Kaizen events, or work-outs, are one to five-day rapid improvement events widely used in Lean and Operational Excellence deployment. Use your work from the Value Stream Map assignment to ide
Kaizen events, or work-outs, are one to five-day rapid improvement events widely used in Lean and Operational Excellence deployment. Use your work from the Value Stream Map assignment to identify improvement opportunities in the value stream that are suitable for Kaizen events or work-outs.
1) List the potential Kaizen Select the one to be deployed, and justify your selection. Then, define the Kaizen objective and scope for the selected event.
2) Develop a detailed agenda for each Kaizen Use a tabular format, showing the following:
- Day and time
- Session topics
- Lean tools to be used
- Deliverables or outputs
- Rationale
3) Explain your choice for the number of days and the sequence for session topics, and justify the Lean tools to be used and outputs from each session. Show how your Kaizen agenda supports the Kaizen objective and scope for the event. This discussion should be specific to your value stream and organization.
I PROVIDED A TEMPLATE TO MAKE IT EASY AND USE WORK FROM THE VALUE STREAM DOCUMENT I PROVIDED TO DO THIS ASSIGNMENT.
Detailed Agenda(s) for Kaizen or Work-Outs
Student Name:
Date:
Professor:
1) List the potential Kaizen events. Select the one to be deployed, and justify your selection. Then, define the Kaizen objective and scope for the selected event.
· [Insert potential Kaizen event]
· [Insert potential Kaizen event]
· [Insert potential Kaizen event]
The chosen Kaizen event is [insert here]. The justification for selecting this Kaizen event is [insert here]. The Kaizen objective is [insert here]. The Kaizen scope is (insert here).
2) Develop a detailed agenda for each Kaizen event.
Day 1
Time |
Session Topic/Objective |
Lean Tools |
Output/Deliverables |
Rationale |
Day 2
Time |
Session Topic/Objective |
Lean Tools |
Output/Deliverables |
Rationale |
3a) Explain your choice for the number of days and the sequence for session topics, and justify the Lean tools to be used and outputs from each session.
Number of Days:
Sequence for Session Topics:
Lean Tools:
Session Outputs:
3b) Show how your Kaizen agenda supports the Kaizen objective and scope
for the event. This discussion should be specific to your value stream and organization.
How the Session Supports the Kaizen Agenda and Scope:
,
MAN 4504 Operational Decision Making
10/29/22
Christian Hernandez
Florida State College at Jacksonville
Value Stream Mapping and Analysis:
1
Current State Value Stream Map
Title: Current State Value Stream Map for Patient Admission
Patient
Insert LT
Insert PT
Total LT* = 121 min |
Total PT* = 57 min |
Dashboard
Registration
RN Exam
Patient History
Provider Exam
Patient History
Provider Order
RN Collects Lab
Completion of labs and req
Labs sent Therapy begins
Patient care received. Patient departs system
Insert LT
Insert PT
Insert LT
INSERT PT
Insert LT
Insert PT
Insert LT
Insert PT
Insert LT
Insert PT
PT= 4min
LT= 5min
PT=12 min
LT=21 min
PT=9 min
LT=17 min
PT=6 min
LT= 12 min
PT=12 min
LT=21 min
PT=14 min
LT= 45 min
2
Value Stream Current State Overview
Overview of the Process
The procedure entails: For the implementation, a six-step strategy that included Lean education, ED observation, patient flow analysis, process redesign, new process testing, and complete implementation was used. The emphasis of process redesign was on soliciting ideas for improvement from frontline employees across all departmental units. During the calendar year, patient volume, cost per patient, ED length of stay (LOS), and value-based and operational outcome metrics such as patient satisfaction were compared.
Challenges
value stream mapping from reception to patient care received is the complexity of the process. There are numerous steps involved in this process, and each one must be completed correctly in order for the patient to receive the necessary care.
The requirement for coordination between all of the hospital's departments in order for the process to run smoothly.
Lack of enough staff to help in providing service to the patient.
Bottlenecks
Reception: The reception area is where patients and visitors arrive, and it is often the busiest area in a hospital. This can become a bottleneck if there aren't enough employees to handle the volume of people.
Waiting areas: In hospital waiting rooms, there is frequently a bottleneck as patients wait to be seen by a doctor or nurse. This can be due to a lack of staff or patients who have been waiting for a long time.
Treatment areas: Treatment areas in a hospital can be a bottleneck because they are where patients receive care. This can be due to a lack of staff or patients who have been waiting for a long time.
References
Erick Dickson, Sabi Singh, Dickson Cheung, Christopher C Wyatt(2018). Application of Lean Manufacturing Techniques in the Emergency Department Value Stream Mapping.
3
Collepals.com Plagiarism Free Papers
Are you looking for custom essay writing service or even dissertation writing services? Just request for our write my paper service, and we'll match you with the best essay writer in your subject! With an exceptional team of professional academic experts in a wide range of subjects, we can guarantee you an unrivaled quality of custom-written papers.
Get ZERO PLAGIARISM, HUMAN WRITTEN ESSAYS
Why Hire Collepals.com writers to do your paper?
Quality- We are experienced and have access to ample research materials.
We write plagiarism Free Content
Confidential- We never share or sell your personal information to third parties.
Support-Chat with us today! We are always waiting to answer all your questions.
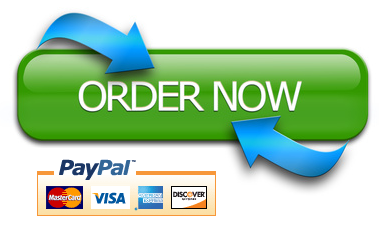