Think about three of your favorite fast-food restaurants. What type of layout is used in the food preparation area of each? Are these layouts a good fit with
Week 5 ~ Discussion Question 9 ~ Due Thursday 9/12
Think about three of your favorite fast-food restaurants. What type of layout is used in the food preparation area of each? Are these layouts a good fit with the organization? Why or why not? Should the layout be changed and if so why? (100 -125 words)
NO AI, CHEGG, CHATGT, ETC.
PPTX IS YOUR ONLY SOURCE
Copyright ©2020 McGraw-Hill Education. All rights reserved. No reproduction or distribution without the
prior written consent of McGraw-Hill Education.
Chapter 5
Manufacturing and Service Process Structures
Copyright ©2020 McGraw-Hill Education. All rights reserved. No reproduction or distribution without the
prior written consent of McGraw-Hill Education.5-2
Learning Objectives
5-1 Compare and contrast the seven process structures: project, job shop, batch, repetitive process, continuous process, mass customization, and cellular manufacturing.
5-2 Compare and contrast the goals and challenges associated with a service factory, a mass service, a service shop, and a professional service.
5-3 Describe how each of the operations layouts—fixed- position, functional, product, and cellular—is designed to meet the demands placed upon it.
5-4 Analyze a product layout using line balancing.
5-5 Explain how technology is used in the supply chain and the benefits and drawbacks of digital transformation.
Copyright ©2020 McGraw-Hill Education. All rights reserved. No reproduction or distribution without the
prior written consent of McGraw-Hill Education.5-3
Learning Objective 5-1
Process Design at Invisalign
• The design of each step from the dentist’s office through manufacturing guarantees that each patient receives a high quality, cost-effective treatment
Copyright ©2020 McGraw-Hill Education. All rights reserved. No reproduction or distribution without the
prior written consent of McGraw-Hill Education.5-4
Learning Objective 5-1
Product-Process Matrix
Figure 5-1 Product-Process Matrix
Source: Adapted from R.Hayes and S.Wheelwright, Restoring Our
Competitive Edge: Competing Through Manufacturing (New York: John Wiley & Sons, 1984).
Copyright ©2020 McGraw-Hill Education. All rights reserved. No reproduction or distribution without the
prior written consent of McGraw-Hill Education.5-5
Learning Objective 5-1
Comparison of Process Types: Project
• Output
– Unique
– One of a kind
• Example
– Custom home
– Designing a video game
• Process
– Unique flow patterns
– High complexity
– Employees and equipment flexibility
– Activities outsourced to specialists
Copyright ©2020 McGraw-Hill Education. All rights reserved. No reproduction or distribution without the
prior written consent of McGraw-Hill Education.5-6
Learning Objective 5-1
Comparison of Process Types: Job Shop
• Output
– Customized, low volume
• Example
– Auto repair
– Beauty salon
• Process
– High variety of materials
– Determining schedules is challenging
– High work-in-process inventory
– Highly skilled, flexible workers
– General-purpose equipment
Copyright ©2020 McGraw-Hill Education. All rights reserved. No reproduction or distribution without the
prior written consent of McGraw-Hill Education.5-7
Learning Objective 5-1
Comparison of Process Types: Batch
• Output
– Moderate volume and variety
• Example
– Bakery
– Automotive parts
– Cinema
• Process
– Dominant flow patterns
– Some common materials
– Setup time can be high
– Moderately flexible employees and equipment
Copyright ©2020 McGraw-Hill Education. All rights reserved. No reproduction or distribution without the
prior written consent of McGraw-Hill Education.5-8
Learning Objective 5-1
Comparison of Process Types: Repetitive Process
• Output
– Standard products with a range of options
• Example
– Appliances
– Automobiles
– Buffet restaurant
• Process
– All products have the same flow pattern
– Standard methods and materials are used
– Low-skilled workers specialize in completing a limited number of activities
Copyright ©2020 McGraw-Hill Education. All rights reserved. No reproduction or distribution without the
prior written consent of McGraw-Hill Education.5-9
Learning Objective 5-1
Comparison of Process Types: Continuous Process (1 of 2)
• Output
– Commodities with high volume, little variety
• Example
– Aluminum cans
– Laundry detergent
– Gasoline
• Process
– Products have the same flow pattern
– Operations often run 24/7
– Line stoppages are very costly
– Highly specialized equipment
– Low-skilled operators
Copyright ©2020 McGraw-Hill Education. All rights reserved. No reproduction or distribution without the
prior written consent of McGraw-Hill Education.5-10
Learning Objective 5-1
Comparison of Process Types: Continuous Process (2 of 2)
• Output
– High-volume continuous and repetitive process while increasing variety
• Example
– Invisalign
– NIKEiD
• Process
– Process flexibility
– Mass customization occurs when products assembled from standard modules
– Product configuration postponed until order is received
Copyright ©2020 McGraw-Hill Education. All rights reserved. No reproduction or distribution without the
prior written consent of McGraw-Hill Education.5-11
Learning Objective 5-1
Student Activity (1 of 3)
Companies focusing on different competitive priorities can use different process structures for the same type of product. One example is clothing—off-the-rack compared to custom tailored. Identify a product and competitors who are using different competitive priorities. What position on the product-process matrix would you expect for each?
Copyright ©2020 McGraw-Hill Education. All rights reserved. No reproduction or distribution without the
prior written consent of McGraw-Hill Education.5-12
Learning Objective 5-1
Student Activity (2 of 3)
Do some research to identify a product that is made using 3D printing. How have operations and supply chain processes changed as a result of moving to the new manufacturing process?
Copyright ©2020 McGraw-Hill Education. All rights reserved. No reproduction or distribution without the
prior written consent of McGraw-Hill Education.5-13
Learning Objective 5-1
Cellular Manufacturing and Mass Customization
• Cellular Manufacturing: the production of products with similar process characteristics on small assembly lines called cells; used to increase flexibility
• Advances in technology like 3D printing, robotics, or flexible manufacturing systems (FMS) allow for mass customization at a lower cost
Copyright ©2020 McGraw-Hill Education. All rights reserved. No reproduction or distribution without the
prior written consent of McGraw-Hill Education.5-14
Learning Objective 5-1
Aligning Process Structure and Market Orientation
• Engineer to Order (ETO): unique, customized products
• Make to Order (MTO): similar design, but customized during production
• Assemble to Order (ATO): produced from standard components and modules
• Make to Stock (MTS): goods made and held in inventory in advance of customer orders
Copyright ©2020 McGraw-Hill Education. All rights reserved. No reproduction or distribution without the
prior written consent of McGraw-Hill Education.5-15 Learning Objective 5-1
Market Orientation and Order Timing
Figure 5-2 Market Orientation and Order Timing
Copyright ©2020 McGraw-Hill Education. All rights reserved. No reproduction or distribution without the
prior written consent of McGraw-Hill Education.5-16
Learning Objective 5-2
Service Process Matrix
Figure 5-3 Service Process Matrix
Source: R.W. Schmenner, ”How Can Service Businesses Survive and
Prosper?” Sloan Management Review 27, no.3 (1986), pp.21–32. Copyright © 1986 by Massachusetts Institute of Technology. Reprinted with permission.
Copyright ©2020 McGraw-Hill Education. All rights reserved. No reproduction or distribution without the
prior written consent of McGraw-Hill Education.5-17
Categories of Services Examples
• Professional services: lawyers, doctors, consultants, accountants
• Service factory: trucking companies, airlines, hotels
• Service shops: automobile repair shops and hospitals
• Mass services: retail banks, gas stations, and other retail outlets
Learning Objective 5-2
Copyright ©2020 McGraw-Hill Education. All rights reserved. No reproduction or distribution without the
prior written consent of McGraw-Hill Education.5-18
Student Activity (3 of 3)
Think of the last service you purchased. What category of service was it? Can you suggest changes in product features or delivery technologies that would move the service to another category? What could be the advantages of such a change?
Learning Objective 5-2
Copyright ©2020 McGraw-Hill Education. All rights reserved. No reproduction or distribution without the
prior written consent of McGraw-Hill Education.5-19
Learning Objective 5-2
Managing Front-Office and Back-Office Processes
• Front Office: processes that have contact with the customer
• Back Office: behind-the-scenes activities not seen by the customer
Copyright ©2020 McGraw-Hill Education. All rights reserved. No reproduction or distribution without the
prior written consent of McGraw-Hill Education.5-20
Learning Objective 5-3
Operations Layout
• Fixed Position: product cannot be moved during production
• Functional: similar resources grouped together
• Product: resources arranged by regularly occurring sequence of activities
• Cellular: workstations arranged into small assembly lines to make families of products with similar processing needs
Copyright ©2020 McGraw-Hill Education. All rights reserved. No reproduction or distribution without the
prior written consent of McGraw-Hill Education.5-21
Learning Objective 5-4
Line Balancing in Product Layouts
Used to assign individual tasks to work areas for a desired output rate
1. Identify precedence relationships
2. Calculate takt time = available production time in a period
outputneeded in that period to meet customer demand
3. Determine theoretical minimum number of workstations
4. Assign as many tasks as possible to each workstation until sum of task times adds up to takt time
5. Determine efficiency of the balanced line
Copyright ©2020 McGraw-Hill Education. All rights reserved. No reproduction or distribution without the
prior written consent of McGraw-Hill Education.5-22
Learning Objective 5-4
Line Balancing: Example (1 of 5)
Table 5-3 Precedence Relationships for Sausage and Pepperoni Pizza Assembly
Task Predecessors Time
(minutes)
A Shape the dough to form the crust None 2
B Add the pizza sauce A 1
C Add the cheese B 2
D Add the sausage C 0.75
E Add the pepperoni C 1
F Package the pizza D, E 1.5
G Label the package F 0.5
Total Time 8.75
Number of Pizzas per Day: 200
Hours Operating per Day: 8
Copyright ©2020 McGraw-Hill Education. All rights reserved. No reproduction or distribution without the
prior written consent of McGraw-Hill Education.5-23
Learning Objective 5-4
Line Balancing: Example (2 of 5)
Figure 5-4 Precedence Diagram for Sausage and Pepperoni Pizza Assembly
Copyright ©2020 McGraw-Hill Education. All rights reserved. No reproduction or distribution without the
prior written consent of McGraw-Hill Education.5-24
Learning Objective 5-4
Line Balancing: Example (3 of 5)
a. What is the takt time?
Takt time = Available service time/Output needed per unit time
Takt time = [Number of hours/day × 60 min/hour]/Pizza per day
Takt time = [8 hours/day × 60 min/hour]/200 Pizzas per day
Takt time = 0.04 hours
Takt time = 2.4 minutes per workstation
b. What is the theoretical number of workstations?
N = Total number of minutes required to process all tasks per
pizza/Number of minutes per station
N = [2 min + 1 min + 2 min + 0.75 min + 1 min + 1.5 min + 0.5 min]/2.4 min per station
N = 8.75 min per pizza/2.4 min per station= 3.7, so round up to 4 workstations
Copyright ©2020 McGraw-Hill Education. All rights reserved. No reproduction or distribution without the
prior written consent of McGraw-Hill Education.5-25
Learning Objective 5-4
Line Balancing: Example (4 of 5)
c. Assign the tasks to the workstations to balance the line using the longest operating time rule.
TABLE 5-4 Workstation Assignments for Pizza: Balanced Using the Longest Task Time
Five workstations needed
Workstation Tasks in Order Workstation
Time (minutes) Idle Time (minutes)
1 A 2 0.4
2 B 1 1.4
3 C 2 0.4
4 E, D 1.75 0.65
5 F, G 2 0.4
Copyright ©2020 McGraw-Hill Education. All rights reserved. No reproduction or distribution without the
prior written consent of McGraw-Hill Education.5-26
Learning Objective 5-4
Line Balancing: Example (5 of 5)
d. What is the efficiency of the balanced line?
Efficiency = [Total time per pizza/(Number of
workstations needed × Number of minutes
per pizza)] × 100
Efficiency = [8.75 minutes needed per pizza/(5
workstations × 2.4 minutes per pizza)] × 100
Efficiency = 0.729 or 72.9 percent
Copyright ©2020 McGraw-Hill Education. All rights reserved. No reproduction or distribution without the
prior written consent of McGraw-Hill Education.5-27
Learning Objective 5-4
Cellular Layout
FIGURE 5-5 Product, Functional, and Cellular Layouts
Copyright ©2020 McGraw-Hill Education. All rights reserved. No reproduction or distribution without the
prior written consent of McGraw-Hill Education.5-28 Learning Objective 5-5
Capability Enabling Technologies
• Decision Support
– Computing power and data management
• Processing
– Material and data processing
• Communications
– Greater connectivity
• Integrative
– Combine all other capabilities
Copyright ©2020 McGraw-Hill Education. All rights reserved. No reproduction or distribution without the
prior written consent of McGraw-Hill Education.5-29
Information Processing and Sharing
• Sales and inventory data are automatically captured by
– Point of sale (POS) bar codes
– RFID scanners
– Sensors
• Manufacturing execution systems (MES)
• Warehouse management systems (WMS)
• Transportation management systems (TMS)
• Blockchain
Learning Objective 5-5
Copyright ©2020 McGraw-Hill Education. All rights reserved. No reproduction or distribution without the
prior written consent of McGraw-Hill Education.5-30
Process Automation
• Mobility: mobile apps increase convenience for customers
• Robots: have helped plants be safer, more efficient, and produce high quality
• Internet of Things (IoT): allows products and machines with software and sensors to connect to the Internet and share data with other devices
Learning Objective 5-5
Copyright ©2020 McGraw-Hill Education. All rights reserved. No reproduction or distribution without the
prior written consent of McGraw-Hill Education.5-31
Challenges to Digital Transformation (1 of 2)
• Cybersecurity: risk of criminals accessing systems to cause damage, steal data, or hold data for ransom
• Data Privacy: data about customers must be protected and not misused
• Supply Chain Talent: challenges in understanding how to effectively adopt and implement appropriate technologies
• Technical Talent: implementing, managing, and maintaining technology requires highly skilled IT professionals, process engineers, and maintenance employees
Learning Objective 5-5
Copyright ©2020 McGraw-Hill Education. All rights reserved. No reproduction or distribution without the
prior written consent of McGraw-Hill Education.5-32
Challenges to Digital Transformation (2 of 2)
• Investment Costs: purchasing and installing technology for physical processes requires capital investment, increasing fixed costs
• Perceived Quality: customers may have concerns with the quality of a more highly automated process
• Societal Issues: some jobs will be eliminated with the use of robots in manufacturing and distribution
Learning Objective 5-5
Copyright ©2020 McGraw-Hill Education. All rights reserved. No reproduction or distribution without the
prior written consent of McGraw-Hill Education.5-33
Manufacturing/Service Process Summary
1. Product-process matrix classifies processes based on volume and variety.
2. Services are categorized by customization and labor/capital intensity.
3. Service processes can be front or back office.
4. Layout is the physical arrangement of resources in a process.
5. Process automation and technology affect costs and capabilities.
Collepals.com Plagiarism Free Papers
Are you looking for custom essay writing service or even dissertation writing services? Just request for our write my paper service, and we'll match you with the best essay writer in your subject! With an exceptional team of professional academic experts in a wide range of subjects, we can guarantee you an unrivaled quality of custom-written papers.
Get ZERO PLAGIARISM, HUMAN WRITTEN ESSAYS
Why Hire Collepals.com writers to do your paper?
Quality- We are experienced and have access to ample research materials.
We write plagiarism Free Content
Confidential- We never share or sell your personal information to third parties.
Support-Chat with us today! We are always waiting to answer all your questions.
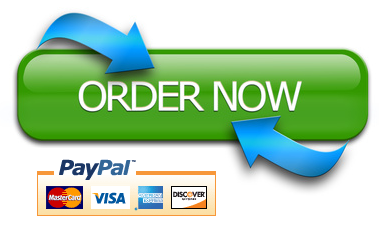