Anderson, D. L. (2019), pages 57-61.?Refer to the?Case?in the textbook for detailed information. Anderson, Donald L. (2019) Orga
Anderson, D. L. (2019), pages 57-61. Refer to the Case in the textbook for detailed information. Anderson, Donald L. (2019) Organization Design: Creating Strategic & Agile Organizations – the case is attached
Your completed case study should consist of:
- Case summary
- Identify the problem
- Present several recommendations
- Indicate their best recommendation
- Provide some way to evaluate within a certain time frame
- Conclusion
Submission Instructions:
- Your case study should be in current APA style, including the title and references page.
- Complete and submit the assignment by 9:00 PM ET Sunday.
Case Study 1: The Supply Chain Division of Superior Module Electronics, Inc.
“Our biggest problem right now is that we are not working together. We are making stupid mistakes, and we know better,” admitted Carl Hoffman, senior vice president for supply chain operations at Superior Module Electronics (SME).
“This company looks nothing like the company that my grandfather started more than 50 years ago. We have performance problems that are keeping us from being competitive. Morale in the division is the lowest it has ever been, and we are endangering our reputation for putting out the highest-quality electronics in our industry segment.”
Superior Module Electronics creates power supplies, batteries, cables, and switches for large industrial applications. Customers of SME use their electronics components in high-risk industrial applications such as mining (minerals, oil and gas) and hazardous manufacturing (industrial gases, fertilizers, explosives). The company’s investment in research and development throughout its history has made it one of the highest-performing companies in its industry. In the past several years, revenues had been steadily rising while competitors reported flat to declining sales. Recently, however, profits at SME have declined and the company is poised to report its first quarterly loss since the recession. Customer complaints about quality have been mounting, and the supply chain division has come under increased scrutiny from the board of directors.
“If one of our power supplies has an electrical surge or it heats up or it causes a fire, it’s no exaggeration to say that there would be fatal consequences,” Carl stressed. “We distinguish ourselves by developing and manufacturing the highest quality products in our industry. We think it’s better to take a little extra time to make it right, because as my grandfather used to say, ‘If it’s not right, it’s wrong.’”
“Government regulations require that our customers adhere to very strict safety practices, and as a result, those same regulations impact us as well. We have to undergo rigorous testing of our products and provide independent data to our customers that certify that our products are safe for use in their environments. But last summer, we had to recall 46,000 power supplies that were shipped out over a 4-month period due to a quality defect in the assembly. There is a possibility that we may face a serious fine for failing to find the defect before the product was sent to customers. If that’s true, it will take a long time to regain our reputation and customer trust. Our CEO, my father Avery Hoffman, screamed at me for three hours,” Carl remembered. “I still can’t get to the bottom of whether the problem was with a supplier or our own internal manufacturing.”
“Our problems are self-imposed. I have a bunch of weak managers reporting to me. They bring all of their problems to me rather than sorting them out among themselves. They are supposed to be organized in a flow: advanced manufacturing does the prototype and then trains the other two manufacturing divisions; supplier contracts work with our external suppliers to get the product here for manufacturing to build; planning tells manufacturing how much to build; shipping sends products to customers; project management improves the quality of the whole operation. None of them takes into account the impact of their work on the other divisions. They operate like independent kingdoms instead of an integrated team. It’s chaos.”
“Many of the problems, I think, stem from the way that we operate as a leadership team. With a few exceptions, we have high-quality people here in the division. The problem is that they are not working together effectively. In addition, there are problems in the attitudes of people. When I go around to meet members of the team, they just don’t seem to have any bigger aspirations or commitment. They don’t seem amped up or energized. A large number of projects are behind schedule. We are not on the same page with where we are going as a division, where we ought to be putting our resources, or how we determine priorities.”
“I have tried to find out more about these issues,” Carl continued. “A recent employee survey indicated that two-thirds of the division’s staff did not believe that they had the authority to make decisions that allowed them to do a quality job. Almost 80 percent indicated that they had untapped capabilities or that they were unable to use their skills to their full potential on the job. In addition, almost 70 percent of the staff felt that the pay practices did not recognize or reward doing quality work. Finally, 73 percent said that promotion decisions were made for political reasons based on preferential treatment rather than qualifications for the job.”
Carl recently called in a consulting team to understand the reasons behind the department’s problems. He provided the consulting team with the current organizational chart for the division (Figure 2.5) and recommended that they hold personal conversations with each leader. Excerpts from interviews with members of the leadership team are included below to explain their perspective about the problems that the supply chain division is experiencing.
Figure 2.5 Superior Module Electronics Organization Chart for Supply Chain Operations Division
The Leadership Team’s Perspective
Rachel Mills, Supplier Contracts
My division is responsible for negotiating contracts with our suppliers, which includes cost, quality, and delivery expectations. If we order 100,000 feet of copper tubing, we want it at a prenegotiated cost, within a certain quality level, and on our time schedule. If we need a delivery of high purity hydrogen sulfide, then it must contain impurities at a level of less than one-half of 1 percent.
As an incentive to negotiate better rates with our suppliers, my team is compensated with a bonus based on supplier performance, specifically their cost. It is a simple formula: For every percentage decrease in cost, my team gets an equivalent salary bonus. A 10 percent reduction in supplier cost is a 10 percent annual bonus. If we can get a part made out of a high-quality composite instead of a pure metal, and the product engineers tell me that it will be the same, then we will change it out with their approval.
Jacob Davidson, Manufacturing (day shift)
“Keep the train moving” is our motto. As the manufacturing engine of the company, the last thing we want is to run out of product and create unhappy customers. It’s my neck on the line, so I will do whatever I need to do in order to make sure that we have enough stock, and I don’t want Carl and Avery coming in my office. My goals are to ensure 100 percent stocking levels on every product, so I miss my goal any time the warehouse is out of stock.
Frankly, everything else is a distraction that wastes my time. On our management team, we have never worked together very well, and most of my department is a duplication of other functions that can’t get their jobs done. I don’t know what Darlene’s team is supposed to be doing. We have our own project leaders that work to improve manufacturing quality, so I see her team as unnecessary. All of my people are doing their jobs. And Rachel’s team lacks the expertise to understand how the products are put together, so when my guys report a quality concern to Rachel’s team, they don’t understand what we are talking about, so we duplicate their work by calling suppliers ourselves. Same thing with Amanda’s team. Her team lacks the basic understanding of what day-to-day manufacturing looks like. They build so few products on her team that they don’t know what it’s like to have 100 times the workload of what they do, so their manufacturing plans are complicated and we have to rework them before we get started.
Franklin Moore, Manufacturing (night shift)
Typically, the manufacturing plan is published every day at 5 p.m. when Louis’s team is leaving for the day. Jacob’s team works until 8 p.m., and then my team comes in and works until 6 a.m. A “planning day” is measured at 6 a.m. for the previous 24-hour period, so my team is the one stuck with any plan changes and we have to scramble to meet the goal. We have two opposite problems with this: too much work, and not enough work. Usually, we fail to meet the newly published plan because we are trying to make up the work that Jacob’s team did not accomplish during the day and we get impossibly difficult goals to meet. But there are also days that the plan is revised downward, so we have less work to do and I have to send workers home. That causes morale problems.
To make matters worse, my turnover on the night shift approaches 40 to 50 percent. It’s rough on the body to have to work the graveyard, so most people stick it out when they first get the job until a position opens up on the day shift. When I have gaps in staffing, I have to turn to our temporary labor until I can get someone hired, which seems to take forever here. Also, no one in our training department is willing to stick around until midnight to run a training program, so we end up doing our own. Most of the training is on the job, led by whoever knows their stuff and has been around the longest.
Shireen Jensen, Warehousing and Shipping
I’m sure you’ve heard the saying “Keep the train moving,” because it’s what Carl tells the whole team all the time. My group consists of the warehouse team that ships out the product based on customer orders. I am evaluated based on warehouse stocking levels and our shipping cycle times, or how fast we can ship out orders to a customer. I have no authority to make decisions on warehouse stocking levels other than to tell Jacob’s team when we are about ready to run out of stock. If his team does not take action, my team pays the price.
We do not have an effective planning or prioritization process because everything feels like an emergency. If one of Carl’s golf buddies complains about an order, he will come down himself to take the materials out of the warehouse and deliver them personally.
Amanda Watson, Advanced Manufacturing
Our job is to take the latest products that are designed by research and development and to actually build them. My team is separate from Jacob’s and Franklin’s manufacturing teams because we have our own manufacturing line to test out what it’s like to build the latest products. Once we create the manufacturing process on any product, we build it for the first 6 months until we feel comfortable that it’s ready to go to Jacob’s and Franklin’s teams.
We’re basically our own self-contained supply chain organization, and we need what we need, so we have our own sourcing organization, too. Rachel’s team won’t help us and is not responsive. For example, when we started our manufacturing plans for the large capacity M4X batteries, Rachel’s team insisted that we use an existing supplier for the chemicals that go in the internal chambers. Our team found that the chemical purity was not to the engineering specifications, so we went ahead and ordered our own. Rachel’s team is pretty incompetent when it comes to the engineering detail. But I have a team of PhDs who can run circles around them, so we just ask them to step aside while we get the job done.
Contributing to the morale problem in the division is that fact that Carl recently decided to outsource the manufacturing of the M4X batteries after we had spent 6 months on the internal manufacturing plan, meaning that all of the time and effort we invested was worthless. The company ended up paying our external manufacturer to repeat the planning work that we had already done, and no one ever asked us for any of our data or findings about how to manufacture the product. If you want to know why morale is so low, consider that we just took a team of brilliant PhDs and flushed their work down the toilet.
Louis Gonzalez, Planning
My team’s responsibility is to create the manufacturing plan, or basically the number of each type of item that our manufacturing teams should be producing. We work with marketing and sales as well as the product managers in the company’s product divisions.
Basically, there is no communication or coordination among each of those groups. There is only conflict and disagreement, plus gaming the system. Sales tells us how many of each type of item they expect to sell, but sales generally overestimates how much they are going to sell because they don’t want us to be out of stock on any of our products. The product division has their own sales estimates, which are almost always lower. I am caught in the middle but I try to accurately predict how much to tell manufacturing to build based on all of that information. Then I have to use our system to convert all of that into specific orders for our suppliers. I might need to increase our order of sheet metal from a supplier, or reduce our order for coils of 10mm gauge wiring. Sometimes our suppliers need advanced notice of our requirements, as early as a few months in advance. The numbers change all the time, so I put out a new manufacturing order almost every day, which makes our suppliers furious. Rachel’s team is supposed to do something about that, but I don’t sense that they care that much.
The biggest problems with planning are communication and politics. The lack of coordination is pervasive across this company, and we are rarely if ever informed about important product releases or features. Engineering comes out with a new product that we didn’t know about, which means that customers want the newest thing, and we’re stuck with a bunch of unsold inventory because we didn’t know what was coming. Or the upper management puts the pressure on Carl to make us build more so it doesn’t look like we didn’t trust their numbers. Carl himself will change the numbers in the system and not tell me until I log in to the system and see the new plan. Then manufacturing has to scramble to get it done. We are always being questioned by upper management and have very little authority to make any decisions.
Darlene Williams, Project Management Office
The mission of my team is supposed to be to orchestrate and manage quality improvement projects across the supply chain division.
I would say that my staff is confused more than anything. Projects are not clearly defined by the leadership team, and there is a great deal of conflict over project priorities. Projects overlap one another and project managers often do not know that they are working on the same thing. Project team members rarely know what their own role is on the team or how they should be working together. Carl himself will come down to the manufacturing floor and shut down a project himself, start another one up, or change the scope or timeline of a project on the spot. The whiplash effect is a demotivator to the whole team. To make it worse, project managers feel that they have no authority over the processes on any of the other teams, so whatever decisions they make can be vetoed by my peers anyway. Decisions about projects and how we allocate resources, including space, time, budgets, and staff, are made arbitrarily by Carl, and there seem to be no priorities to help us decide which projects are the most important. The leadership team does not participate on any project or prioritization process. Sometimes they appear to intentionally undermine the work of my team by starting up teams of their own.
This frustration seems to manifest itself in our relationships with other departments. There is no alignment or engagement with other groups, period. The manufacturing teams feel insulted, defensive, and threatened when my team tries to help them. Manufacturing team members who participate on projects led by my team tend to miss meetings and important deliverables they have committed to. The lack of project stability, unclear roles and responsibilities, and the lack of any kind of rewards for participating on an improvement project outside one’s “day job” have meant that any kind of commitment to a project has plummeted.
Collepals.com Plagiarism Free Papers
Are you looking for custom essay writing service or even dissertation writing services? Just request for our write my paper service, and we'll match you with the best essay writer in your subject! With an exceptional team of professional academic experts in a wide range of subjects, we can guarantee you an unrivaled quality of custom-written papers.
Get ZERO PLAGIARISM, HUMAN WRITTEN ESSAYS
Why Hire Collepals.com writers to do your paper?
Quality- We are experienced and have access to ample research materials.
We write plagiarism Free Content
Confidential- We never share or sell your personal information to third parties.
Support-Chat with us today! We are always waiting to answer all your questions.
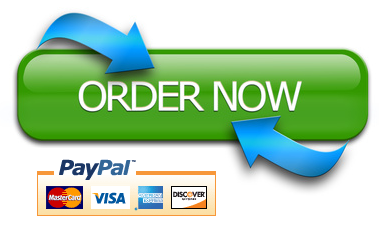