Develop an journal of two to four pages, excluding title and
ndividual Assignment This assignment is an introduction to college-level writing. Create an journal in APA format. Check the examples in the library writing resources and brush up on writing skills. Develop an journal of two to four pages, excluding title and reference page. Create an introduction using APA section title, repeating the title page byline. Then, use 1st and 2nd level section titles to create topics from the reading. Within each section title (topic) develop journal points by combining information from two or more library articles. Select topics from the course readings. Introduce the topic by paraphrasing information from the class reading. Then, search the library for articles on the topics selected from the class reading. Paraphrasing information from resources (class material and library articles) is a good way to demonstrate understanding of course objectives. Remember to match the title page format, section titles, citations, and references in APA format. Match each type to examples in the library writing resources. APA Formatting required.
My journal will be on reverse logistic and sustainability.
Chapter 16. Facility Layout Decision
After selecting a facility's location, the next major decision is to design the best physical layout for the facility. The available space needs to be assessed with workstations, equipment, storage, and other amenities need to be arranged. The goal is to create the most efficient workflow produce necessary to produce its goods or services at the highest level of quality with the lowest possible cost.
Layout planning is organizationally important not only for efficient operations, but other functions are impacted as well such as marketing which is affected by layout when clients come to the site, human resources as layout impacts people and finance as layout changes can be costly endeavors.
The layout decision can determine how efficient a facility is. In the case of the supply chain this is primarily focused in the warehousing function, in both the warehouse itself and various other areas including office and maintenance areas.
Layout should be considered in a variety of situations including when a new facility is being constructed, when there is a significant change in demand or through put volume, when a new good or service is introduced to the customer benefit package or different processes, equipment, and/or technology are installed.
The focus of layout improvements are to minimize delays in materials handling and customer movement, maintain flexibility use labor and space effectively, promote high employee morale and customer satisfaction, provide for good housekeeping and maintenance and enhance sales as appropriate in manufacturing and service facilities .
Types of Layouts
There are five primary types of workflow layouts that managers can choose from:
1. Product layout – Production line (e.g., an automobile assembly plant).
2. Process layout – Arranged in departments (e.g., hospitals, printer).
3. Hybrid layout – A combination of both product and process layouts.
4. Fixed-position layout: building a large item (e.g., airplane, cruise ship).
5. Cellular layout – Reorganizes people and machines into groups to focus on single products or product groups
We will now discuss each in some detail.
Product Layouts
Product arrangements are based on the sequence of operations that are performed during the manufacturing of a fairly standardized good or delivery of a service. Typically, work stations and equipment are located along the line of production, as with an assembly line for example. Batches of semi-finished (i.e. work in process) goods are passed to the next station in a production line.
Some examples of this type of layout include: winemaking industry, credit card processing, Subway sandwich shops, paper manufacturers, insurance policy processing, and automobile assembly lines.
Advantages of product layouts include lower work-in-process inventories, shorter processing times, less material handling, lower labor skills and relatively simple planning and control systems.
Disadvantages include that a breakdown at one workstation can cause the entire process to shut down or a change in product design and the introduction of new products may require major changes in the layout, resulting in limited flexibility.
Process Layouts
Process layouts usually have a functional grouping of equipment or activities that perform similar work.
Examples of process layout include: legal offices, print shops, footwear manufacturing and hospitals.
Advantages of process layouts may include a lower investment in equipment and that the diversity of jobs can lead to increased worker satisfaction.
Disadvantages may include high movement and transportation costs, more complex scheduling and control systems, longer total processing time, higher in-process inventory or waiting time, and higher worker skill requirements.
Warehouse (Process) Layout Considerations
The objective in warehouse (and really all process type) layout is to optimize the trade-offs between handling costs and costs that are associated with warehouse space while at the same time minimizing damage and spoilage to the product.
When considering warehouse layouts, it is most effective to arrange work centers or functional process areas so as to minimize the total costs of material handling between departments or work centers.
The basic cost elements involved in this “load distance” (or LD) minimization calculation are: 1) the number of loads (or people) moving between centers and 2) the distance loads (or people) moved between centers.
Once estimating these elements for all possible combinations, a total “load x distance” is calculated for the current state. One can then look for improved layout arrangements that reduce the total “load x distance” by evaluating various number and distance (can use cost which will vary by distance travelled) of load combinations between the elements. This can be estimated manually in a simple spreadsheet, or for more optimal results by using packaged software such as Factory Flow, Proplanner and CRAFT.
Maximizing Density
By maximizing the total “cube” or space of a warehouse you are able to better utilize its full volume while maintaining low material handling costs.
Material handling costs include all costs associated with a transaction such as: incoming transport, storage, finding and moving material, outgoing transport, equipment, people, material, supervision, insurance and depreciation.
Warehouse density also tends to vary inversely with the number of different items stored. While this may sound counterintuitive, one must realize that each item or SKU will have its own set of dimensions. So if you carried one single item in a warehouse, you would be able to use almost every inch of storage space. However, most warehouses have hundreds if not thousands of items, all with different dimensions, making it more difficult to maximize the use of storage space.
That’s where the concept of “random stocking” can be used, allowing for the more efficient use of warehouse space. Random stocking can be greatly aided by the use of a warehouse management system (WMS; described in chapter 8 ).
Key tasks in random stocking include maintain a list of open locations, accurate inventory records, the sequencing of items to minimize travel and picking time, combining of picking orders and assigning classes of items to particular areas.
Minimizing Travel Time to Maximize Warehouse Efficiency
The concept of “velocity slotting” helps to minimize travel time which is critical to productivity in a warehouse, as it tries to locate at least some of the faster moving “A” type items closer to the shipping area and slower moving items further away and higher up.
The use of automated storage and retrieval systems (ASRS) can significantly improve warehouse productivity.
Dock location is also a key design element. The primary decision is where to locate each department relative to the dock. It is important to organize departments so as to minimize travel time (can be thought of as a “load x distance” total for measurement purposes).
The usage of “cross-docking” which we discuss in chapter 8 , modifies the traditional warehouse layouts. Cross-dock facilities tend to have more docks, less storage space, and less order picking as materials are moved directly from receiving to shipping and are not placed in storage in the warehouse.
Cross-docking requires tight scheduling and accurate shipments, bar code or RFID identification used for advanced shipment notification as materials are unloaded. They also typically require automatic identification systems (AIS’s) and information systems such as WMS.
The location of value-added activities performed at the warehouse, which can enable low cost and rapid response strategies, must be factored into to layout decision. These can include the assembly of components, repairs, customized labeling and packaging among other activities.
Office (Process) Layout Considerations
When we look at an office (process) layout, we consider the grouping of workers, their equipment and the space required to provide comfort, safety and flow of information.
One way to evaluate office layout is using a “relationship matrix” ( Figure 16.1 ) in which you can look at the relative importance to various people and functions and based upon the results, revise the layout.
Figure 16.1. Office Relationship Matrix
The movement of information is a large factor, however, it is constantly changing due to frequent technological advances. In fact, certain advances, like the use of electronic documents, may make the movement of information a “non-factor”.
Much of the American workforce works in an office environment including many supply chain and logistics administrative functions. In this environment, human interaction and communication are the primary factors in designing office layouts.
When considering layout in an office, you need to account for both the physical environment and psychological needs of the organization.
One key layout trade-off is between proximity and privacy. Some companies have gone to more “open office” concept with no walls and sound absorbing ceiling panels. Open concept offices promote understanding and trust, but may not be appropriate depending on job functions and privacy issues.
Flexible layouts can incorporate what is known as “office landscaping” to help to solve the privacy issue in open office environments. Office landscape involves furniture and desk placement, usually in open-plan office settings. It often also involves the selection and placement of plants, the creative use of natural light and the use of artwork to create ambiance.
Hybrid Layouts
Hybrid or combination layouts combine elements of both product and process layouts. They tend to keep some of the efficiencies of product layouts while maintaining some of the flexibility of process layouts.
For example, a business may have a process layout for the majority of its process but also have an assembly line in one particular area. Alternatively, a firm may utilize a fixed-position layout (described below) for the assembly of its final product, but use assembly lines to produce the components and subassemblies that make up the final product (ex: a cruise ship).
Cellular (or “Work Cell”) Layouts
This type of layout design is not typically established according to functional characteristics of equipment, but instead by creating self-contained groups of equipment (called “work cells”; Figure 16.2 ) and dedicated operators needed for producing a particular family of goods or services (by family, we mean one or more items or services that have mostly the same steps or processes).
Figure 16.2. Assembly Line (top) vs. Work Cell (bottom) Layout
The concept of cellular manufacturing or group technology classifies parts into families so that efficient mass-production-type layouts can be designed for the families of goods or services.
Cellular layouts are used to centralize people expertise and equipment capability and are usually laid out in a “horseshoe” type shape instead of a long assembly line. This is to gain better flow, improve use of equipment, smaller batch size (i.e. “make one, pass one”) and fewer more cross-trained operators.
Work cells, while common in manufacturing, can be applied strategically in offices (ex: processing orders) and warehouses (ex: kitting). Additional examples might include group legal or medical specialties.
Benefits and advantages of work cells include:
• Reduced work-in-process,raw material and finished goods inventory.
• Less use of floor space.
• Reduced direct labor cost.
• Heightened sense of employee participation as a result of thehigh level of training, flexibility and empowerment of employees which results in improved morale and increased productivity.
• Increased equipment and machinery utilization.
• As they are essentially self-contained, they have their own equipment and resources.
• Tests such as a poka-yoke, which is a foolproof testing device, are commonly used at stations in work cell to improve quality.
Fixed Position Layout
A fixed position layout consolidates resources necessary to manufacture a good or deliver a service, such as people, materials, and equipment, at one physical location. As the fixed-position layout is typically used with “project” type of processes where the product that is too large or too heavy to move, required resources must be portable so that they can be taken to the job for “on the spot” performance.
Examples of this type of layout include the production of large items such as heavy machine tools, airplanes, buildings, locomotives, and ships is usually accomplished in a fixed-position layout.
Service-providing firms often use fixed-position layouts, such as major hardware and software installations, sporting events, and concerts.
Due to the nature of the product, the user has little choice in the use of a fixed-position layout.
Disadvantages can include those related to limited space on the site resulting in a work area may be crowded which can also cause material handling problems and administration as the span of control can be narrow, making coordination unwieldy.
Facility Design in Service Organizations
Service organizations can use product, process, cellular or fixed-position layouts to organize different types of work.
Process Layout Examples
There are many examples of process layout in service organization. They can be seen in libraries where they place reference materials, serials and microfilms into separate areas; hospitals which group services by function such as maternity, emergency room, surgery and X-ray; and insurance companies which have office layouts in which claims, underwriting and filing are individual departments.
Product Layout Examples
Service organizations that deliver very standardized services tend to use product layouts. For example, the kitchen at a fast food restaurant that has both dine-in and delivery will tend to be arranged in an assembly line type layout with some pre-prepared items such as cooked hamburgers, slice tomatoes, etc. for easier assembly.
Some of the eyeglass chains use both process and product layouts where the customer contact area may be arranged in a process layout, but the lab area, where lenses are manufactured, may be in a product type layout.
Designing and Improving Product Layouts
Assembly-Line Design and Balancing
An assembly line is a product layout dedicated to combining the components of a good or service. Typically there are parts are added as the semi-finished item to be assembled moves from work station to work station. Parts are added in sequence until the final assembly is produced.
Assembly line balancing is a procedure where tasks along the assembly line are assigned to an individual workstation so that each has roughly the same amount of work.
When designing product layouts in this type of situation, one needs to consider the sequence of tasks to be performed by each workstation, a logical order to assemble the finished item and the speed of each process.
Examples of processes that use assembly line layout include the automobile industry, winemaking industry, credit card processing, sandwich shops, paper manufacturers and insurance policy processing.
There are a series of steps required in the line balancing process. They are:
Step 1: Identify tasks and immediate predecessors in the assembly line process.
Step 2: Determine output rate required of the final item.
Step 3: Determine cycle time, which is the longest time that an item can be at any one workstation ( note: a workstation can be made up of one or more individual tasks or processes).
Step 4: Compute the “theoretical” minimum number of work stations.
Step 5: Assign individual tasks to workstations (i.e. balance the line to make sure the process is flowing smoothly and there are no “bottlenecks” that slow up the process).
Step 6: Compute efficiency, idle time and balance or eliminate any delays or bottlenecks identified.
Assembly Line Balancing Example
Step 1: Identify tasks and immediate predecessors (perfume spray filling and packaging line example in Table 16.1 )
Table 16.1. Perfume and Packaging Line Balancing Example – Tasks and Predecessors
Step 2: Determine output rate of final item (Ex: 60 bottles per hour with 8 hours per shift).
Step 3: Determine cycle time (the amount of time each workstation is allowed to complete its tasks)
The throughput or capacity of this process is limited by the bottleneck task (the longest task in a process) which can be calculated as:
Step 4: Compute the theoretical minimum number of stations (i.e. the number of stations needed to achieve 100% efficiency where every available second is used).
Note that you should always round up when calculating the number of workstations.
Step 5: Assign tasks to workstations
Start at the first station and choose the longest eligible task following precedence relationships (i.e. A must precede B, G must follow both E and F, etc.; see Table 16.2 ). Continue adding the longest eligible task that fits without going over the desired cycle time. Once no additional tasks can be added within the desired cycle time, assign the next task to the following workstation until finished.
Table 16.2. Perfume and Packaging Line Balancing Example – Assign Tasks to Workstations
Step 6: Compute efficiency and balance delay
The percent efficiency is the ratio of total task times divided by the number of workstations times the largest assigned cycle time (6 seconds for workstation 4).
Balance delay is the percentage by which the assembly line falls short of 100%.
Balance delay = 100% – 86.1% = 13.9%
Work Cell Staffing and Balancing
As discussed earlier, a work cell reorganizes people and machines into groups to focus on single products or product groups that have similar characteristics and process steps or tasks. In order to justify a cell, there must be sufficient volume, but the cells can be reconfigured as design or volume changes.
When staffing and balancing a work cell, one must first determine the “Takt time” which the rate at which a finished product needs to be completed in order to meet customer demand. It is computed as: [total work time available/units required].
It is also important when setting up a work cell to determine staffing needs. That calculation is: [total operation time required/Takt time] which will determine the number of operators required for the cell.
Work Cell Staffing and Balancing Example
If a picture frame manufacturer requiring 650 frames of a specific size per day produced, is running an 8 hour shift and the manufacturing process requires the operations (and time required) shown in Chart 16.1 , we can then calculate the cell Takt time, number of workers required as well as identify any bottlenecks in the process.
Chart 16.1. Work Cell Staffing and Balancing Example
The Takt time in this case is:
(8 hrs x 60 mins) / 650 units = .74 min = produce one unit every 44 seconds
The workers required for the cell are:
155 seconds/29 = 5.3 or 6(round up)
By calculating the Takt time and staffing requirements of the work cell, we can now also see if there is any imbalance in the operations caused by a bottleneck.
In this example, the assembly operation which takes 55 seconds per picture frame ( Chart 16.1 ) is the bottleneck, as our Takt time is 44 seconds. The result of this is that the operations downstream will either be waiting on the assembly operation, or we will have to run overtime in assembly in order to keep the other processes running. This will incur both higher costs and increased inventory carrying costs.
There are a variety of options to relieve this bottleneck besides running overtime such as cross training of operators in order to shift them to assembly, buying faster or additional assembly equipment etc.
Warehouse Design and Layout Principles
There are some basic guidelines that specifically go into warehouse layout and design. In general, they include: use one story facilities where possible, always try to move goods in a straight-line, use the most efficient materials handling equipment, minimize aisle space and use full building height (i.e. land is expensive; many buildings can go as high as 65’).
Other considerations include when designing a warehouse include:
Cubic capacity utilization
Protection
Efficiency
Mechanization
Productivity
Design and Layout Process
The first major decision in this process is to determine the size of the individual warehouse facility. In addition to specifying the space needed for storage and handling, a location may be needed for processing rework and returns. All warehouses require office space for administrative and clerical activities, so space must be planned for these and other miscellaneous requirements.
The calculation to determine storage space requirements starts with a demand forecast for the facility in question.
Once you have arrived at that, you then need to determine each item’s order quantity (inbound and outbound) which will be converted from units into cubic footage requirements to determine not only storage requirements but other functional area requirements such as for order picking, shipping, receiving, office space, etc. mentioned previously ( Figure 16.3 ).
Figure 16.3. Warehouse Design and Layout Considerations
Some of the most important functions of a warehouse actually occur at the receiving and shipping docks, so it is critical not to neglect these areas during this process.
One should consider the materials received and shipped to help determine dock bay requirements and configuration as well as staging area requirements. There are other miscellaneous requirements for the dock areas such as office space, receiving hold area, trash disposal, empty pallet storage, a trucker’s lounge area and even yard space for vehicles outside that need to be considered.
Of course a lot of thought needs to go into storage space planning, which requires you to:
1. Define the materials to be stored – Define what and how much material will be stored and how the materials are to be stored.
2. Select a storage philosophy – Consider whether selecting a “fixed location” is necessary. If so, determine what specific location each individual stock keeping unit (SKU) is stored in (even if that means that location may be empty sometimes) or if a “random location” storage philosophy will be used instead where any SKU may be assigned to any available storage location.
3. Consider space requirements for aisle space and “honeycombing” storage – It is necessary within a storage area to allow accessibility to the material being stored, so an aisle space “allowance” (i.e. %) must be calculated. The amount of aisle allowance depends on the storage method, which determines the number of aisles required and the material handling method, which in turn helps to determine the size of aisles.
Thought must also be given to an effect known as “honeycombing” storage which is a % allowance of storage space lost whenever a storage location is only partially filled with material and may occur both horizontally and vertically. The unoccupied area within the storage location is honeycombing space.
Additionally, there must be an allowance for growth and adequate aisle space for materials handling equipment.
Technology
As mentioned earlier in this chapter, the design and layout of an office or warehouse can be determined manually by hand, with a spreadsheet, or for more optimal results, by using packaged software such as Factory Flow, Proplanner and CRAFT.
Careers
While other functions such as industrial engineering may have more say in terms of the details of warehouse design and layout, supply chain management has great input, if not the final say, for most if not all of the layout decisions mentioned in this chapter.
At this point, we have covered the major functional areas of supply chain & logistics management in terms of planning and managing them. Next we will look at how to control these processes.
Collepals.com Plagiarism Free Papers
Are you looking for custom essay writing service or even dissertation writing services? Just request for our write my paper service, and we'll match you with the best essay writer in your subject! With an exceptional team of professional academic experts in a wide range of subjects, we can guarantee you an unrivaled quality of custom-written papers.
Get ZERO PLAGIARISM, HUMAN WRITTEN ESSAYS
Why Hire Collepals.com writers to do your paper?
Quality- We are experienced and have access to ample research materials.
We write plagiarism Free Content
Confidential- We never share or sell your personal information to third parties.
Support-Chat with us today! We are always waiting to answer all your questions.
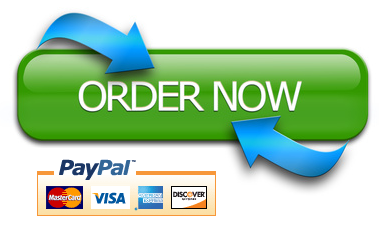