Case Study: Implementing SAP for a Strategic Transition
CASE STUDY III-6 BAT Taiwan: Implementing SAP for a Strategic Transition We needed a new system to support the new business model. A/P and A/R had never been done in Taiwan before, and the timeline was very short. We told them SAP is not new to Asia, and if it works in operating companies similar to ours (like Singapore) there is no reason why it should not work for us. Furthermore, the integrated information derived from the SAP system is going to help make our jobs more efficient and meaningful. There was a huge buy-in. —Mr. Ma, BAT Taiwan Country Manager Very few of our people had any experience in actually using an ERP system; they didn’t have an integrated system view of things. So we depended a lot on the proven template. As a team we said there should be minimal, minimal changes to the template. We don’t want to change the system and get away from those embedded best practices. —Mr. Lee, Project Co-Lead, BAT Taiwan The Asia Pacific Regional IT Manager, Mr. Ponce, was reflecting on the recent SAP implementation in Taiwan. The project marked an important business transition for the Taiwan market, and it also represented a big victory for insourcing an SAP implementation at BAT. What were the important lessons from the implementation approach and management of this project? How could they be amplified as best practices to other parts of the Asia Pacific region and BAT as a whole? Company Background British American Tobacco (BAT) is a 99-year-old company in the tobacco industry that has grown to be one of the top Copyright © 2003 by C.V. Brown and I. Vessey. This case was prepared for class discussion rather than to illustrate either effective or ineffective handling of an administrative situation. Personal names have been camouflaged at the request of British American Tobacco management. The authors are grateful to all of the BAT managers who were interviewed by the authors for this study. 484 three global players through organic growth and acquisitions. Formerly B.A.T. Industries, it spun off its financial services business in 1998 and merged with the global cigarette company Rothmans International in 1999. BAT’s local and international brands are sold in six world regions: Africa, America Pacific, Asia Pacific, Europe, Latin America, and Mesca (Middle East and Central Asia). A seventh division, STC (Smoking Tobacco and Cigars), is a global division operating in more than 100 countries. Corporate headquarters for BAT is based at Globe House in London. The profit centers are end markets, typically at the country level. Small- to medium-sized end- markets typically report into an area cluster, a self-sufficient management unit led by an area director. An end market is headed by a country manager who reports to an area director, and each area director reports to a regional director. For example, the Asia Pacific region has five management units: Asia Pacific North (APN), Asia Pacific South (APS), Malaysia, Australasia, and Indonesia. BAT Taiwan is part of the APN management unit, which also includes Hong Kong, The People’s Republic of China, and Macau. The country manager for Taiwan has a report line to the managing director for APN, who is also the country manager for China. The APN offices are based in Hong Kong. BAT Taiwan BAT Taiwan is a branch office of BAT Services, Ltd., UK (BATUKE), with responsibilities for trade and brand marketing. After the tobacco market in Taiwan was liberalized in 1987, imported cigarettes were allowed to be sold via local agents. Initially, BAT brands were sold in Taiwan by Brown & Williamson and BATUKE through different distributors. Beginning in 1992, all Brown & Williamson’s brands were sold through the BATUKE network worldwide. As a result of this global initiative, the importation and distribution of all BAT brands in Taiwan was consolidated, with China Merchants, Ltd., being appointed as the sole importer/distributor for Taiwan. In 1999, the BATRothmans merger resulted in another realignment. Rothmans used a local agent, Taiwan International Tobacco Case Study III-6 • BAT Taiwan: Implementing SAP for a Strategic Transition 485 Old Tax Law New Tax Law 1) Import duty levied 27% of CIF (import) price Monopoly tax at NT$830 per 1,000 sticks of cigarettes (mille) 2) Excise tax @ NT$590 per 1,000 sticks 3) Health tax @ NT$250 per 1,000 sticks 4) Value added tax (VAT) @ 5% of consumer price EXHIBIT 1 Tax Law Change in Taiwan Company, as its sole distributor. In April 2000, both distributors were merged and now operate under a new corporate entity known as Concord Tobacco Company. The Rothmans merger also resulted in a more progressive portfolio of brands being available to the BAT Taiwan market. Prior to the merger, BAT’s major brand was SE555, but its 2.5-percent market share was declining due to its older consumer profile. After the merger, the BAT market share was slightly boosted from 4.9 percent to 5.3 percent, and the spend focus was shifted to Dunhill, an ex-Rothmans brand, which was more appealing to younger adults.1 The Taiwan management team also rationalized its brands’ stock keeping units (SKUs) to improve its marketing focus and use of resources. Taiwan has more than 70,000 retail outlets, of which about 4,000 outlets are under five large convenience store chains: 7-11 (about 2,600 outlets), Family Mart (about 1,000), Circle K, Hi Life, and Niko Mart. These five large chain stores are still growing at a rapid pace, at the expense of the independent “mom and pop” stores and “beetle hawkers,” and currently account for 43 percent of BAT’s volume. Taiwan’s business environment has also been undergoing some major changes due to major bilateral negotiations in preparation for entry into the World Trade Organization (WTO). To provide a more level playing field for international tobacco companies, the Taiwan Tobacco and Wine Monopoly will have to be dissolved. Two new laws relating to the new administration and taxation of tobacco products were passed in April 2000, but have yet to be enforced, pending Taiwan’s accession—which has been delayed by the deferment of China’s entry. The legislated change in Tobacco Tax legislation from a specific tax per 1 The launch of Dunhill 1mg in July 2000 contributed to the growth of the Dunhill brand family by 170 percent in 2000. mille to a mixed tax regime will have significant impacts on pricing, market size, and profitability. (See Exhibit 1.) In the face of these changing market dynamics, and the BAT-Rothmans merger, BAT Taiwan commissioned Bain Consulting to do a full market potential study, to assess the size of the market opportunities and to identify the investment opportunities. This study identified Taiwan as one of the key profitable growth markets in the Asia Pacific region. It also highlighted various strategic options to pursue in order to realize BAT potential in this market: Besides a higher level of investment behind its “drive brand” (Dunhill), a change in business model would be necessary to grow the business and to reap supply-chain savings. Under the new business model, Taiwan would be directly importing its own products and selling directly to key accounts (e.g., big five convenience chains) and its distributor, who would also focus on direct store delivery, as opposed to selling only to the wholesale trade as it had in the past. The plan was to begin direct importing by January 1, 2001. The direct-sales operation would be piloted first in Taipei and then rolled out to the rest of Taiwan sometime before mid-year 2001. The IT Function at BAT The information technology (IT) function within BAT mirrors the overall company structure. The global CIO is located at Globe House and has direct reports with responsibilities for IT infrastructure, IT service delivery, e-business and business system initiatives, and IT people and processes. Under the global CIO, there has been an increased emphasis on global strategies to help reduce the costs of implementing integrated IT solutions and ongoing IT service delivery. For example, the newly appointed head of business integration at Globe House 486 Part III • Acquiring Information Systems has global responsibilities for IT standardization and consolidation initiatives. BAT currently delivers IT services via three data centers geographically located in Europe (Hamburg, Germany), North America (Macon, Georgia), and Asia Pacific (Kuala Lumpur, Malaysia), and are governed by regional management. All three data centers now operate under a shared services model: by consolidating IT operational support functions at the regional level, economies can be achieved, and these cost savings contribute to the profitability of the BAT end markets that purchase their IT services via a chargeback arrangement. Europe was the first region to extend the shared services concept beyond data center operations to include application services: In 1997 an Enterprise Center of Excellence (ECoE) began to offer hard-to-find SAP expertise to northern European countries for their R/3 implementation projects. Today the ECoE is also providing SAP services for Latin America. In the Asia Pacific region, a data center (APDC) was established in Technology Park, Malaysia, in early 1999. Since that time, the APDC has evolved into a shared services organization (APSS) that combines two business streams: a data center and a competency center (center of excellence) for SAP. Personnel with SAP and other IT skill sets are readily available in Malaysia at a cost quite low compared to the other markets, due in part to early SAP installations in the oil and gas industries and recent government incentives for economic growth in high-technology industries. While the data centers/shared services units are providing support for shared business system solutions, IT organizations that exist at each management unit are responsible for managing the use of IT for their respective end markets. These responsibilities include identifying business requirements, identifying IT solutions, building business cases for IT projects, and managing support services (including local, shared, and outsourced services). For example, APN has an IT organization based in Hong Kong with responsibilities covering all the end markets in APN, including China, Hong Kong, and Taiwan. The smaller end markets typically operate with very few IT resources of their own but share resources from the management unit center. For example, BAT Taiwan only has one IT technical support resource onsite for desktop and LAN support, who has a dotted-line report to the IT organization for APN. New Computer Systems for Taiwan: The ERP Choice The new business model for BAT Taiwan created a need for a new computer system for functions and processes not previously performed. The Taiwan end market needed to have its own accounts payable and accounts receivable systems because these functions had previously been handled by BAT U.K. It also needed a system to support direct selling and inventory management for multiple sales channels, not just for a single distributor. Two ERP platform standards had been prescribed for all BAT solutions by 1998: SAP R/3 and Sage Tetra CS/3. The Sage system was selected for less complex, smaller operations that did not need the functionality of SAP and that required a low-cost ERP solution. SAP R/3 was initially viewed as the standard solution for larger, more complex BAT markets only, because it had proven to be a very expensive system to implement and maintain. However, because the Sage system did not scale well, it was no longer viewed as the best solution for BAT organizations in rapidly growing markets. In mid-1999, for example, the former head of IT for APN (now the Asia Pacific Regional IT manager) had put an ERP implementation for the Hong Kong end market on hold because of the weaknesses of both standard options: CS/3 was not viewed as a sufficiently robust system for the Hong Kong market, but the costs of an SAP solution at that time appeared astronomical. Although Globe House sets strategy and dictates the standard IT platforms, each end market chooses which ERP platform standard to implement, as well as when to implement it. During 1999 and the first six months of 2000, however, several BAT regions had gained much more expertise in implementing both ERP platforms. Some of these implementations were brought forward to achieve Y2K compliance. Other projects were undertaken as part of data integration initiatives for the Rothmans merger: Rothmans brands were transferred to BAT (according to local government restrictions) and BAT’s processes and standard systems were adopted for all operations.2 Within the Asia Pacific region, SAP R/3 projects had been carried out in Australia, Malaysia, and Singapore. Malaysia and Singapore were originally implemented based on the Symphony template; following the merger with Rothmans, however, the Malaysian implementation was changed significantly, and it is now regarded as using a different template. Australia is currently using a BAT SAP system for manufacturing, and a Rothmans SAP system for sales. Hence, the Asia Pacific region is currently using three different SAP R/3 templates to satisfy area needs. Many of these projects had been done with Andersen Consulting (now Accenture) as the implementation partner, some using SAP’s rapid implementation methodology (Accelerated SAP or ASAP). Because of the success of these projects and growing pressures for common data standards, it was 2 Some of Rothmans’ business units had implemented SAP, and other business units were using BPCS on an AS/400 platform. Case Study III-6 • BAT Taiwan: Implementing SAP for a Strategic Transition 487 expected that SAP would become the solution for all end markets over time, if it could be implemented at a reasonable cost. When reviewing the APSS model for implementing SAP, we found that the difference in total cost of ownership between CS3 and SAP became insignificant if we use the common configuration approach. Rather than taking an interim solution for cost reason, it’s more effective for us to commit a marginally higher investment and advance directly to the endgame solution— which is SAP. —Head of IT, APN In July 2000, a two day study of the SAP project for Taiwan was conducted by the APSS Applications Manager for SAP with a team that had representatives from APN, BAT Australia, BAT Singapore, and APSS. The outcome was a high-level system specification document for implementing SAP R/3. The recommendation was that R/3 modules for sales and distribution (SD), materials management (MM— purchasing and inventory management), financials (FI including fixed assets), and controlling (CO including profitability analysis) be implemented in two phases. Phase 1 would support direct importing and distribution to one customer (a former distributor) and would be operational by January 1, 2001. Phase 2 would support direct sales and distribution to key accounts and be operational within six months later. Selecting an IT Partner Although APN IT could provide project management expertise as well as PC desktop and LAN support, it had no SAP R/3 expertise. An implementation partner with functional and technical SAP experience was therefore needed. Further, Taiwan needed a contract for IT services with a BAT global data center to host the SAP application as well as a contract for ongoing application maintenance: IT resources would need to be contracted for periodic system requests such as new reports, as well as for the periodic software upgrades provided by SAP. Following the high-level study, both the European and the Asia Pacific shared services organizations were invited to submit proposals for Taiwan’s R/3 implementation as well as ongoing operations and support. Taiwan would then select the best proposal based on the R/3 template and other considerations. The European shared services groups already provided computer support for BAT Taiwan as a user of SAP financials for the BAT U.K. operations. Because Taiwan had experienced the European data center’s high-quality operational support firsthand, continuing to work with this data center was a clear option. In addition, the SAP Center of Excellence in Europe was a viable partner for the R/3 implementation project. The SAP application services group that was part of APSS was a newer group, but had played a part in the other SAP implementations in the AP region. APSS had also been running SAP applications for Australia, Malaysia, and Singapore for more than 16 months at the time of the Taiwan proposal, so APSS also had a proven track record as a regional data center for SAP. Although Andersen Consulting (now Accenture) had been the implementation partner on a number of BAT R/3 implementations for the AP region, such as those in Australia and Singapore, R/3 project costs using an external implementation partner had been quite expensive. For a new, still small, Taiwan end market, project costs were a very important consideration, so the decision was made to not request a bid from an external consulting firm. In addition, a regional BAT partner would be more knowledgeable about BAT business processes and existing BAT templates for SAP implementations. Proposals were received from the shared services organizations in Europe (EDC and EcoE) and the Asia Pacific (APSS). The decision was made to go with APSS for the R/3 implementation, as well as for SAP hosting and ongoing support, for a number of reasons. First, the proposals from both Europe (EcoE) and APSS were quite similar with respect to implementing R/3. Although the European shared services group had more extensive SAP implementation experience, APSS had recently used a template (code-named “Symphony”) for an SAP implementation with a similar business model in BAT Singapore. Thus, there was high confidence in the SAP functional and technical expertise in the AP region. Second, for the ongoing operations and maintenance roles, APSS had two major advantages over the EDC: lower personnel costs in the AP region compared to Europe and the same time zone. By mid-2000, the annual operational costs at APSS for hosting an SAP R/3 user were U.S.$3,500, and were expected to drop further in 2001. BAT Taiwan would not have to purchase the SAP software licenses, which would be held by APSS. BAT Taiwan saves a lot of time and effort by letting APSS purchase and own the licenses and we only pay a monthly fee. We don’t have to track the licenses as assets, manage maintenance contracts and payments, process procurement and track global pricing policies and terms. We also do not have to worry about selling excess licenses when the number of users comes down. —Head of IT, APN 488 Part III • Acquiring Information Systems It does not matter where the support group sits. What is crucial is the skill competencies, at the right price, in a politically stable region. Since we’re using standard BAT operations, the quality aspect is assured. So cost and support capability become the most critical. —Mr. Ma, BAT Taiwan Country Manager Because Taiwan was in the same time zone as the APSS organization, its people would be able to communicate more easily about their support needs with the shared services group in APSS than with the shared services group located 7 hours away in Europe. There were also some “natural synergies” with APSS that would help with communications: Taiwan, unlike the rest of the Mandarin-speaking world, uses only the Chinese language for business transactions. 3 The APSS staff in Kuala Lumpur, like other Malaysian businesses, includes many people of Chinese heritage, including some who speak Mandarin. The significant time difference between Taiwan and Europe was problematic, as was the lack of knowledge of the Chinese language. Taiwanese are not all fluent in English, and the local system requirements would include preparing invoices and printing reports in Chinese. —Major Project Management Manager, APN IT Taiwan’s R/3 Project The APSS project plan for Taiwan outlined a fixed-cost implementation budget of U.S.$100,000 for Phase 1 and an estimated budget of U.S.$50,000 for Phase 2. Phase 1 would involve 250 APSS man-days and consulting fees of U.S.$77,700. The other costs would include technology upgrades and direct expenses for travel and living expenses for the APSS consultants. The Phase 2 costs would include an estimated U.S.$30,000 for software development costs for unique local requirements. The Taiwan office named this project Confucius because the project kickoff took place during the week of Confucius’ birthday, and it was hoped that the intellectual capability pooled from a number of areas within BAT would be as good as that of the renowned Chinese philosopher, if not better. The project cost was based on several assumptions. (See Exhibit 2.) One key assumption of the plan related to the use of the Symphony template developed by APSS and used in Singapore (BATS). By using this template, Taiwan could leverage BAT’s best practices for the new business processes, as well as take advantage of a template that was recently reported to be 95 percent compliant with the corporate data standards set by Globe House.4 The Symphony template initially included configuration for the financial and controlling modules, with other modules added later. The four primary business processes would be orderto-cash (accounts receivable), requisition-to-payment (accounts payable), inventory management, and plan-andmanage-enterprise, which includes profitability analysis. However, because many of the business processes would be new to the Taiwan office and few staff members had prior in-depth experience with integrated systems in general, few changes to the template itself were anticipated. Customization would only be done for legal or statutory reporting purposes. Further, BAT Taiwan was very mindful of the dangers of customizing standard systems. One of the things I learned from my previous company and in BAT was that when we modified the system to suit our local operational needs, normally in the name of enhancement, we changed the system to a point beyond recognition. That’s where the problems start. Later, we found that it was difficult to fit in vendors’ enhancements, modules, and whatever. To me, it’s the resistance to take on processes that have been established and tested as a more efficient way of doing things; we tend to hold onto old habits. It’s a mind-set challenge. —Mr. Ma, BAT Taiwan Country Manager For Phase 1, a three-stage implementation approach, developed by APSS with reference to the ASAP methodology, was to be used. (See Exhibit 3.) The business users would participate in the detailed requirements study, in cleaning up data to be converted, verifying the data conversion, and participating in system testing and system rollout. The system would be configured by APSS personnel to reflect Taiwan’s business environment, with such details as the number of warehouses and the accounts to be debited or credited in specific circumstances. The development environment would consist of a three-instance development landscape with DEV (development), QAS (quality assurance), and PRD (production) servers, all housed in Kuala Lumpur. R/3 version 3.1H would be implemented for Phase 1. 4 3 Taiwan uses the traditional Chinese language, rather than simplified Chinese, as its official language. Chinese is the written form of the language; Mandarin is the spoken form of the language. A recent review of BAT templates across the regions sponsored by Globe House concluded that the Symphony template had the highest compliance with the corporate data template among all the current templates. Case Study III-6 • BAT Taiwan: Implementing SAP for a Strategic Transition 489 • BATS template is extended to include BAT Taiwan in this implementation, and business requirements not supported by BATS template are considered out of scope, with the exception of Fixed Assets, which is not part of the template but will be set up for BAT Taiwan. • BATS template remains at v3.1H and will be upgraded to v4.6x in Q2 2001. There will be no SAP upgrade during the course of this project. The cost of v4.6x upgrade shall be shared with BATS and BAT Mkt. The cost of upgrade to BAT Taiwan is estimated to be at U.S.$57,000 but the amount will be reviewed again before the upgrade commences. • BAT Taiwan project is to commence not earlier than mid-September 2000 and a lead time of 4–6 weeks is required to mobilize the resources once the project is awarded to APSS. • Estimate is based on the high-level understanding gathered during the two-day SAP study in July 2000. The system specification, documented after the study, forms the basis of this proposal. • The estimate takes into consideration efforts for 18 customized reports (please refer to Appendix B) in Phase 1. • A total of 24 business processes will be covered in this project. Refer to Appendix A for details. • Documents printed in Chinese are not a requirement in Phase 1. • BAT Taiwan will use the data center services from APSS and will use the existing hardware in APSS. Please refer to Appendix C for the service-level agreement. • Existing WAN bandwidth is sufficient but will need to reconfirm during the project. • BAT Taiwan will assume project management, communication plan and execution, development of user procedures, and local infrastructure management. • Project site and resources are based in Taiwan, and there is no necessity to travel outside of Taiwan head office. • Full-time resources are identified and assigned to the project as per project plan to ensure on-time delivery and quality output of project deliverables. • The business resources assigned to the project are subject-matter experts in their respective functional areas, and are either decision makers or are in a position to influence the process owners. • BAT Taiwan resources assigned to the project will be equipped with the knowledge to be the first-level support after Go Live. • A single set of chart of accounts is used by BATS, BAT Mkt, and BAT Taiwan. BATS finance manager has been appointed as custodian for COA. Any request for COA maintenance shall be forwarded by the respective end markets to the custodian for action. EXHIBIT 2 APSS Assumptions for Cost Estimating Phases 1 and 2 The plan for Phase 2 included potential solutions to two system requirements unique to doing business in the Taiwan end market. First, an invoicing system required by the Taiwan government (Government Universal Invoice, referred to as GUI) would need to be purchased and integrated with the SAP system. Because this capability would be required for doing business in Taiwan, it was anticipated that the module would be developed by SAP Taiwan. Second, a Chinese language module would be required because Taiwan conducts business communications almost exclusively in its official language. All reports, including those produced by the GUI, and certain parts of the system needed to be in the official Chinese language. APSS planned to request help from SAP Malaysia in producing such a module. For Phase 1, APSS would provide an application team leader and three other full-time application consultants onsite 490 Part III • Acquiring Information Systems 1 week Analysis and Planning 25-Sep to 29-Sep 2000 • Confirm SAP organization structure • Detailed requirements study • Impact to BATS (Symphony) template 3 weeks 4 weeks Design and Prototype Build and Test 2-Oct to 20-Oct 2000 23-Oct to 17-Nov 2000 • Configure SAP system • Design customized reports • Develop users’ security profiles • Design and complete business blueprint Live System • Develop final configuration • Prepare and conduct conversion • Prepare and conduct system test • Conduct security profile testing • Conduct user acceptance test • Conduct user training • Assess infrastructure readiness • Prepare for rollout 2-Jan, 2001 EXHIBIT 3 Eight-Week, Three-Stage Project Approach (which could include contract employees hired by APSS from their local market). These four APSS team members would work at the BAT Taiwan offices, beginning with the project kickoff at the end of September 2000 until two weeks after the implementation date. A part-time APSS programmer would also be assigned to the project, but would primarily work out of the APSS offices in Kuala Lumpur. changes associated with the new business model. The business users would begin with 18 customized reports. Although the APSS staff would be full-time, the team members from Taiwan needed to continue to perform some of their current functions during the project. Further, the team members would also need to help train temporary or new personnel that would be brought in near the end of the project. Initial Schedule The original schedule was to implement the R/3 modules in two phases. Phase 1, to be initiated September 25 and completed by January 2, involved the modules to support direct importation: parts of the SD, MM (purchasing and inventory management), and FI/CO modules. Phase 2, to be completed by June 2001, would involve implementing the additional modules needed for direct sales and distribution to key accounts, as well as the specific invoicing system required by the Taiwan government and software to support the reports in Chinese for the area offices. The Phase 1 system would therefore support importing to just one customer: Taiwan’s current distributor. The distributor’s system would continue to be used for the GUI reporting until Phase 2 provided these customized capabilities. Initially, the plan was to complete the Phase 1 development and testing within eight weeks (by the end of November) to provide a buffer for training the business users in not only the new system, but also in the process The Project Team The leaders for the project team brought together three sources of expertise from the three organizations involved: IT project management from APN; BAT template, SAP package, and technical knowledge from APSS; and local business needs from BAT Taiwan. The country manager for Taiwan, Mr. Ma, served as the business sponsor for the project. The project leaders from APN, Taiwan, and APSS were empowered to make project decisions and formally reported to Mr. Ma and the head of IT for APN, via a project steering committee. (See Exhibit 4.) The Major Project Manager in the IT APN organization, who had previously been a consultant for one of the Big Five consulting firms but did not have any SAP training, was the IT co-lead responsible for overall management of the project. He developed the schedule and task breakdown, the timing of each task, and the resources needed. His work plan became the final project plan, and he was responsible Case Study III-6 • BAT Taiwan: Implementing SAP for a Strategic Transition 491 Project Steering Committee Mr. Ma, Project Sponsor Head of IT, BAT APN Mr. Lee, BATT Project Co-Lead Major Project Manager, BAT APN Project and Change Management Mr. Lee, BATT Project Co-Lead Major Project Manager, BAT APN Business Process Owners BATT Finance BATT Logistics BATT Materials Management BATT Sales Distribution Project Integration Project Integration Lead, APSS SD/MM Team FI/CO Team Technical Team MM Consultant, APSS SD Consultant, APSS Power User, BATT Project Integration Lead, APSS FI Consultant, APSS Power User, BATT Power User, BATT Power User, BATT Power User, BATT Power User, BATT APSS Technician (pt-time) APSS Technician (pt-time) APN IT Technician (onsite) EXHIBIT 4 Project Team Composition at Time of Kickoff for monitoring the achievement of the milestones and verifying the quality and scope of the resulting system. Initially, the lead business role for the project was played by the manager of finance for BAT Taiwan. However, at the time of the project kickoff, she announced her resignation from BAT. The lead business manager role for the project was then assumed by Mr. Lee, who was at the time the trade marketing manager for BAT Taiwan and was the logistics process owner on the project. Lee had been Country Manager in Thailand and had experience with the core processes (such as accounts receivable and inventory management) during earlier employment at Johnson & Johnson in the U.S. For the remainder of the project, Lee took responsibility for the business process owner role for finance as well as logistics. As project co-lead, he was also responsible for co-leading the change management efforts for the project. Two other Taiwan managers also played business process owner roles. An APSS manager, who was a certified accountant with an MBA, was selected to play the Project Integration Lead role and to lead the APSS development team for the Taiwan project. This APSS manager was selected to lead the project integration because he had strong knowledge of financials, the business, and the [SAP] FI module. Plus he had managed other ERP project implementations. He also was able to speak Mandarin, to foster communications. —SAP Applications Manager, APSS The APSS Project Integration lead was responsible for process integration as well as the day-to-day progress of the project and the work by the APSS team members. He and one other APSS consultant were assigned to the FI/CO modules; one APSS consultant each was assigned to the SD and MM modules. There were two part-time technical team members at APSS (see Exhibit 4). The initial plan was for the four full-time members of the APSS development team to go to Taiwan for three weeks at a time and then return to Kuala Lumpur (KL) for the following weekend for personal reasons. However, government regulations permitted nonresidents to work in Taiwan for only 2 weeks at a time. Therefore the return weekend visits to KL became biweekly. Further, because they could 492 Part III • Acquiring Information Systems obtain a visa for only two months, they remained in Kuala Lumpur for one week every two months to renew their visas. The week-long visa stays in KL were staggered so that two APSS team members always remained onsite in Taiwan. Pressing issues were discussed with absent team members by phone as needed, and the Project Integration Lead provided a weekly progress report by phone to the APSS Applications manager, who was serving as the APSS lead on an R/3 project in Thailand during several weeks of the Taiwan project. reported to him. The trade marketing position was left open, but the country manager helped with that role. Everything was coordinated with timelines. You could do the project at a distance, but being co-located made it a lot easier: when you hit an issue, you could say, “Let’s have a meeting to discuss this.” There were three technical team members (see Exhibit 4). The APN IT resource already based in Taiwan was responsible for the telecommunications infrastructure to support system access by five business partners in Taiwan. The R/3 Basis expert from APSS worked offsite until a week before the Go-Live date, when he spent two weeks in Taiwan. The third person on the technical team was responsible for creating ABAP reports. Later in the project, she was replaced by a programmer from SAP Malaysia. Just prior to Go Live, this programmer spent three weeks in Taiwan to ensure that all the reports were functioning correctly. —SAP Application Consultant, APSS The manager of finance for BAT Taiwan was initially responsible for choosing the “power users” for the project team based on information provided by APSS about the user expertise that would be needed. Five Taiwan employees were selected to work on the FI/CO modules (see Exhibit 4). Only one user was assigned to work on the SD and MM modules because no one in the Taiwan office had previously been performing these functions; the person had gained experience with sales and logistics functions when employed at Rothmans. None of the Taiwan users had prior experience on SAP projects, but some users had entered data into the SAP R/3 financials system (of BATUKE) and one user had some experience with Oracle systems. All team members were considered fast learners who would be able to pick up the new system quickly. The good thing about Taiwan is that most of the managers here are pretty new in the organization. They are young, well-educated (many have MBAs), and have a high level of computer literacy. They are open-minded and are more prepared to take on changes. They knew that whatever we were doing in the past, things were going to be different, and they knew that what we had was cumbersome, that we could not go forward with a bunch of non-integrated systems. They welcomed the [SAP] system; this was going to help them do their job. Their commitment level was extremely high. So the credit is due to the people themselves. —Mr. Ma, BAT Taiwan Country Manager All of the Taiwan team members continued to also do their regular jobs during the project. One manager, who had just rejoined the Taiwan office in a supervisory role, was able to devote 70 percent of his efforts to the project. The BAT Taiwan Project Co-Lead was able to juggle the workloads of the part-time project team members that The Taiwan operations were small at that time. This made it more difficult for the project team, because they had to deal with day-to-day activities as well as the project. But they also had full senior management support. —Major Project Manager, APN IT Kickoff Meeting A one day project kickoff meeting was held in Taiwan at the end of September and was run by the manager of finance for BAT Taiwan. Most of the project team members and all of the business process owners were present, as were the brand and trade marketing managers. The project co-leads from APSS and APN talked to the whole office staff—both expert and casual users—about the need to be supportive of the project team members over the coming months. They made a presentation to the whole office— whether they would be actual users or a final user at the end of the day. They said, “These people are taking on a lot in a short period of time . . . and you should not make too many unreasonable demands during this time period.” They were told that the project was a critical part of the full potential initiative, so let’s pull together on this one. —Mr. Lee, Project Co-Lead, BAT Taiwan The APSS team members worked in a conference room just down the hall from the other managers. All the team members got along well together, both in the work environment and socially—including some weekend get-togethers. Exhibit 5 documents the High-Level Work Plan with the eight week project milestones. During the Business Blueprint Phase (high-level requirements), the APSS team members met with the key users to explain the processes in the template and to learn about local needs. The fact that the APSS personnel knew BAT’s business really helped, Case Study III-6 • BAT Taiwan: Implementing SAP for a Strategic Transition 493 MAIN TASKS 8 weeks’ Duration 25Sep 02 Oct 09 Oct 17 Oct 23 Oct 30 Oct 07 Nov 13 Nov Project Kickoff SAP Functional Overall Training Kickoff Meeting (Sept 26) Details Requirement Study Present Prototype (Oct 11) Detail System Design & Prototype Confirm Business Blueprint (Oct 24) Reports Design & Form Layout SAP System Configurations & Development System Testing Complete UAT (Nov 10) User Acceptance Testing User Training Development Stage Completed Rollout Stage: EXHIBIT 5 Data Conversion System Go Live December 29, 2000 January 2, 2001 Work Plan and Milestones for Phase 1 because Taiwan had not had to deal with accounts payable, accounts receivable, or inventory in the past. They added a lot of value. When we needed to decide how we wanted to configure something, they would say, “The BAT way is this.” —Mr. Lee, Project Co-Lead, BAT Taiwan They knew the alternatives and the impact on the user and the actual process. For example, online approval of a purchase order sounds good, but they asked, “Who will approve it when the person is out of the office?” because someone must go into the system to do it. [Singapore implemented online approval, but it was not effective—so in the end it was not used.] APSS could advise us on these issues. —Major Project Manager, APN IT The APSS people knew BAT’s processes. They asked us to review the blueprint. I had worked with Oracle systems and knew how to link modules— Materials Management and Finance. —FI/CO Team Member, BAT Taiwan The initial configuration was really good. We worked really hard. The APSS team understands our operations and our industry. Also, they spoke my primary language [Mandarin]. —MM/SD Team Member, BAT Taiwan Because BAT Taiwan had no experience with direct distribution, help was sought from some workers at the distributor. Some configuration was also done to take into account the expected future changes in government regulations regarding the payment of taxes that would affect product pricing, as well as the key accounts that would be introduced in a future phase. These changes could be activated when needed. A prototype was ready by the third week. Scope Change: Moving Forward Phase 2 In October, the project leaders recognized that some of the Phase 2 changes would already be done in the initial configuration, so it might be possible to move Phase 2 forward. They believed that Phase 1 could be completed easily within the eight week period and that the team had the resources to also complete Phase 2 by January, 2001. They consulted with the APSS Applications Manager, the Head of IT at APN, and the other project team members, and it was agreed to move Phase 2 forward. A revised proposal was prepared by APSS, and the phase was renamed 1A to signal that the Phase 1 resources would continue on the project team, rather than have a totally different implementation. Changing the schedule for the two-phase implementation greatly increased the risks of the project from both an IT and a business perspective. Phase 1A included the two requirements that were specific to the Taiwan 494 Part III • Acquiring Information Systems implementation: the government- designed invoicing system (GUI) and the Chinese language module. These additional requirements increased the technical complexity of the initial implementation, as well as the need for training on additional business processes. APN management therefore initiated a formal review before the end of October to reassess the risks and to determine whether the project was under-resourced. The APN review team consisted of the IT head at APN and two finance managers from Hong Kong. The team leads walked through the project, and discussions were held in Taiwan with the business sponsor. As a result of this review, BAT Taiwan made plans to hire additional temporary staff prior to the user acceptance testing phase to help relieve the business team members who would be involved. In addition, Hong Kong-based APN staff (mostly from finance, but also logistics and IT) would receive training prior to implementation in case they were needed for emergency backup support. Further, APSS staff would stay longer than originally anticipated following the rollout. There were a lot of concerns. It was a short timeframe and for the first time it was managed by APSS—not jointly managed with Andersen Consulting. A lot of ‘teething problems’ had been experienced in other project rollouts, so APSS consultants were requested to stay longer to provide onsite support. —APSS Project Integration Lead The functionality required for the GUI system5 was originally expected to be part of the version 4.6 upgrade of SAP R/3 proposed for the Phase 2 project. At the end of November it was learned that SAP could not deliver a version of the GUI for the 3.1H system prior to January 1. Another vendor’s GUI system would therefore need to be purchased and interfaced to the R/3 system (as a bolt-on). With advice from BAT’s auditors (PricewaterhouseCoopers), a system from a local supplier that had been implemented by a number of other companies in Taiwan was identified and a contract was signed in mid-December. The Chinese language module was needed to print reports. SAP Malaysia offered to help, but would not have the resources to do it before mid-March. Some other companies that were developing the software as a bolt-on were asked to make presentations, and a system was purchased from E-Com. The APSS Basis team member was 5 The GUI is an official invoice that must be prepared using invoice numbers issued by the government. When a business uses up its assigned range of numbers, it must reapply for a further set of numbers, and so on. Six to eight such reports must be submitted to the government for tax purposes every four to eight weeks. scheduled to come to Taiwan a week before Go Live to ensure that the system would print correctly. User Acceptance Testing and Change Management Because of the change in Taiwan’s business model, the change management activities associated with the SAP implementation involved defining new staff roles and communicating with all personnel, as well as providing training for those involved in the new system. The Project Co-lead at BAT Taiwan, Mr. Lee, was largely responsible for change management as the business lead on the project team, although all the training was done by APSS. Temporary personnel were brought in before user acceptance testing (UAT) to perform functions usually done by project team members. Three temporary accountants were trained for two weeks on the general ledger, issuing checks, and paying employees. Similarly, two extra people were brought on to help in the MM/SD areas. One of these people had previously worked for the distributor and knew the existing system very well; she later became a permanent BAT employee. The other person, who used to work for a consumer products company, had considerable experience in order processing. The UAT phase involved all of the users on the project team. Most of the other finance personnel had received exposure to the new processes during earlier phases of the project. Other Taiwan personnel were trained in early November as part of the UAT phase of the project. Few changes were required as a result of the testing. However, the integrated nature of the system did cause some problems. There were some hiccups here and there. During the user test phase, there were some apprehensions, partly due to the lack of understanding of the system, and the process adjustments that need to be made. With motivation and support from each other within the team, they managed to pull it through with great success. —Mr. Ma, BAT Taiwan Country Manager Following the UAT, an additional 20 people—mostly in marketing functions—received overview training from the APSS consultants. A key challenge here was how to convey the integrated nature of the system when most people were used to focusing on a single function. Quality Reviews Globe House provided funding for two quality reviews. The first one was to be a quality review after the user acceptance test, prior to implementation. The second one Case Study III-6 • BAT Taiwan: Implementing SAP for a Strategic Transition 495 would be part of a post-implementation review process a few months after implementation. The country manager decided that having a thirdparty independent of BAT to do the review would be a good idea, and SAP Taiwan was selected. The first review took place in early December and took the form of the quality check for the Final Preparation Phase in the ASAP methodology. The results were positive and the project team prepared for the final steps: Data Conversion on December 29 and Go Live on January 2, 2001. We were unconcerned about whether someone from SAP or an internal auditor did the review. The issue was: Is the system quality up to the mark? Is there anything substandard that could cause a system failure? —Mr. Ma, BAT Taiwan Country Manager Globe House has sponsored some of the quality reviews. It depends on whether the project management would like to have it done or not. In Brazil, the reviews are being done by an external consulting partner, but it’s a much bigger project: Once a week a person comes in and reviews the implementation progress. —SAP Program Manager, Business Integration, Globe House Go Live Phases 1 and 1A went live according to the revised project plan on January 2, 2001, with one major exception: The functionality for processing the key accounts and for printing the reports with the Chinese language module were included in this release, but the GUI interface was not integrated with SAP until mid-January. Instead, the team’s contingency plan was used for the first two weeks in January: The sales orders were entered into BAT Taiwan’s R/3 system and then submitted to the system used by the country’s long-time distributor to produce the required government reports. This process made the January close very difficult, although it was still completed within a week. There was also a delay in the installation of a new telecommunications line leased from the governmentowned telecommunications company in Taiwan. This meant that a more expensive international dial-up line had to be used to connect to Kuala Lumpur via Hong Kong until early in February, when the leased line could be phased in. Initially, there were also some order processing problems. The Go-Live date was close to the Chinese New Year (January 24), which meant heavy numbers of orders had to be processed at the same time as the new business processes were being implemented. Some orders were delivered late, and sometimes an order contained the wrong pricing, but within six weeks, these problems were worked out. The second close in February went smoothly. The original Phase 1 plan was for all APSS consultants to remain onsite in Taiwan for two weeks after Go Live. Because of the new Phase 1A schedule, the business sponsor asked for four weeks of support. A compromise solution was to provide two APSS team members onsite for six weeks following Go Live. In addition to the Project Integration lead, the MM consultant from APSS remained onsite for the first two weeks and helped coach the users through the new processes, and then the second financial consultant and SD consultant from APSS were onsite for the succeeding two weeks. As of January 2001, APSS is running three separate SAP systems for (1) Singapore, Taiwan, and Thailand; (2) Malaysia; and (3) Australia. BAT Taiwan’s R/3 system is run on the same client system as those of Singapore and Thailand.6 Because all three systems use the same template, each country shares the same organizational hierarchy, chart of accounts, and data definitions. For example, finance is subdivided into the three areas of operating, marketing, and corporate finance, while marketing is subdivided into trade and brand marketing. Each country is defined by a company code, which represents a legal entity for reporting purposes. Although the basic processes within the client are the same, some configuration is specific to the company code. For example, a country can have its own configuration to reflect how it wants to manage costs, how it structures its departments, and with codes for its own area offices and key accounts. Further, controlling area and operating concern are defined at the company code level. There is no consolidation of financials or profitability analysis at the regional level. Exhibit 6 shows the cost center hierarchy for BAT Taiwan. Ongoing Operational Support by APSS In the first 3 months of service, the production server running the Taiwan system had been down only once for a period of approximately two hours. However, in the weeks immediately following Go Live, procedural errors led to a few processing errors. For example, incorrect data was recorded on some occasions when the users specified an incorrect company code (equivalent to a country code). A multi-tier support plan is in place. Tier 1 support is provided locally, and APSS provides support services via their help line based on six priority levels. 6 2000. The Thailand R/3 implementation was also completed in Fall 496 Part III • Acquiring Information Systems TW01_HIER Brand Marketing TW01_BMKTG General Admin TW01_GA CORA 1301 GM Office 1300 Finance 1302 HR 1303 E-Bus 1304 Fin Gen 1305 EXHIBIT 6 Trade Marketing TW01_TMKTG Brand Spend TW01_BMX Brand Admin TW01_BMA Mkt Res 2301 Brand Admin 2300 Trade Spend TW01_TMX Trade Adm 4300 Cartier 2302 Channel GR/CVS TW01_GR SE555 2303 Dunhill 2304 Kent 2306 Craven A 2305 4302 Cartier 4303 SE555 4304 Dunhill 4305 Craven A 4306 Kent ———–4307 FSV Trade Admin TW01_TMA Distribution TW01_DIS Horeca TW01_HOC Trade Mkt Dev 4301 4322 Cartier 4312 Cartier 4323 SE555 4313 SE555 4324 Dunhill 4314 Dunhill 4325 Craven A 4315 Craven A 4326 Kent 4316 Kent —————- —————-4327 FSV 4317 FSV Cost Center Hierarchy for Taiwan’s R/3 System (See Exhibit 7.) Contacts with an APSS consultant on the original Taiwan project team are sometimes feasible, but not guaranteed. However, learnings from the Taiwan project and the modifications to the Symphony template for the local system requirements have been captured in a Lotus Notes database accessible to other members of the APSS support team. User ID and authorization changes are authorized by designated business managers, and these requests are submitted to APSS via an Excel spreadsheet format. As noted earlier, APSS owns the SAP licenses and leases them to the end market as needed. Requests for system changes (new functionality, new configuration, or new reports) for Taiwan are reviewed and authorized by the Project Co-Lead at BAT Taiwan, who is now head of finance for the Taiwan office. Some problems have surfaced over time and certain changes have been requested as users have learned more about how the system works. For instance, a differential pricing policy was not initially specified, but has been added to the configuration. Post-Implementation in Taiwan A project celebration was held as part of a Chinese New Year celebration for the BAT Taiwan office. It involved dinner for the heads of the Taiwan departments and all of the business users on the team. At the dinner, each Taiwan project member who was not a department head received a surprise bonus of a month’s salary in recognition of their effort and extra-long hours. People say that it usually takes a year to do an SAP implementation, or maybe only 6 months when you have the experience. Here it was 4 months for the implementation; it was so fast you’re maybe a little afraid that things may still go wrong. But now we’re starting to feel proud. —FI/CO Team Member, BAT Taiwan Over the past few years, BAT Taiwan has grown from 20 to 100 personnel as it first absorbed Rothmans and then evolved into a full trading company. All data entry is Case Study III-6 • BAT Taiwan: Implementing SAP for a Strategic Transition 497 Priority Definition Users Affected Examples Minimum Service Level * P1 The entire business is stopped, a business process has failed and/or an entire site is affected. All System is unavailable, billing and delivery cannot be processed, month-end processing cannot be completed. 95% resolved in 1 hour = Application & APSS (HD, Sec, Ops) – Resolution External Engineer (third party, i.e., Equant/IBM) – Active assistance P2 Issue impacts a module, prevents a large number of users from doing their work, and/or a workaround is not available. Group Sales and Distribution module fails, orders cannot be taken, volume is too large for a manual workaround. 90% resolved in 2 business hours P3 Issue impacts a module and prevents a large number of users from doing their work and a workaround is available. Group Financial journals cannot be posted but it does not affect third parties, volume is small for a manual workaround. 90% resolved in 3 business hours P4 User is prevented from doing work due to critical task failure, no workaround exists. Single User cannot print documentation, user profile is not complete. 90% resolved in 4 business hours P5 A user is prevented from completing a function, but a workaround can be provided, and/or problem is minor. Single Automatic check printing fails but critical payments can still be processed with manual checks. 90% resolved in 2 business days P6 Query or request. N/A How to extract data for reporting 90% resolved in 3 business days * Minimum service level: a resolution (including workarounds) is handed to the user to confirm acceptance before it is implemented in the production environment. EXHIBIT 7 Help Desk Support by APSS now done in the Taipei office, and invoices are printed at the five area offices. Within the Taipei office a few work imbalances still continued to exist because of the lack of widespread SAP expertise and the loss of some expert business users. For example, the MM/SD lead still regularly worked a few hours of overtime each evening even after the new GUI system was in place. A system upgrade to R/3 version 4.6C is planned for July 2001, and some improvements to the process configurations could be made at the same time. SAP is a very powerful application for a small market. Initially you go through a stage where you learn the basics but you don’t yet know all the functionality. When you become proficient with the system, you begin to look at other needs. APSS needs to be ready to show the business how to use the system better—what the more complex processes are that they couldn’t absorb before. —Mr. Ponce, Asia Pacific Regional IT Manager A formal post-implementation review, sponsored by Globe House, was to be conducted toward the end of March 2001. Other BAT managers are expected to be interested in learning how the implementation was accomplished so quickly, at such a low cost, and whether the business users were happy with the quality of the system. Within APN, Hong Kong would probably be the next end market to implement SAP.
Collepals.com Plagiarism Free Papers
Are you looking for custom essay writing service or even dissertation writing services? Just request for our write my paper service, and we'll match you with the best essay writer in your subject! With an exceptional team of professional academic experts in a wide range of subjects, we can guarantee you an unrivaled quality of custom-written papers.
Get ZERO PLAGIARISM, HUMAN WRITTEN ESSAYS
Why Hire Collepals.com writers to do your paper?
Quality- We are experienced and have access to ample research materials.
We write plagiarism Free Content
Confidential- We never share or sell your personal information to third parties.
Support-Chat with us today! We are always waiting to answer all your questions.
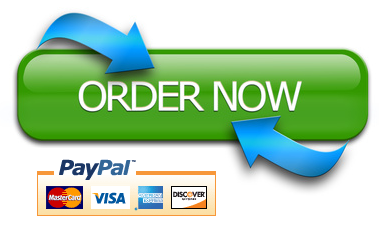