 3.2.2 Economic Order Quantity
Remember we're focusing on independent demand items here, items that a company would purchase from a supplier that's coming from outside. And how much to order is typically based on this model that is very popular called the economic order quantity. So this is a model for calculating the amount of inventory in terms of how much you want to order. Now, this model is based on the principle of trading off of two different costs. One of these costs is the cost of ordering. So if you think about the cost of ordering, if you're thinking about that trip to the grocery store, it's the cost of the time that you're spending to go to the grocery store, it's the cost of of the gas that you might be consuming to get to that distant grocery store. For a company, it might be order processing costs, it might be cost of transportation, it's the cost of getting a truckload and that might be a fixed cost, whether you get a full truckload or you get a quarter of a truckload, it might be a fixed cost based on that. So that would get counted under your
Collepals.com Plagiarism Free Papers
Are you looking for custom essay writing service or even dissertation writing services? Just request for our write my paper service, and we'll match you with the best essay writer in your subject! With an exceptional team of professional academic experts in a wide range of subjects, we can guarantee you an unrivaled quality of custom-written papers.
Get ZERO PLAGIARISM, HUMAN WRITTEN ESSAYS
Why Hire Collepals.com writers to do your paper?
Quality- We are experienced and have access to ample research materials.
We write plagiarism Free Content
Confidential- We never share or sell your personal information to third parties.
Support-Chat with us today! We are always waiting to answer all your questions.
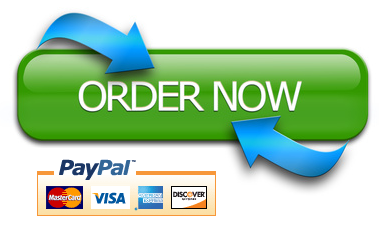