Lab Report
AE 303 Experimental Aerodynamics Lab: Round Jet PIV Measurement Instructor: Prof. Xiaofeng Liu 1 Objectives • • • To familiarize with the principle and practice of Particle Image Velocimetry (PIV) measurement technique. To investigate the near field characteristics of a free turbulent round jet in terms of the streamwise evolution of the cross-jet distributions of fundamental flow quantities such as time-averaged velocity, Reynolds normal and shear stresses and vorticity. To compare results with similar data available in literature. 2 Ovreview Particle Image Velocimetry (PIV) represents a paradigm shift in fluids experiments. The technique is capable of non-intrusively measuring the velocity vector distributions within a planar field of view, whereas previously, velocity could only be measured at a point using a Pitot tube type of probe, a Laser Doppler Velocimeter (LDV, or LDA for Laser Doppler Anemometer), or a hotwire probe. Boosted by technology advancement for computers, lasers and digital cameras, PIV can now measure flow velocity field in a continuously time-resolved fashion when high speed camera and high repetition rate light source are used. Exposure of PIV to undergraduate students not only provides an opportunity for them to learn the state-of-the-art in velocity measurement capabilities, but also better prepare them with improved competency in conducting advanced experiments for their future work in industries. The lab exercise outlined in this document serves as a demonstration of the basic practices of PIV. In particular, the PIV technique is applied to the measurement of a free turbulent jet emitting from a round, 3D printed nozzle. Both instantaneous distributions of the u and v velocity components within an axial symmetric plane of the round jet will be measured by using a PIV system. These measured planar distributions of the instantaneous 2D velocity components can be further used to obtain mean velocity, Reynolds normal stress, Reynolds shear stress and vorticity profiles so that collectively, a comprehensive understanding of the fundamental characteristics of the turbulent round jet development in its near field in an open space can be achieved. In particular, in this PIV lab, we will use the EduPIV system (manufactured by Dantec Dynamics) to quantify the characteristics of a turbulent round jet developing in an open free space. To characterize the jet development sufficiently, we need to obtain a sufficient amount of velocity vector series by using the PIV measurements. These PIV velocity vector series will further allow us to extract data about the jet flow including: 1. The time-averaged velocity profiles at different streamwise locations, 2. Streamwise variations of jet half-width and local maximum velocity with respect to streamwise locations, 1 3. Reynolds normal and shear stress profiles at different downstream locations. 4. Streamwise variations of vorticity profile. These quantities form a preliminary understanding of the jet’s flow structure and its development characteristics. Analysis, presentation and discussion about these quantities and characteristics are expected to be included in the lab report. 3 Equipment The EduPIV round jet experimental setup is shown in Figure 1. As can be seen from the figure, the EduPIV system consists of a round nozzle submerged in a water tank that accommodates the free round jet, a LED light source that generates light sheet to illuminate the seeding particles in flow field, and a digital camera that is connected to a laptop computer via a USB port to acquire particle image series. Both the image acquisition and the PIV image pair analysis are conducted by using the Dantec DynamicStudio software. Detailed components of the EduPIV system and and the materials used in the round jet PIV measurements are listed in Table 1. Figure 1. The experimental setup. Name Dynamic Studio EduPIV Software (Base package) FlowSense USB 2M-165 Camera 35mm Low-Distortion Lens EduPIV LED Fiber Light (Light Sheet Optics) Table1. Equipment and Materials List. Company Comments Dantec Dynamics 2D PIV; Complete Image Processing Library; POD; MATLAB Link Dantec Dynamics Dantec Dynamics Dantec Dynamics Dantec Dynamics Up to 160 frames per second at 1920 x 1200 pixels Field of View USB 3.0 Interface f/2.8 – f/16 aperture 35mm focal length C-mount lockable focus and aperture 150 W Illumination 110/220V Input Fiber-optic line light guide Adjustable Focus Rod Lens 35˚ divergence angle 7.6 cm sheet width at aperture 4mm minimum sheet thickness 2 Seeding Particles Dantec Dynamics 3D Printed Nozzle Dantec Dynamics Dantec Dynamics Aqua Medic Flow Loop (Tank) EcoDrift 8.1 pump and controller Tank back cover Sealable Test Tube Rubbing Alcohol 4 Procedure SDSU N/A N/A Polyamide Seeding Particles Mean particle diameter 50 µm 1.03 g/cm3 9080A5011 Jet diameter at exit: 5 cm Flow range: 2 – 5 cm/s 80 x 35 x 40 cm 112 liters 1600 to 8000 liter/hour 8 – 20 W Black backdrop for the tank to eliminate ambient light sources Mix particles, water, and rubbing alcohol for uniform particle distribution To help particles submerge beneath the surface tension of the water Preparation 1. Fill the tank with tap water. 2. Connect pump to nozzle and place the nozzle in the tank. 3. Use the magnet to attach the pump to the side of the tank, ensuring the nozzle is horizontal. 4. Connect the pump to the pump controller and plug the controller into the wall. 5. Connect the fiber optic lead to the light source and plug the source into the wall. 6. Seed the flow by combining the particles with the water and some rubbing alcohol in a sealable test tube to assist in the submersion and uniform distribution of the particles. 7. Screw the lens on the camera and mount the camera on the rail, so that its view is perpendicular and approximately 19 cm to the tank wall. 8. Connect the camera to the laptop computer using the USB cable. 9. Start DynamicStudio software on the laptop. 10. Turn the room lights off and turn on the light source and turn it up to full power. 11. Adjust the sheet optics to achieve as thin a light sheet as possible (approximately 4 mm thickness). 12. Place the backdrop on the far end of the tank to form a black background. 13. Orient the system so the view of the camera is parallel to the windows to avoid recording reflections in the tank glass. 14. In Dynamic Studio, click the green lightning bolt to enter acquisition mode. (The FlowSense camera should be automatically detected at the bottom right of the screen). 15. In DynamicStudio, set the exposure time to 750 µs and trigger rate to 150 Hz and click “Preview”. 16. Adjust location of the camera to capture the flow field in the central plane of the jet just downstream of the nozzle exit. 3 17. Adjust the zoom and f number of the lens until the particles are clearly visible in the preview frame. 18. Add particles as necessary to increase particle density in the image. 19. Set the pump profile to continuous and speed to its maximum. Calibration 20. With the camera in the position for the test runs, place a calibration target (or ruler) within the view of the camera in the plane of the light sheet. 21. Turn on the room lights and adjust the camera trigger rate and exposure time so that the target is clearly visible in the preview window of the DynamicStudio. 22. In DynamicStudio, set the number of images to capture to 20 and click acquire (Dismiss the warning about missing a synchronizer). 23. Save the acquired images for the calibration. 24. Remove the calibration target from the tank. Execution 25. Turn the room lights back off. 26. Turn the pump on at a low speed and wait 5 to 10 minutes for the flow to stabilize. 27. Reset the camera to 150 Hz trigger rate and 750 µs exposure time. 28. Set the number of images to acquire to at least 300. (Note: For this particular experiment, the flow is assumed to be ergodic with a sample of at least 2 seconds of data, meaning a geometric time average of the results will produce an overall representative flow solution). 29. Click acquire and let the system record images. 30. Save the images to a run. 31. Exit acquisition mode in DynamicStudio. 32. Pre-process the calibration images by finding their mean. 33. Use the mean image to find the scale factor for the images (pixels to mm). 34. Process the run image set using the Adaptive PIV Analysis option in Dynamic Studio, with the following parameter settings: a. Minimum window size: 32 x 32 pixels b. Maximum window size: 64 x 64 pixels c. Step: 16 pixels (50% overlap) 35. Export the velocity vector field for each time step to a .csv file. 36. Import the .csv files into MATLAB for further analysis. 5 Requirement for your report 1. A full report is required. 2. Show the time averaged u-velocity contour map. ����2 contour distributions within the field 3. Show the Reynolds normal stress ���� 𝑢𝑢′2 and 𝑣𝑣′ of view of measurement. 4 ����� contour distribution within the field of view of 4. Show the Reynolds shear stress 𝑢𝑢′𝑣𝑣′ measurement. 5. Show the vorticity magnitude distribution within the field of view of measurement. (Note: in all the above plots, the x and y coordinates need to be non-dimensionalized by the nozzle exit diameter). 6. Show the streamwise variation of the mean velocity, Reynolds normal stress, Reynolds shear stress and vorticity profiles at selected streamwise locations. 7. Discuss about the characteristic behavior of the round jet at its near field investigated. References 1 Adrian, R.J. 1984, Scattering particle characteristics and their effect on pulsed laser measurements of fluid flow: speckle velocimetry vs. particle image velocimetry. Appl. Opt. 23,1690–1691 2. Adrian, R.J. & Yao, C.S. 1984, Development of pulsed laser velocimetry (PLV) for measurement of fluid flow. In: Patterson G, Zakin J (ed) Proceedings of the 8th biennial symposium on turbulence, Rolla, Missouri, September 1984, pp 170–186. 3. Adrian, R.J. 2005, Twenty years of particle image velocimetry, Exp. Fluids, 39, 159– 169. 4. Adrian, L., Adrian, R. J., & Westerweel, J. (2011). Particle image velocimetry (No. 30). Cambridge university press. 5. Cummins, H.Z., Knable, N. & Yeh, Y. 1964, Observation of diffusion broadening of Rayleigh scattered light, Phys. Rev. Lett., 12, 150-153. 6. Melling, A. (1997). Tracer particles and seeding for particle image velocimetry. Measurement science and technology, 8(12), 1406. 7. Raffel, M., Willert, C. E., Scarano, F., Kähler, C. J., Wereley, S. T., & Kompenhans, J. (2018). Particle image velocimetry: a practical guide. Springer. 8. Roth, G.I., 1998, Developments in particle image velocimetry (PIV) and their application to the measurement of the flow structure and turbulence within a ship bow wave. Ph.D. dissertation, Johns Hopkins University. 9. Roth, G.I., Katz. J. 2001 Five techniques for increasing the speed and accuracy of PIV interrogation. Meas. Sci. Technol. 12, 238–245. 10. Sutton, M.M., Wolters. W.J., Peters. W.H., Ranson. W.H. & Macneill, S.R. 1983, Determination of displacements using an improved digital correlation method. Opt. Eng. 1, 113–139. 11. Willert, C.E. & Gharib, M.1991, Digital particle image velocimetry. Exp. Fluids. 10,181–193 12. Yeh, Y. & Cummins, H.Z. 1964, Localized fluid flow measurements with an He-Ne Laser spectrometer, Appl. Phys. Lett., 4, 176-178. 5
Collepals.com Plagiarism Free Papers
Are you looking for custom essay writing service or even dissertation writing services? Just request for our write my paper service, and we'll match you with the best essay writer in your subject! With an exceptional team of professional academic experts in a wide range of subjects, we can guarantee you an unrivaled quality of custom-written papers.
Get ZERO PLAGIARISM, HUMAN WRITTEN ESSAYS
Why Hire Collepals.com writers to do your paper?
Quality- We are experienced and have access to ample research materials.
We write plagiarism Free Content
Confidential- We never share or sell your personal information to third parties.
Support-Chat with us today! We are always waiting to answer all your questions.
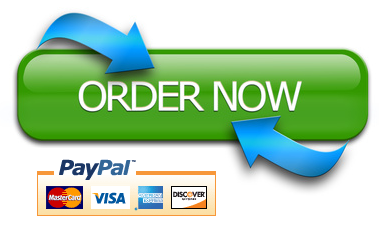