Anticipation of Workplace Hazards
Anticipation of Workplace Hazards
One of the “root causes” of workplace injuries, illnesses, and incidents is the failure to identify or recognize hazards that are present, or that could have been anticipated. A critical element of any effective safety and health program is a proactive, ongoing process to identify and assess such hazards.To identify and assess hazards, employers and workers should collect and review information about the hazards present or likely to be present in the workplace.
Part A:The firstassignmentis to anticipate possible hazards in your workplace. To help you get started , use the OSHA Hazard Awareness Advisor to help you identify possible areas for assessment. The Advisor will ask a series of questions designed to identify your potential hazards. Following the questions, the Advisor will prepare a text report identifying hazards that may be present in your workplace, providing best practices or strategies to control them, and listing applicable standards which you can later review.
NOTE: The Advisor does not automatically save the results of each session. Use the print function to save as a PDF file. File name should be “LAST NAME – OSHA Hazard Awareness Advisor”.
Part B – Prepare a table the following information, as a minimum.
1) Topic/title –
2) Assessment location – Name of the business or workcenter, address, number of employees, brief overview of the mission of the business. Identify type of industry and NAICS code applicable to the business.
3) Brief history of the site – How long has the business been located in that physical location? Was there prior businesses or industries in that location prior?
4) Preliminary list of expected hazardsin their respective categories (chemical, physical, biological)
5) Which OSHA standard applies? Does your state have an OSHA program? Is there an industry-specific resource that applies to your job site?
Submit one document with Part A and B in the Assignment folder of LEO. Don’t forget to document any sources used to answer these questions in APA format with a reference list at the end of your assignment.
ENMT322 Occupational Health and Safety
Week 2 Assignment
Chemical Hazard Identification and Assessment
The Occupational Safety and Health Administration (OSHA) hazard communication standard (HCS), also known as the “employee right-to-know” standard, is found at 29 CFR 1910.1200 of the general industry standards and incorporated into the construction standard at 29 CFR 1926.59.This standard requires all employers to develop a written program addressing labeling and warning requirements, safety data sheets (SDSs) and employee training on hazardous materials. The standard also requires employers to develop and maintain a list of all hazardous substances in the workplace.
Typically, the first step to hazard identification and assessment is looking at the physical inventory of chemicals used in the workplace. If no inventory exists at your workplace, then it will be up to you to gather the necessary information.
• Part A (20 points): Students will need to collect information for one to threechemical product(s) used at their workplace. The following information should be gathered and documented in a table format:
Product Name; ID Number; Manufacturer’s Name and Address; Manufacturer’s Telephone Number; SDS on file (Y/N)?
If the SDS is on file, be sure to get a copy for your records. If not, then you will need to research the internet for that information. The information found on the SDS will be used in Part B of this assignment.
Describe how the chemical product is used in the workplace (including application method, amounts used, personal protective equipment used, any other existing controls in place).
*If your workplace appears to have no chemical products, look for portable fire extinguishers, cleaning supplies, sanitizers, paint cans, compressed gases, or other substances not necessarily used by employees, but nevertheless, present in the workplace. Pesticides, foods, drugs, alcohol beverages and other items listed in 29 CFR 1910.1200(b) are not regulated by OSHA, but are regulated by other federal agencies, and cannot be used in this assignment because they are subject to different labelling and information standards. If nothing in your workplace meets the acceptable criteria, contact the instructor for acceptable alternatives.
**For students who are not currently employed, contact the instructor for alternative avenues.
• Part B (30 pts):Forone chemical product, summarize the information provided on the Safety Data Sheet on the table format attached to this assignment. Submit one full electronic copy of your SDS with the assignment; submitting just an URL will not acceptable and will result in complete loss of points.
• Part C (50 pts): Using the online version of the CDC’s NIOSH Pocket Guide, research the ingredients and complete the remaining information associated with exposure to the chemical.
GHS Product Identifier:
Chemical Product Name:
Synonyms and Trade Names:
Product Type:
Product Use:
Classification of the substance or mixture:
Ingredient Name
1.
2.
3.
4.
%
CAS Number
RTECS No.
Physical Description
Boiling Point
Solubility
Vapor Pressure
Flashpoint
Upper Explosive Limit
Lower Explosive Limit
NIOSH Exposure Limits (REL)
OSHA Exposure Limits (PEL)
IDLH
Measurement Methods
Is it a carcinogen?
Exposure Routes
Symptoms of Exposure
Target Organs
ENMT322 Occupational Health and Safety
Week 3 Assignment
Physical Agents Recognition
Identifying workers’ exposure to health hazards is typically more complex than just identifying safety hazards. In Week 3, we identified chemical hazards found in the chemical products used in the workplacesuch solvents, adhesives, paints, toxic dusts, etc. Week 4 will be dedicated to physical hazards such as noise, radiation, heat, etc., and ergonomic risk factors like heavy lifting, repetitive motions, vibration.
Physical hazards are hazards that can cause harm without the worker coming into direct contact with the hazard. Issues such as high noise levels, extreme temperatures, or radiation fall into this category. If your workplace is considered “administrative” in nature (i.e. office or retail), then an ergonomic evaluation may be appropriate.
Part A (30 pts): Students will need to collect information for one physical hazard presented at their workplace. You will need to provide the following information as a minimum:
• Category of hazard (noise, thermal stress, radiation, ergonomic, etc)
• Enter the name of the source presenting the risk in the workplace. Use specific terms such as “Black and Decker 3/8” drill or AN/TPS-43 Ground Radar”
• Applicable OSHA regulatory standard
• Description of work process where the exposure occurs – include a physical description of the physical location (indoors vs outdoors), number of minutes (hours) that the exposure occurs.
• Existing engineering, administrative or personal protective equipment controls
• Identify any quantitative measurements taken if applicable.
Part B (50 pts): Using the UMUC Library, search for relevant and scholarly articles that address health effects of the physical hazard you have identified.
If you need help using the UMUC Library database, go to http://www.umuc.edu/library/ and click on the Ask a Librarian link, or use our library’s tutorial on obtaining research materials: http://sites.umuc.edu/library/libhow/research_tutorial.cfm
If you are unsure about how tell if an article is scholarly, please review the following information: http://sites.umuc.edu/library/libhow/articles.cfm
Prepare a short essay detailing the following information:
1. Using a relevant and scholarly article, prepare a concise two- to three-paragraph summary describing the potential physical effectson the human body with supportive detail. (50 points)
2. Using a relevant and scholarly article,research the controls that are considered “best practices” for their, or a related, industry. Prepare a one-paragraph discussion of how the information presented in your article relates to observable practices beingused in your workplace. Were the best practice principles being used? What additional recommendations would you make at this point? (30 points).
3. Clear, concise paragraphs, with transitions between paragraphs and no grammatical or spelling errors (10 points)
4. Appropriate APA in-text citations and reference list (10 points)
ENMT322 Occupational Health and Safety
Week 4 Assignment
Evaluation of Workplace Hazards
Wet-bulb Globe Temperature [WBGT]
The Wet Bulb Globe Temperature (WBGT) is a measure of the heat stress in direct sunlight, which takes into account: temperature, humidity, wind speed, sun angle and cloud cover (solar radiation). This differs from the heat index, which takes into consideration temperature and humidity and is calculated for shady areas. WBGT measurements are used to determine when heat exposure hazards are present in the workplace. After the WBGT is measured, clothing adjustment factor added, and workload translated into metabolic rate.
For each step, record the information found on the Table located at the end of the lesson. This will be your assignment submittal!
Step 1: Assessing Conditions
Using the link below, perform an evaluation of the heat stress exposure for your “workplace”. (If working from home, use that as your workplace). Be sure to use the information for OUTDOORS. https://www.weather.gov/tsa/wbgt Once you have clicked on the map to reflect your location, record the information on the Answer Sheet found at the end of this lesson.
Step 2: Clothing Adjustment Factors (CAF):
Identify the ACGIH CAF based on the clothing workers are wearing from Table 2. Add the CAF to the WBGT to determine WBGTeff.
Table 2: Clothing Adjustment Factors
Clothing Worn CAF
Work clothes (long sleeves and pants). Examples: Standard cotton shirt and pants 0
Coveralls (w/only underwear underneath). Examples: Cotton or light polyester material 0
Double-layer woven clothing 3
SMS Polypropylene Coveralls 0.5
Polyolefin coveralls. Examples: Micro-porous fabric (e.g. Tyvek suits) 1
Limited-use vapor-barrier coveralls. Examples: Encapsulating suits, whole-body chemical protective suits, firefighter turn-out gear 11
Example:July 2, 2020 @ 4 pm – HAZMAT Responder (firefighter) working a fuel spill outside onHwy 90 in Pensacola, Florida.
WBGT: 84 degrees FWBGTeff = 84 degrees F + 11 degrees = 95 degrees F
Record your information on the Answer Sheet.
Step 3: Determine the Metabolic Work Rate
The ACGIH metabolic work rates represent impacts to the body core temperature from the heat produced internally as exertion increases. Select a work category in Table 3 that best represents the workload using the examples as a guide. If different work activities are planned for the day, use the heaviest workload activity to determine if it’s possible the workers exposure will exceed the allowable limit without controls.
Using the equation below, determine the Estimated Metabolic Rate. Multiply the metabolic rate from the table the ratio of the workers body weight to 70 kg (154 lbs).
Table 3: Metabolic Work Rates
Work Category Metabolic Rate (Watts) Activity Examples Jobs
Rest 115 Sitting Reading a book
Light 180 Sitting, standing, light arm/hand work and occasional walking Bank teller, store cashier
Moderate 300 Normal walking, moderate lifting Retail, food server in restaurant
Heavy 415 Heavy material handling, walking at a fast pace UPS Delivery
Very Heavy 520 Pick and Shovel Work Construction crew
MRest =Work Category (in Watts from Table 3) x worker body weight (in lbs.)
154 lbs
Example: 187 lb male working the HAZMAT spill from Step 2.
MRest = 415 Watts x 187 lbs = 504 W
154 lbs
Record your information on the Answer Sheet
Step 4: Determine the Threshold Limit Value or Action Limit:
The TLV is the temperature at which there is a heat hazard present for an acclimatized worker and the AL is the temperature at which there is a heat hazard present for a non-acclimatized worker. Once these limits are reached, either through environmental factors or workload, controls are necessary to prevent heat-related illness. Controls include work/rest regimens, shade, and hydration.
Using your results from Steps 1, 2 and 3, determine the TLV for an acclimatized worker and an Action Limit for an unacclimatized worker.
a. Convert WBGTeff Farrenheit° to Celsius°
C= ( __°F -32) x 5/9
b. Find WBFTeff on the y-axis and follow it across the table from left to right until it crosses either the dotted line (for AL) or solid line (for TLV) at the appropriate Metabolic Rate on the x-axis.
c. Record your information on the Answer Sheet
Example: HAZMAT Worker from Steps 2 & 3.
WBGTeff = 95°F or 35°C
MRest = 504 WPart B: WBGT Answer Sheet – Record your answers with the proper units (i.e. F, C, %, etc)
Workplace Conditions:
(geographic location, place of business, physical description of area where work is taking place)
Forecasted Max Temp(F°)
Dew Point(F°)
Relative Humidity (%)
Wind Speed (mph)
Cloud Cover(%)
WBGT(F°)
Precautionary Actions
Clothing Adjustment Factor
WBGTeff (F°)
MRest (W)
WBGTeff (F°)
Did your worker exceed the AL?
Did your worker exceed the TLV?
Double check your work:
https://www.osha.gov/SLTC/heatstress/calculator.html
Did it match your evaluation?
ENMT322 Occupational Health and Safety
Week 5 Assignment
Controlling Hazards
You have been hired at a local industry and must conduct your first workplace visit. Go to OSHA eToollink and select an industry: https://www.osha.gov/dts/osta/oshasoft/index.html
Grading Rubric:
• Part A: Identifying Hazards (15 points)
• Part B: Controlling the Hazard (65 points)
• References (20 points) – provide for each section in proper APA format.
Part A: Identifying Hazards(15 points)– Under each eTool, there might be multiple types ofoperationsto choose from. Select oneand evaluate for the chemical or physical hazard.This website will provide a lot of information for your research: https://www.osha.gov/SLTC/text_index.html
NOTE:I have included examples of information in each area so please delete those before completing your evaluation.
Name of Process:
Battery Manufacturing – Oxide Production
Describe the process (the work environment, layout, conditions, etc.):
Lead oxide is made from refined lead. The oxide is then made into a paste by mixing it with water, acid, and other chemicals. In a process parallel to the production of paste, grids are cast from lead alloy. The paste and grids are later combined in the pasting process.
The major source of lead exposure in the oxide production process comes from leaking equipment and system upsets.
Reference: OSHA eTool: Battery Manufacturing. Retrieved from: https://www.osha.gov/SLTC/etools/battery_manufacturing/oxide_grid/oxide_production.html
Potential Hazard:
Lead Dust
Applicable OSHA Standard:
29 CFR 1910.1025
Part B: Controllingthe Hazard (65 points): Nearly every process in any industry has a form of chemical exposure. Select one chemical component from your process to evaluate.
Type of Hazard (Chemical, Physical or Ergonomic):
Chemical
Potential Source(s) of Exposure:
Lead dust can become airborne due to improper air flow or exhaust ventilation, which results in “puffing” of lead oxide at the mill inlet.
Reference: OSHA eTool: Battery Manufacturing. Retrieved from: https://www.osha.gov/SLTC/etools/battery_manufacturing/oxide_grid/oxide_production.html.
OSHA Safety and Health Topics: https://www.osha.gov/SLTC/batterymanufacturing/hazards.html
Route(s) of Exposure:
Inhalation of dust particles; ingestion of dust particles
OSHA Safety and Health Topics: https://www.osha.gov/SLTC/batterymanufacturing/hazards.html
Associated Health Hazards:
Exposure to high levels of lead may cause anemia, weakness, and kidney and brain damage. Very high lead exposure can cause death.
Lead can cross the placental barrier, which means pregnant women who are exposed to lead also expose their unborn child. Lead can damage a developing baby’s nervous system. Even low-level lead exposures in developing babies have been found to affect behavior and intelligence. Lead exposure can cause miscarriage, stillbirths, and infertility (in both men and women).
Generally, lead affects children more than it does adults. Children tend to show signs of severe lead toxicity at lower levels than adults. Lead poisoning has occurred in children whose parent(s) accidentally brought home lead dust on their clothing. Neurological effects and mental retardation have also occurred in children whose parent(s) may have job-related lead exposure.
REFERENCE: NIOSH (n.d.). Lead: Information for Workers. Retrieved from: https://www.cdc.gov/niosh/topics/lead/health.html#:~:text=Exposure%20to%20high%20levels%20of,a%20developing%20baby’s%20nervous%20system.
OSHA Safety and Health Topics: https://www.osha.gov/SLTC/batterymanufacturing/hazards.html
Engineering Controls Options:
• Local exhaust ventilation around dust generation points or
• Isolate the process:Separate the operation from the rest of the plant and keep it under negative pressure.Build a positive pressure control room for the operator.
Reference: OSHA eTool: Battery Manufacturing. Retrieved from: https://www.osha.gov/SLTC/etools/battery_manufacturing/oxide_grid/oxide_production.html
Administrative Controls Options:
• Implement written policy and procedure to notify supervisor of oxide leaks and perform temporary repairs immediately.
• Implement routine maintenance and monitoring schedule to ensure that the local exhaust ventilation is working properly.
• Housekeeping procedures: Vacuum all oxide spills immediately with a central vacuum system or a HEPA vacuum whenever possible during each shift.
• Provide a change of clothes, and shower rooms to minimize contamination spread.
Reference: OSHA eTool: Battery Manufacturing. Retrieved from: https://www.osha.gov/SLTC/etools/battery_manufacturing/oxide_grid/oxide_production.html
Personal Protective Equipment
OSHA Lead Requirements >> Protective Clothing and Equipment:
The following protective clothing and equipment must always be used when lead levels are above the PEL: [29 CFR 1910.1025(g)(1)] (Figure 1)
? Coveralls or similar full-body work clothing; [29 CFR 1910.1025(g)(1)(i)]
? Gloves, hats, and shoes or disposable shoe coverlets; and [29 CFR 1910.1025(g)(1)(ii)]
? Face shields, vented goggles, and other appropriate protective equipment. [29 CFR 1910.1025(g)(1)(iii)]
Clean and dry protective work clothing must be provided daily or weekly depending on exposure levels. [29 CFR 1910.1025(g)(2)(i)]
? Cleaning, laundering, or disposal of protective clothing and equipment must be provided. [29 CFR 1910.1025(g)(2)(ii)]
? Protective clothing and equipment must be repaired or replaced as needed to maintain its safety an effectiveness. [29 CFR 1910.1025(g)(2)(iii)]
? All protective clothing must be removed at the end of a work shift in change rooms provided for that purpose. [29 CFR 1910.1025(g)(2)(iv)]
? Contaminated protective clothing, which is to be cleaned, laundered, or disposed of, must be placed in a closed, labeled container in the changing area. [29 CFR 1910.1025(g)(2)(v)]
? Persons who clean or launder protective clothing or equipment must be informed in writing of the potentially harmful effects of exposure to lead. [29 CFR 1910.1025(g)(2)(vi)]
Containers of contaminated protective clothing and equipment must be appropriately labeled. [29 CFR 1910.1025(g)(2)(vii)]
Reference: OSHA. 29 CFR 1910.1025. Retrieved from: https://www.osha.gov/SLTC/etools/battery_manufacturing/requirements/ppe.html#Clothing
ENMT322 Occupational Health and Safety
Week 6 Assignment
ENMT 322 – Week 6 Assignment
Overview: Your assignment is to use the OSHA Guide to conduct an incident investigation into your chosen topic. The guide describes a 4-Step Systems approach and your job is to identify and summarize the steps by the information as described by the report.
Instructions:
1. Chose a safety topic from the Week 6 Reading (scaffolding, confined spaces, etc).
To locate an incident report on your chosen topic, go to the OSHA Fatality and Catastrophe Investigation Summaries website: (https://www.osha.gov/pls/imis/accidentsearch.html),enter your chosen topic in the “Keyword” search and press submit.
The next screen will give you the search results for that occupational safety and health topic. Pick an event date within 2019 and click on the “Summary Nr”.
This will bring up the Accident Report Details for that incident. As you can see on the screen below, it will show the details including date of incident, number and demographics for the employees affected. Click on “Inspection” to access additional information.
Part A (20 pts):
1. Summarize the employer information, date of accident andaccident summary. Research the company through Google (or other search engine) to include pertinent information such name of the business or workcenter, address, number of employees, brief overview of the mission of the business. Identify type of industry and NAICS code applicable to the business.
2. Using the table found in the Inspection Detail (example below), summarize all of the violations to include interpretation of each standard cited.
Note: All of the numbers in the standard are run together (i.e.19100134 = 29 CFR 1910.134.)
Part B (80 points):
1. 40 points – Using the OSHA Incident Investigation Guide, determine the root causes. The root causes of an incident are exactly what the term implies: The underlying reasons why the incident occurred in a workplace. Root causes generally reflect management, design, planning, organizational and/or operational failings (e.g., employees were not trained adequately; a damaged guard had not been repaired).
2. 40 points – Using the OSHA standard applicable to the incident, make recommendations for corrective actions. Make sure that the corrective actions address the root causes of the incident. For example, if an employee fell off scaffolding, what would have prevented that incident? Use of fall protection equipment? Written policy on fall protection? Training employees on the use of fall protection equipment? Be specific because most hazards will have more than one recommendation. Hint: read the OSHA standard and see where the worker failed to meet compliance requirements.
ENMT322 Occupational Health and Safety
Week 7 Assignment
Watch the CBS Remember the Triangle Shirtwaist Fire found at https://www.youtube.com/watch?v=4ulaG9x4GpE and using Google, find an article or video about the Imperial Chicken fire in 1991, or the Bangladesh Tazreen factory fire of November 2012. Write a 300-word paper comparing the Triangle fire with one of these fires, with an emphasis on the unsafe conditions in the two workplaces. Include references to both sources of information in a bibliography using the APA format.
ENMT322 Occupational Health and Safety
Week 8 Assignment
There is one thing that occupational safety and health professionals know: it’s not enough to just report and track incidents, near misses, and daily behavior—you have to learn and communicate the lessons exposed by the data. Communicating lessons learned leads to improved safety – no one wants to get hurt at work.
Your Week 8 assignment is to evaluate a major incident in recent history and prepare short “Lessons Learned” briefing. Examples could include a natural disaster, extreme weather event, mass casualty incident, large-loss fire, large-scale hazardous material incident, transportation disaster, terrorist event, or major wildland fire. To be considered a major incident, the incident will normally involve a large-scale response with assistance from other agencies (e.g. fire departments, Homeland Security, FBI, etc.).
The following include a list of recent disasters that you may choose to use:
• Hurricane Harvey (Tx)
• Hurricane Katrina (La)
• Hurricane Maria (PR)
• 9/11
• Tohoku (Japan) Earthquake/Tsunami
• BP Oil Spill
• 2017 Camp Fire (Paradise, California) wildfire
• 2011 tornado that struck Tuscaloosa Al
Instructions:
1. Research your chosen incident and collect the following information:
• Summary of the event (date, location, type of disaster,)
• Summary of conditions that led to the disaster. Was it safety related?
• From Emergency Preparedness perspective:Were they prepared? Did they have emergency plans? Were they effective?
• From response worker perspective: what hazards were present; was the PPE provided adequate? Was the training adequate? Have there been any lingering health effects?
• Summary of agencies involved (FEMA, OSHA, EPA, DHS, etc.)
• What changes were implemented as a result of this disaster?
2. After Action Report –
• Prepare a PowerPoint Presentation to address the concerns. Organize the presentation around the following questions:
• What was expected to happen?
• What actually occurred?
• What went well and why?
• What can be improved and how?
• Areas of grading focus will include:
• Focused Perspective–The focus of your research and your report should be from an Occupational Health and Safety perspective. The observations and conclusions should relate to the content of this course (i.e. human health hazards, protecting employees from safety and health hazards, emergency response).
• Tailored Content – Your audience will be non-scientist executives so your briefing should be written in easy to understand language suitable for that audience. Tell the story the way you would do it around the water cooler, while keeping it technically accurate.
• Appropriate Length and Organization – The material should be grouped on 7-10 slides using headings or bulleted lists (not including the title slide, overview, or summary slide). Please add supporting details (if needed) in the Notes portion of the slides.
• Credible References – Use reliable, credible references. These include federal or state government agencies, peer-reviewed articles, or industry trade resources.
• The specific grading rubric can be found in your Assignments folder.
Collepals.com Plagiarism Free Papers
Are you looking for custom essay writing service or even dissertation writing services? Just request for our write my paper service, and we'll match you with the best essay writer in your subject! With an exceptional team of professional academic experts in a wide range of subjects, we can guarantee you an unrivaled quality of custom-written papers.
Get ZERO PLAGIARISM, HUMAN WRITTEN ESSAYS
Why Hire Collepals.com writers to do your paper?
Quality- We are experienced and have access to ample research materials.
We write plagiarism Free Content
Confidential- We never share or sell your personal information to third parties.
Support-Chat with us today! We are always waiting to answer all your questions.
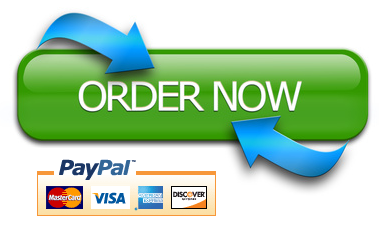