Post one new topic and?two replies to classmates for this discussion. The posts should be based on topics covered in the text or current events that you may read in the newspaper
Discussion Post:
- Post one new topic and two replies to classmates for this discussion.
- The posts should be based on topics covered in the text or current events that you may read in the newspaper, on the internet, or in a magazine.
- Your grade will be based on the quality of your contribution, how you have tied your contribution to what you have learned, and your professional communication skills.
Chapter 9– Capacity Planning
& Facility Location
Operations Management
by
R. Dan Reid & Nada R. Sanders
*
Welcome to Chapter 9 – Capacity Planning and Facility Location. In this session, we’ll be looking at a variety of ways capacity planning is completed as well as several different methods that could be used to decide where to locate a facility.
Learning Objectives
- Define capacity planning and location analysis
- Describe relationship between capacity planning and location, and their importance to the organization
- Explain the steps involved in capacity planning and location analysis
- Describe the decision support tools used for capacity planning
- Identify key factors in location analysis
- Describe the decision support tools used for location analysis
*
Learning objectives to be looked at include:
- Defining capacity planning and location analysis.
- Describe the relationship between capacity planning and location and their importance to the organization.
- Explain the steps involved in capacity planning and location analysis.
- Describe the decision support tools used for capacity planning.
- Identify key factors in location analysis.
- Describe the decision support tools used for location analysis.
After studying this chapter, you’ll have the ability to objectively evaluate different location options and build a confidence level based on the formal methods used to select a site.
Capacity planning
- Capacity is the maximum output rate of a production or service facility
- Capacity planning is the process of establishing the output rate that may be needed at a facility:
- Capacity is usually purchased in “chunks”
- Strategic issues: how much and when to spend capital for additional facility & equipment
- Tactical issues: workforce & inventory levels, & day-to-day use of equipment
*
We’ll first evaluate capacity planning. The definition of capacity is the maximum output rate of a production or service facility. An organization’s capacity is constrained based on the amount of equipment, amount of space, and the amount of labor. Out of these three, typically the easiest and quickest to correct is the amount of labor. The other two require capital dollars to address.
Capacity planning is a must for any organization. The output rate of goods, the speed at which a product can be shipped or the number of people that can be serviced all have impacts on the firm’s success and profitability. It’s critical the output rate required to service the customer is supported by adequate capacity. Typically, capacity is purchased in chucks – meaning its hard and at times financially foolish to increase machine capacity and floor space in small pieces. The organization determines how much and when to spend the capital based on the information being received from marketing and the customers. Local management follows up from the tactical side in determining how to use the space and equipment efficiently.
Measuring Capacity Examples
- There is no one best way to measure capacity
- Output measures like kegs per day are easier to understand
- With multiple products, inputs measures work better
*
There are many different ways capacity can be measured. On this slide you see four different types of businesses and the varied ways their capacity is measured. Note both input and output measures need evaluated.
The key of any measurement is that it’s meaningful, it supports the critical success factors of your organization and it gives you the ability to make good decisions.
Capacity Information Needed
- Design capacity:
- Maximum output rate under ideal conditions
- A bakery can make 30 custom cakes per day when pushed at holiday time
- Effective capacity:
- Maximum output rate under normal (realistic) conditions
- On the average this bakery can make 20 custom cakes per day
*
There are two different ways that capacity can be evaluated.
The first is design capacity. This measure represents what the maximum output rate is under ideal conditions. In other words, what can be done with the equipment and space if more hours or people are thrown at it. Many organizations experience this during the holidays, particularly Christmas time. Stores have a limited amount of room for merchandise, but they ramp up their staffing and extend their hours to make it more convenient for shoppers.
The second is effective capacity. This measure represents what the maximum output rate is under normal or realistic conditions. This is where the firm would want to run the vast majority of the time. Employee effectiveness is improved when avoiding long hours, time is available to perform preventative maintenance on equipment and a more stable workforce can be maintained.
Calculating Capacity Utilization
- Measures how much of the available capacity is actually being used:
- Measures effectiveness
- Use either effective or design capacity in denominator
*
This is the formula used to calculate capacity utilization. As shown, use either effective or design capacity in the denominator.
Example of Computing Capacity Utilization: In the bakery example the design capacity is 30 custom cakes per day. Currently the bakery is producing 28 cakes per day. What is the bakery’s capacity utilization relative to both design and effective capacity?
- The current utilization is only slightly below its design capacity and considerably above its effective capacity
- The bakery can only operate at this level for a short period of time
*
This slide provides a very good example of comparing effective and design capacity. Note how high the percentage is for effective capacity. An organization can only operate at this level for a short period of time.
How Much Capacity Is Best?
- The Best Operating Level is the output that results in the lowest average unit cost
- Economies of Scale:
- Where the cost per unit of output drops as volume of output increases
- Spread the fixed costs of buildings & equipment over multiple units, allow bulk purchasing & handling of material
- Diseconomies of Scale:
- Where the cost per unit rises as volume increases
- Often caused by congestion (overwhelming the process with too much work-in-process) and scheduling complexity
*
When dealing with capacity, there is definitely a best operating level where the unit cost is the lowest. A firm needs to assure they keep proper balance and not put themselves in a deficit situation.
The goal is to maintain a positive economies of scale – which is when cost per unit of output drops as volume of output increases. When a firm enters a diseconomies of scale, the cost per unit rises as volume increases. This is seen when the process is overwhelmed with too much work-in-process. It also can be caused by scheduling complexity based on the type of products being manufactured.
Other Capacity Considerations
- Focused factories:
- Small, specialized facilities with limited objectives
- Plant within a plant (PWP):
- Segmenting larger operations into smaller operating units with focused objectives
- Subcontractor networks:
- Outsource non-core items to free up capacity for what you do well
*
There are other considerations evaluated when looking at capacity.
First, focused factories are an option to stay more product focused. They are specialized facilities that are laid out according to product type. The equipment needed to produce that product line is located in that portion of the factory and is dedicated to that area.
Second, a plant within a plant (PWP) segments larger operations into smaller operating units with focused objectives. This allows the area to be controlled easier and provides the chance of isolating problems more readily due to the more focused approach.
Third, subcontractor networks have become more popular as organizations attempt to lower their capital equipment intensity. Firms decide to outsource non-core items that outside contractors have the capability of making. This opens up capacity for products that are more specialized and ones an organization wishes to keep inside.
Making Capacity Planning Decisions
- The three-step procedure for making capacity planning decisions is as follows:
- Step 1: Identify Capacity Requirements
- Step 2: Develop Capacity Alternatives
- Step 3: Evaluate Capacity Alternatives
*
Capacity planning decisions are broken down into three steps:
- Identify capacity requirements – where is it that you need help
- Develop capacity alternatives – brainstorm all the possibilities
- Evaluate capacity alternatives – determine which one will address your problem the best and prepare to implement it.
Evaluating Capacity Alternatives
- Could do nothing, or expand large now, or expand small now with option to add later
- Use Decision Trees analysis tool:
- A modeling tool for evaluating sequential decisions
- Identify the alternatives at each point in time (decision points), estimate probable consequences of each decision (chance events) & the ultimate outcomes (e.g.: profit or loss)
*
There are three broad alternatives to address capacity.
One is to do nothing. It may be decided the capacity currently in place is all the capital the firm wishes to invest. Outsourcing as business grows would be a likely result of this approach.
Second is to expand large now. This alternative comes with some risks. The organization must be confident in the marketing plan and customer feedback to step out and invest a large amount of dollars. The key is to assure the firm can remain profitable during the expansion period.
Third is to expand small now with an option to add later. This is without question the most conservative approach. Putting the infrastructure in place with the option to expand provides flexibility to grow and to invest capital as needed.
One way to evaluate this is to use the Decision Tree analysis tool. It’s purpose is to evaluate sequential decisions. In addition, it identifies the alternatives at each point in time and estimates probable consequences of each decision including the ultimate outcomes.
Example Using Decision Trees: A restaurant owner has determined that she needs to expand her facility. The alternatives are to expand large now and risk smaller demand, or expand on a smaller scale now knowing that she might need to expand again in three years. Which alternative would be most attractive?
- The likelihood of demand being high is .70
- The likelihood of demand being low is .30
- Large expansion yields profits of $300K(high dem.) or $50k(low dem.)
- Small expansion yields profits of $80K if demand is low
- Small expansion followed by high demand and later expansion yield a profit of $200K at that point. No expansion at that point yields profit of $150K
*
This slide provides an example on how the decision tree analysis works. Note the different paths being examined.
This example is found on pages 325-327 of the textbook. Feel free to read through the details of this problem and see why a certain direction is taken.
Evaluating the Decision Tree
- At decision point 2, choose to expand to maximize profits ($200,000 > $150,000)
- Calculate expected value of small expansion:
- EVsmall = 0.30($80,000) + 0.70($200,000) = $164,000
- Calculate expected value of large expansion:
- EVlarge = 0.30($50,000) + 0.70($300,000) = $225,000
- At decision point 1, compare alternatives & choose the large expansion to maximize the expected profit:
- $225,000 > $164,000
- Choose large expansion despite the fact that there is a 30% chance it’s the worst decision:
- Take the calculated risk!
*
This slide provides the calculation summary of the preceding decision tree analysis.
Facility Location
- Three most important factors in real estate:
Location
Location
Location
- Facility location is the process of identifying the best geographic location for a service or production facility
*
You may have heard before there are three important factors with selecting real estate – that being location, location and location. It goes without saying that when an organization decides where to locate a new facility, it’s very important the correct site is selected.
Facility location is the process of identifying the best geographic location for a service or production facility. There are many stories of businesses placing a facility in the wrong location, only to find them closing it shortly thereafter. Proper research must be conducted to avoid this situation.
Location Factors
- Proximity to suppliers:
- Reduce transportation costs of perishable or bulky raw materials
- Proximity to customers:
- E.g.: high population areas, close to JIT partners
- Proximity to labor:
- Local wage rates, attitude toward unions, availability of special skills (e.g.: silicon valley)
*
Three primary location factors that businesses look at to reduce the chances of failure are proximity to suppliers, proximity to customers and proximity to labor.
Proximity to suppliers reduces the transportation costs of perishable or bulky raw materials. It also reduces the chances of late delivery due to weather, especially if located in areas with a lot of ice and snow. Large automobile and over the road manufacturers have even located key suppliers on their property.
Proximity to customers is also a key. High population areas are important – it makes it that much easier for customers to purchase if in an area where other shops and many people are at. You may notice in a shopping center that similar stores build in the same area. Demographic studies are a tool to decide where these shopping areas should be built.
Proximity to labor is important as well. There needs to be an adequate labor pool available and must be skilled in the areas of the company’s core competencies. Local wage rates and attitudes toward unions are two factors evaluated when looking at labor.
More Location Factors
- Community considerations:
- Local community’s attitude toward the facility (e.g.: prisons, utility plants, etc.)
- Site considerations:
- Local zoning & taxes, access to utilities, etc.
- Quality-of-life issues:
- Climate, cultural attractions, commuting time, etc.
- Other considerations:
- Options for future expansion, local competition, etc.
*
Other location factors include community and site considerations as well as quality of life issues.
It’s important that a local community has a positive attitude toward an organization moving into their area. Facilities housing prisons, mega livestock farms and utility plants can be a challenge in getting buy-in. Community support allows construction to progress smoothly and provides the base for a strong partnership going forward.
The financial package a community puts together to entice a company to locate in their area can be a drawing card. That coupled with local zoning and tax abatements are a lever companies can use to reduce their cost of locating in an area. Access to utilities, highways and railways are also areas viewed critical in location selection.
Quality of life issues such as climate, cultural attractions and commuting time are considerations looked at when understanding where the labor pool will come from. Companies need a high confidence level they can recruit high level candidates to their location if located at this new site.
Other considerations looked at are options for future expansion and if there is any local competition.
Should Firm Go Global?
- Potential advantages:
- Inside track to foreign markets, avoid trade barriers, gain access to cheaper labor
- Potential disadvantages:
- Political risks may increase, loss of control of proprietary technology, local infrastructure (roads & utilities) may be inadequate, high inflation
- Other issues:
- Language barriers, different laws & regulations, different business cultures
*
One question a number of companies are asking today is whether to go global. When evaluating, there are advantages and disadvantages along with other issues that must be taken into consideration.
First, the advantages are an inside track to foreign markets, the ability to avoid trade barriers and the access to cheaper labor.
Second, the disadvantages include the increase in political risks due to being controlled by someone else besides the United States government, the loss of control of proprietary technology, the inadequacy of the local infrastructure such as roads and utilities, and the increased chance of high or uncontrolled inflation.
Lastly, others issues that play a role are the language barriers between the company and the country they are locating in, the different laws and regulations another country has in place for corporations and the different business cultures the company would need to operate within.
Location Analysis Methods
- Analysis should follow 3 step process:
- Step 1: Identify dominant location factors
- Step 2: Develop location alternatives
- Step 3: Evaluate locations alternatives
- Factor rating method
- Load-distance model
- Center of gravity approach
- Break-even analysis
*
The remainder of this chapter will be focused on describing different analysis techniques.
Four different methods will be looked at:
- Factor rating method
- Load-distance model
- Center of gravity approach
- Break-even analysis
Factor Rating Example
*
The first analysis is the rating factor. It basically is a technique that puts greater weight on those items that are considered more important. A full explanation of this example can be found on page 333 in example 9.3.
A Load-Distance Model Example: Matrix Manufacturing is considering where to locate its warehouse in order to service its four Ohio stores located in Cleveland, Cincinnati, Columbus, Dayton. Two sites are being considered; Mansfield and Springfield, Ohio. Use the load-distance model to make the decision.
- Calculate the rectilinear distance:
- Multiply by the number of loads between each site and the four cities
*
The second analysis is the load-distance model. It’s a procedure that evaluates location alternatives by calculating the rectilinear distance between each location.
A detailed explanation of this process can be found on pages 334-336.
Calculating the Load-Distance Score for Springfield vs. Mansfield
Collepals.com Plagiarism Free Papers
Are you looking for custom essay writing service or even dissertation writing services? Just request for our write my paper service, and we'll match you with the best essay writer in your subject! With an exceptional team of professional academic experts in a wide range of subjects, we can guarantee you an unrivaled quality of custom-written papers.
Get ZERO PLAGIARISM, HUMAN WRITTEN ESSAYS
Why Hire Collepals.com writers to do your paper?
Quality- We are experienced and have access to ample research materials.
We write plagiarism Free Content
Confidential- We never share or sell your personal information to third parties.
Support-Chat with us today! We are always waiting to answer all your questions.
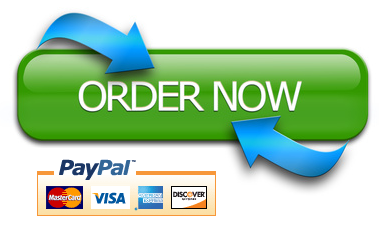
All Rights Reserved Terms and Conditions
College pals.com Privacy Policy 2010-2018