Select a key topic to research and discuss. Key topics are the major concepts addressed within each chapter Concepts that have their own sections consisting of several paragraphs and begin
The student will post one thread of at least 700 words plus the associated annotated bibliography by 11:59 p.m. (ET) on Sunday of the assigned modules. The thread and replies must be written in current APA format in a substantive manner and must not contain spelling and/or grammar errors.
BUSI 650
Discussion Instructions
The student will post one thread of at least 700 words plus the associated annotated bibliography by 11:59 p.m. (ET) on Sunday of the assigned modules. The thread and replies must be written in current APA format in a substantive manner and must not contain spelling and/or grammar errors.
The Thread
Select a key topic to research and discuss. Key topics are the major concepts addressed within each chapter. Concepts that have their own sections consisting of several paragraphs and begin with a bold font heading are appropriate key topics. You may choose the same topic as a peer, but the topics must be addressed from different vantage points (perspectives).
After you have selected your key topic, use the Internet to search for at least 5 scholarly resources that relate to the topic and have been published within the last 5 years. Academic articles and journals must be reputable and obtained from professional websites that address the content of this course. Popular magazines and online sources such as Wikipedia are not permissible.
After reading the articles, select 1 article relating to your key topic that you wish to use in your thread. Your thread must be posted in the text box and in addition to posting the thread in the text box, attach a Word file of your thread. Adhere to the following format:
1. Key Concept Explanation: Define your key topic by using a source other than the textbook. Give a clear, concise overview of the essential elements relevant to understanding your key topic. In addition, explain why you are interested in this topic (e.g., academic curiosity, application to a current issue related to employment, or any other professional rationale). This section must be at least 100 words.
2. Comparison: Compare your research with what you have studied during the module in which the key topic/thread is assigned. Note differences or commonalities about your key topic, providing evidence that you have extended your understanding of this topic beyond the textbook readings. This is an opportunity for you to cite the additional articles you originally researched. This section must be at least 200 words.
3. Article Summary: In your own words, provide a clear and concise summary of the article you selected. This section must be at least 200 words.
4. Biblical Integration: Include at least 3 appropriate biblical references. Explain the relevance of your key topic to God’s law and how it can be applied in a Christian context. This section must be at least 100 words.
5. Application: Specifically state how your key topic has been applied to real-world businesses or describe the potential your key topic has to influence today’s business world. Your application must possess a professional rationale that demonstrates the significance of your key topic. This section must be at least 100 words.
6. Annotated Bibliography: Cite the articles you researched in current APA format. An annotation must accompany each citation. Each annotation will consist of a descriptive and evaluative paragraph that is at least 100 words. The annotations are designed to help your classmates in their understanding of your topic. In addition, provide a persistent link for each article.
Plagiarism will not be tolerated. Review your posts and the Student Expectations prior to submission in order to ensure that your sources are properly cited.
If you need any assistance in writing, format, or persistent links, the Liberty University Online Writing Center will be able to help you.
Page 1 of 2
,
Business process reengineering
Impact on organizational performance
What is BPR?
Business Process Reengineering (BPR) involves fundamental rethinking and radical
redesign of a firm’s processes to bring about drastic improvements in organizational
performance. By increasing the efficiency and effectiveness of core processes, BPR
enables firms to enhance their productivity, quality, speed, and customer satisfaction. BPR
gained in popularity during the 1990s against the backdrop of globalization and
technological developments. Rapidly shifting macro-environmental conditions and intense
competition from both local and global players left firms vulnerable with outdated business
practices. These shifts forced organizations to rethink the way they operated. Adopting BPR
allowed firms to stay competitive and keep up with dynamic market changes. BPR is
particularly beneficial during global crises such as the present pandemic during which firms
can proactively reduce operating costs and maintain profitability.
While BPR can lead to improved firm performance, its implementation often proves to be
immensely challenging. Research suggests that 70% of BPR programs fail. As BPR can
bring about substantial change, such projects are often met with employee resistance and
resentment. Employees who are habituated to a routine way of doing things may be
unwilling to adapt to new systems and processes. Moreover, reengineering is a cyclic
process whereby a set of activities is built upon the success of previous phases. Hence
organization-wide commitment and effort may be required for the successful execution.
Several factors can contribute to the success of BPR programs.
Top management commitment
A firm’s top management team sets the direction of the organization. They must have a clear
vision of how BPR will be implemented and how it could potentially benefit the firm. Sufficient
financial and non-financial resources must be made available to support the program. Top
management is also responsible for cultivating an internal environment or culture that fosters
high performance. New programs such as BPR require a significant change on the part of
employees. The successful application of such programs thus requires the active support and
backing of the top management. Top management must build awareness of the program and
advocate its benefits. They should constantly communicate with employees, motivate them
and sustain their interest in the practice over a long time period.
Organizational readiness
Employees need to be adequately prepared before launching a BPR program. Moreover,
the readiness of employees must be both in terms of knowledge and mindset. Employees
must have the right skills, and necessary training to be able to successfully implement
change. Further, employees must have the belief and confidence that they themselves and
the organization possess the abilities to make the proposed changes. An organization
PAGE 26 j STRATEGIC DIRECTION j VOL. 38 NO. 1 2022, pp. 26-28, © Emerald Publishing Limited, ISSN 0258-0543 DOI 10.1108/SD-11-2021-0136
should have open communication channels to share feedback during the reengineering
phase. The firm must also be adept at overcoming resistance and conflicts that arise during
times of change.
Information technology
IT can play a key enabling role in the implementation of BPR. Technology may allow the
automation of numerous processes and help eliminate manual and lower value-adding
activities. IT can be utilized to redesign business processes to enhance productivity and
quality. Further, IT systems can support decision making, provide timely information, end
facilitate coordination and communication across the enterprise. Thus, before launching the
BPR program, organizations should have integrated information systems in place. Equally
important is having qualified personnel who can expertly utilize such systems.
People management
While top management may initiate BPR, it is the employees who are primarily responsible
for seeing through the execution. People management hence is a critical factor for
successful BPR implementation. The organization must invest resources in the training and
development of employees. These educational initiatives make employees more
knowledgeable about BPR and help them better understand their new processes and tasks.
Moreover, the goal of the training is not only to upgrade skills but also to reduce their
uncertainties about BPR. In addition, employees must be empowered to provide ideas and
suggestions to improve business processes. Their involvement in problem-solving and
decision-making diminishes their resistance to change. Rewards systems should be
aligned with employee participation and successful BPR implementation.
Organizational structure
A firm’s organizational structure may influence the outcome of the reengineering
process. The right structure allows smoother BPR implementation and results in a
greater likelihood of program success. In centralized organizations, decision-making
authority is concentrated at the higher levels of the organization. Such organizations are
more formalized whereby policies, procedures, and rules are explicitly articulated. In
contrast, in decentralized companies, decision-making and problem-solving are done
at the lower levels by employees closer to day-to-day operations. In such organizations,
a flexible work culture fosters greater creativity, teamwork, and collaboration. As BPR
requires significant employee involvement, a more decentralized and less formalized
organizational structure may be advantageous.
Strategic thinking
Strategic thinking refers to a managerial mindset that involves a shift from day-to-day
operational to long-term strategic oriented thinking. When adopting such a mindset, firms
By increasing the efficiency and effectiveness of core processes, BPR enables firms to enhance their productivity, quality, speed, and customer satisfaction.
VOL. 38 NO. 1 2022 j STRATEGIC DIRECTION j PAGE 27
emphasize on continuous information gathering, analysis, and evidence-based decision
making. Firms incorporating strategic thinking in their decision-making are more likely to
benefit from BPR.
To understand how these BPR factors impact organizational performance, the authors
studied electronics manufacturing companies from Malaysia. This industry was pivotal to
the Malaysian economy contributing both to export and employment. However, over time
the country’s electronics industry was experiencing a slowdown which was further
aggravated by the pandemic. This made the situation ripe to examine the impact of
reengineering practices on performance. Some of their key findings include:
� top management commitment positively impacted performance. Their endorsement is
likely to motivate employees;
� organization readiness was the most critical BPR factor influencing performance. Firms
must be prepared with adequate resources, communication systems, employee skill
training programs;
� IT was important to get the best out of BPR;
� people management positively impacted performance. This included having adequate
training, reward systems, employee participation, and empowerment; and
� organizational structure by itself did not have an impact on performance. However,
structure along with strategic thinking had a favorable influence.
Comment
The review is based on ‘The impact of business process reengineering on organizational
performance during the coronavirus pandemic: moderating role of strategic thinking’ by
Shahul Hameed et al. (2021), published in Foresight.
Reference
Shahul Hameed, N.S., Salamzadeh, Y., Abdul Rahim, N.F. and Salamzadeh, A. (2021), “The impact of
business process reengineering on organizational performance during the coronavirus pandemic:
moderating role of strategic thinking”, Foresight.
For instructions on how to order reprints of this article, please visit our website: www.emeraldgrouppublishing.com/licensing/reprints.htm Or contact us for further details: [email protected]
While BPR can lead to improved firm performance, its implementation often proves to be immensely challenging.
Keywords:
Business process reengineering, Strategic thinking, Organizational performance
PAGE 28 j STRATEGIC DIRECTION j VOL. 38 NO. 1 2022
- Business process reengineering
- What is BPR?
- Top management commitment
- Organizational readiness
- Information technology
- People management
- Organizational structure
- Strategic thinking
- Comment
,
Learning from design-prototyping interaction for engineering innovation from a cross- functional perspective
Demei Lee Department of Mechanical Engineering, Chang Gung University,
Taoyuan, Taiwan
Abstract Purpose – Novel engineering designs are usually infeasible for manufacturing or fail to meet the required performance. The dissimilar functionalities andmindsets between design andmanufacturing pose challenges, as well as opportunities for innovation projects. This paper aims to report the innovation process that prototyped a novel engineering design of a haptic device in an engineering research lab. The innovation process went through several design generations. Interaction between design and manufacturing drove the innovation toward both better andworse directions between generations.
Design/methodology/approach – Using the case research method, the steps of theoretical proposition development, case selection, data collection, data analysis and theory modification were followed. By interviewing the key persons, the characteristics, issues and recommendations for improvement of the innovation process were identified.
Findings – It was found that technical issues were not the hurdles in the innovation process. Instead, managing the inter-organizational mechanism proved critical to its eventual success. The educational gap between the design and manufacturing groups gave rise to communicational and perceptional distance, while the gap in terms of work experience between the two groups enlarged that distance.
Research limitations/implications – The research results may be limited to cases with similar organizational and technological contexts. Practical implications – Within an organization, the design and the manufacturing divisions are separated by a functional gap. The functional gap should be managed with multiple views, namely, technical, personal and organizational perspectives. The identified innovation process could help bridge such a gap and facilitate innovative engineering designs in research institutes. Originality/value – The effectiveness of the innovation process was, thus, found to be determined by the positive or negative reinforcement of these two gaps between the design and manufacturing of the research institute.
Keywords Prototyping, Innovation process, Creative problem solving, Design-manufacturing integration, Haptic device
Paper type Research paper
1. Introduction In a university, the research and development (R&D) capacity and the manufacturing facility are disproportionate. Usually, high caliber students and professors conduct the R&D and the manufacturing facility is mediocre and operated by technicians. In most situations, when an engineering design exceeds manufacturing capability, design modifications are required. The work culture within the university leads to a blurring of the roles of design and manufacturing. Sometimes, design functionality is misunderstood or compromised by
Cross- functional
perspective
111
Received 17 August 2019 Revised 3 November 2019
Accepted 14 November 2019
International Journal of Innovation Science
Vol. 12 No. 1, 2020 pp. 111-126
© EmeraldPublishingLimited 1757-2223
DOI 10.1108/IJIS-08-2019-0082
The current issue and full text archive of this journal is available on Emerald Insight at: https://www.emerald.com/insight/1757-2223.htm
the machine shop. Under such circumstances, the prototyping of innovative products that require the integration of both design andmanufacturing can be very challenging.
The engineering science lab at Simon Fraser University engaged in research on a haptic device over a period of six years. Four generations of the design were prototyped and two of them were patented. In spite of these achievements, the research went through a rocky and lengthy process from generation to generation. In attributing the issues that arose to this time- and effort-consuming process, the technical, organizational and personal aspects were investigated. In terms of the technical aspect, advances in interoperating computer-aided design (CAD) and computer-aided-manufacturing (CAM) tools have greatly reduced the technical issues arising from prototyping (Jannery, 2003). By contrast, the heterogeneity in the knowledge between design and manufacturing personnel has given rise to management issues (Liyanage et al., 1999). In a survey conducted on design-manufacturing integration (DMI) practices, a group-based evaluation of design and manufacturing and the use of tools and techniques to transfer manufacturing information to design have been the best tools used in new product development (NPD) (Rusinko, 1997). The various goals of the participating functional departments and the cross-functional team pose a challenge to successful new product development (Rusinko, 1999; Darawong, 2018). In recognizing the challenge as being organizational rather than technical, this study develops an analytical approach to identify the issues or factors that affect the efficiency of the innovation process.
This study has the following three objectives: (1) To identify the factors and/or behavior that barricade the innovation process. (2) To identify the factors and/or behavior that facilitate the innovation process. (3) To examine how these barriers and facilitators were involved in the innovation
process.
During the design-prototyping process, some factors or behaviors were found barriers to the innovation project. These factors may be related to different aspects, such as technical, organizational and personal. Technical factors are related to the functional expertise of the participating group and sometimes related to engineering or scientific knowledge. Personal factors are related to cognition, experience, values and other personality-related elements. Organizational factors are related to culture, value, logic and setting of the organization within which the innovation is in progress. While these factors may barricade the innovation process, they may also facilitate it if well managed. Classifying the types of factors and their underlying causes and relate them to the DMI process would help management to overcome the barriers.
The haptic device research project was used as a case study for the above purposes. The generations of the designs and prototypes are illustrated in this paper, and interviews with the key project members were conducted. The interviewees’ opinions have been synthesized to yield insights and recommendations.
2. Managing design manufacturing processes The most recognized purpose for DMI is to shorten product development time and time-to- market and reduce manufacturing costs (Burhanuddin and Randhawa, 1992). Evaluation of the effectiveness and efficiency of such a process requires a learned approach (Ball and Butler, 2004).
Technical issues such as manufacturability and the CAD/CAM integration of DMI have been well-studied (Brissaud and Tichkiewitch, 2000; Evans, 1988). Dawson’s study found that innovative design is more effective when technical issues and organizational issues are
IJIS 12,1
112
developed and implemented together (Dawson, 1996). Communication and project management principles that remove departmental barriers have been recommended as key factors for effective DMI management (Coughlan and Wood, 1991; Evans, 1988; Howard et al., 2011). The involvement of manufacturing personnel during the early design phase is considerable for advanced product design (Jang and Schunn, 2012). Standards and procedures are also found to be a helpful mechanism for DMI (Fernandes et al., 2011).
Approaches to determine the efficiency of innovation processes are proposed. Mathematical models, such as the analytic hierarchy process (AHP) and data envelopment analysis (DEA) have been used in evaluating or benchmarking the R&D performance of universities (Feng et al., 2004). However, product innovation in a university is a project- oriented process the effectiveness of which should be individually examined. Organization- wide continuous improvement (CI), as well as concurrent engineering (CE), have been proposed to form cross-functional, cross-layer teams for efficient innovation (Jabnoun, 2001; Shina, 1991; Coughlan and Wood, 1991). A mechanism for inter-organizational coordination and/or communication should be developed for this purpose (Twigg, 2002; Wigand and Frankwick, 1989). The hierarchical modeling of the business process and it is being combined with traditional organizational analysis methods can also generate such a social- mechanism (Haque and Pawar, 2003). In sum, socio-mechanisms, such as cross-function teams, co-location and effective communication positively affect the DMI process (Liker et al., 1999; Kahn and McDonough, 1997). However, very few universities have adopted this process-view R&D management for efficiency and, more importantly, for effectiveness (Winkelman, 2013; Lucero et al., 2014).
In addition to the emphasis on efficiency in prototyping innovative design, a good DMI process may well serve to facilitate organizational creativity. The heterogeneous nature of knowledge between design and engineering not only poses problems but also offers opportunities to generate creative solutions. During prototyping, problems are found, alternative solutions to the problems are generated and evaluated, and the most feasible one is implemented. This creative problem solving involves a two-step process, namely, a divergent (creating ideas) step and a convergent (evaluating ideas) step (Panchal and Szajnfarber, 2017). An empirical study found that the ideation to evaluation ratios vary among professional fields (Figueiredo, 2016). In other words, some professional fields, such as those of professors and researchers, emphasize the problem finding stage, while certain others, e.g. manufacturing production, emphasize the solution implementation stage. Divergent and convergent processes exist in all the three stages of problem finding, solving and implementation. The divergent thinking attitudes of individuals in an organization are found to be related to creative problem solving and should be identified and encouraged (Basadur and Hausdorf, 1996). Investigation of the gap between such theories and practice in an engineering department of a university can be studied to understand the needs of complete engineering education. The investigation should also be able to generate suggestions for improving the innovation process in engineering schools.
A Canadian study showed that R&D management is an important discipline for engineering students and has an impact on national welfare (Clarke, 1993). The successful management of university R&D requires training in the areas of system engineering, project management and technology management (Schoonwinkel and Milne, 1997). Managing organizational issues is more important than managing technical issues. Despite the widespread recognition of this necessity, the managerial approach to effective university research is rarely studied. Regardless of TQM, CI, CE or other practices, larger managerial issues must be addressed and contingency-oriented research is needed to integrate the design-manufacturing process (Swink, 1999).
Cross- functional
perspective
113
3. Research method This study adopts a single case research method and uses the haptic device project conducted by the engineering science department of Simon Fraser University as the basis of its empirical study. This case research approach is designed to answer the research questions proposed in the Introduction above. The research method, following the suggestions by Yin (2003), consists of several steps, namely, theory development, case selection, data collection, data analysis and theory modification.
3.1 Theory development In this research, theoretic propositions are obtained by observing the phenomena occurring in the haptic project. These phenomena are compared with the related literature for the systematic development of propositions.
Departments of different functions are likely to have dissimilar orientations, experiences and interests, therefore, successful cooperation among these departments for new product development is quite challenging. Cognitive bias among the functional departments is one of the barriers that impede the NPD process (Skippari et al., 2017). Disparities among participating personnel in competence and motivation levels are also critical barriers to innovation (Stendahl and Roos, 2008). To be productive, these dissimilar functions should be able to share information and knowledge as a cross-fertilizing interactive process (Avan and Hemant, 2000). However, these heterogeneous characteristics of dissimilar functional personnel also facilitate the innovation process if effective coordination and low boundary conflict are managed (Anthony et al., 2014). With the above literature, the first theoretical proposition is stated below:
P1. The heterogeneous natures of design and manufacturing in a research university hinder, as well as facilitate innovation during the prototyping process. The design organization and the manufacturing organization, although they are within the same university, involve different technological disciplines, educational backgrounds and experience levels. These differences can cause barriers to innovation while, on the other hand, they can also give rise to creative solutions.
While the differences in functional expertise can be viewed as technical, dissimilarities in individual experiences, interests and values are some personal factors influencing the DMI process (Avan and Hemant, 2000). Individuals with multiple knowledge or experience, e.g. R&D and business, are found useful to new product development (Hyung-Jin Park et al., 2009). Leadership and the ability to manage a cross-functional team are also found individual-related factors to innovative product development (Larsen and Lewis, 2007).
Organizational logic is an influencing factor in the success of DMI (Hänninen and Kauranen, 2006). If the organizational culture facilitates cooperation and trust, it is possible to turn technical and personal dissimilarities from barriers to facilitators (Hänninen and Kauranen, 2006; Hernandez-Mogollon et al., 2010). The dynamic between individuals and organizations involved in the DMI can collectively influence the result of innovation (Hueske et al., 2015; Petersson et al., 2017). Based on the above literature, the second theoretical proposition is stated below:
P2. Barriers to and facilitators of innovation in the prototyping process are not confined to the technical domain only. Organizations and persons involved in the prototyping process are determinants of the barriers to and facilitators of innovation. The technical, organizational and personal dimensions should be collectively taken into consideration to improve performance (Linstone, 1999).
IJIS 12,1
114
3.2 Data collection The haptic device program is selected as the case, as the program is chara
Collepals.com Plagiarism Free Papers
Are you looking for custom essay writing service or even dissertation writing services? Just request for our write my paper service, and we'll match you with the best essay writer in your subject! With an exceptional team of professional academic experts in a wide range of subjects, we can guarantee you an unrivaled quality of custom-written papers.
Get ZERO PLAGIARISM, HUMAN WRITTEN ESSAYS
Why Hire Collepals.com writers to do your paper?
Quality- We are experienced and have access to ample research materials.
We write plagiarism Free Content
Confidential- We never share or sell your personal information to third parties.
Support-Chat with us today! We are always waiting to answer all your questions.
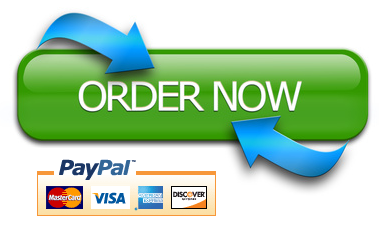