write research on this I have attached the outline you did last time there are 3 sources already and i have attached those sources too take help, and there should be 5 total sources you can
write research on this I have attached the outline you did last time there are 3 sources already and i have attached those sources too take help, and there should be 5 total sources you can include any 2 trusted online article of your choice.
In work please include things like, things that would affect aviation, the global crisis aspect of electric aviation, and also include the opposing view as well.
1
5
Annotated Bibliography
Schäfer, A. W., Barrett, S. R., Doyme, K., Dray, L. M., Gnadt, A. R., Self, R., O’Sullivan, A., Synodinos, A. P., & Torija, A. J. (2019). Technological, economic and environmental prospects of all-electric aircraft. Nature Energy, 4(2), 160–166. https://doi.org/10.1038/s41560-018-0294-x.
In this research article, authors perform a comprehensive evaluation of the potential for all-electric aircraft to become a viable alternative to hydrocarbon fuel-powered commercial aviation. They consider factors such as the energy, economic, and environmental implications of such a transition. The authors argue that for all-electric aircraft to be viable, batteries need to have a higher specific energy and lower costs, as well as a reduction in the costs and CO2 intensity of electricity. I chose this article for my research because it provides a thorough analysis of the technical, economic, and environmental prospects of all-electric aircraft. The authors consider both the potential benefits and drawbacks of such a transition and provide a realistic assessment of the necessary conditions for all-electric aircraft to become a viable alternative to hydrocarbon-fueled aviation. One text citation from this source is: “All-electric aircraft could greatly reduce the environmental impact of aviation” (Schäfer et al. 2019, 164).
Tahir, M., Khan, S. A., Khan, T., Waseem, M., Khan, D., & Annuk, A. (2022). More electric aircraft challenges: A study on 270 V/90 V interleaved bidirectional DC–DC converter. Energy Reports. Retrieved February 6, 2023, from https://www.sciencedirect.com/science/article/pii/S2352484722012240.
The article focuses on the challenges associated with the implementation of a more electric aircraft (MEA) concept. The MEA is seen as a way to make aircraft more energy efficient and reduce their carbon footprint. The authors focus on the design of a dc-dc converter that interfaces between 270 VDC and 28 VDC bus bars in aircraft applications. They argue that while the Dual Active Bridge topology is well-known and promising, the presence of current and voltage ripples can be detrimental to the life of the battery and filtering components. To reduce the voltage gain requirements and minimize ripple, the authors propose a two-stage bidirectional converter that combines a three-phase interleaved buck-boost converter with the Dual Active Bridge. I chose this article for my research because it provides a detailed and practical examination of one of the technical challenges associated with the implementation of the MEA concept. One text citation from this source is: “An efficient and reliable bidirectional dc–dc converter is an indispensable part of More electric aircraft that is energy efficient and playing a curial role in meeting environmental goals” (Tahir et al. 2022, 1139).
Thalin, P., Taubert, S., Mare, J.-C., & Rajamani, R. (2018). Fundamentals of Electrical Aircraft. SAE International. "Fundamentals of Electric Aircraft"
This is text that offers an objective view of the electric aircraft and the innovative technologies enabling aircraft electrification. The book provides insight into the paradigm shift across different aircraft segments from General Aviation to Large Aircraft through case studies. The authors, who are industry veterans, address design constraints, timelines, and performance enhancements of electric aircraft. They analyze how fuel burn savings may bring more value for money with the delivery of new electric technologies. The publication balances futuristic approaches with the operational realities of the business and provides a general view of the progress made so far and what to expect in the future. I chose this book for my research because of its comprehensive coverage of the topic and its focus on the fundamental concepts and technologies behind electric aviation. One text citation from this source is: “From an environmental perspective, a lot of progress has been made thanks to the more-electric aircraft in service, such as the Boeing 787.” (Thalin et al., 2018, 226)
References
Schäfer, A. W., Barrett, S. R., Doyme, K., Dray, L. M., Gnadt, A. R., Self, R., O’Sullivan, A., Synodinos, A. P., & Torija, A. J. (2019). Technological, economic and environmental prospects of all-electric aircraft. Nature Energy, 4(2), 160–166. https://doi.org/10.1038/s41560-018-0294-x
Tahir, M., Khan, S. A., Khan, T., Waseem, M., Khan, D., & Annuk, A. (2022, July 2). More electric aircraft challenges: A study on 270 V/90 V interleaved bidirectional DC–DC converter. Energy Reports. Retrieved February 6, 2023, from https://www.sciencedirect.com/science/article/pii/S2352484722012240
Thalin, P., Taubert, S., Mare, J.-C., & Rajamani, R. (2018). Fundamentals of Electrical Aircraft. SAE International.
,
AnAlysis https://doi.org/10.1038/s41560-018-0294-x
1Air Transportation Systems Laboratory, UCL Energy Institute, University College London, Central House, London, UK. 2Laboratory for Aviation and the Environment, Department of Aeronautics and Astronautics, Massachusetts Institute of Technology, Cambridge, MA, USA. 3Institute of Sound and Vibration Research, Engineering and the Environment, University of Southampton, Highfield, Southampton, UK. *e-mail: [email protected]
Owing to their high energy content per unit weight and vol- ume, easy handling, global availability and manageable costs, liquid hydrocarbons have been a key enabler of com-
mercial flight over the past century. In 2015, the global aircraft fleet consumed 276 million tonnes of jet fuel—7% of global oil products1.
However, reliance on oil products comes at an environmen- tal cost. Aircraft CO2 emissions, owing to combustion of jet fuel, comprise 2.7% of energy-use-related CO2 emissions1,2. It is also esti- mated that the non-CO2 warming impacts of aircraft are of the same magnitude as aircraft CO2 emissions, thus approximately doubling aviation’s contribution to climate change3–5. The single largest non- CO2 contributor to warming may be the formation of contrails and contrail cirrus clouds3. In addition, aviation combustion emissions that affect air quality, such as NOx, are set to rise substantially6. This may increase the estimated 16,000 premature mortalities per year attributable to aviation emissions globally7. There is also growing evidence that noise from aircraft results in adverse health impacts and premature mortality among affected populations8.
Various options exist for reducing CO2 emissions from aircraft. For example, fuel burn per revenue passenger kilometre (RPK) of the US narrow-body aircraft fleet could be reduced by around 2% per year at no cost through 20509, whereas reductions obtainable for wide-body, long-distance aircraft would probably be smaller. However, these rates will be outpaced by the anticipated global aviation demand growth of around 4.5% per year10,11. In contrast to fuel-efficiency improvements, low-carbon fuels (for example, biofuels) could partially decouple CO2 emissions from aviation growth, although these options face cost and scale limitations and do not much help with non-CO2 impacts12,13, except for a potential thinning of contrails (the effect of which has an uncertain sign)14,15. Similarly, liquid hydrogen16 and liquified natural gas17 could greatly reduce direct CO2 emissions, but these fuels’ higher hydrogen con- tent would result in enhanced contrail and cirrus cloud formation.
Until recently, energy carriers that do not entail in-flight com- bustion have not been considered. This work focuses on all-electric
aircraft that have the potential to eliminate both direct CO2 emis- sions and direct non-CO2 impacts, although the net impact will depend on the power generation mix and associated emissions. However, exploiting these unparalleled benefits requires substantial technological advances, especially inbattery performance and cost.
Technology trajectories towards all-electric aircraft Two broad technology trajectories appear to lead to all-electric air- craft. The first trajectory builds upon the incremental electrification of jet engines. This class of hybrid-electric aircraft includes designs without batteries (that is, turbo-electric aircraft), in which the elec- tric propulsion system serves to increase propulsive efficiency and provide for some degree of boundary-layer ingestion (in which ingestion and re-energizing of the aircraft boundary layer improves efficiency)18,19. The extent of fuel burn reductions is then the net effect of the increased propulsive efficiency and the additional weight of the electrical components. Hybrid-electric aircraft with batteries are also being considered, where the batteries may provide for additional power or regeneration at limited specific operating conditions. Although hybrid-electric aircraft with batteries would entail direct combustion emissions for the majority of flights, they could provide for reduced or eliminated emissions during particu- larly sensitive parts of a flight—such as flying through ice super- saturated parts of the atmosphere (to reduce contrails) or during takeoff and landing (to reduce near-airport emissions). With suf- ficient advancements in battery technology, however, the ultimate design is an all-electric aircraft, which would have no direct com- bustion emissions and thus have the potential to remove aviation- specific non-CO2 impacts and reduce CO2 emissions depending on the source of the electricity. In contrast, the second technology trajectory builds upon scaling up all-electric air taxis. Ref. 20 reports 55 such air vehicle designs, 80% of which are already all-electric. Progress in battery technology, especially specific energy, would then enable the scaling up of all-electric designs to larger vehicles, first to regional jets and then to narrow-body aircraft.
Technological, economic and environmental prospects of all-electric aircraft Andreas W. Schäfer 1*, Steven R. H. Barrett2, Khan Doyme1, Lynnette M. Dray1, Albert R. Gnadt 2, Rod Self3, Aidan O’Sullivan1, Athanasios P. Synodinos3 and Antonio J. Torija3
Ever since the Wright brothers’ first powered flight in 1903, commercial aircraft have relied on liquid hydrocarbon fuels. However, the need for greenhouse gas emission reductions along with recent progress in battery technology for automobiles has gener- ated strong interest in electric propulsion in aviation. This Analysis provides a first-order assessment of the energy, economic and environmental implications of all-electric aircraft. We show that batteries with significantly higher specific energy and lower cost, coupled with further reductions of costs and CO2 intensity of electricity, are necessary for exploiting the full range of economic and environmental benefits provided by all-electric aircraft. A global fleet of all-electric aircraft serving all flights up to a distance of 400–600 nautical miles (741–1,111 km) would demand an equivalent of 0.6–1.7% of worldwide electricity consumption in 2015. Although lifecycle CO2 emissions of all-electric aircraft depend on the power generation mix, all direct combustion emissions and thus direct air pollutants and direct non-CO2 warming impacts would be eliminated.
NATuRe eNeRGy | VOL 4 | FEBRUARY 2019 | 160–166 | www.nature.com/natureenergy160
AnAlysisNature eNergy
All-electric aircraft energy use Aircraft energy use (E) per RPK during cruise flight can be described conveniently by the Breguet range equation21,22. Rearranged for energy intensity, equations (1) and (2) report energy use per RPK for jet engine aircraft (JEA) and all-electric aircraft (AEA), with PAX being the number of passengers transported, L/D the lift-to- drag ratio, ηtotal the total (tank-to-wake) efficiency of the jet engine or electric propulsion system, and W the weight of either fuel, the jet engine aircraft at the beginning (i) or the end (f) of the mission, or of the all-electric aircraft at any point during the mission.
η=E PAX L D W W W/ RPK 1 / ( ( / )) / ln( / ) (1)JEA total,JEA fuel i f
η=E PAX L D W/ RPK 1 / ( ( / )) (2)AEA total, AEA AEA
Assuming the same passenger count and lift-to-drag ratio between the jet engine and all-electric aircraft, equations 1 and 2 differ by only the propulsion system efficiencies and the weight fac- tor. The latter is about 50–100% larger for all-electric aircraft as a consequence of the relatively low-specific energy batteries23,24. For narrow-body jet engine aircraft, Wi/Wf is typically 1.1–1.3; with Wfuel accounting for typically 10–30% of a narrow-body aircraft takeoff weight, the weight factor then roughly corresponds to the narrow- body aircraft takeoff weight. The resulting 50–100% higher energy intensity of all-electric aircraft is mitigated by the roughly two-fold tank-to-wake efficiency of electric propulsion systems compared to their jet engine counterparts22,25. We note that this calculation does not include the energy use associated with takeoff and climb, nor does it account for the upstream efficiency losses associated pri- marily with electricity generation. The latter strongly depend on the power generation technology and accounting practices for renew- able energy.
A key enabler of electric flight and a critical determinant of energy intensity is the battery-pack specific energy. This variable enters the energy intensity of all-electric aircraft in equation (2) via the aircraft weight. If the on-board battery energy supply is kept constant, a higher specific energy leads to a lower all-electric air- craft weight and thus a lower aircraft energy use per RPK, which, in turn yields a longer range. In addition, a lighter aircraft would allow the downsizing of other components, such as landing gear, motor power, and so on, which yield additional energy intensity reduc- tions and range gains.
Today’s best available Li-ion battery cells have a specific energy of around 250 Wh kg−1 (refs 26,27). Assuming a packing efficiency of 80%, which is at the lower end of projected future levels28 and below that of the recently developed Airbus E-Fan29, the pack-specific energy would result in roughly 200 Wh kg−1 and 1.7% of the jet fuel energy content. This battery would be capable of powering electric air taxis with 1–4 passengers over a distance of around 100 km20. However, short-range electric aircraft demand battery-pack specific energies of 750–2,000 Wh kg−1, which translates into 6–17% of the jet fuel energy content, depending on aircraft size and range22–24,30,31. Much of the required 4–10-fold increase in battery-pack specific energy could potentially be achieved with advanced Li–S technol- ogy, although Li-air chemistry may ultimately be required for the higher end of that range. Both of these battery technologies have low specific power, so an additional, high-power battery or another means of augmenting power may be required for takeoff and climb.
The historical long-term rate of increase in specific energy of the major battery chemistries has been around 3% per year, a doubling every 23 years32,33, although since 2000, specific energy has increased at a rate of 4% per year33. Although there is no ‘Moore’s Law’ equiva- lent for batteries—since significant advances require entirely new battery chemistries to be made practicable before incremental improvement can occur—this historical observation does suggest
that the timescale for such progress to be made could be of the order of decades. On the basis of a continuation of the historical increase in specific energy, current levels of specific energy of 250 Wh kg−1 for advanced Li-ion battery cells, and a packing efficiency of 80%, a battery-pack specific energy of 800 Wh kg−1 could potentially be reached at around mid-century. This is consistent with the times- cale of change in the aviation industry—for both the infrastructure and aircraft design lifecycles. For the purposes of this work we take the lower end of the above battery-pack specific energy range of 800 Wh kg−1 that is required for Airbus A320/Boeing 737-sized air- craft to be capable of up to 600 nautical miles (1,111 km) missions, depending on the specific layout and amount of batteries carried23.
In addition to battery pack specific energy, all-electric aircraft weight is determined by the power-to-weight ratio of the motors and the supporting infrastructure, consisting mainly of cables and power electronics. Whereas regional jets with about 50 seats are likely to require significantly improved mainstream technology, narrow-body aircraft with 100 seats and above may depend upon lightweight high-temperature superconducting electric motors due to the intrinsically high weight of conventional electric motors and the difficulty in providing cooling34.
environmental impacts All-electric aircraft would completely eliminate direct combus- tion emissions and thus remove associated direct CO2 and non- CO2 warming. The lifecycle CO2 intensity of all-electric aircraft is determined by the CO2 intensity of electricity used, losses associ- ated with battery charging and electricity transmission/distribution, and the specific aircraft design and operation. Figure 1 depicts the warming intensity of a first-generation 180-seat, 150-passenger, all-electric aircraft over a mission of 400 nautical miles (741 km), which is projected to consume 180 Wh per RPK for a battery-pack specific energy of 800 Wh kg−1 (ref. 23). Using the 2015 average US grid CO2 intensity of 456 g of CO2 per kWh, this all-electric aircraft would generate 91 g of CO2 per RPK, if losses associated with electricity transmission/distribution and battery charging are included. This value is about 20% higher than the lifecycle CO2 intensity of its modern, jet engine counterparts (the ‘US’ dashed line in Fig. 1). However, if non-CO2 impacts are taken into account (by way of a factor of two3–5), the overall warming per RPK would be reduced by around 30%. The lifecycle CO2 intensity of all-electric aircraft would further decline with improved aircraft and battery technology and the potential transition of the grid towards renew- able energy. Conversely, a longer range capability would result in a higher energy and thus CO2 intensity owing to the additional bat- tery weight, as visible from equation (2). Note that CO2 emissions and non-CO2 impacts (such as cooling related to sulphur emissions from coal-fired power stations35) may still occur depending on the power generation mix.
If greenhouse gas emissions from battery production were taken into account, the warming intensity of all-electric aircraft shown in Fig. 1 would be slightly larger. Based on Li-ion battery studies, the increase in warming intensity would be 2–10 g of CO2 equivalent per RPK, depending upon the underlying assumptions36. However, employing end-of-economic-life high-performance batteries in sta- tionary applications would significantly reduce these emission lev- els, as would the enhanced use of renewable electricity for battery production (see Methods).
In addition to removing direct non-CO2 impacts, all-electric air- craft would also eliminate direct air pollution. While indirect air pollution may occur depending on the power generation technolo- gies employed, there is greater potential for emissions control of ground-based power generation compared to in-flight combustion.
Noise impacts of all-electric aircraft may be better or worse than conventional aircraft, depending on the design decisions made. Assuming a conventional tube and wing configuration, which
NATuRe eNeRGy | VOL 4 | FEBRUARY 2019 | 160–166 | www.nature.com/natureenergy 161
AnAlysis Nature eNergy
does not take advantage of the design flexibility offered by electric propulsion, we estimated an overall improved noise performance of all-electric aircraft relying on a battery-pack specific energy of 800 Wh kg−1 compared to best-in-class current-generation short- haul aircraft. Considering both takeoff and landing operations, a 36% reduction in noise contour area is estimated, compared to the best-in-class aircraft (see Methods). This could allow extended air- port operation hours, thus increasing aircraft utilization and airport capacity. During takeoff, aircraft noise is mainly determined by the thrust of the engines required. Owing to lower fan pressure ratios and the absence of combustion noise, we anticipate a more than 50% reduction in takeoff noise contour area. In contrast, during landing, the higher weight of all-electric aircraft means that the determi- nants of noise (principally lift, drag and landing speed) will result in a 15% larger noise contour area compared to those of best-in- class narrow-body aircraft. Higher battery-pack specific energy and future aircraft designs would provide the opportunity for reduced noise through novel aircraft design concepts and changes in opera- tional procedures (such as highly distributed propulsion and steep approaches with propulsors in generating mode).
All-electric aircraft economics Compared to gas turbine engine aircraft, all-electric aircraft will have a different operating cost structure. Over its lifetime, an all-
electric aircraft may require several generations of potentially expensive batteries, a factor that contributes to upfront investments (via the first set of batteries) and maintenance costs (via replace- ment batteries). In addition, its higher weight could increase the maintenance requirements of landing gear components. On the other hand, all-electric aircraft may also experience cost savings. For example, they would not require a fuel system or an additional gas turbine (auxiliary power unit) for generating electricity, engine starting, and so on. In addition, there may be potential for reduc- tions in engine maintenance costs owing to the relative mechanical simplicity of electric motors, although this is uncertain for narrow- body aircraft due to the challenges of cooling high-temperature superconducting electric motors.
Taking into account only the differences in the largest-expendi- ture items between an all-electric aircraft and a jet engine aircraft in terms of capital costs (energy storage and propulsion system) and maintenance costs (landing gear and battery replacement), Fig. 2 depicts the potential range of breakeven electricity prices for a first-generation Airbus A320/Boeing 737-sized all-electric air- craft with a range of 400 nautical miles (741 km). Two sets of lines are shown with different levels of specific energy. Each set repre- sents battery costs of US$ 100 kWh−1 and US$ 200 kWh−1, which reflect the target and 2017 level of Li-ion batteries37. At the 2015
0
2
4
Batte ry-
sp ecif
ic energy:
1,200 W h/kg
$100 per k W
h
$200 per k W
h
$100 per k Wh
$200 per k Wh
Batte ry-specific
energy: 8 00 W
h/kg 6
8
10
12
14
0.0 0.5 1.0 1.5 2.0 2.5 3.0 3.5 4.0
B re
ak ev
en e
le ct
ric ity
p ric
e (C
p er
k W
h)
Jet fuel price (US$ per gallon)
Thickness of breakeven cost lines reflects uncertainty of electric propulsor costs
Range of 2015 US electricity price: industry (lower end) – residential (upper end)
2015 +$100/tCO2
Fig. 2 | Break-even electricity price for a first-generation all-electric aircraft. The reference jet engine aircraft is an Airbus A320neo. The all-electric aircraft has batteries with a specific energy of 800 Wh kg−1 (grey lines) or 1,200 Wh kg−1 (blue lines), each with battery costs of US$ 100 kWh−1 or US$ 200 kWh−1. On the basis of a battery-pack specific energy of 800 Wh kg−1, jet fuel prices would need to be at least US$ 2.3 or 2.8 per gallon (US$ 97 or US$ 118 per barrel)—depending on the cost of the battery—in order to achieve cost effectiveness relative to jet engine aircraft in light of the 2015 US electricity end-use prices. Whereas the 2015 US jet fuel price of US$ 1.8 per gallon would lead to breakeven prices below the range of the observed end-use electricity prices in the USA, a CO2 price of US$ 100 per tonne of tCO2 (US$ 0.97 per gallon of jet fuel) would lead to breakeven electricity prices within the range of observed end-use electricity prices (provided electricity is produced on a carbon-neutral basis). If taking into account non-CO2 impacts on the basis of an ‘uplift factor’ of 2, corresponding to a doubling of the greenhouse gasemissions price (here, to US$ 200 per tonne of CO2 equivalent), the cost effectiveness would increase further. It is apparent that battery costs would need to be around US$ 100 kWh−1 or less to achieve cost effectiveness over the longer term. About the same battery cost target exists for automobiles, albeit at a much lower specific energy, to achieve cost parity with internal combustion engine vehicles37. More advanced batteries with a higher specific energy, more advanced aircraft designs, and repurposing end-of-life batteries for use in other sectors would improve the economics of all-electric aircraft. Costs in the graph are in 2015 US$.
0
20
40
60
80
100
120
140
160
180
200
0 200 400 600 800 1,000
A irc
ra ft
w ar
m in
g in
te ns
ity (
g C
O 2
eq ui
v. p
er R
P K
)
Carbon intensity of electricity (g CO2 per kWh)
Jet engine aircraft: CO2 and non-CO2
Jet engine aircraft: CO2 only
Brazil EU-28 World China
US
Coal-based electricity
Oil-based electricity
Gas-based electricity
0
100
200
300
400
500
600
700
800
1970 1980 1990 2000 2010 2020
World average
C ar
bo n
in te
ns ity
( g
C O
2 pe
r kW
h)
Fig. 1 | Warming intensity of a projected first-generation all-electric aircraft and of a current-generation jet engine aircraft versus carbon intensity of electricity. The mission length is 400 nautical miles (741 km). The lifecycle CO2 intensity of the all-electric aircraft with an electricity intensity of 180 Wh per RPK is based on a design in ref. 23 and takes into account efficiencies of 95% for battery charging and 95% for electricity transmission or distribution. In contrast, the lifecycle CO2 intensity of the A320neo of 75 g of CO2 per RPK is based on an energy intensity of 0.9 MJ per RPK, calculated with the aircraft performance model Piano-X61, and a well-to-tank efficiency of 88%62; its warming intensity corresponds to two times its direct CO2 emissions. The shaded areas represent the interquartile range of the CO2 intensity of coal-based (limited to 1,000 g of CO2 per kWh), oil-based and natural gas-based electricity on a country basis in 20152. The 2015 electricity fuel mix in Brazil, the EU-28, the US and the world average would lead to a lower warming intensity of all-electric aircraft compared to jet engine aircraft (two times the CO2 intensity), as exemplified by the dashed red arrows for the US. If we consider only long- lived CO2 emissions, the CO2 intensity of all-electric aircraft would be below that of their jet engine counterparts for the 2015 EU-28 and Brazilian fuel mix, but larger in the US, China and the world as a whole. Meeting the Paris Agreement on climate requires significantly stronger reductions in the CO2 intensity of e
Collepals.com Plagiarism Free Papers
Are you looking for custom essay writing service or even dissertation writing services? Just request for our write my paper service, and we'll match you with the best essay writer in your subject! With an exceptional team of professional academic experts in a wide range of subjects, we can guarantee you an unrivaled quality of custom-written papers.
Get ZERO PLAGIARISM, HUMAN WRITTEN ESSAYS
Why Hire Collepals.com writers to do your paper?
Quality- We are experienced and have access to ample research materials.
We write plagiarism Free Content
Confidential- We never share or sell your personal information to third parties.
Support-Chat with us today! We are always waiting to answer all your questions.
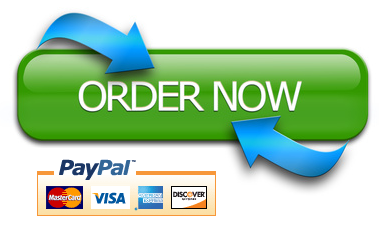