Business Problem-Solving Case GE Bets on the Internet of Things and Big Data Analytics General Electric (GE) wants to be known as the worlds Digital
Read attachment. Answer the questions at the end of the case and use attached information to write your answers for support.
Paper Formatting
- Write at least 200 words per question.
- Follow proper APA format guidelines.
- Include a Cover Page per APA format.
- Set Margins: 1" top, bottom, right, and left.
- Use Font: Times New Roman 12 point.
Business Problem-Solving Case GE Bets on the Internet of Things and Big Data Analytics
General Electric (GE) wants to be known as the world’s Digital Industrial Company. It is moving away from traditional manufacturing toward a much more technology-centric business strategy and business model that
focuses on electric power generators, jet engines, locomotives, and oil-refining gear and software to connect these devices to the cloud. GE is putting its money on the technology that controls and monitors industrial
machines as well as software-powered, cloud-based services for analyzing and deriving value from the data. GE hopes this strategy will turn it into a major software company.
GE is using sensor-generated data from industrial machines to help customers monitor equipment performance, prevent breakdowns, and assess the machines’ overall health. GE has committed $1 billion to
installing sensors on gas turbines, jet engines, and other machines; connecting them to the cloud; and analyzing the resulting data to identify ways to improve machine productivity and reliability. In other words,
GE is betting its future on software and the Internet of Things (IoT).
In a number of industries, improving the productivity of existing assets by even a single percentage point can generate significant benefits. This is true of the oil and gas sector, where average recovery rate of an oil well
is 35 percent. That means 65 percent of a well’s potential is left in the earth because available technology makes it too expensive to extract. If technology can help oil extraction companies raise the recovery rate
from 35 to 36 percent, the world’s output would increase by 80 billion barrels—the equivalent of three years of global supply.
The oil and gas industry is also deeply affected by unplanned downtime, when equipment cannot operate because of a malfunction. A single unproductive day on a platform can cost a liquefied natural gas (LNG)
facility as much as $25 million, and an average midsized LNG facility experiences about five down days a year. That’s $125 to $150 million lost. Minimizing downtime is critical, especially considering declining
revenues from lower energy prices. GE sees a $1 billion opportunity for its IoT software.
The foundation for all of GE’s Industrial Internet (IoT) applications is Predix, a software platform launched in
2015 to collect data from industrial sensors and analyze the information in the cloud. Predix can run on any cloud infrastructure. The platform has open standards and protocols that allow customers to more easily and
quickly connect their machines to the Industrial Internet. The platform can accommodate the size and scale of industrial data for every customer at current levels of use, but it also has been designed to scale up as
demand grows. Predix can offer apps developed by other companies as well as GE, is available for on- premises or cloud-based deployment, and can be extended by customers with their own data sources,
algorithms, and software code. Customers may develop their own custom applications for the Predix platform. GE is also building a developer community to create apps that can be hosted on Predix. Predix is
not limited to industrial applications. It could be used for analyzing data in healthcare systems, for example. GE now has a Health Cloud running on Predix. Data security is embedded at all platform application layers,
and this is essential for companies linking their operations to the Internet.
GE currently uses Predix to monitor and maintain its own industrial products, such as wind turbines, jet
engines, and hydroelectric turbine systems. Predix is able to provide GE corporate customers’ machine
operators and maintenance engineers with real-time information to schedule maintenance checks, improve
machine efficiency, and reduce downtime. Helping customers collect and use this operational data proactively would lower costs in GE service agreements. When GE agrees to provide service for a
customer’s machine, it often comes with a performance guarantee. Proactive identification of potential issues that also takes the cost out of shop visits helps the customer and helps GE.
In early 2013, GE began to use Predix to analyze data across its fleet of machines. A single engine’s
operating data will only tell you there’s a problem with that engine. But by collecting massive amounts of data and analyzing the data across its entire fleet of machines, GE was able to cluster engine data by
operating environment. The company found that the hot and harsh environments in the Middle East and China caused engines to clog, heat up, and lose efficiency, so they required more maintenance. GE found
that engines had far fewer of these problems if they were washed more frequently. Fleet analytics helped GE increase engine lifetime and reduce engine maintenance. The company thinks it can save its customers
an average of $7 million of jet airplane fuel annually because their engines will be more efficient. Predix’s robust data and analytics platform made it possible for GE to use data across every GE engine all over the
world and cluster fleet data.
Predix is starting to provide solutions for GE customers. For example, Invenergy LLC, North America’s
largest independent, privately held renewable energy provider is implementing GE Asset Performance Management reliability management software on 13 turbines at six gas-operated thermal plants in the
United States. The software is based upon Predix and will perform predictive analytics on turbines that produce an operating capacity of 3,159 megawatts, enough to power a half-million homes. The software will
help plant technicians more accurately predict and diagnose equipment failures before they occur in order to avoid unplanned outages. During preliminary testing, the system identified a turbine journal bearing
experiencing early-stage vibration. A failure could have damaged the turbine and produced an unplanned outage, but Invenergy technicians were able to detect and repair the malfunction three months before it
would have occurred. The GE system will also help Invenergy better manage its assets to achieve the optimal solution for reducing cost, managing risk and improving availability and reliability.
British oil and gas company BP plc had been using its own software to monitor conditions in its oil wells but decided to get out of the software business and became a GE customer. By the end of 2015, BP equipped
650 of its thousands of oil wells with GE sensors linked to Predix. Each well was outfitted with 20 to 30 sensors to measure pressure and temperature, transmitting 500,000 data points to the Predix cloud every
15 seconds. BP hopes to use the data to predict well flows and the useful life of each well and ultimately to obtain an enterprise-wide view of its oil fields’ performance.
GE identified pipeline risk management as a major challenge for the oil and gas industry. There are 2 million miles of transmission pipe throughout the globe, moving liquid oil or gas from its point of extraction to
refining, processing, or market. About 55 percent of transmission pipeline in the United States was installed before 1970. Pipeline spills are not frequent, but when they occur, they cause serious economic and
environmental damage as well as bad publicity for pipeline operators and energy companies. Pipeline operators are always anxious to know where their next rupture will be, but they typically lacked the data to
measure pipeline fitness. Operators had no way of integrating multiple sources of data into one place so
they could see and understand the risk in their pipelines.
GE developed a pipeline-management software suite for accessing, managing, and integrating critical data for the safe management of pipelines, including a risk assessment tool to monitor aging infrastructure. GE’s
risk-assessment solution combines internal and external factors (such as flooding) to provide an accurate, up-to-the minute visual representation of where risk exists in a pipeline. This risk assessment tool enables
pipeline operators to see how recent events affect their risk and make real-time decisions about where field service crews should be deployed along the pipeline. The risk assessment tool visualization and analytics
capabilities run on Predix.
Weather has a sizable impact on risk for pipelines in areas prone to seismic activity, waterways, and
washouts. Checking weather patterns along thousands of miles of pipe for rain or flood zones, and integrating those data with other complex pipeline data sets is very difficult to perform manually. But by
bringing all relevant data together in one place, GE gives pipeline operators easier access to information to help them address areas with the greatest potential impact.
GE expects customers to benefit immediately from having all of their data integrated. But it wants them to be able to do more. In addition to being able to examine all current risk, pipeline operators would benefit from a
“what-if” calculation tool to model hypothetical scenarios, such as assessing the impact of adjusting operating pressures or addressing particular areas of corrosive pipe. GE would give them the tools for a
color-coded view of how those actions affect pipeline risk.
GE wants to go beyond helping customers manage the performance of their GE machines to managing the
data on all of the machines in their entire operations. Many customers use GE equipment alongside of equipment from competitors. The customer cares about running the whole plant, not just GE turbines, for
example, and 80 percent of the equipment in these facilities is not from GE. If, for example, if an oil and gas customer has a problem with a turbo compressor, a heat exchanger upstream from that compressor may be
the source of the problem, so analyzing data from the turbo compressor will only tell part of the story. Customers therefore want GE to analyze non-GE equipment and help them keep their entire plant running.
If a customer purchases a piece of GE equipment such as a gas turbine or aircraft engine, GE often enters into a 10- to 15-year contractual services agreement that allows GE to connect to and monitor that machine,
perform basic maintenance and diagnostics, and provide scheduled repairs. GE receives a bonus payment for keeping the equipment running at a specified threshold. GE may now be able to apply such outcome-
based pricing to coverage of non-GE machines.
GE CEO Jeffrey Immelt wants GE to become a top 10 software company by 2020. In order to do this, GE
needs to sell vast amounts of applications and Predix-based analytics. Although few businesses have the capital or infrastructure to operate a platform for integrating and analyzing their IoT data, GE faces
competition from many sources. Amazon, Google, IBM, and Microsoft are all getting into Internet of Things platforms, and dozens of start-ups have similar ambitions. The biggest question is whether other large
industrial companies will turn to GE or to another cloud platform to manage their information. And if you’re a
manufacturer of some size and sophistication, will you allow GE to “own” the data on your business, or will
you manage and analyze the data yourself?
Sources: Paul Gillin, “Industrial IoT Revs Up at Big Renewable Energy Provider,” Silicon Angle, May 17, 2017; www.predix.io, accessed May 20, 2017; Laura Winig,
“GE’s Big Bet on Data and Analytics,” MIT Sloan Management Review, February 2016; www.ge.com, accessed May 20, 2017; Devin Leonard and Rick Clough, “How
GE Exorcised the Ghost of Jack Welch to Become a 124-Year-Old Startup,” Bloomberg Businessweek, March 21, 2016; Holly Lugassy, “GE Leverages Pivotal Cloud
Foundry to Build Predix, First Cloud for Industry,” CloudFoundry.org, May 11, 2016; Cliff Saran, “GE Predictive Analytics Optimises Irish Power Electricity Production,”
Computer Weekly, July 13, 2015; Charles Babcock, “GE Predix Cloud: Industrial Support for Machine Data,” Information Week, August 6, 2015; and “GE: IoT Makes
Power Plants $50M More Valuable,” Information Week, September 29, 2015.
Case Study Questions
MyLab MIS
Go to the Assignments section of MyLab MIS to complete these writing exercises.
11-13 How is GE changing its business strategy and business model? What is the role of information technology in GE’s business?
11-14 On what business functions and level of decision making is GE focusing? 11-15 Describe three kinds of decisions that can be supported using Predix. What is the value to the
firm of each of those decisions? Explain. 11-16 To what extent is GE becoming a software company? Explain your answer.
11-17 Do you think GE will become one of the top 10 U.S. software companies? Why or why not?
11-18 Give three examples of data used in location analytics and explain how each can help businesses.
11-19 How do each of the following types of systems acquire and represent knowledge: expert system, neural network, genetic algorithm?
Chapter 11 References
Agrawal, Ajay, Joshua S. Gans, and Avi Goldfarb. “What to Expect from Artificial Intelligence.” MIT Sloan Management Review (February 7, 2017).
Alavi, Maryam, and Dorothy Leidner. “Knowledge Management and Knowledge Management Systems: Conceptual Foundations and Research Issues.” MIS Quarterly 25, No. 1 (March 2001).
Ask, Julie A., Michael Facemire, and Andrew Hogan. “The State of Chatbots.” Forrester Research
(October 20, 2016).
Breuker, Dominic, Martin Matzner, Patrick Delfmann, and Jörg Becker. “Comprehensible Predictive Models for Business Processes.” MIS Quarterly 40, No. 4 (September 2016).
Erik Brynjolfsson, Tomer Geva, and Shachar Reichman. “Crowd-Squared: Amplifying the Predictive
Power of Search Trend Data.” MIS Quarterly 40, No. 4 (December 2016).
Lacity, Mary C., and Leslie P. Willcocks. “A New Approach to Automating Services.” MIT Sloan Management Review (August 2016).
Burtka, Michael. “Genetic Algorithms.” The Stern Information Systems Review 1, No. 1 (Spring 1993).
Carr, David F. “Collaboration in the Cloud.” Profit (February 2016).
Davenport, Thomas H. “Big Data at Work: Dispelling the Myths, Uncovering the Opportunities.”
Harvard Business Review (2014).
Collepals.com Plagiarism Free Papers
Are you looking for custom essay writing service or even dissertation writing services? Just request for our write my paper service, and we'll match you with the best essay writer in your subject! With an exceptional team of professional academic experts in a wide range of subjects, we can guarantee you an unrivaled quality of custom-written papers.
Get ZERO PLAGIARISM, HUMAN WRITTEN ESSAYS
Why Hire Collepals.com writers to do your paper?
Quality- We are experienced and have access to ample research materials.
We write plagiarism Free Content
Confidential- We never share or sell your personal information to third parties.
Support-Chat with us today! We are always waiting to answer all your questions.
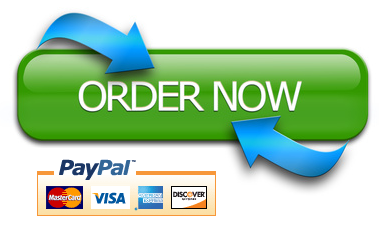