The UTAUT is a model (or theoretical framework) that suggests 4 key constructs (performance expectancy, effort expectancy, social influence, and facilitating conditions) to determine
The UTAUT is a model (or theoretical framework) that suggests 4 key constructs (performance expectancy, effort expectancy, social influence, and facilitating conditions) to determine technology acceptance. This acceptance of technology can be for a single user or organizational-wide. The technology can be an emerging technology, but it can also be an existing technology.
By examining technology acceptance through the use of these constructs in a "real world" environment, researchers and practitioners can assess an individual's intention to use a specific system, thus allowing for the identification of the key influences on acceptance in any given context. This information can be used to inform the development of an implementation plan for the new technology.
Here are some possible emerging technologies to consider (note: feel free to choose an emerging technology from outside this list.
- Cryptocurrency or blockchain (i.e. Bitcoin, Litecoin).
- FinTech (financial technology).
- Cyber analytics – emerging use of analytics to support cybersecurity.
- Artificial Intelligence/machine learning applications in present and near future use.
- Augmented reality/virtual reality applications.
- Biometric advances.
- Wearable technology.
- Other.
Assignment Instructions
Using the study material provided in u03s1 and other resources, choose an emerging technology and submit a 2–3 paper organized around the 4 constructs:
- Performance Expectancy (technology performance).
- Effort Expectancy (ease of use).
- Social Influence (the degree to which an individual perceives that important others believe he or she should use the new system).
- Facilitating Conditions (the degree an individual believes that an organizational and technical infrastructure exists to support the use of the system).
These constructs may also have sub-categories based on gender, age, experience, and voluntariness of use (Venkatesh et al, 2003).
Submit your paper to the assignment area by 11:59 on Sunday of this week.
Assignment Criteria
Your assignment must meet this criteria, please refer to the scoring guide for this assignment.
- Conduct a research activity for selection of an emerging technology.
- Demonstrate knowledge of UTAUT as a theoretical framework for the adoption of an emerging technology.
- Apply the theoretical construct of performance expectancy for emerging technology adoption.
- Apply the theoretical construct of effort expectancy for emerging technology adoption.
- Apply the theoretical construct of social influence for emerging technology adoption.
- Apply the theoretical construct of facilitating conditions for emerging technology adoption.
- Communicate key points in a professional tone in a logical, well-organized manner with credit to external sources that meets the expectations of senior IT leaders.
International Technical Sciences Journal (ITSJ) June 2014 edition Vol.1, No.1
International Technical Sciences Journal
International Technical Sciences Journal (ITSJ) June 2014 edition Vol.1, No.1
International Technical Sciences Journal
(ITSJ)
2014 / June
European Scientific Institute (ESI)
Reviewed by the “International Technical Sciences Journal” editorial board 2014 June 2014 edition vol. 1, no. 1 The contents of this journal do not necessarily reflect the opinion or position of the
European Scientific Institute. Neither the European Scientific Institute nor any
person acting on its behalf is responsible for the use which may be made of the
information in this publication.
International Technical Sciences Journal (ITSJ) June 2014 edition Vol.1, No.1
About The Journal
The International Technical Sciences Journal is a peer – reviewed
international journal which accepts high quality research articles. It is an
annual journal published each June and is available to all researchers who are
interested in publishing their scientific achievements. We welcome
submissions focusing on theories, methods and applications in both articles
and book reviews.
Authors can publish their articles after a review by our editorial board. Our
mission is to provide greater and faster flow of the newest scientific thought.
ITSJ’s role is to be a kind of a bridge between the researchers around the
world. “ITSJ” is opened to any researchers, regardless of their geographical
origin, race, nationality, religion or gender as long as they have an adequate
scientific paper in the field of technical sciences.
Sincerely,
ITSJ Team
International Technical Sciences Journal (ITSJ) June 2014 edition Vol.1, No.1
Table Of Contents: SUSTAINABLE FLY ASH CONCRETE MIXTURES WITH SYNTHETIC FIBERS……………………………………………………..1 Mohammad Alhassan Suleiman Ashur Jerry Brown SURVEILLANCE OF MODERN GASOLINE – ENGINES AND CATALYST BEHAVIOR………………………………………………..10 Periklis G. Chasiotis Panagiotis E. Paroutis COMPARISON OF EXISTING TECHNOLOGY ACCEPTANCE THEORIES AND MODELS TO SUGGEST A WELL IMPROVED THEORY/MODEL…………………………………………………………………………..21 G D M N Samaradiwakara C G Gunawardena TOWARD NEW SOCIAL NETWORK FOR SOLIDARITY…………….37 Malli Mohammad POWER GENERATION METHODS, TECHNIQUES AND ECONOMICAL STRATEGY…………………………………………………………..43 Mansoor-ul-Hassan
International Technical Sciences Journal (ITSJ) June 2014 edition Vol.1, No.1
1
SUSTAINABLE FLY ASH CONCRETE MIXTURES WITH SYNTHETIC FIBERS
Mohammad Alhassan, Associate Prof. of Civil Engineering Suleiman Ashur, Prof. of Civil Engineering
Indiana-Purdue University Fort Wayne (IPFW), Fort Wayne, Indiana, USA Jerry Brown, Field Civil Engineer
Northern Indiana Public Service Company (NIPSCO), Fort Wayne, Indiana, USA
Abstract This study explores the feasibility of replacing large quantities of Portland cement in concrete with Class C fly ash. The influence of structural synthetic fibers on the concrete performance was also explored. A total of 11 fibrous and plain concrete mixtures were designed and evaluated. The results showed that the concrete mixtures with 30% fly ash replacements experience compressive and flexural strengths comparable with companion control mixtures. The compressive and flexural strengths of the mixtures with 60% fly ash replacements were impressive despite the fact that these values are lower than their comparable values in companion control mixtures. The results revealed that replacing up to 60% of the cement in concrete with Class C fly ash is still feasible. The added fibers resulted in significant post- cracking residual strength and reduction in the drying shrinkage. Adding 5 lb/yd3 (3 kg/m3) of the structural synthetic fibers to the mix resulted in about 150 psi (1.0 MPa) residual strength compared with about 80 psi (0.55 MPa) for 3 lb/yd3 (1.8 kg/m3) of synthetic fibers. It was interestingly found that for the used water to cementitious materials (W/CM) ratio of 0.40, the mixtures with total CM of 650 lb/yd3 (390 kg/m3) experienced comparable performance as the mixtures with 750 lb/yd3 (450 kg/m3).
Keywords: Sustainability, Fly ash, Synthetic fibers, Shrinkage, Toughness Introduction: Fly ash is a byproduct of coal consumption and typically used in concrete to replace portion of the cement. Production of cement contributes about 4% to the total CO2 released to the environment. Replacing substantial portion of the cement in concrete with fly ash is considered a sustainable and economical application since it: 1) reduces the impact of coal production and
International Technical Sciences Journal (ITSJ) June 2014 edition Vol.1, No.1
2
CO2 emission on the environment when manufacturing cement; 2) cuts on the amount of fly ash that goes to landfills; and also 3) lowers the concrete cost by reducing the amount of cement needed. On the other hand, incorporating structural synthetic fibers into concrete enhances its structural performance and increases its durability through minimizing the potential for shrinkage cracking and providing crack-arresting mechanism (Alhassan and Ashur, 2012 and 2011, Alhassan 2010, and Issa et al., 208). The enhanced performance combined with the cost reduction and minimized environmental impact are highly desirable for the infrastructure facilities such as highway pavements and bridge decks. These facilities often experience immature cracking and deterioration due to their large surface area that is exposed to the environment and to the effects of cyclic traffic loading conditions.
The use of large quantities of fly ash in concrete has some concerns, especially in terms of the early age strength gain. There is a general notion that fly ash reduces the strength gain at early age. Nevertheless, previous experience with concrete mixtures having 25% fly ash of the total cementitious materials (CM) content showed no such concern about the early age strength (Alhassan and Ashur, 2012 and 2011). Additional research is needed to investigate the effect of using high quantities of fly ash in concrete. On the other hand, incorporating synthetic fibers in fly ash concrete is pioneering since fly ash concrete is typically used in highway structures that experience aggressive environmental exposures, high drying shrinkage, and heavy live loading and impact. Synthetic fibers are noncorrosive, alkali resistant, and typically added in small quantities due to their low density, therefore, a substantial number of uniformly distributed fibers are added.
This study is conducted to obtain reliable experimental results about key- aspects of the performance of fibrous fly ash concrete in terms of strength, shrinkage, toughness, and constructability. It is expected that the availability of such data be of significant interest to many U.S. transportation agencies and researchers. This area of research is fundamental in terms of using special types of fibers and high percentages of fly ash to produce durable sustainable concrete with high resistant to cracking. Such high performance concrete mixtures are in need in many applications. For example, there are major cracking and deterioration problems in the highway pavements and infrastructure systems way before they reach their service lives due to the use of inadequate mix designs and inappropriate construction practices (Soroushian and Ravanbakhsh, 1998 and Ozyildirim et al., 1997). Extending the durability of such systems provides huge life cycle cost savings due to the huge cost of repair. Infrastructure systems with enhanced performance are safer and provide better riding quality.
International Technical Sciences Journal (ITSJ) June 2014 edition Vol.1, No.1
3
Mix Designs and Parameters of Investigation: A total of 11 concrete mixtures were designed to investigate the
influence of major parameters on their performance mainly in terms of strength, shrinkage, and toughness. The mixtures were designed to allow for studying the effects of three major parameters as outlined in Table 1. The studied parameters are: 1) the fly ash content: 0, 30%, and 60% of the total CM content, 2) the fiber content: 0, 3 lb/yd3 (1.8 kg/m3), and 5 lb/yd3 (3 kg/m3), and 3) the total CM content: 650 lb/yd3 (390 kg/m3) and 750 lb/yd3 (450 kg/m3). The W/CM ratio was fixed at 0.40 for all mixtures. The coarse and fine aggregate contents were comparable for all mixtures. The mixing, finishing, curing, and testing practices were consistent for all mixtures and conducted according to the American Society of Testing and Materials (ASTM) standards. Similar dosages of superplasticizer and air-entraining admixtures were added for all mixtures to achieve comparable workability and air content values. The slump values ranged from 6 – 8 in. (150 – 200 mm), the air content values ranged around 6 ± 1%, and the unit weight was around 146 lb/ft3 (2370 kg/m3) for all mixtures. The specimens were covered with wet burlap and plastic sheets for 24 hours before being demolded and moist-cured in a standard moisture room for seven days.
The synthetic fiber type and dosage were selected so that notable performance enhancement is achieved while maintaining adequate constructability. The used fiber type is a 1.55 in. (40 mm) long polyolefin fiber with monofilament configuration and has aspect ration of 90, specific gravity of 0.92, elastic modulus of 1,378 ksi (9.5 GPa), tensile strength of 90 ksi (620 MPa), and high alkali, acid, and salt resistant. The constructability aspects of the fibrous mixtures were monitored during the fresh concrete state to evaluate whether the fibers jeopardize the mixing or the finishing practices. Within the used fiber types and dosages, the fibrous mixtures had a reduction in the slump of about 1-2 in. (25-50 mm) compared with the companion plain mixtures. The mixtures with 3 lb/yd3 (1.8 kg/m3) of fibers were easily constructable while the mixtures with 5 lb/yd3 (3 kg/m3) required some precaution to avoid complications during mixing, compacting, and finishing such as fiber remains in the mixer, clumps, and balling.
Table 1 Mix Designs and Parameters of Investigation
Ingredient Quantity, lb/yd3
Mix 1
Mix 2
Mix 3
Mix 4
Mix 5
Mix 6
Mix 7
Mix 8
Mix 9
Mix 10
Mix 11
Total CM 650 750 650 650 650 650 650 650 750 750 750 Type I cement 650 750 455 455 455 260 260 260 300 300 300 Class C fly ash 0 0 195 195 195 390 390 390 450 450 450 % Fly ash 0 0 30% 30% 30% 60% 60% 60% 60% 60% 60%
International Technical Sciences Journal (ITSJ) June 2014 edition Vol.1, No.1
4
Course t
1,620 1,520 1,600 1,600 1,600 1,590 1,590 1,590 1,490 1,490 1,490 Fine aggregate 1,620 1,520 1,600 1,600 1,600 1,590 1,590 1,590 1,490 1,490 1,490 W/CM 0.40 0.40 0.40 0.40 0.40 0.40 0.40 0.40 0.40 0.40 0.40 Synthetic fiber 0 0 0 3 5 0 3 5 0 3 5
* 1.0 lb/yd3 = 0.601 kg/m3 Compression tests were conducted for all mixtures at 7 and 28 days
according to ASTM C39. Flexural performance tests were conducted at 90 days according to ASTM C 1609. A digitally controlled universal testing machine was used to test the compressive strength and the flexural performance. Unrestrained drying shrinkage tests were conducted for each mixture according to ASTM C157. The shrinkage measurements were taken over a 90 period. The average results are presented in the following sections. The results were then analyzed to evaluate the effects of the three major parameters of investigation of this study.
The plain mixtures Mix 3 and Mix 6 have 30% and 60% fly ash, respectively with a total CM content equivalent to the plain mixture Mix 1 that does not include fly ash. The plain mixture Mix 9 has 60% fly ash with a total CM content equivalent to the plain mixture Mix 2 that does not include any fly ash. Therefore, the effect of the fly ash content can be evaluated through comparing the results of Mix 3 and Mix 6 with Mix 1 as well as Mix 9 with Mix 2. The effect of the fiber content can be evaluated through comparing the results of the fibrous mixtures Mix 4 and Mix 5 with the plain mixture Mix 3, the fibrous mixtures Mix 7 and Mix 8 with the plain mixture Mix 6, and the fibrous mixtures Mix 10 and Mix 11 with the plain mixture Mix 9. The effect of the total CM content can be evaluated through comparing the results of Mix 1 with Mix 2 and Mix 6 with Mix 9. Compressive Strength:
Figure 1 shows the average compression test results at 7 and 28 days. The compressive strengths of Mix 3 and Mix 6 were lower than Mix 1 by 13.7% and 31.4% at 7 days and 6.9% and 17.1% at 28 days, respectively. The compressive strength of Mix 9 was 34.1% and 13.5% lower than Mix 2 at 7 and 28 days, respectively. In spite of the reduction in the compressive strength when replacing the cement with 30% and 60% fly ash, Mix 3 that includes 30% fly ash achieved a compressive strength greater than 4000 psi (28 MPa) at 7 days and greater than 6000 (41 MPa) at 28 days. Mix 6 and Mix 9 that include 60% fly ash both achieved about 3500 psi (24 MPa) at 7 days, and about 5500 (38 MPa) and 6000 psi (41 MPa) at 28 days, respectively. The compressive strength development was better for the mixtures with the fly ash compared with the mixtures without fly ash.
International Technical Sciences Journal (ITSJ) June 2014 edition Vol.1, No.1
5
Comparing the results of the fibrous mixtures that have 3 lb/yd3 (1.8 kg/m3) fibers with their control plain mixtures shows that the compressive strength of Mix 4 is 23.4% and 21.8% higher than Mix 3 at 7 and 28 days, respectively. The compressive strength of Mix 7 is 12.7% lower than Mix 6 at 7 days and 3.6% higher at 28 days. The compressive strength of Mix 10 is 3.1% higher than Mix 9 at 7 days and 2.3% lower at 28 days. Comparing the results of the fibrous mixtures that have 5 lb/yd3 (3.0 kg/m3) fibers with their control plain mixtures shows that the compressive strength of Mix 5 is 3.1% higher than Mix 3 both at 7 and 28 days. The compressive strength of Mix 8 is 7.2% lower than Mix 6 at 7 days and 2.2% higher at 28 days. The compressive strength of Mix 11 is 11.1% and 17.9% lower than Mix 9 at 7 and 28 days, respectively. The fibrous mixtures with 3 lb/yd3 (1.8 kg/m3) experienced higher strength than the companion fibrous mixtures with 5 lb/yd3 (3.0 kg/m3). The results do not show a general trend on whether the fibers increase or decrease the compressive strength; however, addition of fibers to concrete was never intended to increase its compressive strength. The failure modes of the compression test specimens revealed significant advantage for the fibrous additives. The fibrous specimens remained intact after failure due to the internal confinement provided by the fibers, while the plain specimens crushed at ultimate.
Figure 1 Compressive strengths at 7 and 28 days (1000 psi = 6.895 MPa).
Comparing the compressive strength of Mix 1 with Mix 2 shows that
Mix 1 experienced approximately similar compressive strengths at 7 and 28 days as Mix 2 although Mix 1 has 13% less cement. Mix 6 also has 13% lower cement than Mix 9, and experienced almost similar compressive
International Technical Sciences Journal (ITSJ) June 2014 edition Vol.1, No.1
6
strength as Mix 9 at 7 days and just 5% less at 28 days. These results are very interesting and reveal that for a W/CM of 0.40, the use of 650 lb/yd3 (390 kg/m3) of CM in concrete results in almost similar compressive strength as the use of 750 lb/yd3 (450 kg/m3) of CM. One of the reasons might be that the course aggregate content in the mixtures with 650 lb/yd3 (390 kg/m3) of CM is around 6% higher than the mixtures with 750 lb/yd3 (450 kg/m3). Shrinkage:
The drying shrinkage measurements were taken for each mixture over a 90-day period following 7-days of moist curing. The shrinkage-time responses were plotted for the companion mixtures as shown in Figure 2 to allow for clear analysis of the results. It is important to recall that all mixtures have the same W/CM ratio. Comparing Mix 1 with Mix 2 shrinkage results shows that Mix 2 experienced slightly higher shrinkage, which can be attributed to its higher CM content. Comparison between Mix 1, Mix 3, and Mix 6 shows that Mix 6 that has 60% fly ash experienced almost similar shrinkage as Mix 1, while Mix 3 that has 30% fly ash experienced noticeably higher shrinkage that Mix 1 and Mix 6. Comparing Mix 9 that has 60% fly ash with Mix 2 shows that Mix 9 experienced slightly lower shrinkage.
The effect of the fibers on the shrinkage is evaluated through comparing Mix 4 and Mix 5 with Mix 3, Mix 7 and Mix 8 with Mix 6 and Mix 10 and 11 with Mix 9. Inspection of the plots shown in Figure 2 shows that the fibrous mixtures experienced lower shrinkage than the companion plain mixtures. The fibrous mixtures with 3 lb/yd3 (1.8 kg/m3) experienced almost similar shrinkage as the companion fibrous mixtures with 5 lb/yd3 (3.0 kg/m3). At 28 days, the average shrinkage of Mix 4 and Mix 5 was about 18% lower than Mix 1, the average shrinkage of Mix 7 and Mix 8 was about 15% lower than Mix 6, and the average shrinkage of Mix 10 and Mix 11 was about 13% lower than Mix 9. These results show that the used dosages of the structural synthetic fibers resulted in significant reduction in the drying shrinkage of concrete. This is considered a desirable enhancement in the concrete performance increases resistant to cracking.
International Technical Sciences Journal (ITSJ) June 2014 edition Vol.1, No.1
7
Figure 2 Shrinkage-time responses.
Flexural Performance:
Toughness and post-cracking residual strength evaluation were conducted for the fibrous mixtures according to ASTM C1609 using a servo- controlled testing machine. All specimens were tested at age of 90 days. Figure 3 shows the ultimate flexural strengths and the post-cracking and residual strengths (f D150) for each mixture as obtained from the flexural performance tests. The obtained results are the average of two to three specimens. As expected, all the plain mixtures failed suddenly without any residual strength after reaching the ultimate flexural strength. This is the major reason for adding fibers to concrete that is to arrest cracks at any location where the ultimate tensile strength is reached.
International Technical Sciences Journal (ITSJ) June 2014 edition Vol.1, No.1
8
The residual strengths of Mix 4, Mix 7, and Mix 10 that include 3 lb/yd3 (1.8 kg/m3) of fibers were respectively 80 psi (0.55 MPa), 75 psi (0.52 MPa), and 80 ksi (0.55 MPa) with an average of 78 psi (0.54 MPa), which is about 11% of the average flexural strength of the previous three fibrous mixtures that is 727 psi. The residual strengths of Mix 5, Mix 8, and Mix 11 that include 5 lb/yd3 (3 kg/m3) of fibers were respectively 160 psi (1.1 MPa), 120 psi (0.83 MPa), and 190 ksi (1.3 MPa) with an average of 157 psi (1.1 MPa), which is about 21% of the average flexural strength of the previous three fibrous mixtures that is 735 psi (5.1 MPa). The results also show that the fibrous additives do not affect the flexural strength for the two used dosages of the synthetic fibers. Some fibrous mixtures experienced slightly higher flexural strengths than the companion plain mixtures, while others experienced slightly lower flexural strengths.
In terms of the influence of the total CM on the flexural strength, Mix 1 and Mix 2 almost experienced similar flexural strengths. Also Mix 6 and Mix 7 experienced almost similar flexural strengths. These interesting results were consistent with the compressive strength results for the same mixtures indicating that for W/CM = 0.40, the use of 650 lb/yd3 (390 kg/m3) of CM in concrete results in almost similar flexural and compressive strengths as the use of 750 lb/yd3 (450 kg/m3) of CM. In terms of the influence of the fly ash content on the flexural strength, Mix 3 that has 30% fly ash experienced higher flexural strength than Mix 1 by 8%, which is impressive. Mix 6 that has 60% fly ash experienced lower flexural strength than Mix 1 by 14.6%, and also Mix 9 that has 60% fly ash experienced 13.8% lower flexural strength than Mix 2. In spite of the reduction in the flexural strength when replacing the cement with 60% fly ash, Mix 6 and Mix 9 both achieved flexural strength above 650 psi (4.5 MPa).
Figure 3 Flexural and residual strengths (1000 psi = 6.895 MPa).
International Technical Sciences Journal (ITSJ) June 2014 edition Vol.1, No.1
9
Conclusion: Based on the results, it can be concluded that replacement of 60% of
cement in concrete with Class C fly ash is a feasible-sustainable measure resulting in large savings in the cost of concrete, lowering CO2 emission, and recycling effectively coal-consumption byproduct. The compressive and flexural strengths of the mixtures with 60% fly ash replacements were impressive, but lower than the companion mixtures. Replacement of 30% of the cement with Class C fly ash results in nearly comparable performance characteristics. Addition of 5 lb/yd3 (3 kg/m3) of the structural synthetic fibers to concrete results in about 150 psi (1.0 MPa) residual strength; while addition of 3 lb/yd3 (1.8 kg/m3) results in about 80 psi (1.0 MPa) residual strength. For similar W/CM of 0.40, the mixtures with total CM of 650 lb/yd3 (390 kg/m3) experienced comparable performance as the mixtures with 750 lb/yd3 (450 kg/m3). References: Mohammad Alhassan and Suleiman Ashur. Superiority & Constructability of Fibrous Additives for Bridge Deck Concrete Overlays. Research Report FHWA-ICT-12-003: Illinois Center for Transportation, June 2012. Mohammad Alhassan and Suleiman Ashur. Sustainable Fly Ash Concrete Overlay Mixture for Preserving Bridge Decks. Journal of the Chinese Ceramic Society (JCCS): Vol. 39, No. 10, October 2011, pp. 77-83. Mohammad Alhassan. Shrinkage-Time Responses of Bridge Deck Overlay Mixtures with Fibrous Additives. Journal of the Chinese Ceramic Society (JCCS): Vol. 38, No. 9, 2010, pp. 1638-1644. Mohsen Issa, Mohammad Alhassan, and Hameed Shabila. High Performance Plain and Fibrous Latex-Modified and Micro-Silica Concrete Overlays. ASCE Journal of Materials Engineering: Vol. 20, No. 12, December 2008, pp. 472-753. Soroushian, P. and Ravanbakhsh, S. Control of Plastic Shrinkage Cracking with Specialty Cellulose Fibers. ACI Materials Journal: Vol. 95, No. 4, 1998, pp. 429-435. Ozyildirim, C., Moen, C., and Haldky, S. Investigation of Fiber Reinforced Concrete for Use in Transportation Structures. Journal of the Transportation Research Board (TRB): Vo. 1574, 1997, pp. 63-70. Voigt, G.F. Early Cracking Of Concrete Pavement-Causes and Repairs. Presented at the 2002 Technology Transfer Conference-Federal Aviation Administration Airport: May 2002. American Society for Testing and Materials (ASTM). Construction Concrete and Aggregates: Section 4, Vol. 04.02, ASTM Annual Book of Standards, Philadelphia, 2008.
International Technical Sciences Journal (ITSJ) June 2014 edition Vol.1, No.1
10
SURVEILLANCE OF MODERN GASOLINE – ENGINES AND CATALYST BEHAVIOR
Periklis G. Chasiotis, Associate Prof. Technological Educational Institute (TEI) of Thessaly, Greece
Panagiotis E. Paroutis Graduate Technological Educational Institute (TEI) of Thessaly, Greece
Abstract In the last two decades an integral and continuous development of the two most important engine systems, i.e. the mixture preparation system and the ignition system, was achieved. This development is due to several factors such as to minimize the exhaust emissions, to reduce the fuel consumption, to increase the intervals between successive engine services, and to insure an easy motor operation into these intervals. Furthermore, a significant improvement of the driving system in order to better drivability and regular car kinematic was obtained. Therefore, a full diagnosis of the operation condition of all new engine systems isnecessary to prevent their possible malfunction or to restore them in the case of damages. In the course of modern engines diagnosis, measurements were taken on a Matiz Daewoo car which belongs to the Internal Combustion Engines laboratory of the Dept. of Mechanical Engineering TE, TEI of Thessaly, by using of an appropriate control program. The influence of transient load condition to the catalyst behavior also was studied and the response of the λ-sensors signals was explained.
Keywords: Gasoline, engines HISTORICAL The application and the evolution of the On Board Diagnosis system (OBD) is due to the so called main USA Organizations :
a. The California Air Resourse Board – CARB and b. The California Air Protection Agency – CAL EPA
The CAL EPA restrictions and his policy enforcement have given the possibility to the CARB to apply air quality programs which were used as a direction for likely legislation in several countries, even the EU. OBD I system has been applied in California since 1988. In accordance to this simple system the mission of the Engine Control Unit
International Technical Sciences Journal (ITSJ) June 2014 edition Vol.1, No.1
11
(ECU) was the surveillance of the motor systems affecting the exhaust emissions and the creation of an optical warning signal, when an engine malfunction occurred. This signal was produced either from a LED lamp upon the ECU or from a Malfunction Indicator Lamp (MIL) on the driving board. According to the OBD I system only the λ–sensor, the EGR system, the fuel system and the ECU was supervised. The most important two disantvages of the OBD I system were: 1. MIL activation occurred only after an engine damage, without any possibility of searching a malfunction in progress so as to prevent a total engine system destruction. 2. There were not provided any formality instructions between manufacturers. Since 1996, the OBD II engine surveillance system has been applied in the whole USA. According to the OBD II system MIL is activated at any time as the CO, HC and NOx emissions exceed over 50% the Federal Test Procedure (FTP) standards depended on year model. These errors might result due to the following factors: 1. Random abnormal ignitions which cause increase in HC emission 2. Catalyst efficiency reduction 3. Air leak into fuel supplying and/or fuel distribution system 4. Defective sensor The driver is responsible for immediate system malfunction check and repair. In other case, when the car is checked, a tester could be used to read out and display the stored malfunctions, even the total emissions not exceed the acceptable mandated standards and thereafter a penalty could be inflicted. The second significant improvement of the OBD II system against OBD I system is the fact that specific standards for all manufacturers and all models have been legislated : 1. 16-pin Data Link Connector – DLC, Figure 1 2. Electronic protocols 3. Detection Troubles Codes (DTC) 4. Terminology
Figure 1 : 16-pin data link connector
International Technical Sciences Journal (ITSJ) June 2014 edition Vol.1, No.1
12
The OBD II Diagnosis system also includes a truly most unfolded management system improved up today. This logistic comprises : 1. Two lambda oxygen sensors (λ–sensor), usually heated, upstream and downstream of the catalytic converter (HO2S). 2. More powerfull Electronic Control Module (ECM) with Electronic Erased Programmized Read Only Memory (EEPROM) which permits the ECM to be reprogrammized with the latest logistic improvement. 3. Evaporative emissions control system with activated charcoal filter. 4. Exhaust Gas Recirculation system (EGR). 5. Serial fuel injection system instead of the Multi–Point Injection system (MPI) or the Mono–Jetronic system. 6. Manifold Absolute Pressure sensor (MAP) and Mass Air Flow sensor (MAF) to engine load monitoring. 7. Cut–off engine operation calculated from throttle valve position, engine speed and cool water temperature. Since June 1994, SAE
Collepals.com Plagiarism Free Papers
Are you looking for custom essay writing service or even dissertation writing services? Just request for our write my paper service, and we'll match you with the best essay writer in your subject! With an exceptional team of professional academic experts in a wide range of subjects, we can guarantee you an unrivaled quality of custom-written papers.
Get ZERO PLAGIARISM, HUMAN WRITTEN ESSAYS
Why Hire Collepals.com writers to do your paper?
Quality- We are experienced and have access to ample research materials.
We write plagiarism Free Content
Confidential- We never share or sell your personal information to third parties.
Support-Chat with us today! We are always waiting to answer all your questions.
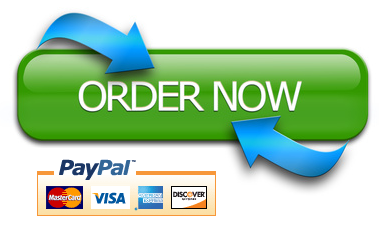