Summarize the report into around
Dedication Acknowledgments Abstract This project focuses on reducing fuel consumption in RTG crane operations in port terminals, applying the Lean Six Sigma methodology with the DMAIC approach. The goal of the project is to optimize operational efficiency and promote sustainability by decreasing the Fuel/TEU indicator by 10% by 2024. To date, the “Define” phase has been completed, establishing the scope and objectives of the project, and the “Measure” phase, where detailed data on fuel consumption and operations of RTG cranes were collected. In the “Analyze” phase, the main areas of inefficiency and possible causes of variability in fuel consumption were identified. Future work involves further improving the already implemented improvement strategies, such as optimizing crane allocation and improving operating procedures. In this sense, while initial results are promising and they lead to a steady decrease of about 5-7% in fuel consumption, further work is still necessary to optimize the different parameters and hence reach the goal of 10% fuel consumption reduction. Keywords Lean Six Sigma, RTG cranes, fuel efficiency, port operations, DMAIC methodology List of figures Figure 1. SIPOC diagram Figure 2. Temporal variation of diesel consumption since 2023 Figure 3. Temporal variation of the number of 20 foot containers transported in 2024 Figure 4. Temporal variation of the number of 40 foot containers transported in 2024 Figure 5. Temporal variation of the number of moves since 2023 Figure 6. Temporal variation in the number of TEU transported since 2023 Figure 7. Temporal variation of the fuel efficiency in terms of the fuel consumption per move Figure 8. Temporal variation of the fuel efficiency in terms of the fuel consumption per TEU Figure 9. Ishikawa digrama for the operation of the RTG cranes and their impact on fuel consumption Figure 10. General view of the port Figure 11. RSTG terminal 1 (30 RTG cranes) Figure 12. RSTG Terminal 2 (12 RTG cranes) Figure 13. RSTG terminal 3 (8 RTG cranes) List of tables Table 1. Project charter Table 2. Descriptive statistics for weekly measures during 2024 Introduction The Lean Six Sigma method is a structured work approach and methodology that focuses on reducing process variability and thus minimizing defects in products and services that go beyond specifications. As a management system, it focuses on users, processes and data management using statistical and problem-solving tools (Kurnia & Purba, 2021). It is based on the use of the DMAIC methodology, which focuses on creating processes with fewer defects and deviations that are usually the causes of food production-related waste, being able to apply this methodology when the variables are multiple and even when cause and effect relationships are not evident (Trubetskaya et al., 2023). These steps are defined based on Trubetskaya et al. (2023): • • • • • Define. Approach the problem and focus on its resolution, collect the voice of the organization and set the indicators that will allow the achievement of the objectives. Measure. Analysis of the information collected by analysing the selected processes in order to measure the indicators. This allows the development of descriptive performance statistics in the real work area. Analyze. Use Lean and Six Sigma tools simultaneously to provide the best results for process improvement and efficiency. Relationships are established between the performance of the processes and their respective inputs, establishing the assumptions and in turn designing a work plan to establish the necessary improvements. Improve. The improvements are implemented by complying with the actions and improving the levels obtained in the initial indicators. The final analysis is the calculation of the new capacity and the new sigma value of the processes. Control. In the last phase we proceed to automate the controls established with that of its durability over time, the purpose being the self-sustainability of the indicators with the improvements made. The RTG fuel consumption reduction project represents a strategic effort aimed at optimizing costs through the significant reduction of fuel use in port and container terminal operations. The considerable variability in fuel consumption levels of RTG equipment currently results in operational inefficiencies and increased costs. These issues have a great impact on the overall performance and profitability of our RTG equipment. In response to this problem, the scope of the project encompasses a holistic approach, starting with the strategic assignment of locations for RTGs, providing hands-on mentoring for equipment operators in the field, and culminating in a targeted improvement of the terminal layout. The overarching goal is to achieve a substantial reduction in fuel consumption while maintaining operational effectiveness. A strategic goal of decreasing the Fuel/TEU indicator by the RTG cranes operating at the Red Sea Gateway Terminal Company at Jeddah Islamic Port (Saudi Arabia) by 10% by 2024 has been settled to achieve these objectives. The project team consists of SVD managers, planning manager, planning strategist Khaled Alghamdi, terminal operations optimization manager, controllers and PEX team. Khaled Alghamdi leads the project as its champion, while Badr Alotaibi acts as a sponsor, supporting the initiatives and resources needed for the successful implementation of the project. The operational and financial impact of the project is expected to be significant. Operationally, it is planned to reduce crane downtime and unnecessary movements, improve standard operating procedures for RTGO and develop the communication process between RTGO and supervisors or operational team. From the financial point of view, it seeks to reduce the costs associated with fuel consumption and increase the useful life of the engines, which would result in significant savings and an improvement in the sustainability of the operations in the long term. Literature review The Lean Six Sigma methodology stands out for its effectiveness in improving efficiency and minimizing waste, which makes it a valuable tool to face challenges such as reducing fuel consumption. This efficiency is complemented by additional research that addresses from optimization in the use of fuel, heat recovery in biomass equipment, the use of start-up systems- stop in vehicles to reduce fuel consumption and CO2 emissions (Kurnia & Purba, 2021). In addition, innovations in the design of industrial processes such as the production of formiate through the electro-production of CO2, the calibration of climatic equipment, and energy planning to reduce consumption in industrial processes, highlighting the importance of energy efficiency and reducing the carbon footprint (Kurnia & Purba, 2021). These studies, along with research on the use of artificial intelligence to optimize combustion efficiency and energy efficiency improvements in management that offer significant returns, as well as the evaluation of energy performance in vehicles, demonstrate the wide applicability of Lean Six Sigma for environmental and efficiency improvements (Kurnia & Purba, 2021). Applying the Lean Six Sigma methodology in reducing fuel use and improving energy efficiency is an effective strategy, as demonstrated by several case studies in different industries. For example, in the Irish dairy industry, the implementation of an ISO 50001 energy management system using Lean Six Sigma resulted in a significant reduction in energy consumption, demonstrating how the principles of continuous improvement can be applied to optimise energy use and reduce source CO2 emissions (Trubetskaya et al., 2022). In addition, in the aviation sector, the application of Lean Six Sigma in GE90 engine tests led to a halving of fuel consumption, from 20,000 gallons to 10,000 gallons, which also generated significant savings and a reduction in greenhouse gas emissions source (EPA, 2016a). Similarly, in the oil and gas industry, the adoption of Lean Six Sigma has improved operational efficiency and production, optimizing processes such as oil rig movements (Yoon, 2020). The optimization of vehicle fleets using the Six Sigma model has also been shown to be effective in reducing costs and increasing fleet availability, demonstrating the versatility of Six Sigma to optimize the use of resources in various applications (Stanivuk et al., 2020) . The implementation of Lean in companies such as Apollo Hardwoods Company and Baxter Healthcare Corporation has led to innovations that use less natural resources and energy, while offering improvements in water management and waste reduction (EPA, 2016b; EPA, 2016c). At Boeing, the adoption of Lean initiatives has resulted in significant improvements in resource productivity and the elimination of unnecessary packaging materials, reducing the use of chemicals by aircraft (EPA, 2016d; EPA, 2016e). Companies such as Canyon Creek Cabinet Company and Columbia Paint & Coatings have achieved significant annual economic savings and reductions in the use of hazardous materials, VOCs and waste, thanks to the implementation of process improvements (EPA, 2016f). Lean chemical management at Goodrich Aerostructures and process improvement initiatives at JEA have resulted in substantial cost savings and reductions in energy use as well as waste generation (EPA, 2016g). Lockheed Martin and Plymouth Tube have implemented Lean techniques to reduce hazardous waste and optimize the use of lubricants, leading to annual savings and costly waste stream disposal (EPA, 2016h; EPA, 2016i). These examples highlight how Lean Six Sigma is not only an effective strategy for improving operational efficiency and reducing costs, but also plays a crucial role in promoting sustainable practices and reducing environmental impact across a wide range of industries. The adoption of Lean Six Sigma and DMAIC as a systematic method for reducing fuel consumption is justified by its structured and data-based approach, which allows identifying and eliminating inefficiencies in any process, resulting in significant improvements in both energy efficiency and environmental sustainability. The evidence accumulated through these studies reinforces the selection of Lean Six Sigma as an ideal strategy to address complex problems of efficiency and sustainability in a wide range of industries. This methodology has thus been selected as an ideal systematic method to address the problem of reducing fuel consumption, leveraging its structured and data-based approach to identify and eliminate inefficiencies in any process. Research methodology The DMAIC methodology is the central pillar of our approach to address and solve the problem of excessive fuel consumption in RTG cranes in our port operations. As mentioned above, this methodology has been selected because it offers a systematic and rigorous strategy through a cycle of continuous improvement. This tool derives from a proven tool derived from Lean Six Sigma principles and focuses on reducing process variability and eliminating defects. In this way, it allows identifying critical areas for improvement, implementing effective solutions and evaluating the effectiveness of such solutions from a structured approach. Below, we detail how each DMAIC phase specifically applies to our goal of reducing TEU fuel consumption by 10% by 2024. Define: In this phase, we addressed the problem by clearly identifying and delineating the factors that influence the fuel consumption of RTG cranes in port operations. This process begins with collecting the voice of the customer and the voice of the process to fully understand the expectations and operational requirements. We then establish key performance indicators (KPIs) that will allow us to measure the success of the project, such as the TEU fuel consumption. Measure: During the Measurement stage, we focused on the collection and analysis of existing data on the fuel consumption of RTG cranes and created a reliable measurement system to monitor the current performance. The variables monitored included the amount of diesel used, the Twenty-foot equivalent unit (TEU), the number of 20 foot and 40 foot containers, the number of times that the container was loaded, unloaded, or repositioned (moves), and the relationships between the fuel consumed and the moves and between the fuel consumed and the TEU. These measurements were done on a weekly basis since 2023. Analyze: The data collected from the measure phase were analyzed statistically. In this sense, the baseline level for each of these variables was established. Morevoer, the trends in these variables were monitored over time through relevant control charts. Improve: A series of strategies have been designed to improve the performance of RTG cranes. The goal of these strategies is that of addressing the issues identified during the previous stages. Their optimization is currently under work to reach the goal of 10% fuel consumption reduction in 2024. Control: The impact of the implemented strategies on the consumption of fuel by RTG cranes will be monitored by evaluating if they decrease the fuel consumption, compared to the baseline levels monitored during the measure phase. Results and discussion Recognizing the high potential of the DMAIC methodology to solve complex process problems, we have decided to apply it in our effort to address the variability of fuel consumption of Gantry Cranes on Tires (RTG), an operational inefficiency that is increasing our costs significantly. In the Definition phase of the project, we have clearly delineated the scope of this initiative: reduce the Fuel/TEU indicator by 10% by 2024. With a committed team, led by Khaled Alghamdi and supported by project sponsor Badr Alotaibi as outlined in the project charter shown in table 1, we have established a solid foundation and defined achievable goals. Our direction is firm, and our goal is set; we are now ready to proceed with the subsequent stages of Measure, Analyze, Improve and Control, confident that these actions will lead us to meet our fuel optimization goals. Table 1. Project charter 1. General Project Information Project Name: Reduce the Fuel Consumption of the Rubber-Tired Gantry Cranes (RTG) Project Sponsor: Bradt Alotaibi Project champion: Khaled Alghamdi 2. Project Team Operation director: Bradt Alotaibi Team Members: SVD managers, Planning Manager, Planning Strategist, Khaled Alghamdi, Terminal Operations Optimization Manager, Controllers, PEX Team 3. Stakeholders (e.g., those with a significant interest in or who will be significantly affected by this project) Port terminal operators Shipping and transport companies Port terminal managers 4. Project Scope Statement Project Scope The project aims to significantly enhance the efficiency of RTG (Rubber-Tired Gantry) fuel consumption through a comprehensive optimization strategy. The scope encompasses a holistic approach, starting with the strategic assignment of locations for RTGs, providing hands-on mentoring for equipment operators in the field, and culminating in a targeted improvement of the terminal layout. The overarching goal is to achieve a substantial reduction in fuel consumption while maintaining operational effectiveness. Objectives (in business terms) To reduce the Fuel/TEU by 10% in 2024 Deliverables Periodic progress reports 5. Communication Strategy Communication will be done through both e-mail and regular meetings of interested team members 6. Sign-off Project Sponsor Project champion Figure 1 shows a SIPOC diagram, which highlights the key suppliers, inputs, processes, outputs, and customers of the present project. As outlined in this diagram, suppliers play a crucial role in the reduction of fuel consumption in RTG crane operations in port terminals. Among these suppliers we find not only the companies that supply diesel fuel, essential for the operation of cranes, but also those in charge of their maintenance, as they ensure that cranes operate efficiently and contribute to reduce unnecessary fuel consumption. The terminal’s operations team, composed of planners and operators, plays a key role in the strategic allocation and operation of cranes, seeking to maximize efficiency and minimize downtime. From the perspective of the inputs, the most relevant variables for the project are the fuel and operational data that allow us to monitor and optimize the use of the cranes, in addition to the maintenance plans ensure their optimal operation. Within the process, the strategic allocation of the cranes and their efficient operation, along with proactive maintenance, are the keys to improving operational efficiency, reflected in the reduction of fuel consumption and the increase of TEUs handled. These improvements benefit not only port terminal operators, who rely on efficient crane operation for their daily operations, but also shipping and transportation companies, which require efficient movement of their containers. Finally, terminal management benefits from maximizing operational efficiency and reducing costs, including fuel consumption, which reinforces the sustainability and competitiveness of port operations. Figure 1. SIPOC diagram The variables monitored during the measure phase to evaluate the performance of the RTG included the following: fuel consumption, number of 20- and 40-foot containers transported by the RTG cranes, TEU, moves, fuel consumption/moves, and fuel consumption/TEU. In our project, “fuel consumption (litres)” refers to the total amount of fuel used by RTG cranes. It represents a critical measure of operational efficiency and economic cost. The variables “20 foot” and “40 foot”, on the other hand, describe the sizes of containers handled by the RTGs. These variables are closely related with the variable “TEU” is the “Twenty Foot Equivalent Unit”. This represents an international standard for measuring load capacity of the containers, where a “40 foot” container is considered as two TEUs. An increase on any of these three variables implies that the RTG crane had done a higher amount of work, hence consuming a higher amount of fuel. The variable “moves” represents the number of times that the RTG was used to load, unload, and transfer of containers within the port, as each of these movements involves fuel consumption. Two relative variables, namely the “litres/moves” and “TEU/moves” metrics, were used to normalize the afore-mentioned variables, as they provide a precise measurement of fuel efficiency by relating the amount of fuel used to either the number of movements or the amount of load handled, respectively. These two metrics provide a deep understanding of the relationship between fuel use and productivity of port operations. To date, we have measured weekly the values of each of these variables from the beginning of the year to establish a baseline and the variability inherent in each, which is essential to identify areas for improvement and monitor progress towards our fuel efficiency goals. The results of such measurements are shown in figures 2-7. The graphs present a comprehensive view of the weekly variability of diesel consumption, container handling and operational efficiency in RTG crane operations over since January 2023. Figure 2 shows the temporal variation of the average amount of diesel consumed per week, observing significant fluctuations in fuel use week by week, indicating possible operational inefficiencies or variations in workload. Figures 3 and 4 show the number of containers of 20 and 40 feet mobilized in 2024, with a generally constant trend for those of 20 feet and a slight decrease for those of 40 feet towards the last weeks. Figure 5 points to “moves”, or container movements, by maintaining a relatively flat line with slight increases, which could reflect a stability in moving operations. Figure 6 shows the variation of TEUs handled, which seems to remain stable, suggesting a direct relationship with the recorded movements. Finally, Figures 7 and 8 compare relative fuel consumption, evidencing a disparity between litres per movement (figure 7) and litres per TEU (figure 8). It is observed that the liters per movement (litres/moves), shown in Figure 7, present a variation with values higher than the metric of liters per TEU (litres/TEU), shown in Figure 8, which shows lower values and a consistency over time. This trend suggests that, while fuel consumption per movement varies, fuel consumption relative to the total amount of TEUs handled remains more constant. This pattern underscores the importance of considering multiple dimensions of efficiency in fuel management and can point to specific areas for improving operational performance. Consistency in the liter/TEU ratio implies that efficiency in terms of the amount of cargo handled per fuel consumed remains stable, which is a positive indicator for terminal operations. Despite the variation, the trendline remained extraordinarily stable in both cases until the implementation of the initial improvement strategies. Figure 2. Temporal variation of diesel consumption since 2023 Temporal variation of 20 foot containers transported in 2024 20 foot containers 25000 20000 15000 10000 5000 0 1 2 3 4 5 6 7 8 9 10 11 Week Figure 3. Temporal variation of the number of 20 foot containers transported in 2024 Temporal variation of 40 foot containers transported in 2024 40 foot containers 60000 50000 40000 30000 20000 10000 0 1 2 3 4 5 6 7 8 9 10 11 Week Figure 4. Temporal variation of the number of 40 foot containers transported in 2024 Weekly average moves Temporal variation of moves 90000 80000 70000 60000 50000 40000 30000 20000 10000 0 Week Figure 5. Temporal variation of the number of moves done since 2023 Temporal variation of TEU Weekly average TEU 140000 120000 100000 80000 60000 40000 20000 0 Week Figure 6. Temporal variation in the number of TEU transported since 2023 Fuel efficiency Average litres/moves 2.50 2.00 1.50 1.00 0.50 0.00 12/5/2022 3/15/2023 6/23/2023 10/1/2023 1/9/2024 4/18/2024 Date Data Linear (Data) Figure 7. Temporal variation of the fuel efficiency in terms of the fuel consumption per move Fuel efficiency 1.40 Average litres/TEU 1.20 1.00 0.80 0.60 0.40 0.20 0.00 12/5/2022 3/15/2023 6/23/2023 10/1/2023 1/9/2024 4/18/2024 Date Data Linear (Data) Figure 8. Temporal variation of the fuel efficiency in terms of the fuel consumption per TEU Table 2 shows a sumary of the key descriptive statistics that will be used to monitor the efficiency of the implemented strategies to reduce fuel consumption. Table 2. Descriptive statistics for weekly measures during 2024 Mean Median Standard deviation Minimum Maximum CV Diesel Liter/ quantity 20 ft 40 ft Moves TEU Moves Liter/TEU 104081 17741 41221 58962 100183 1,771 1,043 102084 17640 38547 55821 94368 1,747 1,032 12522 82790 129499 12,0% 1887 13928 20732 10,6% 5399 34967 49456 13,1% 6895 51036 68213 11,7% 12240 86022 117187 12,2% 0,15 1,51 1,97 8,6% 0,09 0,87 1,16 9,0% According to this table, the average weekly fuel consumption iesel quantity: The average diesel consumed is 104,081 litres, with a median of slightly less than 102,084 litres, suggesting a slightly positively skewed distribution with respect to fuel consumption. The standard deviation is 12,522 liters, indicating that a variability of about 12% in the fuel weekly consumption. This high variability is also reflected in the broad range existing between the minimum (82,790 litres) and the maximum (129,499 liters). An average of 17,741 ft and 41,221 ft containers were moved on a weekly basis. The standard deviations are 1,887 and 5,399 respectively, suggesting more variability in 40-foot container handling. Their coefficients of variation in this case were 10.6% and 13.1%, respectively. The average number of weekly moves were 58,962, with a slightly lower median (55,821). The obtained standard deviation (6,895) suggests a high variability (11.7%). Lastly, the average TEU was of 100,183 with a slightly lower median (94,368). Its standard deviation (12,240) suggests a high coefficient of variation when compared ot the average value (12.2%). It is important to note that that the fuel efficiency measures, obtained by normalizing the consumed fuel with either the moves done or the TEU were far more stable than any of these variables when considered separately. In this regard, the coefficient of variation for the litres/moves was of 0.15 / 1.771 = 8.6% while that of the litres/TEU was of 0.09/1.043 = 9.0%. This result suggests that using these fuel efficiency indices gives a better overview of the actual trends in the consumption of oil, as it compensates for multicollinearity effects between the different variables monitored. The obtained results can help identify areas of inefficiency and design interventions to improve performance in RTG crane operations. For example, the large difference between maximum and minimum diesel consumption suggests that there could be significant opportunities to improve fuel efficiency. In order to understand better how to define such areas for improvement, a detailed analysis of the potential causes was carried out. The key results obtained from such analysis is summarized in the following Ishikawa diagram: Figure 9. Ishikawa diagram for the operation of the RTG cranes and their impact on fuel consumption. The provided Ishikawa diagram is a cause-effect analysis tool that explores factors that could contribute to the problem of fuel consumption in RTG crane operations. On the main axis of the diagram highlights the key areas of “Machine”, “Measurement”, “Man”, “Material”, “Mother Nature” and “Method”, which represent the possible categories of causes that have the highest impact on fuel efficiency. The key causes identified under the “Machine” category include engine life and yard infrastructure issues, suggesting that machine maintenance and the adequacy of the operating environment are crucial for fuel efficiency. The causes under “Measurement” focus on the accuracy of engine readings, movements and diesel, stating that accuracy in tracking and measuring data is vital to understanding and managing fuel consumption. The “Man” category highlights the influence of the human factor, including the skill and practices of RTG operators and controllers, as well as the importance of downtime and effective communication among staff. As for “Mother Nature”, the diagram suggests that external factors such as yard infrastructure or a new construction may influence fuel consumption in this segment of the diagram. Lastly, “Method” refers to the need to review the operating procedures and management strategies of RTG cranes, such as the transfer of RTG from block to block, which can have a significant impact on fuel consumption. Based on the analysis of the results and the Ishikawa diagram provided, the following improvement strategies were developed: • • • Optimization of the Use of Machinery (Machine): Given that the life of the engine is a potential cause of high fuel consumption, we could implement a predictive maintenance program focused on RTG engines. Using data from engine operating hours and diesel meter readings, we can predict when maintenance is required before engines show suboptimal performance, which could reduce fuel consumption and extend engine life. Improved Personnel Management and Training (Man): Idle time and the need to move RTGs from one block to another can contribute to unnecessary fuel consumption. We can design training programs for RTG operators that focus on fuel efficient handling techniques, as well as improving communication between operator and supervisor to optimize machine usage and reduce downtime. Review of Operating Methods (Method): Variability in handling 40-foot containers suggests that we could benefit from a redesign of operating methods. We could analyze yard layout planning and container movement logistics to minimize unnecessary transfers and improve the efficiency of RTG positioning, which could potentially decrease the number of movements required and, therefore, the fuel consumption. These improvement techniques not only aim to address the symptoms of the problem, but also its root causes, as reflected in the Ishikawa diagram. By focusing on these critical aspects and considering fuel efficiency indices that show less variability, more effective interventions can be developed that result in a more efficient and sustainable operation of RTG cranes. To verify their effectiveness in addressing the poor fuel efficiency, additional measurements will be necessary to verify whether there was a real increase in the fuel efficiency indices from the current baseline level. The results obtained until now after the implementation of the afore mentioned strategies have been quite promising, as we observed a gradual decrease in fuel consumption between 5 and 7% since these strategies were firstly implemented. However, additional work is required to reach our target goal of reducing the fuel consumption by 10% by the end of 2024. Conclusion and future work This study has successfully applied the Lean Six Sigma methodology and the DMAIC approach to identify significant opportunities for reducing fuel consumption in RTG crane operations. The analysis phase has revealed the presence of significant variability in fuel consumption, underlining the need for targeted interventions to improve operational efficiency and sustainability. Through meticulous data collection and analysis, the foundations have been laid for an informed and strategic implementation of improvements, with the goal of achieving a 10% reduction in the Fuel/TEU indicator by 2024. The path towards the implementation of improvement strategies represents an opportunity to significantly transform RTG crane operations, towards greater efficiency and sustainability. Some of the key steps to follow in the future include: 1. Implementation of Improvement Strategies: It is necessary to optimize the implemented strategies to meet the 10% fuel consumption reduction goal. However, the results obtained so far are promising, as the fuel consumption has decreased by 5-7% since their implementation. 2. Continuous Monitoring and Evaluation: Establish a continuous monitoring system to assess the impact of strategies implemented on fuel consumption and adjust tactics as necessary to ensure that reduction targets are met. 3. Culture of Continuous Improvement: Foster an organizational culture that values continuous improvement, innovation, and sustainability, through continuous training and the empowerment of staff to identify and implement improvements in their areas of work. Effective implementation of these strategies will not only contribute to reducing fuel consumption and improving operational efficiency, but will also strengthen the position of the port terminal as a leader in sustainability and environmental responsibility in the sector. References Environmental Protection Agency. (2016a, November 30). General Electric: Peebles, Ohio. EPA. Retrieved from https://19january2017snapshot.epa.gov/lean/generalelectric-peebles-ohio_.html Environmental Protection Agency. (2016b, November 30). Apollo Hardwoods Company. EPA. Retrieved from https://19january2017snapshot.epa.gov/lean/apollo-hardwoods-company_.html Environmental Protection Agency. (2016c, November 30). Baxter Healthcare Corporation. EPA. Retrieved from https://19january2017snapshot.epa.gov/lean/baxter-healthcare-corporation_.html Environmental Protection Agency. (2016d, November 30). Boeing Everett. EPA. Retrieved from https://19january2017snapshot.epa.gov/lean/boeingeverett_.html Environmental Protection Agency. (2016e, November 30). Boeing Auburn Machine Fabrication. EPA. Retrieved from https://19january2017snapshot.epa.gov/lean/boeing-auburn-machinefabrication_.html Environmental Protection Agency. (2016f, November 30). Canyon Creek Cabinet Company. EPA. Retrieved from https://19january2017snapshot.epa.gov/lean/canyon-creek-cabinetcompany_.html Environmental Protection Agency. (2016g, November 30). Goodrich Corporation. EPA. Retrieved from https://19january2017snapshot.epa.gov/lean/goodrichcorporation_.html Environmental Protection Agency. (2016h, November 30). Lockheed Martin. EPA. Retrieved from https://19january2017snapshot.epa.gov/lean/lockheedmartin_.html Environmental Protection Agency. (2016i, November 30). Plymouth Tube Company. EPA. Retrieved from https://19january2017snapshot.epa.gov/lean/plymouthtube-company_.html Kurnia, H., & Purba, H. (2021). A systematic literature review of lean six sigma in various industries. Journal of Engineering and Management in Industrial System, 9(2), 1 12. https://doi.org/10.21776/ub.jemis.2021.009.002.3 Stanivuk, T., Gvozdenović, T., Žanić Mikuličić, J., & Lukovac, V. (2020). Application of six sigma model on efficient use of vehicle fleet. Symmetry, 12(5), 857. Trubetskaya, A., McDermott, O., & McGovern, S. (2022). Implementation of an ISO 50001 energy management system using Lean Six Sigma in an Irish dairy: a case study. TQM Journal, 35(9), 1–24. https://doi.org/10.1108/TQM-08-2022-0252 Yoon, D. (2020). The application of Lean Six Sigma in oil & gas. The Application of Lean Six Sigma in Oil & Gas. Retrieved from https://blog.kainexus.com/improvement-disciplines/six-sigma/the-applicationof-lean-six-sigma-in-oil-gas Appendix: Eagle – eye view of the Red Sea Gateway Terminal Company at Jeddah Islamic Port (Saudi Arabia) Figure 10. General view of the port Figure 11. RSTG terminal 1 (30 RTG cranes) Figure 12. RSTG Terminal 2 (12 RTG cranes) Figure 13. RSTG terminal 3 (8 RTG cranes)
Collepals.com Plagiarism Free Papers
Are you looking for custom essay writing service or even dissertation writing services? Just request for our write my paper service, and we'll match you with the best essay writer in your subject! With an exceptional team of professional academic experts in a wide range of subjects, we can guarantee you an unrivaled quality of custom-written papers.
Get ZERO PLAGIARISM, HUMAN WRITTEN ESSAYS
Why Hire Collepals.com writers to do your paper?
Quality- We are experienced and have access to ample research materials.
We write plagiarism Free Content
Confidential- We never share or sell your personal information to third parties.
Support-Chat with us today! We are always waiting to answer all your questions.
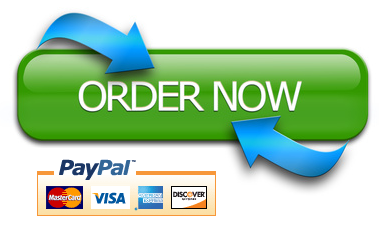