The business is a 3D printing company specializing in assistive and accessibility devices. The owner, Mark Peterson, started the business as a hobby using a single 3D printer in his home. Ho
I am attaching the stage 1 and 2. Based on 1 and 2 you have to complete 3 and 4. Please dont copy from any other place. The citation must be in APA style. I need the original work.
Requirements: It shoulld answer all the question or complete the requirement.
IFSM 310 3D Printing Stage 1
Students Name
Instructors Name
Course Title
Date
Background
The business is a 3D printing company specializing in assistive and accessibility devices. The owner, Mark Peterson, started the business as a hobby using a single 3D printer in his home. However, as demand for his products grew, he expanded his operation to an industrial park, rented additional space, and purchased more printers (3D Printing Case Study IFSM 310, 2016). He plans to add seven more 3D printers and a 3D scanner and hire five full-time employees. To manage his growing business more effectively, Mark wants to implement a small business enterprise resource management (ERP) information system and set up his IT infrastructure to support his production and management needs (3D Printing Case Study IFSM 310., 2016). He also wants to ensure that his employees have mobile access to the ERP system and the 3D printers and that there is flexibility in how the computers control the printers.
Current Infrastructure
Based on the information provided in the case study, Mark currently has the following IT infrastructure components in place:
Hardware:
3D printer (1)
PC (1)
Software:
3D design software (unspecified)
Spreadsheet software (unspecified)
Google email
Network:
The Verizon FiOS modem has a built-in wireless router (3D Printing Case Study IFSM 310, 2016).
Requirements
Here are five requirements that Mark has identified that the new IT infrastructure will have to perform or support as he expands his business:
Manage customer orders, invoices, and supply ordering more effectively through a small business enterprise resource management (ERP) system (3D Printing Case Study IFSM 310, 2016).
Provide mobile access to the ERP system and 3D printers to all employees anywhere in the facility.
Allow flexibility in which computers control which 3D printers.
Store the facility’s 3D production files and business management information locally and use cloud storage for backup files.
Provide training videos for new employees to learn 3D printing and business management processes (3D Printing Case Study IFSM 310, 2016).
How will the requirements be met?
Mark must implement an ERP software solution to manage customer orders, invoices, and supply ordering more effectively through a small business enterprise resource management (ERP) system. The software must include inventory, purchasing, accounting, and customer relationship management (CRM) modules. Mark must also acquire a dedicated server to host the ERP system or subscribe to a cloud-based ERP service.
To provide mobile access to the ERP system and 3D printers to all employees from anywhere in the facility, Mark must set up a wireless network infrastructure that supports mobile devices. According to Hedge et al. (2021), this will require additional wireless access points and a secure authentication and authorization mechanism such as Wi-Fi Protected Access II (WPA2) or 802.1X. The ERP software will also need a web-based interface or mobile app accessed from smartphones or tablets.
To allow flexibility in which computers control which 3D printers, Mark must set up a networked 3D printing infrastructure using 3D printing management software. The software will allow Mark to queue up print jobs and assign them to specific 3D printers from any computer in the facility. Mark will also need to ensure that the network can handle the increased traffic and bandwidth demands of multiple 3D printers.
To store 3D production files and business management information locally in the facility and use cloud storage for backup files, Mark will need to set up a file server or Network-Attached Storage (NAS) device to store and share files among the employees (Tasnim et al., 2022). Mark can also subscribe to a cloud storage service such as Amazon S3 or Dropbox for backing up files and data. Mark should also implement a backup and disaster recovery plan to ensure data security, including regular backups and offsite storage.
To provide training videos for new employees to learn 3D printing and business management processes, Mark can use video conferencing software such as Zoom or Skype or set up an internal video hosting platform using open-source software. Mark can also use online learning platforms such as Udemy to provide structured training courses for his employees.
Data Representation and Storage
a. Digital and numerical data:
Digital and numerical data are represented in binary form (0s and 1s) in digital systems. Data is usually stored in files the system can access and process in computing. Mark can use his PC’s hard drive to store digital and numerical data in spreadsheets, text documents, and databases. These files can also be stored on a network-attached storage (NAS) device, a specialized file server that allows multiple users to access files and folders from a central location (Ng et al., 2020). Mark can use cloud-based storage solutions, such as Google Drive or Dropbox, to store and access digital and numerical data from anywhere with an internet connection. These cloud-based storage solutions offer a range of storage options, from free plans to enterprise-level plans with larger storage capacities. Mark should also consider implementing a backup strategy for his digital and numerical data to ensure its safety and availability in case of hardware failure, cyber-attacks, or accidental deletion. He can use external hard drives or cloud-based backup solutions like Backblaze or Carbonite to create regular data backups.
b. Audio data:
Audio data is represented in digital form as a sequence of binary values that represent the amplitude of the sound wave at regular intervals. In other words, the digital data represents a series of samples of the analog sound wave. Mark can store audio data in various formats, such as WAV, MP3, and FLAC (Baloch et al., 2021). He can use his PC’s hard drive to store audio files, an external hard drive, or a NAS device for more storage capacity. In addition to storage, Mark will need appropriate software to play, edit, and record audio data. For example, he can use a media player such as Windows Media Player or iTunes to play audio files on his PC. For editing and recording, he can use digital audio workstation (DAW) software such as Audacity or Pro Tools (Baloch et al., 2021). If he needs to stream audio data over the internet, he can use streaming media software such as Icecast or Shoutcast.
c. Video data: Video data is represented in digital form as a sequence of images (frames) displayed rapidly to create the illusion of motion. Each frame is represented by a series of binary values that represent the color and brightness of each pixel in the frame. Mark can store video data in various formats, such as MP4, AVI, and MKV. He can use his PC’s hard drive to store video files or use an external hard drive or a NAS device for more storage capacity (Sadeghi et al., 2020). Mark can also consider using a dedicated video storage system such as a digital video recorder (DVR) or a network video recorder (NVR) for storing large amounts of video data. These systems are designed to handle video data more efficiently and securely than a regular PC or hard drive. They also provide features such as remote access, video analytics, and data redundancy for backup and recovery.
d. Graphics data: Graphics data is represented in digital form as a collection of binary values representing each pixel’s color and brightness. Mark can store graphics data in various formats such as JPEG, PNG, and BMP. He can use his PC’s hard drive to store graphics files, an external hard drive, or a NAS device for more storage capacity. Mark can also use a dedicated graphics card on his PC or a graphics processing unit (GPU) for faster rendering of graphics-intensive applications.
References
3D Printing Case Study IFSM 310. (2016)
Baloch, J. A., Jumani, A. K., Laghari, A. A., Estrela, V. V., & Lopes, R. T. (2021). A Preliminary Study on Quality of Experience Assessment of Compressed Audio File Format. In?2021 IEEE URUCON?(pp. 161-165). IEEE.
Hegde, S. B., Ranjan, A., Raj, A., Paul, K., & Santra, S. (2021, December). Wpa2-based wireless enterprise configuration. In 2021 IEEE International Conference on Mobile Networks and Wireless Communications (ICMNWC)?(pp. 1-8). IEEE.
Ng, Q. A., Loo, N. L., Chiew, Y. S., Tan, C. P., Ralib, A. M., & Nor, M. B. M. (2020). Mechanical ventilation monitoring: development of a network data acquisition system.?IFAC-PapersOnLine,?53(2), 15916-15921.
Sadeghi, N., Fahiminia, M., & Teimouri, M. (2020). Dataset for file fragment classification of video file formats.?BMC Research Notes,?13(1), 1-3.
Tasnim, R., Mim, A. A., Mim, S. H., Jabiullah, P. D., & Ismail, M. (2022). A Comparative Study On Three Selective Cloud Providers.?arXiv preprint arXiv:2208.14482.
3D Printing Case Study IFSM 310 10/28/2016 3D Printing Case Study In late 2015, Mark Peterson acquired a 3D printer from Best Buy for $500. As he began to play around with it, he discovered that he could use designs he downloaded from the Internet to create a wide variety of objects. One day as he was exploring designs on the website MyMiniFactory.com (https://www.myminifactory.com/), he came across a category of accessibility items. He was very excited to discover such things as an umbrella holder for a wheelchair, because his brother Peter uses a wheelchair for mobility. He downloaded the umbrella holder design and made one for Peter. The first time Peter used the umbrella holder, several people came up and asked him where he had gotten it. Of course, he was proud to say his brother had made it, but he had no idea how much it would cost for Mark to make one for a customer. Peter took the names and phone numbers of two people he encountered and promised to get back to them. When Peter approached Mark with the requests, Mark knew that he had found the start of something good. He figured out what the time and material cost would be to make the holders, called the interested parties, and made his first two sales. As he continued exploring, Mark ran across an article describing ten 3D printable assistive and accessibility devices (https://3dprint.com/126214/103dp-devices-for-the-disabled/). After investing in a heavy duty 3D printer, Mark used his Facebook page to advertise his growing business in 3D printing assistive and accessibility devices. He soon had many orders and his 3D printing hobby became his fulltime occupation. Mark rented space in an industrial park, bought two more wireless 3D printers, and hired two part-time assistants. He brought his PC from home to control the 3D printers, and set up an Internet connection using Verizon FiOS. His PC is connected to a FiOS modem which has a built-in wireless router. Mark obtains his 3D printing designs from sources on the internet. He uses Google email and keeps track of his orders on a spreadsheet on his PC. Mark’s Expansion Plan: Now, just three months later, he is ready to add seven more 3D printers and a 3D scanner, and hire five fulltime employees. Before he grows that much, he needs to set up his IT infrastructure to manage not only the additional 3D printers, but also to manage his business. He wants to implement a small business enterprise resource management (ERP) information system in his facility to help him manage his business (customer orders, invoices, supply ordering, employees, etc.) more effectively. He realizes he will also need a document printer to print invoices, etc. In addition, he wants each of his employees to have mobile access to the ERP system and the 3D design files and printers from anywhere in the facility, and he wants as much flexibility in which computers control which 3D printers as possible. He has a large collection of 3D print design files and has downloaded some training videos that he will use to train his new employees. Mark has already decided that he wants to store all of his 3D production files and his business management information locally in his facility, and to use cloud storage for his backup files. Your assignment, which will be done in four stages, is to assist Mark in understanding what kind of infrastructure he needs; how it would be configured; how it will change when his business grows into a much larger, multi-location operation; and how the various devices communicate with each other. Specific instructions for each of the four staged assignments may be found under the Assignments tab.
IFSM 310 3D Printing Stage 2
Students Name
Instructors Name
Course Title
Date
Part 1
a. Components needed for the computer system(s) to create 3D printed items:
3D Printer: This is the primary hardware component for creating 3D-printed items. Depending on his production requirements, Mark will need to purchase one or more 3D printers.
Computer Workstations: Mark will need desktop or laptop computers with sufficient processing power and memory to run 3D modeling and slicing software. These computers will be connected to the 3D printers through a wired or wireless network.
3D Modeling Software: This software is used to design and create 3D models of the objects to be printed. Mark must purchase or subscribe to 3D modeling software such as SketchUp, Fusion 360, or Tinkercad.
Slicing Software: Once the 3D model is created, it needs to be sliced into layers and converted into a format that the 3D printer can read. Slicing software such as Cura or Slic3r is used for this purpose.
Filament: Filament is the raw material used for 3D printing. Mark will need to purchase filaments of various colors and types depending on his production requirements.
Storage Devices: Mark must store 3D models, slicing profiles, and other related files. He can use external hard drives, USB drives, or cloud-based storage solutions like Google Drive or Dropbox.
b. Components needed for the small business enterprise resource management (ERP) information system:
ERP Software: Mark must purchase or subscribe to an ERP system that meets his business requirements. Beric et al. (2020) offer that some popular ERP software options for small businesses include NetSuite, Sage Intacct, and Acumatica.
Computer Workstations: Mark will need desktop or laptop computers with sufficient processing power and memory to run the ERP software (3D Printing Case Study IFSM 310, 2016). These computers will be connected to the ERP server through a wired or wireless network.
Server: Mark will need a server to run the ERP software and store the database. He can purchase a physical server or use a cloud-based solution such as AWS or Azure.
Database Management System (DBMS): A DBMS such as Oracle or Microsoft SQL Server will be required to manage the ERP database.
Inventory Management System: The ERP software should have an inventory management module to keep track of the inventory of supplies and products.
Customer Relationship Management (CRM) System: The ERP software should have a CRM module to manage customer orders, sales, and other related information.
Payroll and HR Management System: The ERP software should have a module to manage employee records, payroll information, and other HR-related tasks.
Financial Management System: The ERP software should have a financial management module to manage accounting, billing, invoicing, and other financial tasks.
c. The 3D computer system, the ERP information system, and the communication networks supporting both systems must work together to provide Mark with all the IT capability he needs to run his business. The 3D computer system will create 3D printed items, while the ERP information system will manage customer orders, supplies, employees, and financial records (Kenge & Khan, 2020). The communication networks, including the wired and wireless networks, will connect the computers and devices used in both systems. The ERP software will integrate with the 3D computer system to manage the inventory of supplies and finished products. The ERP system will also integrate with the customer orders received through email and telephone, and the financial records will be automatically updated as transactions occur (Kenge & Khan, 2020). Finally, employees can access the 3D computer system through mobile devices, which will be connected to the wireless network. The diagram will show how these components are connected and located within Mark’s facility.
Part 2
References
3D Printing Case Study IFSM 310. (2016)
Beric, D., Havzi, S., Lolic, T., Simeunovic, N., & Stefanovic, D. (2020). Development of the MES software and Integration with an existing ERP Software in Industrial Enterprise. In?2020 19th International Symposium INFOTEH-JAHORINA (INFOTEH)?(pp. 1-6). IEEE.
Kenge, R., & Khan, Z. (2020). A research study on the ERP system implementation and current trends in ERP.?Shanlax International Journal of Management,?8(2), 34-39.
IFSM 310 3D Printing Stage 3 Assignment
Before you begin this assignment, be sure you:
Have completed all previously assigned readings.
Read the ??3D Printing Case Study.”
Reviewed the feedback on your 3D Printing Stage 1 and Stage 2 Assignments.
It is several months later and Mark has implemented your recommendations for his IT infrastructure. Business is booming! Mark’s father has seen what a great success Mark’s 3D printing business is, and he wants to provide the capital to open two more facilities near Veterans Administration Hospitals in Memphis, Tennessee and Phoenix, Arizona. Mark is very excited about expanding his business and being located near service men and women who will benefit from his 3D printed accessibility and assistive devices. Since he has already purchased several server and storage devices to hold his designs and business information, he would like to retain that investment. One thing he has learned is that, with very high speed internet connections, the 3D design files can be downloaded in just a few seconds, so they would not have to be stored at each of his new locations. Mark’s plan is to create two new facilities, each with the same number of 3D printers and staff as he has at his current location. The employees at the new locations will also need access to the ERP system to report their time and order supplies, etc.
Mark has asked you to explain how his IT infrastructure should be changed to accommodate these two new facilities and allow him to manage the overall enterprise as one business. Use the following outline for your paper:
List the components. In part 1 of your Stage 2 assignment, you listed the computer system, information system, and network components needed at Mark’s facility. Here you will list which of those components (hardware, software, security devices, communication network and its devices, wired/wireless devices, internet, and data and information, as appropriate) will be located at each of the two new (remote) locations. (Create one list; it will be the same for both.) Some components may not be needed at the new locations; you should not list those. The new locations may require some components not in use at the original site; these should be included in the list.
Explain the changes that will be needed in Mark’s current (existing) IT infrastructure to incorporate the two new locations, and handle the increase in the number of designs and orders and the additional employees.
Explain what is different in the IT infrastructure at the two new locations versus the IT infrastructure now in place at Mark’s current facility, and explain why the differences exist.
Create an original graphical representation of the three facilities and show the devices that would be located at each location. Show how the locations would be connected and the devices required.
Formatting:
Parts 1, 2, and 3 should be about 2 single spaced pages in length, and be in Microsoft Word format, or a format that can be read in Word.
Part 4 is an original graphic diagram(s) that should be included in the same document. If you have too much difficulty inserting the diagram, you may provide it as a separate file that can be read by Word, Excel or PowerPoint.
Compare your work to the Grading Rubric below to be sure you have met content and quality criteria.
Your submission should include your last name first in the filename: Lastname_firstname_Stage_3
GRADING RUBRIC:
The “right” and “wrong”?answers have to do with whether or not you correctly incorporated the course vocabulary and concepts from the textbook to support your choices and have addressed all parts of the assignment.?
IFSM 310 3D Printing Stage 4 Assignment
Before you begin this assignment, be sure you:
Have completed all previously assigned readings.
Read the ??3D Printing Case Study.”
Reviewed the feedback on your 3D Printing Stage 1, 2 and 3 Assignments.
It is now a year later, and Mark has opened his two new facilities in Memphis, Tennessee and Phoenix, Arizona. All three locations are operating almost around the clock to create 3D printed accessibility and assistive devices. Mark and his father are planning to open several more facilities, also located near Veterans Administration Hospitals and rehab facilities.
Mark does not want to continue to increase his IT infrastructure at the original location and has decided to move all of his systems and files to a cloud service provider. You have recommended that since he has everything set up the way he wants it and the systems are performing well for him, that he just move what he has to an Infrastructure as a Service (IaaS) cloud provider. Before Mark agrees to this, he wants to understand more about just how that would work, using his current systems and locations. He also has a lot of questions about how the communications systems work, and he wants to understand the protocols, the architecture and the four layer TCP model.
Use the following outline for your paper:
Provide an opening paragraph as an introduction that explains what is contained in the paper. (You might write this after you develop the rest of your paper.)
Explain what IT infrastructure changes will occur at the original location by telling Mark which components will be located at the IaaS cloud provider’s location and what will remain at his facility. Explain any changes that are needed at the two remote locations in order to use the IaaS cloud services. Provide a list of which components will be located at the cloud location, at Mark’s primary facility, and at the two remote locations.
Create an original graphical representation showing the cloud provider and the three current locations. Show which components will be located at the cloud provider’s site and which will remain at the three locations. Label each component and the locations.
List the protocol involved for each communication link in the design, including internet connectivity, wired connections, and wireless connections. Be sure to include security protocols, as appropriate to the infrastructure design you created and the components you identified.
Explain the concept of a layered systems architecture to aid in communications and the benefit of a layered architecture such as the TCP or OSI model.
Using the four layer TCP model, explain what each layer’s function is and how it will apply when Mark uses his ERP information system that will be located at the cloud service provider’s location.
Using the four layer TCP model, explain what happens when a packet of information travels from the server at the cloud provider to a tablet device at Mark’s facility. Be sure to identify the points at which each of the layers of the model are the primary enabler of the communication.
Formatting:
All parts of the assignment except for the graphic should be about 3-4 single spaced pages in length, and be in Microsoft Word format, or a format that can be read in Word.
Part 3 is an original graphic diagram that should be included in the same document.
Compare your work to the Grading Rubric below to be sure you have met content and quality criteria.
Your submission should include your last name first in the filename: Lastname_firstname_Stage_4
GRADING RUBRIC:
The “right” and “wrong”?answers have to do with whether or not you correctly incorporated the course vocabulary and concepts from the textbook to support your choices and have addressed all parts of the assignment.?
Collepals.com Plagiarism Free Papers
Are you looking for custom essay writing service or even dissertation writing services? Just request for our write my paper service, and we'll match you with the best essay writer in your subject! With an exceptional team of professional academic experts in a wide range of subjects, we can guarantee you an unrivaled quality of custom-written papers.
Get ZERO PLAGIARISM, HUMAN WRITTEN ESSAYS
Why Hire Collepals.com writers to do your paper?
Quality- We are experienced and have access to ample research materials.
We write plagiarism Free Content
Confidential- We never share or sell your personal information to third parties.
Support-Chat with us today! We are always waiting to answer all your questions.
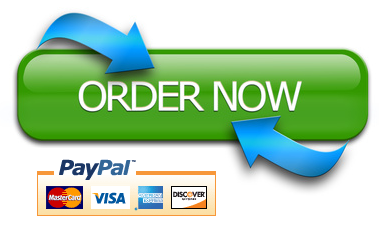