Toughness is one of the mechanical properties of materials. In this ?discussion, you will learn more about this important property and ?understand its importance.? ?Before you begin, be
Toughness is one of the mechanical properties of materials. In this discussion, you will learn more about this important property and understand its importance.
Before you begin, be sure to review the following resources:
In your original post, answer the following:
- What are the definition and units used to describe Toughness?
- List at least two tests used to determine the toughness of a material?
- Pick one of these tests and explain how it is performed.
- Compare the toughness of two materials.
PHYSICAL PROPERTIES OF MATERIALS
Volumetric and Melting Properties
Thermal Properties
Electrical Properties
Electrochemical Processes
©2012 John Wiley & Sons, Inc. M P Groover, Fundamentals of Modern Manufacturing 5/e
Physical Properties Defined
Properties that define the behavior of materials in response to physical forces other than mechanical
Volumetric, thermal, electrical, and electrochemical properties
Components in a product must do more than withstand mechanical stresses
They must conduct electricity (or prevent conduction), allow heat to transfer (or allow its escape), transmit light (or block transmission), and satisfy many other functions
©2012 John Wiley & Sons, Inc. M P Groover, Fundamentals of Modern Manufacturing 5/e
Physical Properties in Manufacturing
Important in manufacturing because physical properties often influence process performance
In machining, thermal properties of the work material determine cutting temperature, which affects tool life
In microelectronics, electrical properties of silicon and how these properties can be altered by chemical and physical processes is the basis of semiconductor manufacturing
©2012 John Wiley & Sons, Inc. M P Groover, Fundamentals of Modern Manufacturing 5/e
Volumetric and Melting Properties
Properties related to the volume of solids and how these properties are affected by temperature
Density
Thermal expansion
Melting point
©2012 John Wiley & Sons, Inc. M P Groover, Fundamentals of Modern Manufacturing 5/e
Density and Specific Gravity
Density = weight per unit volume
Typical units are g/cm3 (lb/in3)
Determined by atomic number and other factors such as atomic radius, and atomic packing
Specific gravity = density of a material relative to density of water
Ratio with no units
©2012 John Wiley & Sons, Inc. M P Groover, Fundamentals of Modern Manufacturing 5/e
Why Density is Important
A consideration in material selection for a given application, but it may not be the only property of interest
Strength may also be important, and the two properties are often related in a strength‑to‑weight ratio (specific strength), which is tensile strength divided by density
Useful ratio in comparing materials for structural applications in aircraft, automobiles, and other products where weight and energy are concerns
©2012 John Wiley & Sons, Inc. M P Groover, Fundamentals of Modern Manufacturing 5/e
Thermal Expansion
Density of a material is a function of temperature
In general, density decreases with increasing temperature
Volume per unit weight increases with increasing temperature
Thermal expansion is the name for this effect of temperature on density
Measured as coefficient of thermal expansion
©2012 John Wiley & Sons, Inc. M P Groover, Fundamentals of Modern Manufacturing 5/e
Coefficient of Thermal Expansion
Length ratio rather than volume ratio because this is easier to measure and apply
Change in length for a given temperature change:
L2 ‑ L1 = L1 (T2 ‑ T1)
where = coefficient of thermal expansion; L1 and L2 are lengths corresponding respectively to temperatures T1 and T2
©2012 John Wiley & Sons, Inc. M P Groover, Fundamentals of Modern Manufacturing 5/e
Thermal Expansion in Manufacturing
Thermal expansion is used in shrink fit and expansion fit assemblies
Part is heated to increase size or cooled to decrease size to permit insertion into another part
When part returns to ambient temperature, a tightly‑fitted assembly is obtained
Thermal expansion can be a problem in heat treatment and welding due to thermal stresses that develop in material during these processes
©2012 John Wiley & Sons, Inc. M P Groover, Fundamentals of Modern Manufacturing 5/e
Melting Characteristics for Elements
Melting point Tm of a pure element = temperature at which it transforms from solid to liquid state
The reverse transformation occurs at the same temperature and is called the freezing point
Heat of fusion = heat energy required at Tm to accomplish transformation from solid to liquid
©2012 John Wiley & Sons, Inc. M P Groover, Fundamentals of Modern Manufacturing 5/e
Melting of Noncrystalline Materials
In noncrystalline materials (glasses), a gradual transition from solid to liquid states occurs
The solid material gradually softens as temperature increases, finally becoming liquid at the melting point
During softening, the material has a consistency of increasing plasticity (increasingly like a fluid) as it gets closer to the melting point
©2012 John Wiley & Sons, Inc. M P Groover, Fundamentals of Modern Manufacturing 5/e
Importance of Melting in Manufacturing
Metal casting – the metal is melted and then poured into a mold cavity
Metals with lower melting points are generally easier to cast
Plastic molding – melting characteristics of polymers are important in nearly all polymer shaping processes
Sintering of powdered metals – sintering does not melt the metal, but temperatures must approach the melting point to achieve bonding of the powders
©2012 John Wiley & Sons, Inc. M P Groover, Fundamentals of Modern Manufacturing 5/e
Thermal Properties
Thermal expansion, melting, and heat of fusion are thermal properties because temperature determines the thermal energy level of the atoms, leading to the changes in materials
Additional thermal properties:
Specific heat
Thermal conductivity
These properties relate to the storage and flow of heat within a substance
©2012 John Wiley & Sons, Inc. M P Groover, Fundamentals of Modern Manufacturing 5/e
Specific Heat
The quantity of heat energy required to increase the temperature of a unit mass of material by one degree
To determine the energy to heat a certain weight of metal to a given temperature:
H = C W (T2 ‑ T1)
where H = amount of heat energy; C = specific heat of the material; W = its weight; and (T2 ‑ T1) = change in temperature
©2012 John Wiley & Sons, Inc. M P Groover, Fundamentals of Modern Manufacturing 5/e
Volumetric Specific Heat
The quantity of heat energy required to raise the temperature of a unit volume of material by one degree
Density multiplied by specific heat C
Volumetric specific heat = C
©2012 John Wiley & Sons, Inc. M P Groover, Fundamentals of Modern Manufacturing 5/e
Thermal Conductivity
Capability of a material to transfer heat through itself by the physical mechanism of thermal conduction
Thermal conduction involves the transfer of thermal energy within a material from molecule to molecule by purely thermal motions
No mass transfer
Coefficient of thermal conductivity k is generally high in metals, low in ceramics and plastics
Units for k: J/s mm C (Btu/in hr F)
©2012 John Wiley & Sons, Inc. M P Groover, Fundamentals of Modern Manufacturing 5/e
Thermal Diffusivity
The ratio of thermal conductivity to volumetric specific heat is frequently encountered in heat transfer analysis
©2012 John Wiley & Sons, Inc. M P Groover, Fundamentals of Modern Manufacturing 5/e
Thermal Properties in Manufacturing
Important in manufacturing because heat generation is common in so many processes
In some cases, heat is the energy that accomplishes the process
Heat treating, sintering of powder metals and ceramics
In other cases, heat is generated as a result of the process
Cold forming and machining of metals
©2012 John Wiley & Sons, Inc. M P Groover, Fundamentals of Modern Manufacturing 5/e
Electrical Properties
Engineering materials exhibit a great variation in their capability to conduct electricity
Flow of electrical current involves movement of charge carriers ‑ infinitesimally small particles possessing an electrical charge
In solids, these charge carriers are electrons
In a liquid solution, charge carriers are positive and negative ions
©2012 John Wiley & Sons, Inc. M P Groover, Fundamentals of Modern Manufacturing 5/e
Electrical Properties
Movement of charge carriers is driven by the presence of electric voltage
And resisted by the inherent characteristics of the material, such as atomic structure and bonding between atoms and molecules
Ohm's law: I =
where I = current, A, E = voltage, V, and R = electrical resistance,
©2012 John Wiley & Sons, Inc. M P Groover, Fundamentals of Modern Manufacturing 5/e
Electrical Resistance
Resistance in a uniform section of material (e.g., a wire) depends on its length L, cross‑sectional area A, and resistivity of the material r
or
where resistivity r has units of ‑m2/m or ‑m (‑in)
©2012 John Wiley & Sons, Inc. M P Groover, Fundamentals of Modern Manufacturing 5/e
Resistivity
Property that defines a material's capability to resist current flow
Resistivity r has units of (‑m) or (‑in)
Resistivity is not a constant; it varies, as do so many other properties, with temperature
For metals, resistivity increases with temperature
©2012 John Wiley & Sons, Inc. M P Groover, Fundamentals of Modern Manufacturing 5/e
Conductivity
Often more convenient to consider a material as conducting electrical current rather than resisting its flow
Conductivity of a material is simply the reciprocal of resistivity:
Electrical conductivity =
where conductivity has units of (‑m)‑1 or (‑in)‑1
©2012 John Wiley & Sons, Inc. M P Groover, Fundamentals of Modern Manufacturing 5/e
Materials and Electrical Properties
Metals are the best conductors of electricity, because of their metallic bonding
Most ceramics and polymers, whose electrons are tightly bound by covalent and/or ionic bonding, are poor conductors
Many of these materials are used as insulators because they possess high resistivities
©2012 John Wiley & Sons, Inc. M P Groover, Fundamentals of Modern Manufacturing 5/e
Semiconductors
A material whose resistivity lies between insulators and conductors
Most common semiconductor material is silicon, largely because of its abundance in nature, relative low cost, and ease of processing
What makes semiconductors unique is the capacity to significantly alter conductivities in their surface chemistries in very localized areas to fabricate integrated circuits
©2012 John Wiley & Sons, Inc. M P Groover, Fundamentals of Modern Manufacturing 5/e
Electrical Properties in Manufacturing
The important welding processes, such as arc welding and resistance spot welding, use electrical energy to melt the joint metal
Capability to alter electrical properties of semiconductor materials is the basis for microelectronics
©2012 John Wiley & Sons, Inc. M P Groover, Fundamentals of Modern Manufacturing 5/e
Electrochemistry
Field of science concerned with the relationship between electricity and chemical changes, and the conversion of electrical and chemical energy
In a water solution, molecules of an acid, base, or salt are dissociated into positively and negatively charged ions
Ions are the charge carriers in the solution
They allow electric current to be conducted, playing the same role that electrons play in metallic conduction
©2012 John Wiley & Sons, Inc. M P Groover, Fundamentals of Modern Manufacturing 5/e
Terms in Electrochemical Processes
Electrolyte – the ionized solution
Electrodes – where current enters and leaves the solution in electrolytic conduction
Anode – positive electrode
Cathode – negative electrode
The whole arrangement is called an electrolytic cell
©2012 John Wiley & Sons, Inc. M P Groover, Fundamentals of Modern Manufacturing 5/e
Electrolysis
The name given to these chemical changes occurring in the solution
At each electrode, chemical reaction occurs, such as:
Deposition or dissolution of material
Decomposition of gas from the solution
©2012 John Wiley & Sons, Inc. M P Groover, Fundamentals of Modern Manufacturing 5/e
Hydrogen Through Electrolysis – Ocean Geothermal Energy Foundation
Electrolysis in Manufacturing Processes
Electroplating ‑ an operation that adds a thin coating of one metal (e.g., chromium) to the surface of a second metal (e.g., steel) for decorative or other purposes
Electrochemical machining ‑ a process in which material is removed from the surface of a metal part
Production of hydrogen and oxygen gases
©2012 John Wiley & Sons, Inc. M P Groover, Fundamentals of Modern Manufacturing 5/e
Video
Copper Plating – Easy Electrolysis & Electroplating
(https://youtu.be/kEkWRE028EY)
©2012 John Wiley & Sons, Inc. M P Groover, Fundamentals of Modern Manufacturing 5/e
oleObject1.bin
image2.emf
oleObject2.bin
image3.wmf
oleObject3.bin
image4.emf
oleObject4.bin
image5.emf
oleObject5.bin
image6.emf
image7.png
image1.png
,
MECHANICAL PROPERTIES OF MATERIALS
Stress‑Strain Relationships
Hardness
Effect of Temperature on Properties
©2012 John Wiley & Sons, Inc. M P Groover, Fundamentals of Modern Manufacturing 5/e
Mechanical Properties in Design and Manufacturing
Mechanical properties determine a material’s behavior when subjected to mechanical stresses
Properties include elastic modulus, ductility, hardness, and various measures of strength
©2012 John Wiley & Sons, Inc. M P Groover, Fundamentals of Modern Manufacturing 5/e
Stress‑Strain Relationships
Three types of static stresses to which materials can be subjected:
Tensile – stretching the material
Compressive – squeezing the material
Shear – causing adjacent portions of the material to slide against each other
Stress‑strain curve – basic relationship that describes mechanical properties for all three types
©2012 John Wiley & Sons, Inc. M P Groover, Fundamentals of Modern Manufacturing 5/e
Tensile Test
Most common test for studying stress‑strain relationship, especially metals
In the test, a force pulls the material, elongating it and reducing its diameter
(left) Tensile force applied and (right) resulting elongation of material
©2012 John Wiley & Sons, Inc. M P Groover, Fundamentals of Modern Manufacturing 5/e
Tensile Test Specimen
ASTM (American Society for Testing and Materials) specifies preparation of test specimen
©2012 John Wiley & Sons, Inc. M P Groover, Fundamentals of Modern Manufacturing 5/e
Tensile Test Setup
Tensile testing machine
©2012 John Wiley & Sons, Inc. M P Groover, Fundamentals of Modern Manufacturing 5/e
Engineering Stress
Defined as force divided by original area:
©2012 John Wiley & Sons, Inc. M P Groover, Fundamentals of Modern Manufacturing 5/e
where s = engineering stress, F = applied force, and Ao = original area of test specimen
Engineering Strain
Defined at any point in the test as
©2012 John Wiley & Sons, Inc. M P Groover, Fundamentals of Modern Manufacturing 5/e
where e = engineering strain; L = length at any point during elongation; and Lo = original gage length
Typical Engineering Stress-Strain Plot
Typical engineering stress‑strain plot in a tensile test of a metal
Two regions:
Elastic region
Plastic region
©2012 John Wiley & Sons, Inc. M P Groover, Fundamentals of Modern Manufacturing 5/e
Tensile Test Sequence
(1) No load; (2) uniform elongation and area reduction; (3) maximum load; (4) necking; (5) fracture; (6) final length
©2012 John Wiley & Sons, Inc. M P Groover, Fundamentals of Modern Manufacturing 5/e
Elastic Region in Stress‑Strain Curve
Relationship between stress and strain is linear
Hooke's Law: e = E e
where E = modulus of elasticity
Material returns to its original length when stress is removed
E is a measure of the inherent stiffness of a material
Its value differs for different materials
©2012 John Wiley & Sons, Inc. M P Groover, Fundamentals of Modern Manufacturing 5/e
Yield Point in Stress‑Strain Curve
As stress increases, a point in the linear relationship is finally reached when the material begins to yield
Yield point Y can be identified by the change in slope at the upper end of the linear region
Y = a strength property
Other names for yield point:
Yield strength
Yield stress
Elastic limit
©2012 John Wiley & Sons, Inc. M P Groover, Fundamentals of Modern Manufacturing 5/e
Plastic Region in Stress‑Strain Curve
Yield point marks the beginning of plastic deformation
The stress-strain relationship is no longer guided by Hooke's Law
©2012 John Wiley & Sons, Inc. M P Groover, Fundamentals of Modern Manufacturing 5/e
Tensile Strength in Stress‑Strain Curve
Elongation is accompanied by a uniform reduction in cross‑sectional area, consistent with maintaining constant volume
Finally, the applied load F reaches a maximum value, and engineering stress at this point is called the tensile strength TS (a.k.a. ultimate tensile strength)
TS =
©2012 John Wiley & Sons, Inc. M P Groover, Fundamentals of Modern Manufacturing 5/e
Ductility in Tensile Test
Ability of a material to plastically strain without fracture
Ductility measure = elongation EL
©2012 John Wiley & Sons, Inc. M P Groover, Fundamentals of Modern Manufacturing 5/e
where EL = elongation; Lf = specimen length at fracture; and Lo = original specimen length
Lf is measured as the distance between gage marks after two pieces of specimen are put back together
Example
A tensile test specimen has a starting gage length = 50 mm and a cross-sectional area = 200 mm2. During the test, the specimen yields under a load of 32,000 N (this is the 0.2% offset) at a gage length of 50.2 mm. The maximum load of 65,000 N is reached at a gage length of 57.7 mm just before necking begins. Final fracture occurs at a gage length of 63.5 mm. Determine (a) yield strength, (b) modulus of elasticity, (c) tensile strength, (d) engineering strain at maximum load, and (e) percent elongation.
©2012 John Wiley & Sons, Inc. M P Groover, Fundamentals of Modern Manufacturing 5/e
Solution
©2012 John Wiley & Sons, Inc. M P Groover, Fundamentals of Modern Manufacturing 5/e
True Stress
Stress value obtained by dividing the instantaneous area into applied load
©2012 John Wiley & Sons, Inc. M P Groover, Fundamentals of Modern Manufacturing 5/e
where = true stress; F = force; and A = actual (instantaneous) area resisting the load
True Strain
Provides a more realistic assessment of "instantaneous" elongation per unit length
©2012 John Wiley & Sons, Inc. M P Groover, Fundamentals of Modern Manufacturing 5/e
True Stress-Strain Curve
True stress‑strain curve for previous engineering stress‑strain plot
©2012 John Wiley & Sons, Inc. M P Groover, Fundamentals of Modern Manufacturing 5/e
Strain Hardening in Stress-Strain Curve
Note that true stress increases continuously in the plastic region until necking
In the engineering stress‑strain curve, the significance of this was lost because stress was based on the original area value
It means that the metal is becoming stronger as strain increases
This is the property called strain hardening
©2012 John Wiley & Sons, Inc. M P Groover, Fundamentals of Modern Manufacturing 5/e
Videoes
Understanding Material Strength, Ductility and Toughness
( https://youtu.be/WSRqJdT2COE)
Engineering vs True Stress
(https://youtu.be/rZN5uSbSvSo)
©2012 John Wiley & Sons, Inc. M P Groover, Fundamentals of Modern Manufacturing 5/e
22
Compression Test
Applies a load that squeezes the ends of a cylindrical specimen between two platens
Compression force applied to test piece and resulting change in height and diameter
©2012 John Wiley & Sons, Inc. M P Groover, Fundamentals of Modern Manufacturing 5/e
Compression Test Setup
©2012 John Wiley & Sons, Inc. M P Groover, Fundamentals of Modern Manufacturing 5/e
Engineering Stress in Compression
As the specimen is compressed, its height is reduced and cross‑sectional area is increased
= –
where Ao = original area of the specimen
©2012 John Wiley & Sons, Inc. M P Groover, Fundamentals of Modern Manufacturing 5/e
Engineering Strain in Compression
Engineering strain is defined
©2012 John Wiley & Sons, Inc. M P Groover, Fundamentals of Modern Manufacturing 5/e
Since height is reduced during compression, value of e is negative (the negative sign is usually ignored when expressing compression strain)
Collepals.com Plagiarism Free Papers
Are you looking for custom essay writing service or even dissertation writing services? Just request for our write my paper service, and we'll match you with the best essay writer in your subject! With an exceptional team of professional academic experts in a wide range of subjects, we can guarantee you an unrivaled quality of custom-written papers.
Get ZERO PLAGIARISM, HUMAN WRITTEN ESSAYS
Why Hire Collepals.com writers to do your paper?
Quality- We are experienced and have access to ample research materials.
We write plagiarism Free Content
Confidential- We never share or sell your personal information to third parties.
Support-Chat with us today! We are always waiting to answer all your questions.
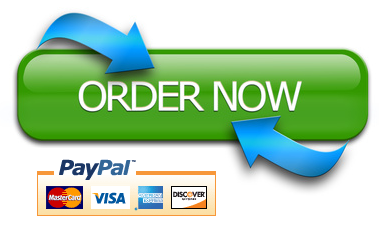
All Rights Reserved Terms and Conditions
College pals.com Privacy Policy 2010-2018