business discussion question and need an explanation and answer to help me learn. Please respond to my two classmates discussion post. Please use in-text citation and include a re
business discussion question and need an explanation and answer to help me learn.
Please respond to my two classmates discussion post. Please use in-text citation and include a reference list.
Post 1:
Lucio Mauro Cota
RE: Week 2 Discussion
Top of Form
Hello Professor J. and Classmates!
As mentioned in my previous DQ for week 1, I work for a BPO/Fintech company from the US. I oversee the company in Latin America, both Brazil and Colombia entities. The main reason we have the entities in Latin America is related to the workforce for the company, which means Latin America supports the entire operations from the Americas (North, Central, and South America). Our primary goal in “Latam” is to have employees working on different projects across the board. For the last six months, we have hired an average of 10 to 15 employees per month due to the company’s constant growth and turnover.
The most important process here is “the recruiting and hiring process.” Somehow, it has been working well for the last three years and a half; however, improvements are needed. The process I’m studying for this term will be the Recruiting and Hiring Process. Creating a value stream for this process will contribute a lot to the organization, adding value to the process itself and understanding gaps we have and don’t have visibility yet. “Gaining a deep understanding of current state value stream performance is vital in designing and making improvements” (1).
The value this value stream can deliver are the following:
– Understand the end-to-end process (current stage): validate individual steps, the steps needed, and the necessity for changes. With that, increasing productivity and efficiency and adding more quality to the process.
– Map the blocks and gaps found: validate which steps cause delays or are not required. With that, support to create guidelines for the teams, making sure they understand R&Rs.
– Understand the Process time, Lead time, and %C&A: validate the SLA and time taken for each step to be completed. With that, creating appropriate metrics and SMART goals for the process.
With the details above, we can recreate the process, if necessary, or make the adjustments required to deliver a better service. “Without a value stream map, organizations fail to develop customer-centric processes and fail to organize in a way that best serves the very reason they exist” (2).
We are only measuring the turnover process, not the hiring process. We can measure the entire process, SLAs, process, and lead times with a value stream map. At the same time, understanding the individual contributions of all involved and aligning the leadership team.
Regards
Lucio Cota
References:
1 ? JWI 550. Week Two Lecture Notes. 2023. Operational Excellence.
2 ? Martin & Osterling. Value Stream Mapping.
Post 2:
Patrick Hebda
Top of Form
Week 2 Discussion Post
At General Motors, our business is mainly manufacturing vehicles for our customers. In 2021 GM sold 6.291 million cars, less than in 2020 (1). Some plants, like Flint Assembly, build over 1000 heavy-duty pickups daily (2), making you wonder how this process can be improved. Multiple value streams leading up to the production of each piece of a vehicle, let alone the end product. Therefore, many improvements can be made in various value streams. For this discussion post, I will focus on the value steam of manufacturing a heavy-duty truck for a customer.
What value does this value stream deliver to the organization or contribute to its competitiveness?
GM’s “money-maker” is the heavy-duty trucks such as the GMC Sierra and Chevrolet Silverado models. Each minute the line is down, it can cost GM thousands of dollars. Flint Assembly plant’s ability to make this amount of trucks keeps our prices lower than competitors and makes our trucks more readily available to the workforce. Our quality for these trucks is also second to none.
There are situations in the plant where multiple line operators switch off a job on each truck because of a great ergo concern.
As a wire harness engineer, a goal of mine is to diminish opportunities for my part to cause issues in the plant. This goal means minimizing high ergo forces from my harness, simplifying the complexity of my parts, reducing part numbers in general, and ensuring my designs are done on time to ensure timely delivery to the plant. This process is a value stream in itself.
What metrics are currently used (or should be used) to monitor the performance of this value stream?
At Flint assembly, specific metrics monitoring performance for producing heavy-duty trucks. The most important is timing. A car moves down a conveyor belt and ideally does not stop, which means that every piece of the vehicle needs to be in the right place at the right time, ranging from a small bolt or screw to entire seat structures or wheels. Depending on the vehicle, there can be over 30,000 parts that go on a car (3). If one of these pieces is slightly off the timing, it can slow down the production of the truck, costing GM thousands.
This situation is why specific metrics such as manufacturing cycle time and yield are essential. Cycle time is simply the amount of time it takes for a vehicle to get from the beginning of the line to driving off the line (4). Each job has a particular Process Time (PT) (5), which totals the Cycle time for the plant. Yield is simply a percentage of the accuracy of the vehicle that was built. Some cars do not work correctly right off the line; this could be part of many things. Maybe one of those 30,000 pieces was missed. Yield tracks the number of vehicles that successfully start and can be shipped and divides that number by the total number of cars that went down the production line (4).
What do you predict might be some improvement opportunities in this value stream?
Constant changes and improvements are made to this value stream every day in plants worldwide. Manufacturing plants, and engineers for that matter, are a great example of the Plan-Do-Study-Adjust Cycle (PSDA) (6). To improve yield, I must ensure that my harnesses are accurate to the schematics. I work with an electrical architect daily during a release process to ensure the info is correct from device owners, compiled into the schematics, communicated to the supplier, released correctly, and then more supplier quality checks after that. A short wire could make the vehicle fail or cause significant damage to the car and the customer. This process almost seems like a value stream in itself. It is something I can work on every day to improve that process to be quicker and better quality.
To improve the cycle times at the plant, I must also ensure I am using the best clipping and taping strategies for my harness. A simple clip change can ease the process for the operator, meaning there will be no hold-up at any particular point. We battle with this today.
I have a personal DFSS project we are doing at work for my harness near the front of the dash grommet. It has gotten a lot of attention, and maybe I can share the project with you all when we complete it.
Professor J, please let me know if I understand this concept. I feel like there are multiple value streams within larger ones. Maybe that is just different processes? I would like to set up a time to talk about this.
Thank you, class. I can’t wait to dive into this even deeper to strengthen my portion of the value stream.
Patrick Hebda
Reference:
Wall Street Zen. 2021. General Motors Co Production & Sales Statistics https://www.wallstreetzen.com/stocks/us/nyse/gm/statistics
Jamie L. LaReau. June 2021. GM to increase vehicle deliveries to dealers: ‘Help is on the way.’ Detroit Free Press. https://www.freep.com/story/money/cars/general-motors/2021/06/03/gm-dealers-production-semiconductor-chip-shortage/7521111002/
Collectors Auto Supply. May 2020. How Many Parts Are in a Car? https://collectorsautosupply.com/blog/how-many-parts-are-in-a-car/#:~:text=The%20average%20car%20has%20roughly,of%20individual%20parts%20inside%20it.
Guiding Metrics. The Automotive Industry’s 11 Most Critical Metrics. https://guidingmetrics.com/content/key-automotive-industry-metrics/
Martin & Osterling. Value Stream Mapping. Chapter 3.
Martin & Osterling. Value Stream Mapping. Chapter 1.
Collepals.com Plagiarism Free Papers
Are you looking for custom essay writing service or even dissertation writing services? Just request for our write my paper service, and we'll match you with the best essay writer in your subject! With an exceptional team of professional academic experts in a wide range of subjects, we can guarantee you an unrivaled quality of custom-written papers.
Get ZERO PLAGIARISM, HUMAN WRITTEN ESSAYS
Why Hire Collepals.com writers to do your paper?
Quality- We are experienced and have access to ample research materials.
We write plagiarism Free Content
Confidential- We never share or sell your personal information to third parties.
Support-Chat with us today! We are always waiting to answer all your questions.
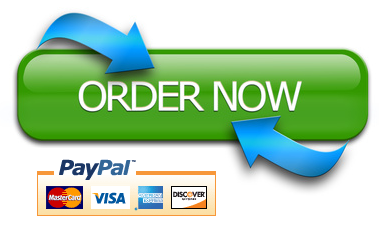