When we look at quality cost we look at a few areas:
Please see below and write a responseat least a paragraph long for each:
Posting #1:
The first thing we need to answer is “what is the cost of quality?” The cost of quality (COQ) simply explained is process of an organization to determine the extent of what resources and activities are needed to prevent poor quality in their products or services to prevent both internal and external failures. This cost can be both monetary and non-tangible.
When we look at quality cost we look at a few areas:
Cost of poor quality (COPQ) – cost of providing poor quality products or services
Appraisal costs – measuring and monitoring the activities related to quality (parts inspections, products, services confirm to specifications, supplier ratings)
Internal failure costs – incurred to remedy defects after delivery from suppliers, before delivery to final customer (waste, scrap, rework, analysis)
External failure costs – incurred to remedy defects discovered after shipment to final customers (repairs, service, warranty claims, complaints, returns)
Prevention costs – incurred to prevent or avoid quality issues or concerns (design, implementation, internal QM maintenance – Planning, Assurance, Training)
COQ and organizational objectives – total cost of quality to do the job (costs of poor quality [failures] + good quality [appraisal/prevention])
The are just a few examples of these areas. Each organization will most likely follow a standard, but the actual cost of quality is depending on their entire organizational structure and how many areas of quality managements they put into place.
Posting #2:
The term “cost of quality” refers to all of the costs that are incurred to prevent defects in products, or costs that are a result of defects in products. These costs are incurred in an effort to keep defective products from falling into the hands of customers. The Cost of Conformance is made up of Prevention’s costs and Appraisal costs.
Prevention costs include; all those costs which are incurred for activities that are specifically designed to prevent poor product quality from happening in the first place. It is much less expensive to prevent a problem from happening than it is to find and correct the problem after it has occurred.
Appraisal costs; which are also called inspection costs, are those costs which are incurred to identify defective products before they are shipped to customers. However, performing appraisal activities does not prevent defects from occurring. Most managers now realize that maintaining a team of inspectors is not an effective approach to quality control. A better approach is asking employees to be responsible for their own quality control, along with creating designs for how to manufacture a defect-free product. This approach allows quality to be built into the product, rather than relying on inspections to identify any defects.
the cost of non conformance are costs are incurred because defects are produced despite efforts by the organization to prevent them. Therefore these costs are also known as costs of poor quality (Links to an external site.). These failure costs are incurred when a product fails to conform to its design specifications .The cost of non conformance is made up of internal failure costs and external failure costs.
Internal failure costs result from identification of defects before they are shipped to customers. They are identified within the scope of the project. These costs include rejected products, reworking of defective units, and downtime caused by quality problems.It also includes any costs involved if the company has to reject and throw parts of their project work, which is also called “scrap”. If an organization’s appraisal activities are effective, it has a better chance of detecting defects internally. This increases the level of internal failure costs.
External failure costs are costs that are a result of delivering a defective product to the customer. These costs include warranty, repairs and replacements, product recalls, liabilities arising from legal action against a company, and lost sales arising from a reputation for poor quality. Such costs can even decimate a business’s profits.External failure costs also give rise to intangible costs. For instance, an organization may lose its future business with its existing customer for delivering a product of poor quality. These kinds of costs are not there on the balance sheet, but they can definitely have an adverse impact on the income statement.
In conclusion I think that any business entity will always make more if they spend more. Customers and people alike will always want to spend a little bit more money for a product that is that of quality and is something that will last.
Collepals.com Plagiarism Free Papers
Are you looking for custom essay writing service or even dissertation writing services? Just request for our write my paper service, and we'll match you with the best essay writer in your subject! With an exceptional team of professional academic experts in a wide range of subjects, we can guarantee you an unrivaled quality of custom-written papers.
Get ZERO PLAGIARISM, HUMAN WRITTEN ESSAYS
Why Hire Collepals.com writers to do your paper?
Quality- We are experienced and have access to ample research materials.
We write plagiarism Free Content
Confidential- We never share or sell your personal information to third parties.
Support-Chat with us today! We are always waiting to answer all your questions.
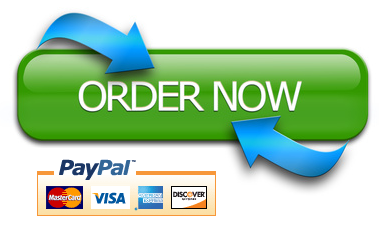