Illustrate a basic process flow diagram for Harvest. ? How does Harvest generate revenue? What are Harvests costs? ?Include th
- Illustrate a basic process flow diagram for Harvest.
- How does Harvest generate revenue? What are Harvest’s costs? Include those costs and revenue sources on the process flow diagram.
- What is the key profitability driver for Harvest, i.e., what drives greater profits?
- How many tons of waste does the plant need to process per year in order to break even? What would be the potential profit (or loss) if the plant operates at capacity? (Hint, find the marginal revenue/costs per ton, and the fixed costs per year to find the break-even quantity. Use the provided assumptions and formulas to capture variable costs/variable revenue/fixed costs to support your decision.)
- Compare/contrast the pre-processing and source separation options. What are the pros and cons of each?
- How does preprocessing or source separation change the process flow? Illustrate two new process flow diagrams for the pre-processing and source separation options and include on the diagrams for each option the new costs and revenue sources (if any).
- How many tons of waste does each option need to process per year in order to break even? (Same process as above.)
- Which option would you recommend and why?
Definitions of and hints for avoiding plagiarism can be found at https://wp.odu.edu/plagiarism/.
Assumptions/additional information
- Benefits cost an additional 40% of an employee's salary.
- Assume straight line depreciation for equipment, i.e., total cost divided by expected years of use.
For those who might not remember capacity planning/cost-volume analyses, refer to the following formulas to help.
TC = total cost
FC = total fixed costs
VC = total variable costs
v = variable cost per unit
Q = quantity or volume of output
TR = total revenue
R = revenue per unit
QBEP = break-even point (quantity)
P = Profit
Total costs = total fixed costs + total variable costs
TC = FC + VC
Total variable costs = quantity*variable cost per unit
VC = Q*v
Total revenue = revenue per unit*quantity
TR = R*Q
Profit can be derived from any of the following:
Total revenue – total costs = P = TR – TC
Revenue per unit – (fixed costs + variable cost per unit *quantity) = P = R*Q – (FC + v*Q)
Quantity*(revenue per unit – variable cost per unit) – total fixed costs = P = Q(R – v) – FC
Break even quantity = fixed costs/(revenue per unit – variable cost per unit)
9 – 6 1 1 – 0 3 4
R E V : A U G U S T 1 , 2 0 1 2
________________________________________________________________________________________________________________
Professors Deishin Lee (HBS) and Baris Ata (Northwestern University) and Doctoral Candidate Mustafa H. Tongarlak (Northwestern University) prepared this case. HBS cases are developed solely as the basis for class discussion. Cases are not intended to serve as endorsements, sources of primary data, or illustrations of effective or ineffective management. Copyright © 2010, 2012 President and Fellows of Harvard College. To order copies or request permission to reproduce materials, call 1-800-545- 7685, write Harvard Business School Publishing, Boston, MA 02163, or go to www.hbsp.harvard.edu/educators. This publication may not be digitized, photocopied, or otherwise reproduced, posted, or transmitted, without the permission of Harvard Business School.
D E I S H I N L E E
B A R I S A T A
M U S T A F A H . T O N G A R L A K
Harvest: Organic Waste Recycling with Energy Recovery (B)
The management team at Harvest decided to go forward with the organic waste recycling facility in one of the large U.S. West Coast cities. Although the municipal curbside composting program seemed promising, the company decided to target commercial and industrial facilities with high organic content in their waste streams (e.g., grocery stores) as the company’s main waste-generating customers. The company thought that working with a few large customers would make it easier to anticipate the quantity of incoming organic waste.
After committing to developing the plant, the company quickly focused on its operational strategy. A key factor that influenced the company’s operational strategy was the quality of incoming waste. Although its anaerobic digestion technology was robust to non-organic contamination, if the percentage of contaminants was too high, the quality of the compost would be too low to sell. Therefore, even though its input material was waste, as with any manufacturer, Harvest had to ensure that its raw material was of sufficiently high quality. The company considered two possible options: It could build a capital- and labor-intensive pre-processing facility to sort incoming waste (i.e., comingled organic and inorganic waste), or it could work with waste generators to source separate their waste (accepting only organic waste), which would allow Harvest to directly feed incoming waste into its anaerobic digester. Noting that the success of this project would be an example and possibly a template for how other organic-waste recycling operations could be developed, the company wanted to maximize its chances of success.
Pre-Processing
The pre-processing facility would sort the incoming waste, removing most of the contaminants before the waste was fed into the digestion process. This allowed Harvest to accept waste of varying levels of quality. Harvest would essentially contract with the waste generators to act as their waste disposal service (substituting for landfill or incineration) and would sort the useful organic waste in the waste stream from the inorganic contaminants. Harvest anticipated that the pre-processing plant would yield approximately 75% “clean” waste from the incoming waste stream (although 1%–2% contaminants would remain). Of the contaminants that were sorted out of the incoming waste stream, 40% were recyclables such as metal and plastic, 40% was unrecyclable trash, and 20% was
611-034 Harvest: Organic Waste Recycling with Energy Recovery (B)
2
recyclable organics. Although the recyclables were mixed with the trash and therefore degraded, the company could still sell the recyclables, but would have to dump the rest in a landfill. The net revenue from the contaminated waste stream was approximately $40 per ton (recyclable revenue minus landfill cost).
The capital cost for the pre-processing facility was $4 million. A significant part of this cost was for equipment to sort the incoming waste. This equipment included air separators to pull out light plastic, “star decks” to separate large pieces from small, and magnets to extract metals. Also, an additional eight workers were required to staff the picking line. Harvest would contract with a labor- supply firm and anticipated paying $15 per hour for workers to run the pre-processing machinery and hand-sort the incoming waste. Additionally, a full-time technician would be required to maintain the pre-processing machinery. This machinery typically lasted eight years. Because Harvest would accept all the waste from the waste generator, it believed it could charge a tipping fee that was very close to the landfill tipping fee, approximately $80 per ton. The compost generated from this pre- processed waste input would probably contain some level of contamination, which would degrade the quality (the primary concern was glass particles). Thus, Harvest could not sell the compost, but could dispose of it for a reduced tipping fee at the landfill. The cost of this additional disposal would be $10 per ton. The equipment-intensive pre-processing facility would increase the plant’s annual maintenance and utility cost by $400,000.
Source Separation
The other option Harvest considered was to educate and work with waste generators to source separate their waste. This involved working with each supplier to develop a process for keeping their organic waste separate from inorganic waste. Depending on the internal processes of the supplier, source separation might be as simple as having two dumpsters on the loading dock, one for each type of waste. For example, the waste stream from a restaurant could easily be sorted into organic (leftover food) and inorganic (containers such as cans and jars) in the kitchen. In more complicated settings, dual waste receptacles throughout the supplier’s plant might be necessary. An example was a sports stadium where hundreds of waste receptacles would have to be duplicated for organic and inorganic waste. This duplication would also complicate collection throughout the stadium. To ensure the ongoing quality of incoming waste, Harvest anticipated having to dedicate a client management employee to audit its clients periodically and work with them on process improvements. Harvest planned to target clients with naturally high percentage of organics in their waste stream, i.e., 70%– 75% organic waste.
Because source separation pre-empted the comingling of organic and inorganic waste, if done well, close to 100% of the organic waste would be available for recycling. However, the quality of the incoming waste stream would be determined by the supplier’s process. Although the anaerobic digestion process was robust to inorganic contamination, a screening process after the digestion process was required to filter out contaminants from the compost. However, the post-processing would be less labor intensive given the reduction of mass that took place in the digestion process. Although Harvest hoped to significantly reduce the post-processing effort by working with its suppliers, the company anticipated that initially, source separation would remove only 95% of the contaminants, leaving the remaining 5% to be screened out in a post-processing step. These contaminants would be taken to a landfill, but ultimately the goal was to train suppliers well enough to reduce contamination rates to 1%–2%.
Harvest: Organic Waste Recycling with Energy Recovery (B) 611-034
3
Harvest realized that some of the waste generators with more complicated source-separation processes would not choose to contract with Harvest for waste disposal. To compensate suppliers for their efforts and to retain reluctant waste generators, Harvest decided to charge a lower tipping fee, in the range of $50 per ton, for source-separated waste. Even so, Harvest knew that it would lose some waste generator clients if they were required to source separate. The company had to ensure that it could still source enough organic waste to use the capacity of its plant. Since the quality of the incoming waste was higher, the compost quality was also higher, allowing the firm to charge $20–$22 per ton.
An additional advantage of source separation was that the waste generator could simultaneously separate the recyclables. By keeping metals, plastic, glass, and paper separate from trash, recyclable material was more valuable, garnering a price of $130 per ton.
,
9 – 6 1 1 – 0 3 3
R E V : A U G U S T 1 , 2 0 1 2
________________________________________________________________________________________________________________
Professors Deishin Lee (HBS) and Baris Ata (Northwestern University) and Doctoral Candidate Mustafa H. Tongarlak (Northwestern University) prepared this case. HBS cases are developed solely as the basis for class discussion. Cases are not intended to serve as endorsements, sources of primary data, or illustrations of effective or ineffective management. Copyright © 2010, 2012 President and Fellows of Harvard College. To order copies or request permission to reproduce materials, call 1-800-545- 7685, write Harvard Business School Publishing, Boston, MA 02163, or go to www.hbsp.harvard.edu/educators. This publication may not be digitized, photocopied, or otherwise reproduced, posted, or transmitted, without the permission of Harvard Business School.
D E I S H I N L E E
B A R I S A T A
M U S T A F A H . T O N G A R L A K
Harvest: Organic Waste Recycling with Energy Recovery (A)
Waste is merely raw material in the wrong place. — Frederick Talbot
With a nonchalant flick of his wrist, George tossed the remainder of his sandwich in the trash can on his way to his operations class. The sandwich remnant, loosely wrapped in parchment paper, sitting on a rigid polystyrene plate, fluttered briefly inside the receptacle before landing atop an ignoble heap, henceforth relegated to a comingled existence with other items that had served their brief useful purpose. The amount of natural, human, and capital resources that were spent to produce and assemble the components of the sandwich, and the plate and parchment paper that fleetingly encapsulated it, seemed hardly justified by George’s unappreciative hurried bites and last gesture of indifference—consigning the remains to a purgatory in the waste management system.
Municipal Solid Waste
Total and per capita municipal solid waste (MSW) generation had increased steadily in the latter part of the twentieth century (Exhibit 1), in parallel with and often attributed to the increase in the U.S. gross domestic product. In 2008, 250 million tons of MSW were generated in the U.S.1 MSW included trash from households and commercial establishments, and institutions such as grocery stores, schools, and office buildings.2 MSW was composed of containers and packaging (30.8% by weight), nondurable goods (23.5%), durable goods (18.3%), yard trimmings (13.2%), food scraps (12.7%), and miscellaneous inorganic wastes (1.5%) (see Exhibit 2). There were two general dispositions for MSW: disposal and recycling.
1 To put this in perspective, 250 million tons of waste could cover the entire state of Ohio with a 7-foot layer of trash.
2 In addition to MSW, the industrial sector generated waste that was classified as industrial waste. A conservative estimate of industrial waste generated in the U.S. per year was 7.6 billion tons. Most of this waste was from agricultural and mining operations. (Source: U.S. EPA http://www.epa.gov/wastes/nonhaz/industrial/guide/index.htm.)
611-033 Harvest: Organic Waste Recycling with Energy Recovery (A)
2
Disposal
The disposal of waste implied that the material would no longer serve a useful purpose. The most common form of waste disposal was to dump it in a landfill, a large hole in the ground that was “filled” by the waste. This was typically the most inexpensive disposal method and the easiest to operate. Although the smelly and unattractive “town dump” was generally tolerated by the population, the realization that landfills were polluting the environment led to a series of regulations. As rain trickled through the waste underground, mixing with the various forms of organic and inorganic waste, it created toxic leachate that could potentially contaminate the soil and groundwater. The decomposition of organic material in the landfill also released greenhouse gases into the atmosphere (including methane, a particularly potent greenhouse gas that had 20 times the global warming potential of carbon dioxide). Although some of these gases could be captured, the technology available could capture only half of the landfill gas that was generated, which meant that the rest was still released into the atmosphere (including half the methane). The captured methane was typically flared, turning it into carbon dioxide and water, but it could also be used as fuel to generate electrical energy.
Because of these environmental hazards, the Resource Conservation and Recovery Act (RCRA) of 1976 gave the U.S. Environmental Protection Agency (EPA) the authority to regulate the management of non-hazardous solid wastes (and control hazardous waste). In particular, Subtitle D of the RCRA specified technical and operational requirements for municipal solid waste landfills to minimize their environmental impact, significantly raising the capital and operating costs of a landfill.3 Moreover, as land became more valuable, many states started to severely limit the number of landfill permits.
In response to higher operating costs and increased permit restrictions, landfill operators strived to increase the existing landfill capacity by compacting the waste to fit as much per cubic meter as possible. However, the increase in capacity afforded by compacting the waste did not keep pace with the growth of urban populations and the resulting increase in waste generation. A shortage of landfill space close to population centers led to higher tipping fees4 or higher transport costs to remote landfills. Further, compacting the waste significantly hindered the decomposition of the waste material and supported an anaerobic environment inside the landfill. An environment without oxygen led to the production of methane, accelerating the rate at which the powerful greenhouse gas was released by landfills into the atmosphere.
Incineration of organic and inorganic MSW in a furnace served as an alternative disposal method to landfilling. Incineration reduced the volume of waste material by approximately 95%. The remaining 5% was toxic ash material that had to be landfilled. Flue gases5 were also generated in the incineration process. Although regulations required that exhaust from incinerators be cleaned by a series of filters and scrubbers before entering the atmosphere, it was impossible to completely remove pollutants from the exhaust stream. The incineration process also produced heat, which could be used to boil water to power steam engines to generate electricity. This process was commonly called “waste to energy.” The amount of electricity that a ton of waste could generate depended on the
3 Federal standards for landfills included location restrictions, composite-liner requirements, leachate collection and removal systems, operating practices, groundwater monitoring requirements, closure and postclosure care requirements, corrective- action provisions, and financial assurance. (Source: http://epa.gov/osw/nonhaz/municipal/landfill.htm.)
4 A tipping fee was the dollar rate charged by the landfill operator to accept waste that was dumped, or “tipped,” into its landfill.
5 Flue gas was exhaust from a fireplace, oven, furnace, boiler, or steam generator that exited into the atmosphere through a flue—i.e., a pipe or channel.
Harvest: Organic Waste Recycling with Energy Recovery (A) 611-033
3
composition of the waste. Inorganic materials such as plastics were high energy-conversion materials (i.e., they produced large amounts of energy); however, plastics could generate dangerous dioxin emissions. Metals in the waste stream did not burn at all, and organic material such as food waste typically consumed more energy than it produced when burning because of its water content. Given an average mix of MSW, the incineration process could convert approximately 15%–20% of the potential energy of the fuel source into electrical energy. The minimum feasible capacity for an incinerator waste-to-energy plant was roughly 10 megawatts (MW) and required a capital investment of approximately $50 million. However, typical incinerator waste-to-energy plants had a much higher capacity, requiring capital investment in the hundreds of millions of dollars, most of which was spent on pollution-abatement equipment.
Recycling
When material was recycled, it could be used again, either in its original application or in another application. For example, aluminum cans could be recycled back into aluminum cans. Paper products, on the other hand, were generally down-cycled into less-refined paper products—e.g., office paper was down-cycled into newsprint. As the cost of waste disposal increased, municipalities and businesses started to look toward recycling as a way of diverting material from their waste streams. Recycling inorganic material such as glass, metal, and plastic was common throughout the U.S. For organic material, paper and cardboard recycling was well established, as was composting of yard trimmings. However, compared with other categories of materials, the percentage of food waste that was recycled was very low. Nationally, only 2.5% of food waste was recycled. (See Exhibits 1, 2, and 4 for recycling statistics.)
Anaerobic digestion, a form of organic recycling, broke down organic waste by using naturally occurring bacteria. Similar in nature to composting, this process was capable of decomposing a much wider range of organic material, including wood waste, agricultural residue, and food scraps (including meat products, which regular composting could not handle). The biomass in an anaerobic digestion process decomposed without oxygen and produced biogas (consisting of approximately two-thirds methane, one-third carbon dioxide, and small amounts of other gases) and “digestate” solids.6 The biogas produced could be captured and fed into an engine to generate electricity. The digestate could be aerated to produce compost, reducing the solid output to approximately 40% of the original waste volume. Thus, the anaerobic digestion process produced useful electrical and biomass output with very little associated waste. (Emissions from the gas engine generator and discharge water were the only unproductive outputs from the plant.) Anaerobic digestion technology was feasible at capacities as low as 1 MW.
The Waste Management Industry
In 2008, the waste management industry generated $56 billion in revenues from collection, processing, and disposal services. (See Exhibit 3 for waste management industry statistics.) Solid waste management was a growing industry with two public companies dominating the landscape— Waste Management, Inc. and Republic Services, respectively earning revenues of $13.4 billion and $9.4 billion in 2008. In addition to public companies, privately held companies such as Oakleaf Waste Management and Norcal Waste Systems, and municipalities also provided waste management services.
6 Digestate was a neutralized, stable biomass.
611-033 Harvest: Organic Waste Recycling with Energy Recovery (A)
4
The trend in the industry had been toward consolidation. For example, Republic Services merged with Allied Waste Industries, Inc. in December 2008, creating the second-largest waste management company in the U.S. The operational and environmental requirements imposed by the EPA made it more cost effective to operate fewer and larger landfills. Additionally, consolidation enabled pooling of expensive capital such as garbage trucks; and greater geographic coverage facilitated the optimization of collection routes.
The Waste Management Process
The waste management process was a series of aggregations. After the unceremonious dumping of George’s sandwich in the trash can, the items in the can were collected and aggregated in a dumpster that served as the collection point for George’s institution. The collection within the institution was typically done by employees or contracted to third-party firms that provided janitorial services.
Waste in the dumpster was collected by a hauler. The hauler scheduled waste collection vehicles or “garbage trucks” (typically holding 5–10 tons) to pick up waste on specific routes. Route optimization was critical to minimize collection costs. Ideally, each truck would complete its route before reaching capacity, and then drive the load to its unloading destination. If the truck filled up before the end of its route, it would have to break off to go unload. The truck would either be sent back to finish the route, or the dispatch could send another truck to finish the route if one was available. Breaking off was very expensive for the hauler. Often the unloading destination was far from the pickup route requiring additional time (for the driver and truck) and fuel. Moreover, there was a high opportunity cost for the highly specialized, expensive truck to drive back and forth between the unloading destination and the pickup route.
Garbage trucks could take the waste directly to its disposal destination (e.g., landfill site, waste-to- energy plant, or a materials recovery facility), or it could take it to a transfer station. A transfer station was a temporary holding site for locally collected waste. Waste from multiple smaller waste collection vehicles was aggregated at the transfer station and then loaded into larger-capacity vehicles (e.g., railcars) that transported the waste to distant disposal sites.
Recyclables were collected separately from waste by recycling trucks, and if separated at the source, different types of recyclable material were collected by different trucks. Therefore, if organics became another recycling category, an additional truck would have to be deployed to pick up organic waste in addition to trucks that collected paper or glass, metal, and plastics. Often, recycling trucks were operated by the same hauler that collected waste.
Recycling trucks took recyclables to a materials recovery facility (MRF, pronounced “murf”). MRFs were capital-intensive facilities with highly specialized automated equipment. A “clean” MRF was a plant that accepted and sorted recyclable material. A clean MRF could process single- or dual- stream recyclables. Single-stream MRFs accepted comingled recyclable material, and dual-stream MRFs handled source-separated material, usually separated into a mixed container stream (glass, metal, and plastic) and a mixed paper stream. The percentage of residuals (non-recyclable materials that had to be taken to a landfill) from a clean MRF was typically less than 10% by weight.
A “dirty” MRF accepted a mixed solid-waste stream and sorted recyclable items from residential and commercial waste streams. Although a dirty MRF recovered a smaller fraction of the incoming waste stream (5%–45%), it had greater potential to recover recyclables. Whereas clean MRFs processed only the fraction of material that waste generators chose to recycle, dirty MRFs sorted the
Harvest: Organic Waste Recycling with Energy Recovery (A) 611-033
5
entire waste stream. MRFs (clean and dirty) sorted recyclables into homogeneous material types, then baled and sold the material to commodity brokers (e.g., recycled paper brokers) or end-user manufacturers (e.g., paper mills).
Harvest Company Overview
Harvest was founded in 2008 by Paul Sellew and Nathan Gilliland, and by mid-2010 had grown to a 25-employee boutique organics waste management and recycling company. Sellew had over 20 years of experience in the organics industry and saw the societal importance and business opportunity of waste diversion, recycling, and renewable energy. Gilliland brought a wealth of experience in managing and consulting for utilities, power generation, and consumer products. The company received funding from Kleiner Perkins Caufield & Byers and Munich Venture Partners. Shortly after Harvest was founded, Waste Management invested in the new company.
Harvest sought to capitalize on the untapped potential of organic waste in the waste stream. Its stated mission was to “[define] a new path for empowering organic waste—extracting value from societal waste through the production of renewable energy and nutrient-rich compost products that created healthy soils.” Organic waste recycling, like other types of recycling, leveraged the value inherent in discarded items. In the case of organics, the value was the nutrients and carbon contained in the biomass. Landfilling or incinerating organic material destroyed this value, and over time, would deplete the natural soil resources required to grow vegetation. By recycling the organic waste using a natural process (i.e., decomposition), the nutrients and carbon were converted back into rich soil. Moreover, this process allowed potential energy in the form of biogas to be captured and used to produce renewable energy.
Harvest sought markets where the supply of organic waste was abundant and reliable, and energy markets were favorable for renewable energy projects. The company was also poised to provide value through carbon markets once climate-change legislation put a price on carbon, because its recycling process avoided landfill gas and incinerator emissions. Once Harvest identified a site for a recycling plant, it worked with its technology vendors, local municipalities and businesses, and utility companies to build its operations. In 2010, it operated one of the largest food and yard-waste compost facilities in North America. This Canadian facility was located in Richmond, British Columbia, and processed 200,000 tons of organic waste per year.
Organic Waste Recycling Business Model
Harvest, and organic waste recycling firms in general, generated revenue from multiple sources. A major source of revenue came from the tipping fees that waste generators paid for each ton of waste that Harvest accepted. Typically, the tipping fee was lower than the competing landfill tipping fee. Additional revenues came from sales of electricity and compost. The price of electricity ranged from $0.06 to $0.11 per kilowatt hour (kWh).7 Harvest also received a Renewable Energy Credit (REC)8 premium for its electricity. Typically, this premium was on the order of $0.02 per kWh,
7 The price of electricity in the commodity market was typically much lower than the price negotiated through a power purchase agreement, hence the range of energy prices.
8 A Renewable Energy Credit represented one MWh of energy produced by a renewable source (solar, wind, biomass, etc.). Many states had adopted Renewable Portfolio Standard legislation requiring a percentage of the total electricity produced in the state to be from renewable sources. Instead of building their own renewable generation facilities, utilities and speculators could buy and sell “compliance” RECs to satisfy this obligation. There was also a “voluntary” market for RECs which allowed
611-033 Harvest: Organic Waste Recycling with Energy Recovery (A)
6
although it could range from less than $0.01 to $0.08 per kWh. High-quality compost could be sold for at least $20–$22 per ton, possibly higher depending on the quality of incoming waste. The cost of hauling waste was approximately $20 per ton.
The capital cost for a 50,000-ton facility was approximately $12 million ($10 million for the processing equipment and $2 million for the engine generator). The expected life of the facility was 20 years, although the engine generator would have to be replaced after 10 years. To staff the facility, one supervisor (at $50,000 per year plus benefits) and two operators (at $40,000 per year plus benefits) to load and unload waste were required. Other operational costs included maintenance, utilities, and administration, which would total an average of $670,000 per year. The plant operated 8 hours per day, 6 days per week, 52 weeks per year.
Organic Waste Recycling Process
Over the course of a working day, approximately 20 recycling trucks arrived at the plant, each carrying an average 8 tons of organic waste. When a truck arrived at the recycling plant, it was first weighed. The contents were then dumped onto the tipping floor where rough sorting for obvious inorganic content was done. A front-end loader stacked the waste in a pile on the tipping floor until it could be loaded into one of 16 hydrolysis percolators, where the anaerobic digestion process started. The truck was weighed again as it left the plant, and the tipping fee was charged for the difference between the inbound and outbound weight.
The plant’s operations had to adhere to the conditions of state and local permits. One of these conditions was the control of odor. To minimize the odor emanating from the plant, the entire tipping floor was enclosed in a building that exhausted all indoor air continuously to a biofilter. Moreover, organic waste could be stored on the tipping floor for a maximum of two days. Therefore, the operations of the plant had to be carefully synchronized with the expected incoming organic waste stream.
The basic organic waste recycling process consisted of an anaerobic decomposition process that generated nutrient-rich digestate and biogas. The length of time and quality of the biogas produced from this natural process could vary considerably. To shorten the process and reduce the variance in output, Harvest used state-of-the-art technology to manage and increase the efficiency of the decomposition process.
The company used an anaerobic digestion system that processed organic waste in two stages— hydrolysis and methanization—over a span of approximately 15 days. The organic waste was first loaded into a 150-ton percolator where hydrolysis took place. Spray mechanisms inside the percolator distributed anaerobic microorganisms in a liquid solution. These microorganisms produced enzymes that broke down the complex soluble particles into simpler molecules like sugars, which were then converted into organic acids in solution, or “hydrolysate.” The hydrolysis percolator was essentially a 15x20x90-foot rectangular tunnel (see Exhibit 6). The size of the tunnel was determined by the loading and unloading mechanics of the waste. The digester had to be big enough for th
Collepals.com Plagiarism Free Papers
Are you looking for custom essay writing service or even dissertation writing services? Just request for our write my paper service, and we'll match you with the best essay writer in your subject! With an exceptional team of professional academic experts in a wide range of subjects, we can guarantee you an unrivaled quality of custom-written papers.
Get ZERO PLAGIARISM, HUMAN WRITTEN ESSAYS
Why Hire Collepals.com writers to do your paper?
Quality- We are experienced and have access to ample research materials.
We write plagiarism Free Content
Confidential- We never share or sell your personal information to third parties.
Support-Chat with us today! We are always waiting to answer all your questions.
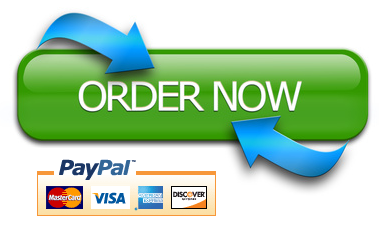