Financial Analysis for Master Budget Planning Interpret core managerial finance concepts and data. Analyze operational budget drivers and variances. Interpret financia
Deliverable 7 – Financial Analysis for Master Budget Planning
Assignment Content
- Competency
- Interpret core managerial finance concepts and data.
- Analyze operational budget drivers and variances.
- Interpret financial decision-making criteria.
- Evaluate financing strategies for business operations.
- Evaluate operational performance using analytic and comparative techniques.
- Devise risk mitigation strategies in financial management.
- Student Success Criteria
View the grading rubric for this deliverable by selecting the “This item is graded with a rubric” link, which is located in the Details & Information pane.Scenario
You are a department manager for a distribution team that packages and ships products from a warehouse location to fulfill customer orders. Your company has been acquired by a larger firm. The new owners are requesting that each department manager prepare a master budget for the upcoming year and submit it for approval. The submission must include a written justification of the requested amount and at least one risk mitigation action to control or reduce costs.The information available to meet this request includes:
- The department’s expenses, staffing, and output for the past 12 months;
- Metrics, financial and operational, that can be used to compare the department’s performance and output to a department that provides similar distribution support to another division of the company;
- One potential efficiency project with two available financing options;
- Data on the company’s historic employee practices such as annual raises and bonuses; and
- The level of output that the department must meet in the upcoming year based on the new owners’ sales goals.
- Instructions
Using the information provided, as well as relevant economic data researched independently, make decisions about: - The staffing level required to meet the expected output requirements;
- The annual raises and bonuses that should be included in the budget;
- Whether the efficiency project option should be implemented, and if so, using which financing option; and
- The cost control (i.e. risk mitigation) action(s) for implementation.
- From your decisions, prepare a master budget for the upcoming year in Excel. Then, prepare a written justification, memo-style, for the budget that discusses your decisions and the rationale for each. Include support for your decisions from your analysis of the data and the financial and operational metrics (historical and expected) as well as at least one external economic or industry source.
In the justification memo, include one visual (chart, graph, etc.) created from the data. The purpose and type of visual selected should be based on the data being highlighted. Examples include a summary pie chart of the total budget, a bar chart comparing the department’s historical metrics to the expected metrics with the new budget, or costs across time to implement the efficiency project using the recommended financing options.
Submit an Excel file with the new master budget and a justification memo with embedded visual.
Criterion 1
A – 4 – Mastery
Prepared a professional style master budget for the upcoming year in Excel; utilized all of the information provided for each decision.
Criterion 2
A – 4 – Mastery
Submitted an extensive memo-style justification for the budget that thoroughly discusses the decisions and the rationale for each.
Criterion 3
A – 4 – Mastery
Thoroughly communicates the support for the decisions from the analysis of the data, financial, and operational metrics (historical and expected) as well as at least one external economic or industry source.
Criterion 4
A – 4 – Mastery
Submitted a very professional, formatted Excel file with the new master budget and a justification memo with embedded visual; the type of visual selected was based on the data being highlighted.
,
Budget Prior 12 Months
Warehouse Distribution Budget | (Warehouse budget covers operating expenses only; product sales, corporate expenses such as taxes, etc. are covered by other company departments.) | |||||||||||||||
Year Ending December 31 | Formulas | |||||||||||||||
Statement in U.S. Dollars | Actual | Actual | Actual | Actual | Actual | Actual | Actual | Actual | Actual | Actual | Actual | Budget | ||||
Expenses | January | February | March | April | May | June | July | August | September | October | November | December | Total Year | Comments | ||
Warehouse Operations | ||||||||||||||||
Receiving Team | ||||||||||||||||
Employee Wages Including Overtime | 7,785 | 7,455 | 7,556 | 7,069 | 7,313 | 7,042 | 7,293 | 6,825 | 7,562 | 7,556 | 7,581 | 7,324 | 88,361 | See Staffing worksheet | ||
Employee Bonus and Benefit Programs | 1,946 | 1,864 | 1,889 | 1,767 | 1,828 | 1,761 | 1,823 | 1,706 | 1,891 | 1,889 | 1,895 | 1,831 | 22,090 | See Staffing worksheet | ||
Stocking Team | ||||||||||||||||
Employee Wages Including Overtime | 19,811 | 18,969 | 19,230 | 18,250 | 18,609 | 18,369 | 17,969 | 18,369 | 19,245 | 18,230 | 18,748 | 18,868 | 224,667 | See Staffing worksheet | ||
Employee Bonus and Benefit Programs | 4,953 | 4,742 | 4,808 | 4,563 | 4,652 | 4,592 | 4,492 | 4,592 | 4,811 | 4,558 | 4,687 | 4,717 | 56,167 | See Staffing worksheet | ||
Receiving and Stocking Operations | ||||||||||||||||
Equipment Rentals | 3,000 | 3,000 | 3,000 | 3,000 | 3,000 | 3,000 | 3,000 | 3,000 | 3,000 | 3,000 | 3,000 | 3,000 | 36,000 | 1 warehouse forklift for every 2 receiving and stocking employees @ $500 per month per truck | ||
Picking Team | ||||||||||||||||
Employee Wages Including Overtime | 31,683 | 27,777 | 30,752 | 28,769 | 29,761 | 27,777 | 28,944 | 28,333 | 30,777 | 30,752 | 30,784 | 29,629 | 355,738 | See Staffing worksheet | ||
Employee Bonus and Benefit Programs | 7,921 | 6,944 | 7,688 | 7,192 | 7,440 | 6,944 | 7,236 | 7,083 | 7,694 | 7,688 | 7,696 | 7,407 | 88,935 | See Staffing worksheet | ||
Packing Team | ||||||||||||||||
Employee Wages Including Overtime | 59,648 | 52,294 | 57,898 | 54,162 | 56,030 | 52,294 | 52,791 | 52,294 | 57,944 | 57,898 | 54,529 | 54,876 | 662,658 | See Staffing worksheet | ||
Employee Bonus and Benefit Programs | 14,912 | 13,074 | 14,475 | 13,541 | 14,008 | 13,074 | 13,198 | 13,074 | 14,486 | 14,475 | 13,632 | 13,719 | 165,665 | See Staffing worksheet | ||
Picking and Packing Operations | ||||||||||||||||
Equipment Rentals | 2,100 | 2,100 | 2,100 | 2,100 | 2,100 | 2,100 | 2,100 | 2,100 | 2,100 | 2,100 | 2,100 | 2,100 | 25,200 | 1 order picker forklift for every 2 picking employees @ $300 per month per truck | ||
Equipment Depreciation | 1,000 | 1,000 | 1,000 | 1,000 | 1,000 | 1,000 | 1,000 | 1,000 | 1,000 | 1,000 | 1,000 | 1,000 | 12,000 | $1,000 per month continues in new year | ||
Supplies – Customer Shipments | 100,623 | 90,104 | 97,669 | 91,589 | 94,519 | 89,247 | 90,529 | 89,534 | 97,747 | 96,823 | 94,459 | 94,500 | 1,127,343 | See General Info for rate per order | ||
Third Party Shipping (UPS, FedEx) | 536,654 | 480,555 | 520,901 | 488,474 | 504,101 | 475,984 | 482,820 | 477,513 | 521,316 | 516,388 | 503,780 | 504,000 | 6,012,486 | See General Info for rate per order | ||
Sub-Total Expenses | 792,036 | 709,878 | 768,965 | 721,476 | 744,361 | 703,184 | 713,195 | 705,423 | 769,573 | 762,356 | 743,892 | 742,971 | 8,877,308 | |||
Warehouse General & Administrative | ||||||||||||||||
Rent | 20,000 | 20,000 | 20,000 | 20,000 | 20,000 | 20,000 | 20,000 | 20,000 | 20,000 | 20,000 | 20,000 | 20,000 | 240,000 | Remains fixed in new year; warehouse has capacity for 50% growth in volume | ||
Insurance | 6,667 | 6,667 | 6,667 | 6,667 | 6,667 | 6,667 | 6,667 | 6,667 | 6,667 | 6,667 | 6,667 | 6,667 | 80,000 | Remains fixed in new year | ||
Repairs and Maintenance | 5,650 | 2,800 | 8,820 | 1,000 | 18,270 | Varies based on equipment | ||||||||||
Utilities | 1,840 | 1,693 | 1,803 | 1,858 | 1,877 | 1,849 | 1,950 | 1,987 | 1,822 | 1,766 | 1,748 | 1,900 | 22,094 | Average of $1,840 per month | ||
Licenses and Fees | 12,000 | 12,000 | Remains fixed in new year | |||||||||||||
Administrative and Management Salaries | 31,183 | 31,183 | 31,183 | 31,183 | 31,183 | 31,183 | 31,183 | 31,183 | 31,183 | 31,183 | 31,183 | 31,183 | 374,200 | See Staffing worksheet | ||
Employee Bonus and Benefit Programs | 11,338 | 11,338 | 11,338 | 11,338 | 11,338 | 11,338 | 11,338 | 11,338 | 11,338 | 11,338 | 11,338 | 11,105 | 135,827 | See Staffing worksheet | ||
Miscellaneous | 368 | 55 | 147 | 530 | 222 | 500 | 1,822 | |||||||||
Shrinkage | 23,628 | 23,628 | 23,628 | 23,628 | 23,628 | 23,628 | 23,628 | 23,628 | 23,628 | 23,628 | 23,628 | 23,628 | 283,541 | See Performance Metrics for % and General Info for values | ||
Supplies – Office | 35 | 20 | 88 | 45 | 76 | 10 | 150 | 22 | 65 | 100 | 611 | |||||
Sub-Total Expenses | 95,060 | 94,530 | 100,413 | 106,822 | 97,539 | 94,742 | 95,307 | 94,804 | 103,608 | 94,605 | 94,852 | 96,083 | 1,168,364 | |||
Net Operating Expense | 887,095 | 804,407 | 869,378 | 828,298 | 841,900 | 797,925 | 808,502 | 800,227 | 873,181 | 856,961 | 838,743 | 839,054 | 10,045,673 | |||
Beginning of Year Budget | 10,000,000 | |||||||||||||||
Variance | (45,673) | |||||||||||||||
Variance % | -0.46% |
Staffing Prior 12 Months
Prior Year Staffing by Team | Monthly Salary | Hourly Rate | Overtime Rate | Avg Hours per Month | Avg OT Hours per Month | Bonus % | Benefits % | Comments | |
Receiving Team 1 | $ 13.50 | $ 20.25 | 173.3 | 5.0 | 5% | 20% | Annual raises for the receiving team have averaged 4% in each of the past 3 years | ||
Receiving Team 2 | $ 13.50 | $ 20.25 | 173.3 | 5.0 | 5% | 20% | Benefits were 20% of wages in the prior year; HR has informed your group that this percent increases to 22% in the new year | ||
Receiving Team 3 | $ 13.50 | $ 20.25 | 173.3 | 5.0 | 5% | 20% | |||
Receiving Team Open | $ – 0 | 173.3 | 5.0 | 5% | 20% | ||||
Receiving Team Open | $ – 0 | 173.3 | 5.0 | 5% | 20% | ||||
Stocking Team 1 | $ 12.50 | $ 18.75 | 173.3 | 2.0 | 5% | 20% | Annual raises for the stocking team have averaged 3% in each of the past 3 years | ||
Stocking Team 2 | $ 14.00 | $ 21.00 | 173.3 | 2.0 | 5% | 20% | Benefits were 20% of wages in the prior year; HR has informed your group that this percent increases to 22% in the new year | ||
Stocking Team 3 | $ 14.00 | $ 21.00 | 173.3 | 2.0 | 5% | 20% | |||
Stocking Team 4 | $ 13.50 | $ 20.25 | 173.3 | 2.0 | 5% | 20% | |||
Stocking Team 5 | $ 13.50 | $ 20.25 | 173.3 | 2.0 | 5% | 20% | |||
Stocking Team 6 | $ 13.50 | $ 20.25 | 173.3 | 2.0 | 5% | 20% | |||
Stocking Team 7 | $ 13.00 | $ 19.50 | 173.3 | 2.0 | 5% | 20% | |||
Stocking Team 8 | $ 13.00 | $ 19.50 | 173.3 | 2.0 | 5% | 20% | |||
Stocking Team Open | $ – 0 | 173.3 | 2.0 | 5% | 20% | ||||
Stocking Team Open | $ – 0 | 173.3 | 2.0 | 5% | 20% | ||||
Stocking Team Open | $ – 0 | 173.3 | 2.0 | 5% | 20% | ||||
Picking Team 1 | $ 11.00 | $ 16.50 | 173.3 | 6.0 | 5% | 20% | Annual raises for the picking team have averaged 3% in each of the past 3 years | ||
Picking Team 2 | $ 10.00 | $ 15.00 | 173.3 | 6.0 | 5% | 20% | Benefits were 20% of wages in the prior year; HR has informed your group that this percent increases to 22% in the new year | ||
Picking Team 3 | $ 9.50 | $ 14.25 | 173.3 | 6.0 | 5% | 20% | |||
Picking Team 4 | $ 10.50 | $ 15.75 | 173.3 | 6.0 | 5% | 20% | |||
Picking Team 5 | $ 11.00 | $ 16.50 | 173.3 | 6.0 | 5% | 20% | |||
Picking Team 6 | $ 10.50 | $ 15.75 | 173.3 | 6.0 | 5% | 20% | |||
Picking Team 7 | $ 11.50 | $ 17.25 | 173.3 | 6.0 | 5% | 20% | |||
Picking Team 8 | $ 11.00 | $ 16.50 | 173.3 | 6.0 | 5% | 20% | |||
Picking Team 9 | $ 11.00 | $ 16.50 | 173.3 | 6.0 | 5% | 20% | |||
Picking Team 10 | $ 13.50 | $ 20.25 | 173.3 | 6.0 | 5% | 20% | |||
Picking Team 11 | $ 10.50 | $ 15.75 | 173.3 | 6.0 | 5% | 20% | |||
Picking Team 12 | $ 14.50 | $ 21.75 | 173.3 | 6.0 | 5% | 20% | |||
Picking Team 13 | $ 14.00 | $ 21.00 | 173.3 | 6.0 | 5% | 20% | |||
Picking Team 14 | $ 14.00 | $ 21.00 | 173.3 | 6.0 | 5% | 20% | |||
Picking Team Open | $ – 0 | 173.3 | 6.0 | 5% | 20% | ||||
Picking Team Open | $ – 0 | 173.3 | 6.0 | 5% | 20% | ||||
Picking Team Open | $ – 0 | 173.3 | 6.0 | 5% | 20% | ||||
Picking Team Open | $ – 0 | 173.3 | 6.0 | 5% | 20% | ||||
Packing Team 1 | $ 13.50 | $ 20.25 | 173.3 | 4.0 | 5% | 20% | Annual raises for the packing team have averaged 2% in each of the past 3 years | ||
Packing Team 2 | $ 13.50 | $ 20.25 | 173.3 | 4.0 | 5% | 20% | Benefits were 20% of wages in the prior year; HR has informed your group that this percent increases to 22% in the new year | ||
Packing Team 3 | $ 11.00 | $ 16.50 | 173.3 | 4.0 | 5% | 20% | |||
Packing Team 4 | $ 11.50 | $ 17.25 | 173.3 | 4.0 | 5% | 20% | |||
Packing Team 5 | $ 12.50 | $ 18.75 | 173.3 | 4.0 | 5% | 20% | |||
Packing Team 6 | $ 12.50 | $ 18.75 | 173.3 | 4.0 | 5% | 20% | |||
Packing Team 7 | $ 13.50 | $ 20.25 | 173.3 | 4.0 | 5% | 20% | |||
Packing Team 8 | $ 12.00 | $ 18.00 | 173.3 | 4.0 | 5% | 20% | |||
Packing Team 9 | $ 11.00 | $ 16.50 | 173.3 | 4.0 | 5% | 20% | |||
Packing Team 10 | $ 13.50 | $ 20.25 | 173.3 | 4.0 | 5% | 20% | |||
Packing Team 11 | $ 12.50 | $ 18.75 | 173.3 | 4.0 | 5% | 20% | |||
Packing Team 12 | $ 14.50 | $ 21.75 | 173.3 | 4.0 | 5% | 20% | |||
Packing Team 13 | $ 14.00 | $ 21.00 | 173.3 | 4.0 | 5% | 20% | |||
Packing Team 14 | $ 13.50 | $ 20.25 | 173.3 | 4.0 | 5% | 20% | |||
Packing Team 15 | $ 14.50 | $ 21.75 | 173.3 | 4.0 | 5% | 20% | |||
Packing Team 16 | $ 12.50 | $ 18.75 | 173.3 | 4.0 | 5% | 20% | |||
Packing Team 17 | $ 12.50 | $ 18.75 | 173.3 | 4.0 | 5% | 20% | |||
Packing Team 18 | $ 13.00 | $ 19.50 | 173.3 | 4.0 | 5% | 20% | |||
Packing Team 19 | $ 14.50 | $ 21.75 | 173.3 | 4.0 | 5% | 20% | |||
Packing Team 20 | $ 13.00 | $ 19.50 | 173.3 | 4.0 | 5% | 20% | |||
Packing Team 21 | $ 12.00 | $ 18.00 | 173.3 | 4.0 | 5% | 20% | |||
Packing Team 22 | $ 13.00 | $ 19.50 | 173.3 | 4.0 | 5% | 20% | |||
Packing Team 23 | $ 11.00 | $ 16.50 | 173.3 | 4.0 | 5% | 20% | |||
Packing Team 24 | $ 11.00 | $ 16.50 | 173.3 | 4.0 | 5% | 20% | |||
Packing Team Open | $ – 0 | 173.3 | 4.0 | 5% | 20% | ||||
Packing Team Open | $ – 0 | 173.3 | 4.0 | 5% | 20% | ||||
Packing Team Open | $ – 0 | 173.3 | 4.0 | 5% | 20% | ||||
Packing Team Open | $ – 0 | 173.3 | 4.0 | 5% | 20% | ||||
Packing Team Open | $ – 0 | 173.3 | 4.0 | 5% | 20% | ||||
Packing Team Open | $ – 0 | 173.3 | 4.0 | 5% | 20% | ||||
Packing Team Open | $ – 0 | 173.3 | 4.0 | 5% | 20% | ||||
Packing Team Open | $ – 0 | 173.3 | 4.0 | 5% | 20% | ||||
Packing Team Open | $ – 0 | 173.3 | 4.0 | 5% | 20% | ||||
Packing Team Open | $ – 0 | 173.3 | 4.0 | 5% | 20% | ||||
Receiving Team Lead | $ 3,333.33 | 10% | 20% | Annual raises for the administrative and lead staff have averaged 4% in each of the past 3 years | |||||
Stocking Team Lead | $ 3,683.33 | 10% | 20% | Benefits were 20% of wages in the prior year; HR has informed your group that this percent increases to 22% in the new year | |||||
Picking Team Lead | $ 3,166.67 | 10% | 20% | ||||||
Packing Team Lead 1 | $ 3,333.33 | 10% | 20% | ||||||
Packing Team Lead 2 | $ 3,000.00 | 10% | 20% | ||||||
Lead or Manager Open | 10% | 20% | |||||||
Administrative 1 | $ 3,000.00 | 10% | 20% | ||||||
Warehouse Assistant Mgr | $ 5,000.00 | 20% | 25% | Annual raises for the management team have averaged 5% in each of the past 3 years | |||||
Warehouse Manager | $ 6,666.67 | 20% | 25% | Benefits were 25% of wages in the prior year; HR has informed your group that this percent increases to 26% in the new year |
Performance Metrics
Receiving and Stocking | Department (Prior Year) | Company Warehouse 2 | Industry Best | Industry Average | Description | |
Receiving Cycle Time (Dock to Stock) in Hours | 3.0 | 3.2 | 1.9 | 12.6 | Time in hours from products being delivered at warehouse docks to stocking as available inventory in warehouse shelves for distribution | |
Receiving Productivity (Cases per Person per Hour) | 50.0 | 52.0 | Time in hours for receiving tasks (processing receipts in computer system, unloading deliveries, scanning/recording codes, and placing in holding areas) | |||
Stocking Productivity (Cases per Person per Hour) | 20.0 | 19.5 | Time in hours for stocking tasks (pickup from holding areas then transfer to, unbox, and stock on designated shelving areas based on item types and sizes) | |||
Receiving and Stocking Cost (Average Cost per Case) | $ 1.34 | Costs of employee labor and related benefits for receiving and stocking staff plus equipment costs related to processes (such as forklift leases) | ||||
Picking and Packing | Department (Prior Year) | Company Warehouse 2 | Industry Best | Industry Average | Description | |
Order Cycle Time (Order to Pick to Ship) in Hours | 9.2 | 8.0 | 3.8 | 15.0 | Time in hours from products being delivered at warehouse docks to stocking as available inventory in warehouse shelves for distribution | |
Picking Productivity (Orders per Person per Hour) | 17.0 | 16.0 | Time in hours for picking tasks (retrieving inventory for order from designated shelving area and transferring to packing holding areas) | |||
Packing Productivity (Orders per Person per Hour) | 15.0 | 16.0 | Time in hours for packing tasks (retrieve from pickup holding areas then pack in box, label and transfer to shipping vendor holding area plus process shipment details in computer system) | |||
Picking and Packing Cost (Average Cost per Order) | $ 1.74 | Costs of employee labor and related benefits for picking and packing staff plus equipment costs related to processes (such as forklift leases); does not include packaging supply costs such as boxes and tape or third party shipping charges which vary based on customer order size and destination | ||||
Order Picking Accuracy | 99.20% | 99.00% | 99.85% | 98.00% | # Accurate Orders / Total # of Orders = Order Picking Accuracy Inaccurate orders (shipped goods do not match customer order) result in customer returns and rework plus additional shipments | |
Rate of Customer Returns (Damaged Goods) | 0.22% | 0.70% | 0.20% | 0.95% | # of Orders Returned Due to Damage / Total # of Orders Sent = Rate of Return (Damaged Goods) | |
Shrinkage % of Inventory Value (Theft, Breakage/Damage, Other) | 2.00% | 1.00% | 0.50% | 1.50% | Value of Inventory Missing or Unsellable / Total Value of Inventory = Shrinkage Rate |
Efficiency Project Options
Option 1 – Purchase Pick-t- Ship Conveyor Lines | Description | Month 1 | Month 2 | Month 3 | Month 4 | Month 5 | Month 6 | Month 7 | Month 8 | Month 9 | Month 10 | Month 11 | Month 12 | Terminal Value | |||
Start-up delay | 1 month | Productivity savings (estimated) | $ 11,133 | $ 11,133 | $ 11,133 | $ 11,133 | $ 11,133 | $ 11,133 | $ 11,133 | $ 11,133 | $ 11,133 | $ 11,133 | $ 11,133 | ||||
Number of conveyor lines | 3 | Equipment purchase and installation | $ (120,000) | $ 98,000 | |||||||||||||
Purchase / install per line | $40,000 | Depreciation adjustment for equipment | $ (2,000) | $ (2,000) | $ (2,000) | $ (2,000) | $ (2,000) | $ (2,000) | $ (2,000) | $ (2,000) | $ (2,000) | $ (2,000) | $ (2,000) | $ (98,000) | |||
Deprecation life | 5 years | Income tax | $ – 0 | $ (1,827) | $ (1,827) | $ (1,827) | $ (1,827) | $ (1,827) | $ (1,827) | $ (1,827) | $ (1,827) | $ (1,827) | $ (1,827) | $ (1,827) | $ 19,600 | ||
Net cash flow excl depreciation | $ (120,000) | $ 9,306 | $ 9,306 | $ 9,306 | $ 9,306 | $ 9,306 | $ 9,306 | $ 9,306 | $ 9,306 | $ 9,306 | $ 9,306 | $ 9,306 | $ 117,600 | ||||
Net present value | $ 80,848 | ||||||||||||||||
Option 2 – Lease Pick-to-Ship Conveyor Lines | Description | Month 1 | Month 2 | Month 3 | Month 4 | Month 5 | Month 6 | Month 7 | Month 8 | Month 9 | Month 10 | Month 11 | Month 12 | Terminal Value | |||
Start-up delay | 1 month | Productivity savings (estimated) | $ 11,133 | $ 11,133 | $ 11,133 | $ 11,133 | $ 11,133 | $ 11,133 | $ 11,133 | $ 11,133 | $ 11,133 | $ 11,133 | $ 11,133 | ||||
Number of conveyor lines | 3 | Start-up installation costs | $ (90,000) | ||||||||||||||
Start-up installation | $ 90,000 | Monthly equipment rental | $ (1,500) | $ (1,500) | $ (1,500) | $ (1,500) | $ (1,500) | $ (1,500) | $ (1,500) | $ (1,500) | $ (1,500) | $ (1,500) | $ (1,500) | ||||
Monthly payment | $ 1,500 | Income tax | $ 18,000 | $ (1,927) | $ (1,927) | $ (1,927) | $ (1,927) | $ (1,927) | $ (1,927) | $ (1,927) | $ (1,927) | $ (1,927) | $ (1,927) | $ (1,927) | $ – 0 | ||
Net cash flow | $ (72,000) | $ 7,706 | $ 7,706 | $ 7,706 | $ 7,706 | $ 7,706 | $ 7,706 | $ 7,706 | $ 7,706 | $ 7,706 | $ 7,706 | $ 7,706 | $ – 0 | ||||
Net present value | $ 7,895 | ||||||||||||||||
Company Factors (All Options) | Project description: The pick-to-ship conveyor lines will move items picked by the picking team from the shelving area direct to the packing/shipping area. The lines will reduce the distance that the picking team has to travel — saving 30 seconds per pick. This potentially increases the picking productivity from 17.0 to 19.8 orders per hour. There is also a distance reduction for the packing team — saving 20 seconds per order. This potentially increases the packing productivity from 15.0 to 16.4 orders per hour. | ||||||||||||||||
Discount rate (monthly) | 1% | ||||||||||||||||
Income tax rate | 20% | ||||||||||||||||
Depreciation adjustments to income tax are calculated | Productivity savings estimates are based on prior year volumes; savings would likely be greater for new year volume increase | ||||||||||||||||
on a straight line basis for this high level analysis | Project implementation is optional. If project is implemented, the manager must decide whether to purchase or lease. | ||||||||||||||||
Objectives &a
Collepals.com Plagiarism Free Papers
Are you looking for custom essay writing service or even dissertation writing services? Just request for our write my paper service, and we'll match you with the best essay writer in your subject! With an exceptional team of professional academic experts in a wide range of subjects, we can guarantee you an unrivaled quality of custom-written papers.
Get ZERO PLAGIARISM, HUMAN WRITTEN ESSAYS
Why Hire Collepals.com writers to do your paper?
Quality- We are experienced and have access to ample research materials.
We write plagiarism Free Content
Confidential- We never share or sell your personal information to third parties.
Support-Chat with us today! We are always waiting to answer all your questions.
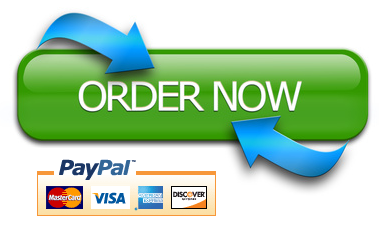