These four information sources are production schedules
Peer 1:
Material requirements planning (MRP) systems use time-sensitive, priority-planning techniques to calculate labor schedules and material requirements for product runs in manufacturing facilities. MRP systems heavily rely on innovative IT solutions to maintain updated information about manufacturing needs, customer demands, inventory levels and current deadlines. MRP systems are designed to optimize inventory handling and production management.MRP systems use four key pieces of information to determine what and when materials should be ordered. These four information sources are production schedules, material specs, production cycle times and supplier lead times. Production schedules describe in detail when each product should manufactured. This information is used to adjust production machines and process flows. Material specs list the parts and materials that are required to make each product. The production cycle time establishes standard time frames in correlation with target material needs at each manufacturing stage. The supplier lead time indicates procurement and logistical time frames.The primary objective of MRP systems is to get the correct materials to the right place at the correct time. Most organizational objectives focus on production inventory, priorities and capacity. When it comes to inventory, MRP systems help management to order the right quantity of parts at the right time. Materials that are prematurely delivered to a manufacturing facility with limited storage space may cause inventory problems. When it comes to priorities, MRP systems help management prioritize the most time sensitive deadlines while monitoring due dates. MRP helps management with capacity planning because they can forecast accurate and complete production runs.
References
Render, B., Heizer, J., & Munson, C. (2017). Principles of operations management: Sustainability and supply chain management (10th ed.). Boston: Pearson
Peer 2:
“Most of the product line is custom designed and assembled to meet the specific and often unique requirements demanded by the ambulance’s application and customer preferences. This variety of products and the nature of the process demand good material requirements planning (Heizer, Render, & Munson, 2017). The five requirements are:
“1. Master production schedule (what is to be made and when)
2. Specifications or bill of material (materials and parts required to make the product
3. Inventory availability (what is in stock)
4. Purchase orders outstanding (what is on order, also called expected receipts)
5. Lead times (how long it takes to get various components)” (Heizer, Render, & Munson, 2017).
The master production schedule needs to be in lined with an aggregate plan. The master production schedule specifies when and what is being made, it basically disaggregates the aggregate plan.
Heizer, J., Render, B., & Munson, C. (2017). Principles of Operations Management. Pearson Education, Inc.
Collepals.com Plagiarism Free Papers
Are you looking for custom essay writing service or even dissertation writing services? Just request for our write my paper service, and we'll match you with the best essay writer in your subject! With an exceptional team of professional academic experts in a wide range of subjects, we can guarantee you an unrivaled quality of custom-written papers.
Get ZERO PLAGIARISM, HUMAN WRITTEN ESSAYS
Why Hire Collepals.com writers to do your paper?
Quality- We are experienced and have access to ample research materials.
We write plagiarism Free Content
Confidential- We never share or sell your personal information to third parties.
Support-Chat with us today! We are always waiting to answer all your questions.
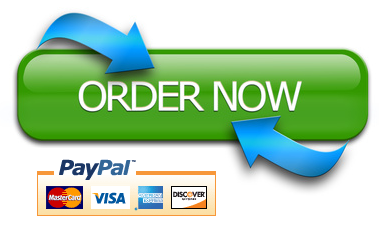