For their newsletter covering hazard analysis and risk reduction techniques, as well as the importance of management commitment and building a sound safety c
For their newsletter covering hazard analysis and risk reduction techniques, as well as the importance of management commitment and building a sound safety culture. Include the following: The appropriate uses of a preliminary hazard analysis.
The process to perform a risk assessment of an ergonomic hazard at a workplace.
Use an example of an ergonomic hazard in your discussion based on the provided scenario.
Determine which regulations/standards/guidelines apply to ergonomic hazards at a workplace.
Recommend abatement strategies to reduce the risks associated with the identified ergonomic hazard.
Discuss how management can promote safety by example. Explain the process of creating a participative safety culture. Use the scenario below.
Scenario: One ergonomic hazard you could consider if you have not come up with one on your own is one with which most people are somewhat familiar: airline baggage handling. Moving heavy baggage of all different shapes and sizes around all day can take a real toll on their rotator cuffs, often resulting in surgery. Removing them from the conveyor, placing them on carts, then onto the loading conveyor, and into the cargo hold of the plane requires all sorts of awkward shoulder motions while under load. This is a significant hazard that has been well-documented in the industry.
Qualitative Risk Assessment in Water Bottling Production: A Case Study of Maan Nestlé
Pure Life Factory
Diana Rbeht* , Mohammed S. El-Ali Al-Waqfi , Jawdat Al-Jarrah
Fire and Safety Engineering Department, Prince Al-Hussein Bin Abdullah II Academy of Civil Protection, Al-Balqa Applied
University, P.O. Box 206, Al Salt 19117, Jordan
Corresponding Author Email: [email protected]
Copyright: ©2023 IIETA. This article is published by IIETA and is licensed under the CC BY 4.0 license
(http://creativecommons.org/licenses/by/4.0/).
https://doi.org/10.18280/ijsse.130605 ABSTRACT
Received: 27 August 2023
Revised: 8 October 2023
Accepted: 31 October 2023
Available online: 25 December 2023
A comprehensive qualitative risk assessment (QRA) was conducted at the Maan Nestlé
Pure Life factory, encompassing its production, storage, and bottling sections. Through a
meticulous review of records, analysis of activities, and examination of work procedures,
potential hazards within the factory were identified and subsequently categorized using
the risk matrix technique. In total, seventeen hazards were identified, of which seven were
deemed high risk, eight medium, and two low. This assessment underscores the
imperative for measures aimed at risk control, reduction, or elimination. The QRA's
qualitative approach, while effective in broad hazard identification, may have led to an
incomplete hazard inventory. Nonetheless, it proved instrumental in pinpointing safety
hazards and informing the development of robust safety policies. These policies integrate
considerations of human behavior and equipment failure, focusing on preserving product
quality while safeguarding the business and its operators. Despite the presence of an
unsafe workplace, the study revealed that the need for new infrastructure is non-essential.
Instead, a series of modifications are recommended, including the replacement of
defective roofs, installation of electrical rolls and lifts, segregation of chemical storage,
personnel training, and various ergonomic and procedural adjustments. The study further
advocates for a subsequent phase of analysis utilizing quantitative techniques such as fault
tree analysis. This is particularly pertinent for hazards requiring specific root cause
identification, enabling the determination of necessary safety controls to address these
root causes and prevent hazard occurrence.
Keywords:
hazard, risk, risk matrix, QRA, risk rating
1. INTRODUCTION
1.1 Basics and definitions
In industrial facilities, safety is a paramount concern,
primarily due to the risks of workplace fatalities and injuries
resulting from inadequate safety measures and the absence of
robust Occupational Health and Safety Management Systems.
In the Jordanian labor market, as reported by Jordan Labor
Watch, occupational injuries are recorded every 25 minutes,
with a work-related death occurring every two days. Estimates
from the Social Security Corporation indicate approximately
20,000 work accidents annually, equating to a rate of 11.7
injuries per 1,000 individuals. The industrial sector accounts
for approximately 25.3% of all work-related fatalities, with the
wholesale and retail trade sector contributing to 17.7%.
Furthermore, the industrial sector experiences 31.6% of total
work injuries, followed by the health and social work sector at
22.0%. Notably, almost half of all occupational injuries befall
workers under 30 years of age, underscoring the imperative for
heightened awareness and specialized training to safeguard the
health and safety of younger workers [1].
Safety, as a discipline, aims to minimize the loss of life and
property attributable to accidents as much as possible [2].
Workplace incidents not only affect workers but also have
adverse financial implications for employers. The costs
associated with an accident can manifest in various forms,
including salary expenditures, productivity losses, retraining,
compensation payments, repairs, and medical expenses.
Like any industrial sector, the water bottling industry faces
occupational hazards at various stages, including production,
storage, and distribution. The industry predominantly employs
automated processes, supplemented by some manual handling
and repetitive tasks performed by workers. Consequently, this
environment presents multiple workplace hazards, including
ergonomic challenges, mechanical design issues, physical
activity demands, chemical exposures, and psychosocial
stressors. As a result, factory workers in this sector are more
vulnerable to occupational morbidities and fatalities due to
these heightened workplace risks.
Globally, the International Labor Organization (ILO)
estimates that approximately 2.78 million individuals
succumb annually to occupational diseases or job-related
accidents. Furthermore, around 374 million non-fatal injuries
occur each year, leading to a minimum of four days of work
missed per injury. The economic implications of substandard
workplace safety and health practices account for about 3.94
percent of the global gross domestic product annually [2]. Yet,
International Journal of Safety and Security Engineering Vol. 13, No. 6, December, 2023, pp. 1025-1038
Journal homepage: http://iieta.org/journals/ijsse
1025
the human toll of this frequent adversity is incalculable.
Risk, in this context, is the possibility or likelihood of harm
resulting from exposure to a hazard. However, Kaplan and
Garrick [3] describe risk as uncertainty coupled with potential
damage or loss, while safety is defined as being protected from
possible harm. The Society for Risk Analysis (SRA) [4]
characterizes risk as “The potential for realization of unwanted,
adverse consequences to human life, health, property, or the
environment”. Conversely, risk assessment involves the
identification, analysis, and evaluation of hazards [3].
The risk assessment process is integral to occupational
health and safety management plans, serving to heighten
employee awareness of potential workplace hazards and risks
[5]. This process is methodical and recurring, commencing
with the identification of risks and risk factors capable of
causing harm. It then progresses to the analysis and assessment
of the risks associated with these identified hazards,
culminating in the determination of appropriate measures for
risk elimination or control. The selection of strategies to
minimize or eradicate these risks is contingent upon the nature
of the risk in question [6].
Effective risk management begins with risk assessment.
When a company employs five or more individuals,
conducting and documenting a risk assessment becomes a
legal obligation [7]. In response to this requirement,
companies often develop informative tools to facilitate risk
assessments. According to HSE [8], the fundamental
components of successful risk management systems include
policy, organization, planning and implementation,
performance measurement, and review. The techniques
employed in risk assessment are pivotal in establishing
priorities and setting objectives for the elimination of hazards
and the reduction and control of risks in health and safety
management [9].
1.2 More on the concepts
Comprehending risk assessment necessitates a clear
understanding of the concepts of hazard, risk, and safety. A
hazard is defined as any potential source of harm; it may pose
a threat to people, organizations, or the environment. For
instance, a wet floor constitutes a hazard. Hazards are diverse
and can encompass physical hazards, which are factors
capable of causing harm (like a spill on the floor or constant
loud noise), and chemical hazards, which include harmful
chemical substances in any form (such as cleaning products or
asbestos) [8]. When conducting risk assessment, various
methods are employed to identify hazards and assess their
potential effects [3]. Statistics from social security reveal that
falls constitute the most common type of work injury,
accounting for 28.03 percent of total injuries. This is followed
by incidents involving manual labor tools, which represent
11.9 percent of injuries, and injuries resulting from falling
objects at 9.68 percent. Additionally, the data indicate that
road accidents are the leading cause of injury-related deaths,
responsible for 46.8 percent of total fatalities, followed by
incidents involving explosions, fires, and falls [1].
Risk is defined as the likelihood of the occurrence of a
harmful event and the severity of the resultant harm. For
example, the risk associated with slipping on a wet floor
encompasses both the probability of the slip occurring and the
potential consequences of such an event [9]. The interplay
between probability and consequences can significantly
impact individuals' daily activities, as well as their
professional and personal decision-making processes [10]. An
alternate perspective on risk considers it as the probability that
a hazard will adversely affect individuals, organizations, or the
environment, coupled with the potential outcomes of the
hazard’s occurrence. A risk is deemed low when the likelihood
of the event happening is minimal, and its impact is considered
mild. Conversely, the risk is considered high if there is a high
probability of the event occurring and the potential effects are
severe. It is important to note that while a hazard is a
prerequisite for risk, the presence of a hazard invariably
implies some level of risk [9].
Safety involves determining whether a risk is sufficiently
low to be considered safe or high enough to be deemed
harmful. Safety assessments, which may vary in their
conclusions, can be conducted either individually or by
governmental organizations [9]. Risk assessment, therefore, is
a process enabling safety teams to identify hazards, assess the
likelihood and severity of hazardous events, and then
determine necessary actions. As a distinct concept, risk
management is a dynamic, continuous process encompassing
hazard identification, analysis, mitigation measures, and
response to risk factors. While risk assessment is focused on
detecting hazards and analyzing all potential hazards and risks
in the workplace, it is a component of risk management.
Essentially, risk assessment involves hazard identification,
analysis, and evaluation. The responsibility for hazard
identification typically lies with managers and senior
employees who possess knowledge about various workplace
hazards and risks. These hazards might include fires, chemical
exposures, data breaches, and other incidents capable of
harming people and property. The associated risks could
pertain to health, safety, or quality. Risk analysis, a crucial part
of risk assessment, delves into the consequences of identified
hazards and their impact on work sustainability. Following this,
risk evaluation involves categorizing risks based on their
severity and likelihood. To facilitate this, risks can be ranked
using a risk assessment matrix.
1.3 Types of risk assessments
In any workplace, the types of risk assessments conducted
should be proportionate to and aligned with the operational
activities being carried out. The choice of risk assessment
method depends on the frequency of occurrence and the
factors that trigger the need for such assessments [7].
Generally, risk assessments can be categorized into two
primary types based on these considerations [4]. The first type
is the standard risk assessment, which is routinely conducted
at regular intervals. This form of assessment is a foundational
element of ongoing safety management, providing a consistent
review of potential risks within the workplace. The second
type, known as dynamic risk assessment, serves to address any
gaps identified in the standard risk assessment. It is typically
implemented when new hazards are introduced or identified in
the workplace, ensuring that emerging risks are promptly and
effectively managed [11].
Standard risk assessment encompasses five prevalent types.
The first is a fire risk assessment, which systematically
evaluates factors related to fire hazards, the likelihood of a fire
occurring, and the potential consequences should one arise
[12]. Manual handling assessments are crucial in sectors like
healthcare, agriculture, manufacturing, and construction,
recognized for high-risk manual handling activities due to
their frequency and nature. Display Screen Equipment (DSE)
1026
assessments are required in workplaces where employees use
computers, LCDs, etc. [5], and are also applicable to tablets,
smartphones, and laptops [7]. COSHH (Control of Substances
Hazardous to Health) assessments focus on hazards and risks
from hazardous substances in the workplace. Lastly, complex
risk assessments are necessary for larger-scale systems, such
as nuclear power plants or meteorological systems, which
involve intricate interactions between mechanical, electronic,
nuclear, and human elements [11]. In contrast, dynamic risk
assessment is utilized to address any gaps left by standard risk
assessments or in response to the introduction of new hazards
in the workplace [11]. Dynamic risk assessment involves
analyzing workplace risks and hazards and implementing
controls to reduce or eliminate them. However, sudden
changes in the work environment, such as the introduction of
new hazards, necessitate this form of assessment [12].
Dynamic Risk Assessments enable safety professionals to
quickly evaluate risks in changing environments, ensuring
continued safe work practices. While standard risk
assessments are prepared in advance, recorded, and regularly
monitored, dynamic risk assessments are conducted on the
spot by individuals as they encounter new environments or
changes within them.
Furthermore, the implementation of a dynamic risk
assessment does not negate the necessity for a standard risk
assessment. Rather, the dynamic risk assessment serves as a
complement to the standard risk assessment, addressing any
unforeseen gaps or nuances that the latter may not have
anticipated [11]. It is incumbent upon those responsible for
safety to conduct a dynamic risk assessment prior to
encountering any new situation or environment. Essentially, as
circumstances evolve, it is imperative for the safety team to
continually reassess risks and hazards, adapting their approach
to ensure the utmost safety and hazard mitigation.
1.4 The implementation of risk assessment
The risk assessment process is designed to evaluate the
likelihood and severity of potential harm. This process
encompasses five sub-processes: hazard identification, risk
analysis, risk evaluation, risk control, and assessment review,
with the provision for reassessment if necessary. Hazard
identification involves scrutinizing processes and work
procedures to identify conditions that could potentially harm
people. In the stages of risk analysis and risk evaluation,
assessors determine the probability of each hazard occurring
and the severity of its potential consequences. Risk evaluation
also facilitates the ranking of hazards based on their risk
ratings. Risk control, on the other hand, focuses on identifying
measures to eliminate hazards, either by preventing their
occurrence or, if that is not feasible, by controlling the risk.
This stage includes documenting the findings of the
assessment. The final stage involves revising control plans,
making improvements, and implementing administrative
actions to ensure a healthy and safe working environment [6].
The ISO-IEC 31010:2019 standard outlines the steps involved
in hazard identification and risk assessment. Published as a
dual-logo standard with ISO, it offers guidance on the
selection and application of various techniques for assessing
risk in diverse situations. These techniques aid decision-
making in scenarios with uncertainty, provide insights about
specific risks, and are part of a broader risk management
process. The standard provides a framework for organizations
to identify, assess, and manage risk, applying to various
contexts and industries. It aims to assist organizations in
making informed decisions about risk management and in
developing risk management strategies tailored to their unique
needs and circumstances [12].
Several categories of risk evaluation methods exist to
estimate individual components of risk accurately, aiming to
reflect reality more effectively. These categories include
qualitative, quantitative, and semi-quantitative risk
assessments. The choice among these types depends on the
specific circumstances and the availability of data. In certain
situations, it is feasible to implement more than one type of
assessment.
QRA is the most prevalent among these types. In QRA,
either an individual or a team can collect the necessary
information to conduct the assessment. This method is
particularly useful when numerical data are scarce or when
resources and records are limited.
QRA is primarily utilized for workplace risk assessments.
In this approach, the experience and knowledge of the assessor
play a pivotal role. The process involves not only reviewing
relevant data but also consulting employees and laborers who
are directly involved in the work activities. This consultation
is critical for making informed decisions about the potential
and severity of risks, followed by categorizing these risks into
levels such as high, medium, or low. A key feature of QRA is
its assignment of numerical values to different levels of risk,
enabling the computation of a risk rating. This rating is
typically calculated as the product of the severity and
likelihood of a given risk. Consequently, QRA is particularly
suited for workplace environments, where it aims to determine
the likelihood of someone being at high, medium, or low risk
of injury. The assessment involves an evaluation of the
severity of potential consequences and the probability of their
occurrence, without relying on quantitative tools. QRA is a
systematic examination of workplace factors that may cause
harm. It facilitates decision-making regarding the adequacy of
existing precautions and controls, and whether additional
measures are necessary to mitigate identified risks [13].
QRA does not inherently involve numerical data, qualitative
expressions are often quantified to estimate the Risk Rating
(RR), which represents the product of severity and potential.
In QRA, numbers are typically assigned to the severity and
likelihood or potential of a consequence, ranging from 1 to 5.
The five levels of severity are categorized as insignificant,
minor, moderate, major, and catastrophic. Similarly, the
likelihood of consequences is classified into five categories:
rare, unlikely, possible, likely, and certain [8].
Constructing a risk assessment matrix involves placing the
likelihood or potential on the abscissa and the severity on the
ordinate. This yields a 5×5 matrix, with each element
representing the product of severity and likelihood. The
magnitude of these elements reflects the risk rating. The
ratings are classified into three categories: low (RR ranging
from 1 to 5), medium (RR ranging from 6 to 12), and high (RR
ranging from 15 to 25). Risks with a high rating necessitate
immediate action, while those with a medium rating may allow
for delayed measures, and a low rating might not require
further action. Ultimately, QRA is descriptive and heavily
relies on the competency and experience of the assessors.
Their expertise is crucial in accurately interpreting and
applying the qualitative data to the risk assessment process,
ensuring that the assessments are reflective of the actual
workplace risks.
Semi-quantitative risk assessment employs a methodology
1027
that combines qualitative and quantitative elements to
articulate the relative scale of risks. This approach utilizes
numerical values, primarily in the form of frequency ranges or
levels of consequence, to provide a more defined assessment
of risk. The use of consequences-likelihood matrices, with
consequences plotted on the x-axis and likelihood on the y-
axis, enables the classification of risks. This classification
leverages expert knowledge, often in scenarios where
quantitative data is limited [13]. The foundational aspect of
semi-quantitative risk assessment is categorical labeling. This
process involves describing the probability, impact, and/or
severity of a risk as Very Low, Low, Medium, High, or Very
High. Alternatively, a scaling system such as A-F may be used,
with each term having a clear and distinct definition [14].
In the semi-quantitative risk assessment approach, various
scales are employed to characterize the likelihood of events
and their consequences or severities. This method does not
necessitate precise mathematical data for analyzing
probabilities and their outcomes. Instead, the goal is to
establish a hierarchy of risks relative to their quantification,
identifying which risks require further review without
implying a direct relationship between them.
Conversely, quantitative risk assessment assigns numerical
values to risks based on realistic and measurable data. Rather
than categorizing risks as high, medium, or low, they are
assigned specific numerical values, such as 3, 2, and 1,
although the scale can be broader. This type of risk assessment
is particularly applicable to industries with significant hazards,
such as aviation, chemicals, and nuclear power plants.
Quantitative measurements may encompass a variety of
factors, including hazards associated with equipment,
chemicals, design, and modeling techniques.
Quantitative risk assessment necessitates specialized
instruments and procedures for hazard identification, severity
consequence estimation, and likelihood determination of
hazard actualization. These tools include event trees,
sensitivity analysis, simulation software, and others. The use
of these tools enables a more detailed and precise assessment
of risks, especially in scenarios where high-risk factors are
present.
Based on the aforementioned discussion, it can be
concluded that each category of risk assessment—qualitative,
quantitative, and semi-quantitative—has its own set of
advantages and disadvantages. QRA is advantageous in its
speed and ease of implementation, as it does not rely on
numerical measurements. This simplicity allows for prompt
execution. However, it is inherently descriptive and heavily
reliant on the competency and experience of the assessors. As
a result, there is a degree of subjectivity involved, with the
potential for variability in determining probabilities and
consequences.
In contrast, QRA is more objective and offers detailed
decision-making. However, this method is time-intensive and
can be complex, as quantitative data are often challenging to
Collepals.com Plagiarism Free Papers
Are you looking for custom essay writing service or even dissertation writing services? Just request for our write my paper service, and we'll match you with the best essay writer in your subject! With an exceptional team of professional academic experts in a wide range of subjects, we can guarantee you an unrivaled quality of custom-written papers.
Get ZERO PLAGIARISM, HUMAN WRITTEN ESSAYS
Why Hire Collepals.com writers to do your paper?
Quality- We are experienced and have access to ample research materials.
We write plagiarism Free Content
Confidential- We never share or sell your personal information to third parties.
Support-Chat with us today! We are always waiting to answer all your questions.
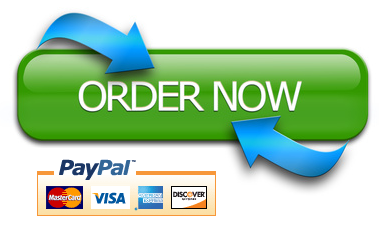