Referencing to the course materials and required sources is necessary read geography chapter content? watch chapter 3 lecture ?h
Discussion 2
700 words
Referencing to the course materials and required sources is necessary
read geography chapter content
watch chapter 3 lecture
http://forecast.uchicago.edu/lectures.html
Read the external link and attached dococument
complete the discussion below
As you learn about attributive factors to climate change, you will discover that cement factories are one of the major greenhouse gas emitters in our world. While cement factories contribute to job creation and stimulate local economies (and without say have contributed significantly to the creation of modern society), it is crutial that we understand the environmental impact that these factories have. After watching the video clip posted here and reading the article, please post your opinion about what you think is the strongest argument to support/not support the need for cement factories, and idea(s) for possible mitigation. Respond to at least two peer postings.
Resources: - 1) In Northeast India, Cement Plants Disrupt Forest and a Way of Life (external link)
https://e360.yale.edu/features/in-northeast-india-cement-plants-disrupt-forest-and-a-way-of-life
– 2) Health Risk and Environmental Assessment of Cement Production in Nigeria (attached pdf)
atmosphere
Review
Health Risk and Environmental Assessment of Cement Production in Nigeria
Mmemek-Abasi Etim 1,* , Kunle Babaremu 2, Justin Lazarus 1 and David Omole 1
���������� �������
Citation: Etim, M.-A.; Babaremu, K.;
Lazarus, J.; Omole, D. Health Risk
and Environmental Assessment of
Cement Production in Nigeria.
Atmosphere 2021, 12, 1111.
https://doi.org/10.3390/
atmos12091111
Academic Editor: Deborah Traversi
Received: 19 July 2021
Accepted: 11 August 2021
Published: 30 August 2021
Publisher’s Note: MDPI stays neutral
with regard to jurisdictional claims in
published maps and institutional affil-
iations.
Copyright: © 2021 by the authors.
Licensee MDPI, Basel, Switzerland.
This article is an open access article
distributed under the terms and
conditions of the Creative Commons
Attribution (CC BY) license (https://
creativecommons.org/licenses/by/
4.0/).
1 Department of Civil Engineering, College of Engineering, Covenant University, Ota 112233, Nigeria; [email protected] (J.L.); [email protected] (D.O.)
2 Directorate of Pan African University for Life and Earth Science Institute, University of Ibadan, Ibadan 200284, Nigeria; [email protected]
* Correspondence: [email protected]
Abstract: The cement manufacturing industry has played a fundamental role in global economic development, but its production is a major facilitator to anthropogenic CO2 release and solid waste generation. Nigeria has the largest cement industry in West Africa, with an aggregate capacity of 58.9 million metric tonnes (MMT) per year. The Ministry for Mines and Steel Development asserts that the nation possesses total limestone deposits of around 2.3 trillion MT with 568 MMT standing as established reserves and 11 MMT used. Cement industries are largely responsible for releasing air pollutants and effluents into water bodies with apparent water quality deterioration over the years. Air pollution from lime and cement-producing plants is seen as a severe instigator of occupational health hazards and work-related life threats, negatively affecting crop yields, buildings, and persons residing in the vicinity of these industries. World Bank observed in 2015 that 94% of the Nigerian populace is susceptible to air pollutants that surpass WHO guidelines. In 2017, World Bank further reported that 49,100 premature deaths emanated from atmospheric PM2.5, with children beneath age 5 having the greatest vulnerability owing to lower respiratory infections, thereby representing approximately 60% of overall PM2.5-induced deaths. Cement manufacturing involves the significant production of SO2, NOx, and CO connected to adverse health effects on humans. Sensitive populations such as infants, the aged, and persons having underlying respiratory ailments like asthmatics, emphysema, or bronchitis are seen to be most affected. Consequently, in addressing this challenge, growing interests in enacting carbon capture, usage, and storage in the cement industry is expected to alleviate the negative environmental impact of cement production. Still, no carbon capture technology is yet to achieve commercialization in the cement industry. Nonetheless, huge advancement has been made in recent years with the advent of vital research in sorption-enhanced water gas shift, underground gasification combined cycle, ammonium hydroxide solution, and the microbial-induced synthesis of calcite for CO2 capture and storage, all considered sustainable and feasible in cement production.
Keywords: cement production; particulate matter (PM2.5 & PM10); carbon capture; public health; air pollution; water pollution
1. Introduction
Cement is the most common and extensively used adhesive in the construction in- dustry. It is employed on highways, houses, embankments, bridges, commercial estab- lishments, and flyovers. Hence, the cement manufacturing industry has played a funda- mental role in global economic development, with construction, steel, crude oil, iron, and telecommunications, constituting major infrastructural aspects worldwide. Swift commer- cialization, urban civilization, and the necessity to boost domestic goods production have been the lead cause for the surge in cement production [1]. In Nigeria, the availability of raw materials has encouraged numerous local productions. As of 2013, annual cement
Atmosphere 2021, 12, 1111. https://doi.org/10.3390/atmos12091111 https://www.mdpi.com/journal/atmosphere
Atmosphere 2021, 12, 1111 2 of 16
production increased significantly above 1300%, from below 2 million tonnes in 1990 to above 28 million tonnes in 2013 [2]. Cement is a powder-like material comprising lime and mud-clay as fundamental elements, utilized in all kinds of building and civil constructions. The used clay provides silica, iron oxide, and alumina, while the calcined lime principally gives calcium-oxide. As highlighted in Table 1, raw materials used for cement produc- tion are obtained by blasting rock quarries with explosives [3,4]. The blasted rocks are transported to the plants, where they are crushed into chunks of 12 inch-sized particles. Through the process of prehomogenization, cement is produced depending on the needed proportion of ground clay and limestones. For a pressurized rotatory furnace of around 1400 ◦C, these unprocessed resources (Table 1) are calcined to become a clinker [3,5]. The clinker is then pulverized with some minerals to a powder to produce Portland cement [4].
Table 1. Raw materials used for clinker production.
Calcium, Ca Limestone involving quick-lime from treating wastewater, caustic-lime
Silicon, Si Sand such as harnessed mould (silica sand-clay-liquid mixture)
Silicon–Aluminium, Si–Al Kaolinite, bentonite, and similar forms of terra-cotta clay
Iron, Fe Iron-based metals, including heated pyrite and adulterated metallic minerals
Silicon–Aluminium–Calcium, Si–Al–Ca Powdered blast furnace slag such as ashes from fuel combustion ashes, oil-soluble
Aluminium, Al Raw metallic apparatus constituting recycling salt slag, aluminium hydroxide
Sulphur, S Non-artificial gypsum such as Natural anhydrite Gypsum from flue gas desulfurization
Global cement generation was 4.1Bnt in 2020 with a growth rate of 24% from its highest in 2010 [6], with China clearly leading as the world’s largest cement producer, representing 59.31% of overall manufactured cement globally. Table 2 shows the global cement production, with China producing more than 12 of the world’s cement combined. These recent expansions have been driven by developing countries such as India and China, with a substantial increase in cement manufacturing around Asia, Africa, and South America. As the earth’s population and industrialization boom, universal cement production is bound to surge by at least 12–23% by 2050 [7]. Nigeria possesses the largest cement industry within West Africa, with at least 12 registered companies amounting to a merged cement capacity of 58.9 Mt/yr. Dangote Cement is the largest cement producer in Nigeria and West Africa, manufacturing a combined share of more than 28.5 Mt/yr of cement capacity. Also, LafargeHolcim (through its subsidiary AshakaCem & Lafarge WAPCO) and BUA Group boost 18.9 Mt/yr and 11.5 Mt/yr of integrated cement capacity, respectively [8]. With the increasing presence of cement manufacturing, the industry poses as one of the most significant CO2 emitters. Evaluating the risk factors of its spillover impact on public health is inevitable.
In Nigeria, limestone and marble are the main minerals of cement production. The conversion of this limestone into cement by heat releases carbon dioxide as a waste product. Ndefo [9] highlighted the deposits of these minerals and their carbon contents in various percentages, as shown in Figure 1. They are mainly composed of the carbonates of calcium and magnesium. Large deposits of calcium carbonate (CaCO3) are observed in Calabar, Yandev, and Ukpilla, with Ewekoro having the largest deposit of Magnesium carbonate MgCO. The Nigerian Ministry of Mines and Steel Development reports a total limestone collection of approximately 2.3 TMT, of which 568 MMT stands as proven reserve and
Atmosphere 2021, 12, 1111 3 of 16
11 MMT is used. Such deposits are endowed unadulterated, mainly across Ebonyi, Cross- River, and Benue cities with large industrial volumes among Gombe, Edo, Sokoto, and Ogun. Nonetheless, the largest enriched West African nation is Nigeria.
Table 2. Global cement production in selected countries (in metric tonnes) [6].
Countries 2018 2019
United States 87,000 89,000 Brazil 53,000 55,000 China 2,200,000 2,200,000 Egypt 81,200 76,000 India 300,000 320,000 Indonesia 75,200 74,000 Iran 58,000 60,000 Japan 55,300 54,000 Korea, Republic of 57,500 55,000 Russia 53,700 57,000 Turkey 72,500 51,000 Vietnam 90,200 95,000 Other Countries 870,000 900,000
Atmosphere 2021, 12, x FOR PEER REVIEW 3 of 16
serve and 11 MMT is used. Such deposits are endowed unadulterated, mainly across Eb- onyi, Cross-River, and Benue cities with large industrial volumes among Gombe, Edo, Sokoto, and Ogun. Nonetheless, the largest enriched West African nation is Nigeria.
Figure 1. Percentage quantity of calcium carbonate and magnesium carbonate in Nigerian Lime- stone Deposit [9,10].
In 2018, data from World Health Organization (WHO) indicated that 9 in 10 persons breathe air containing excessive concentrations of toxins beyond the approved threshold stated by WHO. Africa and Asia amass the worst hit with 90% deaths from environmental air contaminants [11]. During cement production, soot molecules and dusty residues emerge extensively, thereby triggering respiratory ailments across humans. Diverse pul- monic-connected diseases are prevalent mostly to indigenous persons living around ce- ment industries. One cement factory releases massive atmospheric pollution. Given the voluminous process of producing cement, any certain potential environmental impact would be significant. As such, key players must prioritize atmospheric safety and decon- tamination since this undeniably plays an important role in achieving sustainable devel- opment (SDGs) goals 3, 6, 7, 11, 12 and 13.
Higher cement production and usage, switching fuel types, and dirt restriction mech- anization influence the quantity and cluster of environmental impurities. Numerous in- vestigations admit that manufacturing cement constitutes the broadest source for PM emission, accounting for 20–30%, which is 40% of the gross industrial emission [12]. Fur- thermore, making cement represents 5–6% of total artificial CO2 discharge, which accord- ing to the European Cement Association (ECA), yields at least half a ton of CO2 for a ton of cement produced. The most common pollutants responsible for air pollution are vola- tile organic compounds (VOCs), carbon monoxide (CO), particulate matter (PM), sulfur dioxide (SO2), nitrogen oxides (NOx), and hydrocarbons [13]. Decarbonation propels off about 50% of the emission, while fuel for kiln firing induces approximately 40% of pollu- tants. With projected manufacturing spike, cement makers are under pressure to lower or sustain CO2 outflows. Carbon-neutral biomass amidst other substitute fuels is seeing heightened usage in reducing certain cement-based CO2 discharge. Cement manufactur- ing entails severe health constraints; nearly every production phase adversely affects man and its environment. When dismantling rocks, particulate matter is dispersed into the at- mosphere, making it harmful to man. Moreover, this disintegration process causes noise pollution. The urban geography might likewise impact the gadgets adopted during this procedure [12,13]. Diverse equipment is recently employed to mitigate these adverse shortcomings. The equipment helps to limit dusty release, particularly across cement in- dustries. Gas trappers similarly capture extreme toxins, including sulphur, nitrogen ox- ide, and carbon dioxide, among others [11,13]. An essential constituent of gas for cement
0 20 40 60 80 100 120
Calabar
Kwara
Yandev
Nkalagu
Sokoto
Igumale
Makurdi
Ewekoro
Total Calcium Carbonate (CaCO3) (%) Total Magnesium Carbonate (MgCO) (%)
Figure 1. Percentage quantity of calcium carbonate and magnesium carbonate in Nigerian Limestone Deposit [9,10].
In 2018, data from World Health Organization (WHO) indicated that 9 in 10 persons breathe air containing excessive concentrations of toxins beyond the approved thresh- old stated by WHO. Africa and Asia amass the worst hit with 90% deaths from envi- ronmental air contaminants [11]. During cement production, soot molecules and dusty residues emerge extensively, thereby triggering respiratory ailments across humans. Di- verse pulmonic-connected diseases are prevalent mostly to indigenous persons living around cement industries. One cement factory releases massive atmospheric pollution. Given the voluminous process of producing cement, any certain potential environmental impact would be significant. As such, key players must prioritize atmospheric safety and decontamination since this undeniably plays an important role in achieving sustainable development (SDGs) goals 3, 6, 7, 11, 12 and 13.
Higher cement production and usage, switching fuel types, and dirt restriction mech- anization influence the quantity and cluster of environmental impurities. Numerous investigations admit that manufacturing cement constitutes the broadest source for PM emission, accounting for 20–30%, which is 40% of the gross industrial emission [12]. Fur- thermore, making cement represents 5–6% of total artificial CO2 discharge, which according
Atmosphere 2021, 12, 1111 4 of 16
to the European Cement Association (ECA), yields at least half a ton of CO2 for a ton of cement produced. The most common pollutants responsible for air pollution are volatile organic compounds (VOCs), carbon monoxide (CO), particulate matter (PM), sulfur diox- ide (SO2), nitrogen oxides (NOx), and hydrocarbons [13]. Decarbonation propels off about 50% of the emission, while fuel for kiln firing induces approximately 40% of pollutants. With projected manufacturing spike, cement makers are under pressure to lower or sustain CO2 outflows. Carbon-neutral biomass amidst other substitute fuels is seeing heightened usage in reducing certain cement-based CO2 discharge. Cement manufacturing entails severe health constraints; nearly every production phase adversely affects man and its environment. When dismantling rocks, particulate matter is dispersed into the atmosphere, making it harmful to man. Moreover, this disintegration process causes noise pollution. The urban geography might likewise impact the gadgets adopted during this procedure [12,13]. Diverse equipment is recently employed to mitigate these adverse shortcomings. The equipment helps to limit dusty release, particularly across cement industries. Gas trappers similarly capture extreme toxins, including sulphur, nitrogen oxide, and carbon dioxide, among others [11,13]. An essential constituent of gas for cement production is carbon dioxide (CO2). Heating calcium carbonate as the main ingredient produces lime, whereas carbon dioxide is given off as a chemical procedure. Cement production contributes 40% of global CO2 discharge; 60% of this CO2 volume comes from Portland cement [14,15], transforming limestone to lime. Sometimes, weighty metallic minerals spanning across mercury, chromium, thallium, and zinc have proximity to cement factories.
2. The Growing Nigerian Cement Industry
In recent years, the Nigerian cement industry has grown from import-dependency to an export-thriving epicentre within Africa. Cement is still a critical part of developing infrastructures globally as Nigerian cement producers continuously ramp up activities and expand into futuristic times. Given growing demands on infrastructural development, the National Integrated Infrastructure Master Plan (NIIMP) has projected a cumulative investment of approximately $3 trillion for a duration of 3 decades to construct and sustain infrastructures. The Ministry for Mines and Steel Development [16] estimates Nigeria’s highway system to be at 193,200 km, whereby 28,980 km is paved and about 85% is un- paved. This fact highlights the tremendous pressure on cement manufacturers in meeting the country’s demand for infrastructural development. Environmental health risks are of significant concern with the absence of a greener and more sustainable cement production in Nigeria. Juxtaposing the high degree of deficiency across the residential and structural facilities, particularly regarding the dire need for building properties and roadways, the capacity for expansion in this sector is evidently captivating. Additionally, the currently established amplitude has broadened to exceed projected demand as governmental strate- gies, including tax-relief schemes, banning imported cement, and similar enacted plans, have facilitated the rapid enlargement of capabilities for proprietary stakeholders [17]. In the medium term, Nigeria’s concrete industry indicates a likelihood for considerably sustained growth into the next generation, supported by unimpaired cement demand essentials as revealed by multiple measurable benchmarks. Projections place Nigerian cement consumption per capita at about 150 kg falling behind the worldwide average of 561 kg. Over the long term, several factors encompassing enhanced accessibility to construc- tion funds, increased civilization, larger populace, heightened infrastructural and housing investment, political consistency, and economic affluence determine the possibilities for boosting cement demand in Africa’s biggest country.
Besides other trivial functions of concrete for building, fascinations exist of using cement in constructing roads due to its resilience and easy preservation. More so, with the current population surge within Nigeria, it is believed that the government and increasing private sector will invest more in furnishing houses for bustling youths and working-class people, particularly inside and at the borders of urban cities. Consequently, to foster this movement, the federal government recently founded the Presidential Infrastructure De-
Atmosphere 2021, 12, 1111 5 of 16
velopment Fund (PFID) in 2018, overseen by the Nigeria Sovereign Investment Authority (NSIA), whose goal is to narrow down the investment to electricity and road schemes nationwide. Hence, cement demand growth in Nigeria is expected to increase local ce- ment production over the following years. Nigeria’s cement sector exhibits oligopolistic tendencies with three major competitors as presented in Figure 2. Dangote Cement Plc, the indisputable biggest producer in Sub-Sahara and Nigeria with an installed capacity of 48.6 Mta and 32.3 Mta respectively, just recently added 3 million tonnes to its capacity in 2020 in the Obajana Cement Plant. Lafarge Africa Plc has a capacity of 10.5 million metric tonnes, accounting for a market share of 21.8%. BUA Group (recently sealed a merger of CCNN and Obu) has an 8.0 million metric tonnes capacity, accounting for a market share of 17.6%. Regardless of the current capabilities, the key manufacturing industrial giants are relentless in diversification strategies. According to their media sources, Dangote Cement has hinted at developing two extra 6MTPA factories in Edo city’s Okpella and Ogun state’s Itori. Additionally, BUA Group (CCNN) intends to extend its Sokoto’s Kalambaina Plant by supplementary 3MMTA. These plants are generally sited close to the raw material to cut the cost of transporting them. With limestone in its abundance, cement production in Nigeria is at its infant stage. Dangote cement further observes that Obajana’s accumulated limestone of 647 MT should stretch for approximately 45 years, Ibese’s 1150 MT should cover 78 years, and Gboko’s 133 MT should surpass three decades.
Atmosphere 2021, 12, x FOR PEER REVIEW 5 of 16
private sector will invest more in furnishing houses for bustling youths and working-class people, particularly inside and at the borders of urban cities. Consequently, to foster this movement, the federal government recently founded the Presidential Infrastructure De- velopment Fund (PFID) in 2018, overseen by the Nigeria Sovereign Investment Authority (NSIA), whose goal is to narrow down the investment to electricity and road schemes nationwide. Hence, cement demand growth in Nigeria is expected to increase local ce- ment production over the following years. Nigeria’s cement sector exhibits oligopolistic tendencies with three major competitors as presented in Figure 2. Dangote Cement Plc, the indisputable biggest producer in Sub-Sahara and Nigeria with an installed capacity of 48.6 Mta and 32.3 Mta respectively, just recently added 3 million tonnes to its capacity in 2020 in the Obajana Cement Plant. Lafarge Africa Plc has a capacity of 10.5 million metric tonnes, accounting for a market share of 21.8%. BUA Group (recently sealed a merger of CCNN and Obu) has an 8.0 million metric tonnes capacity, accounting for a market share of 17.6%. Regardless of the current capabilities, the key manufacturing industrial giants are relentless in diversification strategies. According to their media sources, Dangote Ce- ment has hinted at developing two extra 6MTPA factories in Edo city’s Okpella and Ogun state’s Itori. Additionally, BUA Group (CCNN) intends to extend its Sokoto’s Kalambaina Plant by supplementary 3MMTA. These plants are generally sited close to the raw mate- rial to cut the cost of transporting them. With limestone in its abundance, cement produc- tion in Nigeria is at its infant stage. Dangote cement further observes that Obajana’s accu- mulated limestone of 647 MT should stretch for approximately 45 years, Ibese’s 1150 MT should cover 78 years, and Gboko’s 133 MT should surpass three decades.
Figure 2. Major Cement Plants in Nigeria.
Over time, Nigerian cement manufacturers have used domestic cinder and proxy combustibles such as LPFO (Low Pour Fuel Oil—a byproduct of petroleum oil) as an al- ternative to gas in powering their plants. Dangote Cement, for instance, has tactically re- inforced its limekilns to function better with coals. This encompasses Ibese and Obajana industries, which were formerly structured to operate on gas, whereas Benue’s factory previously used LPFO. Dangote group also indicated tendencies to utilize its numerous
Figure 2. Major Cement Plants in Nigeria.
Over time, Nigerian cement manufacturers have used domestic cinder and proxy combustibles such as LPFO (Low Pour Fuel Oil—a byproduct of petroleum oil) as an alternative to gas in powering their plants. Dangote Cement, for instance, has tactically reinforced its limekilns to function better with coals. This encompasses Ibese and Obajana industries, which were formerly structured to operate on gas, whereas Benue’s factory previously used LPFO. Dangote group also indicated tendencies to utilize its numerous damaged tyres as energy sources. Similarly, Lafarge Africa Plc has heightened its usage of substitute power, including coal and industrial waste.
Atmosphere 2021, 12, 1111 6 of 16
3. Cement Production on Climate Change and Global Warming
As highlighted by USGS, global warming is one of many characteristics of climate change. Global warming is the rise in global temperatures largely due to escalating concentrations of atmospheric greenhouse gases. Similarly, climate change involves the gradual alteration of climatic actions for an extended period [18]. Increased urbanization and industrialization have led to higher cement production in Nigeria as cement plants have substantially ramped up their output, triggering greater CO2 emissions into the air. Ndefo [9] highlighted that using the ratio of one cement to carbon dioxide tonne, Nigeria would manufacture beyond 25 MMT of cement, thereby inducing 25 MMT of CO2 yearly. This has eventually drawn the country into global warming and weather crisis. Developing nations like Nigeria lack sufficient preparation for global warming consequences, which is already evident and glaring for its citizens. Notwithstanding that Africa’s largest country has fortunately not encountered severe atmospheric-spurred dis- aster, occurrences are constantly seen in tremendous heat waves around major industrial cities; increased greenhouse gases and particulate matter; PMs from cement dust pollution; and high precipitations leading to flooding and gully erosion [14] in Lagos, Jigawa, Edo, and Anambra States. The atmospheric CO2 before industrialization was about 200 ppm, but it is presently estimated to surpass 800 ppm as the 21st century reaches its end, causing great concerns. The cement sector is a principal contributor to weather disruptions be- cause its manufacturing operations emit enormous CO2, which is primarily unrecoverable and reusable [19,20]. Wilson & Law (2007) [21] further describe cement production as a greenhouse double whammy, by which the conversion of limestone to cement produces carbon dioxide; the fossil fuel used in heating it also produces carbon dioxide. In 2019, Netherlands Environmental Assessment Agency reported the increase in earthly CO2 discharge by a projected 350 MtCO2 or 0.9% to reach 38 GtCO2, such that China incurs the highest contribution with an increased 3.4% (or 380 MtCO2) and Nigeria’s emission at approximately 100 MtCO2 [22]. Table 3 highlights the atmospheric emissions from 1970 to 2019 in Nigeria. Cement manufacturing is estimated to supply 5–10% of worldwide anthropogenic CO2 outflow [23]. However, about 40% of CO2 emissions from dry cement manufacturing come from the combustion of fossil fuels [24] in the kiln process, while 50% comes from the roasting of limestone. The roasting (calcination) process liberates CO2 from limestone to give quick-lime: an essential resource in making cement clinkers. The process is energy-intensive and with extreme temperatures of about 1450 ◦C [25].
Table 3. Atmospheric emissions from 1970 to 2019 in Nigeria.
Years Carbon Dioxide (CO2)
Emission Methane (CH4)
Emission Nitrous Oxide, (N2O)
Emission Greenhouse Gases (F-Gases):
(HFCs, PFCs and SF6) Emission
1970 0.03 130 12 –
1971 0.04 190 12 –
1972 0.06 230 12 –
1973 0.07 280 13 –
1974 0.08 350 14 –
1975 0.06 260 14 –
1976 0.08 290 14 –
1977 0.07 250 15 –
1978 0.07 240 15 –
1979 0.10 370 16 –
1980 0.09 310 16 –
Atmosphere 2021, 12, 1111 7 of 16
Table 3. Cont.
Years Carbon Dioxide (CO2)
Emission Methane (CH4)
Emission Nitrous Oxide, (N2O)
Emission Greenhouse Gases (F-Gases):
(HFCs, PFCs and SF6) Emission
1981 0.07 230 16 0.1
1982 0.07 200 17 0.1
1983 0.07 200 17 0.1
1984 0.07 210 17 0.1
1985 0.07 220 18 0.1
1986 0.07 220 18 0.1
1987 0.07 200 18 0.1
1988 0.08 230 19 0.2
1989 0.08 240 19 0.2
1990 0.07 240 19 0.2
1991 0.08 250 20 0.2
1992 0.09 250 20 0.1
1993 0.09 260 21 0.1
1994 0.08 250 21 0.1
1995 0.09 260 22 –
1996 0.10 280 22 0.1
1997 0.10 250 23 0.1
1998 0.09 210 24 0.2
1999 0.09 190 24 0.2
2000 0.10 190 25 0.3
2001 0.11 200 25 0.3
2002 0.10 170 26 0.4
2003 0.11 190 26 0.5
2004 0.10 190 26 0.6
2005 0.10 190 29 0.7
2006 0.09 180 28 0.8
2007 0.08 180 28 0.8
2008 0.09 170 29 0.9
2009 0.08 170 29 1.0
2010 0.09 180 30 1.1
2011 0.10 180 32 1.2
2012 0.09 190 32 1.3
2013 0.09 180 32 1.3
2014 0.09 180 32 1.4
2015 0.09 180 34 1.5
2016 0.09 180 35 1.6
2017 0.09 180 36 1.7
2018 0.10 180 37 1.7
2019 0.10 180 38 1.8
Unit = 109 kg CO2 eq (1 million metric tonnes). CO2 equivalent is calculated with Global Warming Potentials (GWP-100) of the Fourth IPCC Assessment report (2017). Graphical illustration in Supplementary Data.
Atmosphere 2021, 12, 1111 8 of 16
Globally, increasing industrialization has led to a rise in carbon dioxide levels in the atmosphere to about 0.03% (570 ppm) [26]. To maintain the CO2 concentration below 550 ppm by 2050, Cement Technology Roadmap has recommended cutting CO2 emissions to 30–60%, thereby mitigating global warming [27]. Cement plants are a major source of CO2 emissions due to the high CO2 concentration in cement kiln flue gas [26]. However, with the advent of carbon capture and storage (CCS), cement manufacturers have discov- ered a system of reducing the role of fossil fuel emissions in global warming by capturing and storing CO2 directly from the atmosphere [28]. Together with the underground gasifi- cation combined cycle (UGCC), CCS is a viable method for exploiting clean limestone and coal [29]. Techniques of pre-combustion capture, post-combustion capture, and oxy-fuel combustion are widely used for carbon dioxide capturing in the cement industry [30].
The manufacturing sector and agricultural sector have contributed significantly to the Nigerian Gros
Collepals.com Plagiarism Free Papers
Are you looking for custom essay writing service or even dissertation writing services? Just request for our write my paper service, and we'll match you with the best essay writer in your subject! With an exceptional team of professional academic experts in a wide range of subjects, we can guarantee you an unrivaled quality of custom-written papers.
Get ZERO PLAGIARISM, HUMAN WRITTEN ESSAYS
Why Hire Collepals.com writers to do your paper?
Quality- We are experienced and have access to ample research materials.
We write plagiarism Free Content
Confidential- We never share or sell your personal information to third parties.
Support-Chat with us today! We are always waiting to answer all your questions.
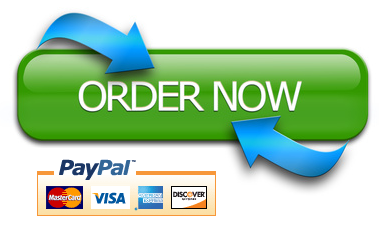