Open circulation cooling water systems are commonly used in the manufacturing industry to cool equipment and goods and release waste heat into the environment. Waste water from the system, a
chemical engineering report
Requirements: fix my report
Date: 27th February 2023.
To: TA Name
From: Your name, team #, lab section
Subject: Investigating the effects of air flow rate and water flow rate on the performance of Open Circuit Cooling Tower System.
Summary.
The purpose of cooling towers is to remove excess heat from the water source. In many cases, this water is heated as a result of some industrial process (e.g. a reaction in a nuclear power plant) or (more often) from an air conditioner condenser. A cooling tower is essentially a heat exchanger in which the blown air acts as a cool stream while the flowing water acts as a hot stream. There are two main types of cooling towers: 1) open circuit or 2) closed circuit. The device used is designed with an open circuit; this type of cooling tower is a special type of heat exchanger in that the hot and cold streams come into direct contact as the blown air and water interact in the tower. In general, open circuit designs offer lower costs, cooler water and are smaller compared to closed circuits, but are more prone to clogging. An analysis of the conditions under which evaporative cooling is most effective and can be used to transfer large amounts of heat. By utilizing mass and energy balances in the system, as well as determining important thermodynamic and heat transfer parameters, cooling tower design, analysis, and operation can be improved.
Introduction
Open circulation cooling water systems are commonly used in the manufacturing industry to cool equipment and goods and release waste heat into the environment. Waste water from the system, as well as water lost to evaporation and leaks, result from this procedure. As water supplies become scarcer and serious environmental contamination increases, there has been a heightened emphasis on water conservation and the reduction of emissions from open cooling water systems. With the help of water-saving devices and water-alternative technologies, industrial water-saving research is also focusing on optimising the structure and operational characteristics of the water system as a whole (such as air cooling instead of water cooling).
Most manufacturing procedures necessitate careful management of temperatures. As such, cooling towers are an integral part of many power plant setups. As a heat removal mechanism, a cooling tower works by dissipating waste heat energy from hot water into the surrounding air, which is often cool and dry.
In order to dissipate excess heat, cooling towers are often utilised to dissipate heat from a water stream into the surrounding air. Power plants frequently employ cooling towers to chill the water that circulates around the facility. Many computational and experimental investigations of cooling towers have been conducted. This section summarises some important books.
The effectiveness of a dry natural draught cooling tower was investigated in order to improve its cooling capacity. The building’s performance under varying wind speeds was calculated using computational fluid dynamics software. Results show that beyond 4 m/s, a dry natural draught cooling tower’s cooling efficiency declines as wind speed increases due to non-uniform ventilation and vorticity within the tower. An increase in cooling efficiency was observed while using a cover, regardless of the wind speed tested.
The use of inlet air spray cooling improves the performance of dry natural draught cooling towers. Experimental and theoretical data on dry natural draught cooling towers were reviewed, and a spray cooling system was investigated. This system uses a number of spray nozzles, each of which produces a spray with its own unique characteristics in terms of pressure, flow, and droplet size distribution. As can be seen from these findings, precooling the incoming air improves cooling tower performance and reduces power generating losses in hot environments.
Using balance equations, we anticipated how the water and air temperatures and humidity would change with increasing and decreasing tower height. Pilot studies have evaluated the performance of cooling tower parts like water jets and droplet separators. Using a 3D version of Computational Fluid Dynamics / Fluent, the flow structure and properties were anticipated. Using a 2D version of Fluent, we also projected the airflow outside of a cooling tower in both cold and hot conditions.
Considering the impact of operating parameters like relative humidity, inlet water temperature, air dry bulb temperature, heat load, and tower efficiency, an analytical model was proposed to predict the amount of water absorbed by the ambient air in a cross-flow wet cooling. tower. The conclusions from the model and the data from the experiments were in good agreement. All aforementioned aspects, as well as dry bulb temperature, were significantly correlated with cooling tower efficiency.
The cooling tower was built with a number of physical factors in mind, such as the size of the water droplets and the humidity of the air. Tower performance in relation to atmospheric conditions and atmospheric pressure were also studied. Using calculative strategies, a mechanical draught cooling tower control system was developed and quantitatively studied.
Figure 1: A schematic view of nuclear power plant with cooling tower and main components
Materials, methods and safety
A cooling tower is operated vertically, with hot water being “sprayed” into the tower from above, while ambient air is blown into the tower in the opposite direction (i.e. upwards) as seen in Figure 2 below. Here, most of the water (which has been cooled) collects at the bottom of the cooling tower, which can then be pumped out and reheated as it acts as a source of cooling.
Figure 2. Illustration of interactions occurring in a cooling tower between the warm water circuit flowing from top to bottom and the cool air circuit blowing from bottom to top
Cooling towers work on the principle of evaporative cooling; in fact, most of the cooling effect seen in cooling towers is the result of evaporative cooling rather than simply heat transfer by conduction or convection. The cooling potential of this evaporation process is significant ? evaporating a single liter of water releases ~2260 joules into the atmosphere (enough energy to run a 60W light bulb for >10 hours.
There are two main components in a cooling tower system (dry air and water), so a mass balance should be performed for both dry air and water with boundaries set at the inlet and outlet of the cooling tower (Figure 3). As can be seen in Figure 3 and Equation 1, the dry air mass balance is relatively trivial because air flowing in also flows out. However, the water mass balance is a bit more complicated because some of the water is lost by evaporation (Equation 2).
In Equations 1 and 2, the subscripts 1, 2, 3 and 4 correspond to the inlets and outlets for the respective components as seen in Figure 3.
Figure 3. Mass balance utilizing boundaries at the inlet and outlet of the cooling tower; the dry air stream (gray arrow) and liquid water stream (solid blue arrow) interact within the black box. The points 1 and 2 indicate the inlet and outlet of the dry air stream, respectively, while points 3 and 4 indicate the inlet and outlet of the liquid water stream, respectively. The dashed blue line indicates the water that evaporates inside the cooling tower and leaves the system with the air.
For the energy balance, you can assume that the cooling tower is well insulated (so heat transfer outside the tower is minimal, no work is done inside the tower (water pump and air fan are out of bounds), and changes in kinetic and potential energy are negligible.
Figure 4. Mechanical Draft Forced Type Cooling Tower.
Results and Discussion
We investigated the effect of air flow rate at three different flow rates on cooling tower performance. This was set using the throttle on the intake air pump. Flow changes were estimated based on differential pressure. For these estimated changes in air flow rate during the lab, we connected the positive sensor to the very top pressure port on the column, while leaving the negative sensor unconnected to measure ambient pressure.
We also investigated the effect of water flow of at least three different flow rates on cooling tower performance (the maximum allowed by the device is ~50 L/h).
Now we will compare two of the 5 available cooling towers that can be used. Since we had two experimental days, we examined one tower on the first day and another tower on the second day. We used 0.5 or 1.0 heating rates to vary the inlet water temperature. 0.5 or 1.0 were used because overheating problems can occur at 1.5 kW.
Figure 5 and Figure 6 show the experimental results data of Tower 1 and Tower 2, respectively. By comparing the corresponding values ??of the two towers, we can understand the trends to analyze the conditions under which evaporative cooling is most effective and can be used to transfer large amounts of heat.
Figure 5. Experimental Results of Tower 1.
Figure 6. Experimental Results of Tower 2.
There is no doubt that the CT evaporation rate is a crucial variable in the current model. Parameters of the ambient air (dry bulb temperature and wet bulb temperature), inlet and exit temperatures of the cooling water, and the air-to-water ratio all play significant roles in determining the evaporation rate.
Cooling Column K
Range = inlet water Temp ? outlet water Temp
= 22.7C – 22.9C
= -0.2C
Approach = outlet water Temp ? outlet bulb Temp
= 22.9 ? 18.2
= 4.7C
Efficiency = x 100%
= x 100%
= -4.4%
Evaporation Loss = 0.00085 x 1.8 x Range x Circulating Water Flow
Evaporation Loss = 0.00085 x 1.8 x -0.2 x 50
= 0.0153
Cooling Column Type 3
Range = inlet water Temp ? outlet water Temp
= 22.1C – 24C
= -1.9C
Approach = outlet water Temp ? outlet bulb Temp
= 24 ? 17.3
= 6.7C
Efficiency = x 100%
= x 100%
= -39.5%
Evaporation Loss = 0.00085 x 1.8 x Range x Circulating Water Flow
Evaporation Loss = 0.00085 x 1.8 x -1.9 x 43.7
= 0.127
Conclusions
The literature was studied to determine the fundamental features of an open circuit cooling tower. The importance of cooling towers in various types of power plants has been discussed at length. This includes not only nuclear power plants and chemical factories, but also oil refineries, petrochemical plants, and food processing facilities.
In this analysis, open cooling water systems are subjected to both the mass conservation and energy conservation equations. Mathematical models of the link between water consumption, dewatering rate, water quality, and water temperature factors have been established in order to analyse the fluctuation in water supply and runoff of open cooling water systems under varied water quality and temperature parameters.
Data from the experimental results of Tower 1 and Tower 2 were compared to understand the trends to analyze the conditions under which evaporative cooling is most effective and can be used to transfer large amounts of heat.
From the results, we can conclude that by reducing outlet water temp, and by increasing wet bulb temperature the efficiency of the system can be improved and hence the evaporation losses will be minimum.
References
1. Liu, W.; Chien, S.H.; Dzombak, D.A.; Vidic, R. D. Scale control for heat exchangers in recirculating cooling systems using treated municipal wastewater. Indian. Eng. Chem. Res. 2014, 53, 16366?16373.
2. Fisenko, S.P., Brin, A.A., Petruchik, A.I. “Evaporative cooling of water in a mechanical draft cooling tower”. International Journal of Heat and Mass Transfer, 47(1), 165-177 (2004).
3. Milosavljevic, N., Heikkilä, P. “A comprehensive approach to cooling tower design”. Applied Thermal Engineering, 21(9), 899-915 (2001).
4. Naik, B.K., Muthukumar, P. “A New Approach to Performance Evaluation of Mechanical Draft Wet Cooling Towers”. Applied Thermal Engineering, 121, 14-26 (2017).
5. Sai, B.B., Swathi, I., Prasanna, K.S.L., Rao, K.S. “Design of Cooling Tower”. International Journal of Scientific & Engineering Research, 4(5), 1560 (2013)
6. Linnhoff, B.; Vredeveld, R. Pinch technology has matured. Chem. Ing. Prog. 1984, 80, 33?40.
Appendix A: (Diagrams/Labels of Apparatus and Sensor Locations)
Appendix B: Information on Cooling Column Options, Fan and Water Pump
Cooling column 1
?? Packing density = 93 m2/m3
?? L x W x H = 210 x 210 x 630 mm
?? Weight = ~5 kg
Cooling column 2
?? Packing density = 73 m2/m3
?? L x W x H and weight same as column 1
Cooling column 3
?? Packing density = 187 m2/m3
?? L x W x H and weight same as column 1
Cooling column 4
?? Packing density = 0 m2/m3
?? L x W x H and weight same as column 1
Cooling column 5
?? Packing density = variable
?? W x H same as column 1 (length = 922 mm)
?? Number of distributor bases = 3
Fan
?? Power = 0.25 kW
?? Maximum differential pressure = 4.30 mbar
?? Maximum volume flow ~ 17 l/s
A water pump
?? Power = 0.66 kW
?? Maximum transport height = 70 m
Cooling Tower
Broad Objectives: To apply thermodynamic and heat transfer principles to the analysis of cooling towers and investigate the utility of cooling towers and analyze what properties affect performance characteristics of the towers.
Background: The purpose of cooling towers is to remove excess heat from a source (i.e., usually water). In many circumstances, this water is heated due to some industrial process (e.g., nuclear power plant reaction) or (more commonly) from an air conditioning condenser. Essentially, a cooling tower is a heat exchanger where blowing air acts as the cool stream while the flowing water acts as the hot stream. There are two main types of cooling towers: 1) open circuit or 2) closed circuit. The apparatus in our lab is an open circuit design; this type of cooling tower is a special type of heat exchanger in that the hot and cold streams come into direct contact as the blowing air and water interact in the tower. In general, open circuit designs offer lower costs, cooler water and a smaller approach (is a smaller approach good or bad? why?) compared to closed circuits but are more susceptible to fouling.
Usually (and in the case of the experimental cooling tower seen in our lab), the cooling tower is operated vertically with hot water being ?sprayed? into the tower from above while ambient air is blown into the tower in the opposite direction (i.e., up) as seen in Figure 1 below. Here, most of the water (which has been cooled) pools at the bottom of the cooling tower which can then be pumped away and heated again as it acts as a cooling source (as discussed above).
Figure 1. Illustration of interactions occurring in a cooling tower between the warm water circuit flowing from top to bottom and the cool air circuit blowing from bottom to top
Cooling towers operate on the principles of evaporative cooling; in fact, most of the cooling effect seen in cooling towers is the result of evaporative cooling rather than simply heat transfer by conduction or convection. The cooling potential of this evaporative process is significant – in fact, the evaporation of a single liter of water releases ~2,260 Joules into the atmosphere (enough energy to run a 60W light bulb for >10 hours). By understanding the conditions under which evaporative cooling is most effective (i.e., where are swamp coolers most effective?), cooling towers can be used to transfer large amounts of heat.
There are two main components in the cooling tower system (dry air and water) so a mass balance should be done on both the dry air and the water with boundaries set at the inlet and outlet of the cooling tower (Figure 2). As seen in Figure 2 and Equation 1, the mass balance on the dry air is relatively trivial as the air flowing in also flows out. However, the water mass balance is slightly more complicated as some water is lost to evaporation (Equation 2). There is no direct way to measure this evaporative mass flow rate – can you develop an expression that can be used to represent this?
Mass Balance of dry air:? (Eq. 1)
Mass Balance of water: (Eq. 2)
In Equations 1 and 2, the subscripts 1, 2, 3 and 4 correspond to the inlets and outlets for the respective components as seen in Figure 2 while indicates a mass flow rate.
Figure 2. Mass balance utilizing boundaries at the inlet and outlet of the cooling tower; the dry air stream (gray arrow) and liquid water stream (solid blue arrow) interact within the black box. The points 1 and 2 indicate the inlet and outlet of the dry air stream, respectively, while points 3 and 4 indicate the inlet and outlet of the liquid water stream, respectively. The dashed blue line indicates the water that evaporates inside the cooling tower and leaves the system with the air.
For the energy balance, you can assume that the cooling tower is well insulated (so heat transfer outside of the tower is minimal, there is no work done inside the tower (water pump and air fan are outside of the boundaries), and the changes in kinetic and potential energy are negligible. Therefore, the energy balance simplifies to only depend on changes in enthalpy as seen in Equation 3.
Energy Balance: (Eq. 3)
In Equation 3, the subscripts in and out represent the inlets and outlet streams, respectively,indicates a mass flow rate and h indicates enthalpy on a per mass basis. By utilizing mass and energy balances on the system as well as determining important thermodynamic and heat transfer parameters, the design, analysis and operation of a cooling tower can be improved.
Experimental Notes:
You should investigate the effect of air flow rate (at least three (3) different flow rates) on the performance of the cooling tower.
This is set using a butterfly valve on the inlet air pump.
While calculating the air flow rate during lab may be difficult, you can estimate changes in the flow rate based on differential pressure (see Note on Air Flow Rate below).
You should investigate the effect of water flow rate (at least three (3) different flow rates) on the performance of the cooling tower (maximum allowed by apparatus is ~50 L/h).
There are 5 possible cooling towers to utilize – you must compare and contrast at least two (2) of them. As you have two experimental days, you may want to plan on investigating one tower on the first day, and another tower on the second day.
Note: There are three (3) rates of heating (0.5, 1.0 and 1.5 kW) that you can utilize to alter the inlet water temperature – we recommend using 0.5 or 1.0 as there can be some overheating issues that occur at 1.5 kW).
If you are measuring pressure differential, ensure that the pressure sensors are connected to the correct ports.
Note on Air Flow Rate: To help estimate changes to the air flow rate during lab, connect the positive sensor to the very top pressure port on the column while leaving the negative sensor unconnected (to measure ambient pressure).
If time allows, perform replicates. Timing will vary based on your team but if you are getting more than 12-16 runs in a lab period, you are going far too fast and not letting the system reach steady state.
Analysis that must be completed and you may want to present in report:
Utilize an h-x diagram (an h-x diagram is a type of psychometric chart; there are paper and electronic h-x diagrams in Canvas) or another resource to determine the following parameters for the inlet and outlet of your tower:
Absolute humidity (g water/kg dry air)
Enthalpy (kJ/kg)
Note that enthalpies obtained from an h-x diagram usually have a (1+x) subscript associated with them indicating that the enthalpy value applies to 1 kg dry air with x kg water
Wet bulb temperature
You don?t necessarily need to report on the above parameters but you will likely need them for further analysis.
Calculate the volumetric flow rate of air.
There is no simple, direct way to measure the air flow rate in our apparatus. There are two ways to calculate from the measured values – see the document in Canvas for some hints/details on how to do it.
Minimum Analysis that you must present in your report:
Calculate the approach and efficiency of your system. What do these tell us about our cooling tower operation?
Calculate the volumetric rate of water lost to evaporation in the system (this is also referred to as the water make-up).
Compare the above quantities and analyze trends when using different columns, air and water flow rates.
There are a lot of different variables (both independent and dependent) in this experiment – make sure you give extra thought into the most effective methods to present your data and trends.
Appendix A: Diagrams/Labels of Apparatus and Sensor Locations
Appendix B: Information on Cooling Column Options, Fan and Water Pump
Cooling Column 1
Packing density = 93 m2/m3
L x W x H = 210 x 210 x 630 mm
Weight = ~5 kg
Cooling Column 2
Packing density = 73 m2/m3
L x W x H and weight same as Column 1
Cooling Column 3
Packing density = 187 m2/m3
L x W x H and weight same as Column 1
Cooling Column 4
Packing density = 0 m2/m3
L x W x H and weight same as Column 1
Cooling Column 5
Packing density = variable
W x H same as Column 1 (length = 922 mm)
Number of distributor bases = 3
Fan
Power = 0.25 kW
Maximum differential pressure = 4.30 mbar
Maximum volumetric flow rate ~ 17 L/s
Water Pump
Power = 0.66 kW
Maximum head = 70 m
Tower 1123M1 (%)30.8M1 (%)29.9M1 (%)29M2 (%)75.2M2 (%)74.7M2 (%)74.5T1 (C)23.5T1 (C)23.5T1 (C)23.6T2 (C)16.6T2 (C)16.6T2 (C)16.6T3 (C)22.7T3 (C)22.7T3 (C)22.7T4 (C)22.9T4 (C)22.6T4 (C)22.4T5 (C)16.6T5 (C)16.2T5 (C)15.8PD1 (mbar)1.49PD1 (mbar)1.76PD1 (mbar)1.99F1 (L/h)50F1 (L/h)50F1 (L/h)49456M1 (%)29M1 (%)27.9M1 (%)28M2 (%)74.1M2 (%)73.9M2 (%)73.2T1 (C)23.5T1 (C)23.6T1 (C)23.6T2 (C)16.5T2 (C)16.6T2 (C)16.6T3 (C)22.7T3 (C)22.7T3 (C)22.8T4 (C)22.4T4 (C)22.5T4 (C)22.7T5 (C)25.5T5 (C)15.8T5 (C)16.3PD1 (mbar)1.99PD1 (mbar)1.75PD1 (mbar)1.49F1 (L/h)45F1 (L/h)44F1 (L/h)44789M1 (%)27.8M1 (%)27.3M1 (%)27.5M2 (%)72M2 (%)71.7M2 (%)71.4T1 (C)23.7T1 (C)23.8T1 (C)23.8T2 (C)16.8T2 (C)16.9T2 (C)16.8T3 (C)22.8T3 (C)22.9T3 (C)22.9T4 (C)23.3T4 (C)23.5T4 (C)23.5
T5 (C)16.2T5 (C)15.8T5 (C)25.6PD1 (mbar)1.5PD1 (mbar)1.7PD1 (mbar)2F1 (L/h)39F1 (L/h)39F1 (L/h)38Tower 2123M1 (%)38.3M1 (%)37.5M1 (%)38.9M2 (%)81.3M2 (%)81.3M2 (%)83T1 (C)23T1 (C)23T1 (C)23T2 (C)16.1T2 (C)16.3T2 (C)16.8T3 (C)21.9T3 (C)21.9T3 (C)22T4 (C)23.5T4 (C)23.4T4 (C)23.4T5 (C)16.9T5 (C)16.9T5 (C)17.3PD1 (mbar)1.88PD1 (mbar)1.75PD1 (mbar)1.5F1 (L/h)49F1 (L/h)48F1 (L/h)48456M1 (%)39.5M1 (%)40.5M1 (%)41.4M2 (%)83.2M2 (%)82.2M2 (%)81.9T1 (C)23T1 (C)23T1 (C)23.2T2 (C)16.9T2 (C)16.9T2 (C)17.2T3 (C)22.1T3 (C)22.2T3 (C)22.3T4 (C)23.8T4 (C)24.1T4 (C)24.3T5 (C)17.3T5 (C)17.3T5 (C)17.4PD1 (mbar)1.47PD1 (mbar)1.76PD1 (mbar)1.86F1 (L/h)44F1 (L/h)44F1 (L/h)44789M1 (%)42M1 (%)41.5M1 (%)41.3M2 (%)80.6M2 (%)81M2 (%)82.7
T1 (C)23.2T1 (C)23.1T1 (C)23.2T2 (C)17.4T2 (C)17.5T2 (C)17.7T3 (C)22.3T3 (C)22.4T3 (C)22.3T4 (C)23.7T4 (C)25.1T4 (C)25.4T5 (C)17.5T5 (C)17.7T5 (C)17.9PD1 (mbar)1.9PD1 (mbar)1.72PD1 (mbar)1.51F1 (L/h)39F1 (L/h)39F1 (L/h)39
Collepals.com Plagiarism Free Papers
Are you looking for custom essay writing service or even dissertation writing services? Just request for our write my paper service, and we'll match you with the best essay writer in your subject! With an exceptional team of professional academic experts in a wide range of subjects, we can guarantee you an unrivaled quality of custom-written papers.
Get ZERO PLAGIARISM, HUMAN WRITTEN ESSAYS
Why Hire Collepals.com writers to do your paper?
Quality- We are experienced and have access to ample research materials.
We write plagiarism Free Content
Confidential- We never share or sell your personal information to third parties.
Support-Chat with us today! We are always waiting to answer all your questions.
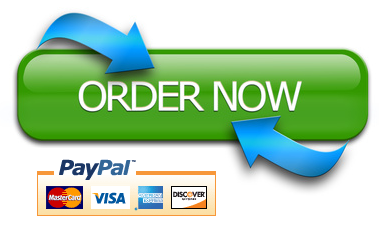