Costing Systems and Analysis Discuss the usage and creation of standard costs by an operation. How are these costs developed
Week 7 DiscussionCOLLAPSE
Costing Systems and Analysis
Option 1
Discuss the usage and creation of standard costs by an operation. How are these costs developed? How can they be used in the creation of a forecast? How can these be used in an individual or organizational measurement system?
– OR –
Option 2
Discuss a current business activity that you or your department does that could be improved by leveraging Variance Analysis. Discuss the perspective you could gain, and what a "favorable price" and a "favorable quantity" variance mean in this application.
Post your initial response by Wednesday, midnight of your time zone, and reply to at least 2 of your classmates' initial posts by Sunday, midnight of your time zone.
1st person to respond to
Chris
RE: Week 7 DiscussionCOLLAPSE
Professor and Class,
We have used variance analysis a few time in our antique car restoration business and it was really eye opening. Variance analysis is the process of identifying, measuring, and investigating the causes of significant differences (variances) between budgeted plans and actual results (1). We failed miserably with our property plant and equipment section of the balance sheet. We usually try and budget around $500 per month or $6,000 per year for new tools and equipment. Last year we spent $14,500 on new equipment which would not be a favorable variance. The main culprit of this was the owner of the company purchasing tools and equipment from sales people that come into the shop selling their latest, greatest product and falls for it hook-line and sinker!! A majority of the stuff purchased, they guys in the shop do not even use. I learned during this process that we do not need to purchase half of the stuff that we do. I would consider this wasteful spending!! In a year that we are purchasing the building and property that we have been renting, we need to really keep an eye on all expenses.
Chris
References:
1. Gene Siciliano. Finance for nonfinancial managers, second edition.
JWI 530
The Mary Story
WHAT’S MY REAL COST?
WHAT’S MY REAL COST? Mary worked on a custom-made perfume project with Mike, the VP of Operations. Not only did she learn some interesting things about how specialty orders are handled vs. standard products, she learned a lot about fixed and variable costs as they apply to the overall production process.
During her tour of the plant and subsequent meetings with Mike, the two talked quite a bit about SKU’s, and how they relate to accounting. SKU is short for “Stock Keeping Unit”, and they are typically given a numeric value. The numbers associated with unique SKUs provide a way of keeping track of items produced, and the costs associated with those items. Their warehouse was almost filled to capacity. Calculating required storage space was one of the many tasks Mary was determined to work out. Mary knew that there were expensive products such as fragrance ingredients, labels, and branded packaging in all those boxes. Inventory = Money!
After returning to her office from the plant tour, she reviewed a report Andrea had provided for her reference. After she reviewed the figures, she checked her email to find some follow-up notes from Andrea. She refilled her coffee, and set her mind to making an outline – and following through. Mary was on a quest to streamline costs where ever she could! With regards to the report, Mary assumed that all she needed to do in the fragrance division was to sort the list from the highest profit per oz. to lowest profit per oz.…and then start cutting the lowest profit producing SKUs. It sounded too easy…
Andrea’s notes reminded Mary that before she could get her cost slashing “axe” out, she first needed to understand the allocation methods that were used in calculating the total cost. Andrea wrote that Cost is not always cost… Some costs are direct costs, and are easily traceable to the individual unit. Items such as the perfume
formula or the cost of the bottle, even the label on that bottle are considered raw material costs – these are all examples of direct cost, as they are linked directly to a product.
But there are also indirect costs – the things that are necessary to create the product; but in an indirect way. One example of these costs would be the salary of the Plant Manager, as that cost impacts all of the units produced. Other examples would include items such as rent expense, equipment depreciation, and insurance. All of the indirect costs are pooled, and then ‘spread out’ or allocated over the products on the same basis. There are a host of different allocation methods available. The key is to choose the allocation method that most accurately reflects which units drive the cost, but to do so in a way that is not cost-prohibitive to administer.
The simplest allocation method is to spread the costs evenly over the units. If the indirect cost pool is $100 and there are 10 SKUs, each unit is assigned $10 of cost. But what if SKU A has 10x the unit volume of all of the rest? Another method is to spread the cost based on units of production. Again, if the cost pool is $100 and there are 2 SKUs, one with 90 units produced and the other 10 units, SKU A would absorb $90 and SKU B would be allocated $10. This method is typically a more accurate representation of the cost per SKU – if indeed production volume is the activity that mostly drives the cost.
Andrea reminded Mary that she also needed to consider what would happen if the cost pool was related to a “rework,” for instance, a salvage department for dealing with production and quality control issues. Suppose in this example, that all of the quality issues come from SKU B; SKU B would have to pay 100% of the salvage department’s cost!
There is a special type of Accounting called “Activity Based Costing”, or ABC. This approach makes very close observations related to internal processes, and identifies each individual pocket of indirect
spend, such as the salvage group. The goal is to identify the single best driver and use the measurement of that driver, like quality issues by SKU. Allocation is then based on the activity. One drawback with ABC is that it’s very expensive, and it requires lots of record keeping in order to run properly. This means extra work for accountants and for people in operations, who may have to track and report at incredible levels of detail. Its great data, but it often comes with a high cost. Mary learned that her company would implement activity-based approaches where practical. They focused on the largest elements of cost, and used ABC when a tracking or reporting system already existed.
For example, they would allocate storage costs based on the number of units of a SKU in the warehouse. This approach utilized data they already had from the warehouse operations report. But for the all other items, they would simply allocate based on the number of units of production. This approach produced the best results with the least expense. The “best results / least expense” philosophy really resonated with Mary.
But before she could make her final cuts, she needed to think about any unusual characteristics of the SKUs she was evaluating, such as complicated handling, small batch sizes, or unusual packaging that might not be reflected in the SKU P&L report. The SKU P&L report can be an incredible tool, but Mary knew that a savvy manager needs to understand its limitations. She also knew she had to ask follow-up questions and ensure that the answers made sense on every level. Financial data can get you 80% of the way to the final answer, but there is never a replacement for the judgment and experience of a great Business Manager.
As she finished reading through Andrea’s notes on these important topics, Mary felt a real sense of her duties and goals. She was getting “hands on” experience working directly with Mike in the plant, and Andrea was supplementing that knowledge by sharing key details
about the financial aspects of the manufacturing process. And both types of knowledge were helping Mary to realize what her “Real Costs” were.
Collepals.com Plagiarism Free Papers
Are you looking for custom essay writing service or even dissertation writing services? Just request for our write my paper service, and we'll match you with the best essay writer in your subject! With an exceptional team of professional academic experts in a wide range of subjects, we can guarantee you an unrivaled quality of custom-written papers.
Get ZERO PLAGIARISM, HUMAN WRITTEN ESSAYS
Why Hire Collepals.com writers to do your paper?
Quality- We are experienced and have access to ample research materials.
We write plagiarism Free Content
Confidential- We never share or sell your personal information to third parties.
Support-Chat with us today! We are always waiting to answer all your questions.
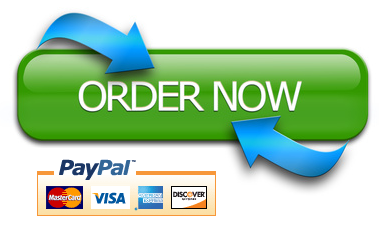