Individual Assignment This assignment is an introduction to college-level? writing. Create an journal in APA format. Check the examples in the library writing resources and brush up on w
Individual Assignment This assignment is an introduction to college-level writing. Create an journal in APA format. Check the examples in the library writing resources and brush up on writing skills. Develop an journal of two to four pages, excluding title and reference page. Create an introduction using APA section title, repeating the title page byline. Then, use 1st and 2nd level section titles to create topics from the reading. Within each section title (topic) develop journal points by combining information from two or more library articles. Select topics from the course readings. Introduce the topic by paraphrasing information from the class reading. Then, search the library for articles on the topics selected from the class reading. Paraphrasing information from resources (class material and library articles) is a good way to demonstrate understanding of course objectives. Remember to match the title page format, section titles, citations, and references in APA format. Match each type to examples in the library writing resources. APA Formatting required.
My journal will be on reverse logistic and sustainability.
Chapter 10. Reverse Logistics and Sustainability
Reverse logistics, an often overlooked process that can help companies reduce waste and improve profits, is as the name implies the reverse of what we’ve described so far in terms of planning and operations. It can be defined as the process of planning, implementing and controlling the efficient flow of recyclable and reusable materials, returns, and reworks from the point of consumption for the purpose of repair, remanufacturing, redistribution, or disposal
To take this a step further, with today’s environmental concerns, organizations need to try to integrate environment thinking into the entire supply chain process, forward and reverse. This includes product design, material sourcing and selection, manufacturing processes, delivery of the final product to the consumers and “end-of-life” management of the product after its useful life.
In a perfect world of course, there would be no need for much of the material handled in reverse logistics and later in the book we will discuss ways to use Lean thinking to reduce waste in the supply chain, but for now we will examine concepts and applications in this area.
Reverse Logistics Activities
Figure 10.1. Logistics and Reverse Logistics Processes
According to a 2010 Aberdeen Group study, the average manufacturer spends an astounding 9 to 15% of total revenue on returns [Aberdeen Group, 2010].
There are a variety of reasons for the reverse logistics process. They include:
Processing returned merchandise including damaged, seasonal, restock, salvage, recall, or excess inventory.
Green initiatives such as recycling packaging materials/containers.
Reconditioning, refurbishing, remanufacturing of returned product.
Disposition of obsolete inventory.
Hazardous materials recovery and electronic waste disposal.
So depending on the specific reasons for the process existing in the first place with in an organization, the reverse logistics network can be used for a variety of purposes such as refilling, repairs, refurbishing, remanufacturing and so on, depending on the nature of the product, unit value, sales volume and distribution channels.
Let’s look at some of the major reasons mentioned above in some more detail.
Repairs and Refurbishing
Repair is a regular feature in service based products under a warranty period and almost all consumer durables need repairs on a regular basis. Refurbishing, on the other hand, is applied to goods returned by damage, defects or below promised performance during the warranty period.
Manufacturers may establish the reverse logistics system, not only for offering free service during the warranty period but also for extending the services beyond the warranty period on a chargeable basis.
The system usually operates through the company’s service centers where repair and refurbishing takes place.
The physical collection of defective products is performed through a dealer network. The collected products are sent to the nearest service center for overhaul, repairs or refurbishing.
Re-filling
Reverse logistics is integrated to an organizations supply chain in the cases of the reusable nature of packages such as glass bottles, plastic containers, print cartridges, etc.
In case of large refillable water bottles, for example, the delivery truck delivers filled bottles to and collects the same number of empty bottles from them for delivery to the factory. No extra transportation costs are involved in the process as the same delivery truck originates and terminates its journey at the factory where these reusable bottles are refilled for re-delivery to customers.
Typically, this type of arrangement is accomplished via a “hub and spoke” distribution system (i.e. a centralized distribution system where inventory is shipped from a central location to smaller locations or directly to consumers, similar to a bicycle hub and spoke configuration).
Recall
This is an emergency situation where the products distributed in the market are called back to the factory because of any of the following reasons:
• Product not giving the guaranteed performance.
• Quality complaints from many customers.
• Defective products causing harm to human life.
• Products beyond expiry date.
• Products with defective design.
• Incomplete product.
• Violation of government regulations.
• Ethical considerations.
• Save the company image.
A product recall puts a large financial burden on a company but in the competitive scenario the companies consider “recall” as an opportunity to increase customer satisfaction.
Remanufacturing
Manufacturers in developed countries are putting in practice a relatively new concept of re-manufacturing as during the usage of the product it undergoes wear and tear. During remanufacturing, worn out parts are replaced with new ones and the performance of the product is upgraded to the level of a new one.
Similarly, equipment sold can be checked after use to the remanufacturing process and be brought back to the remanufacturing unit.
The investment in remanufacturing and related reverse logistics supply chain can be justified on the basis of economies of scale.
Recycling and Waste Disposal
Leftover materials, used product and package waste are causing environmental pollution and creating problems for disposal.
In many countries, governments are devising regulations to make manufacturers responsible to minimize waste by recycling products.
Returns Vary by Industry
In some industries, returns are the major reason for a reverse logistics system as percentages can range from as low as 2-3% (chemicals) to over 50% (magazine publishing).
Let’s look at some industries to examine why the return rates are so high.
Publishing Industry
The publishing industry has the highest rate of unsold copies (28% on average). This has been partially a result of the growth of large chain stores requiring more books and magazines. To secure a prominent display in superstores, publishers must supply large quantities of books. The fact is that superstores sell less than 70% of books they order and they have a relatively short shelf life.
Computer Industry
Computers have a relatively short life cycle so there are opportunities to reuse and create value out of computer equipment. They contain what is known as “e-waste” such as lead, copper, aluminum gold, plastics and glass. E-waste not only comes from computers but also televisions, cell phones, audio equipment and batteries.
For example in the remanufacturing of toner cartridges there are 12,000 remanufacturers, employing 42,000 workers that sell nearly $1 billion worth of remanufactured cartridges annually.
Automotive Industry
There are three primary areas for reverse logistics in the automotive industry.
1. Components in working order are sold “as is” (ex: parts from junk yards).
2. Components, such as engines, alternators, starters, and transmissions are refurbished before they can be sold.
3. Materials are reclaimed through crushing or shredding.
Automotive recyclers handle more than 37% of the nation’s metal scrap and remanufactured auto parts market is estimated at $34 billion annually.
Retail Industry
Profit margins in retail are so slim that good return management is critical as returns reduce the profitability of retailers marginally more than manufacturers. In fact, returns reduce the profitability of retailers by 4.3% [ Rogers and Tibben-Lembke, 1998 ]
Reverse Logistic Costs
Reverse logistics costs come from a variety of activities such as merchandise credits to the customers, transportation costs of moving the items from the retail stores to the central returns distribution center, repackaging of the serviceable items for resale, the cost of warehousing the items awaiting disposition and the cost of disposing of items that are unserviceable, damaged, or obsolete.
Besides those tangible costs, there are “intangibles” that greatly impact the customer such as increased customer wait times, loss of confidence in the supply system, and the placement of multiple orders for the same items.
Reverse Logistics Process
There are five steps to the product returns process, no matter what industry you are in…receive, sort and stage, process, analyze, and support [ Stock, et al, 2006 ].
1. Receive
Product returns are received at a centralized location, usually a warehouse or distribution center (usually after being gathered from retail locations or returned by the end user themselves). In many cases, a first step in this process is to provide a return acknowledgment.
The returns may arrive via many carriers and in a variety of packages, either on full pallets or individual containers.
The concept of “pre-postponement” can be useful in this process where companies such as Sauder Woodworking Company who makes ready to assemble furniture, processes returns as close as possible to the point of sale so as to determine quickly which returns were recoverable and which were not.
2. Sort and Stage
In this stage, returned products are received and sorted for further staging in the returns process.
The sorting can be based upon how the items have been returned (i.e. pallets, cartons, packets) or the type, size or number of the return. This process generally takes three days or less to accomplish.
3. Process
Returned products are then sub-sorted into items, based on their stock-keeping unit number. They can then be returned to inventory. If they are vendor returns, they are sorted by vendor.
There is usually some kind of processing station where they are process by order of their receipt, type of product, customer type or location, physical size of the items, etc.
Paperwork that came with the return is separated from the item and compared with the electronic records to identify any discrepancies.
4. Analyze
The value of the returned item is determined by trained employees to see if it should be repaired or refurbished and which are allowable versus non-allowable returns for example.
The last part of this step is the marketing of products that have been repackaged, repaired, refurbished or remanufactured, which are usually shipped to secondary markets.
5. Support
At this point, returns in good condition such as back-to-stock or -store items are returned to inventory. If the items require repair, refurbishment or repackaging, then diagnostics, repairs and assembly/disassembly operations are performed as needed.
Reverse Logistics as a Strategy
As opposed to looking at reverse logistics as a cost center to be minimized, as the reality is that it is only around 4% of total supply chain costs, some forward looking companies have started looking at it as a strategic weapon to positively impact revenue.
Using Reverse Logistics to Positively Impact Revenue
A recent UPS white paper on reverse logistics found some key areas where companies can positively impact revenue with reverse logistics activities. They are:
“ Returns-to-Revenue: Companies that ensure timely delivery and processing of returns position themselves to save more or earn more from the returned product. From refurbishing, repackaging and reselling to parts reclamation and recycling, returned products are often untapped sources for revenue. With the secondary, discount market for products continuing to grow, there is even more reasons to think about returns as revenue opportunities.
Protecting Profits: Handling returns properly and tracking all activities is critical to help companies avoid fines and penalties from various government regulatory agencies such as the FDA, the Consumer Product Safety Commission and other state and federal agencies.
Customer Loyalty: According to a nation-wide survey conducted in 2005, 95% of customers will not buy from a company if they have a bad returns experience. This, in part, explains why companies considered best in class in reverse logistics enjoy a 12% advantage in overall customer satisfaction over their competition
Disposal Benefits: Knowing what is returned and where it ends up makes it easier for companies to deal with regulatory issues and evaluate returned stock for possible secondary sales channels.
There are also other beneficial byproducts to disposing of products, such as avoiding excess inventory carrying costs, avoiding excess taxes and insurance, and managing staff levels.
Maximize Recovery Rates: Mishandled or completely misplaced returns affect the efficiency of any reverse logistics process, but it also means that products could end up a being a total loss for a company instead of an opportunity for resell or a spare parts resource.” [ Greve and Davis, 2012]
Other Strategic uses of Reverse Logistics
Reverse logistics can also be strategically used to reduce the risk from buying products that may not be “hot selling” items, by adjusting return rates based upon popularity of an item.
It can also be used to increase the switching costs of changing suppliers to “lock” customers in by taking back unsold or defective merchandise quickly, while crediting the customer without delay. Many retailers and manufacturers have liberalized their return policies in recent years due to competitive pressures. One e-tailer, www.zappos.com , even encourages returns as a way to increase customer loyalty.
Many companies use reverse logistics to clean out customer inventories, so that they can purchase more new goods. That way, fresher inventories can demand better prices, which in turn, protects margin.
Still others use reverse logistics as a form of “good corporate citizenship” using the process for altruistic reasons, such as philanthropy. These activities enhance the value of the brand and are a marketing incentive to purchase their products.
There is also the opportunity to recapture value and recover assets as in some cases a large portion of bottom-line profits is derived from asset recovery programs. The profit comes from materials that were previously discarded.
Legal disposal issues can create a concern as landfill fees are increasing and the options for the disposal of hazardous material are decreasing. So legally disposing of non-salvageable materials becomes more difficult (and may be subject to fines if not done properly). [ Rogers and Tibben-Lembke, 1998 ]
Reverse Logistics System Design
The success of reverse logistics system in achieving the desired objectives depends on the efficiency and effectiveness of a number of sub-systems. They are:
Product Location
The first step in the call back process is to identify the product location in the physical distribution system of the firm. Product location becomes more difficult after it is sold and handed over to the customer.
It is a bit easier in the case of industrial or high value products due to the limited number of customers and personal interaction with the clients due to direct selling.
Product Collection System
Once the product location is identified, the collection mechanism gets into operation.
This can be done either through company’s field force, channel members or third party. However, proper instructions have to be given to motivate the customer for returning the products.
Third parties are often used if it is not an area of expertise for a company and the third party can do it cheaper and more efficiently.
For example, “ Best Buy [a major electronics retailer] created a business unit…to focus on developing sales of consumer electronics into the secondary markets…No longer was the handling of customer returns, return to vendor and overstock a cost center sitting in a dark corner, but now it was transformed into a profit center…at Best Buy, maximizing profit in the reverse logistics business is involving partnerships with both new and existing customers as well as manufacturers and third party service providers (3PSPs).
Online stores & Auctions – with product testing, inventory management, listing, payment collection and order fulfillment, Best Buy has built an integrated supply chain to take returned product from the stores and resell it to its value-seeking customers through eBay, a private online store and other online channels. Best Buy recently acquired Dealtree, its provider of these services.
Trade-in, an online program was launched in 2007, offering customers a fast and easy alternative to selling online themselves, or just letting working products sit in a drawer. It allows customers to recapture economic value, and through the Dealtree technology, Best Buy has instant access to current market value of products.
Refurbishment – working with a variety of 3PSPs, Best Buy has been integrating refurbished products into its warranty replacement program and selling direct to consumers.
Recycling – in 2008, Best Buy began testing offering free recycling in several markets. They have been building up a network of local certified recyclers and plan to roll nationwide in 2009.” [ Reverse Logistics Magazine Staff, 2009 ]
Recycling or Disposal Centers
These may be the company’s plants and warehouses or some fixed location in the reverse logistics network.
The called back products are inspected before they are further processed for further repairs, refurbishing, remanufacturing or waste disposal.
Investments in facilities for these activities depend on the objectives of the system, cost implication, complexity of the operations and expected gains.
Documentation System
Tracing the product location becomes easier if proper documentation is maintained at each channel level. However, at the time of handing over the product to the customer, the detailed information if collected through proper documentation, can form a good database that can be used in case of product call backs
Reverse Logistics Challenges
There are many challenges to running and maximizing the efficiency of the reverse logistics process. They include:
Retailer – Manufacturer Conflict
There may be inefficiencies in a reverse logistics process that can lengthen the time for processing returns such as the condition and value of the item and the timeliness of response. The buyer and seller have to develop a good working partnership to derive mutual benefit.
Problem Returns and their Symptoms
Unprocessed returns are easy to observe but some of these other symptoms are not as easily observed such as:
Returns arriving faster than processing or disposal.
Large amount of returns inventory held in the warehouse.
Unidentified or unauthorized returns.
Lengthy processing cycle times.
Unknown total cost of the returns process.
Customers have lost confidence in the repair activity.
Lack of information about the reverse logistics process can result in the process being out of control. As the saying goes “if you aren’t measuring it, you can’t manage it”.
Cause and Effect
Poor data collection can lead to uncertainty about return causes. By improving the return process, it is possible to decreases costs. It is important to be able to see defective product by problem code in an information system making it possible to track return issues.
Reactive Response
In recent years, government regulation or pressure from environmental agencies has forced companies to begin to focus on an area that is not one of their core competencies. It has not been possible to justify a large investment in improving reverse logistics systems and capabilities. Some have been able to see it as a “win-win” game by developing strategies mentioned previously such as good corporate citizenship and recapturing value and recovering assets.
Overall, in many companies, there has been management inattention and the lack of importance of reverse logistics especially handling returns and non-salable items, resulting in restrictive policies in this regard. This may be in part due to not wanting their returns being used to cannibalize existing sales. Recently, there seems to be a trend toward reducing or eliminating restrictive policies and attempting to handle returns more effectively in order to recover value from what can be a valuable resource. [ Rogers and Tibben-Lembke,1998 ]
Managing Reverse Logistics
A research team at the Reverse Logistics Executive Council [ Rogers and Tibben-Lembke,1998 ] identified key reverse logistics management elements examined the return flow of product from a retailer back through the supply chain toward its original source, or to some other disposition (see Figure 10.2 ).
Figure 10.2. Key Reverse Logistics Management Elements
These elements, depending on how they are handled, can either positively or negatively impact a company’s profitability. The elements are:
Gatekeeping
Gatekeeping is the screening of defective or unwarranted returned merchandise at into the beginning of the reverse logistics process.
It is the first critical factor to ensure that the entire reverse flow is both manageable and profitable. In the past, companies have put most resources into the forward logistics process and have given very little time and effort into the reverse process.
While liberal return policies, like those at L.L. Bean, Walmart and Target may draw customers, they can also encourage customer abuse such as the return of items lightly used for an event or one occasion.
So it is important to have a solid gatekeeping process. For example, the electronic gaming company Nintendo will rebate retailers if they register the game player sold to the consumer at the point of sale. By doing this, Nintendo and retailers can determine if the product is under warranty, and also if it is being returned inside the allowed time window. The impact pact from this new system on their bottom line was substantial: an 80% drop in return rates
Compacting the Distribution Cycle Time
One of the major goals of the reverse logistics process once an item has entered it is to reduce the amount of time to figure out what to do with returned products once they arrive. This includes return product decisions, movement, and processing.
So it is important to know beforehand what to do with returned goods. When material often comes back in to a distribution center, it is not clear whether the items are: defective, can be reused, or refurbished, or need to be sent to a landfill. The challenge of running a distribution system in reverse is difficult…employees have difficulty making decisions when the decision rules are not clearly stated and exceptions are often made.
Reverse Logistics Information Technology Systems
One of the most serious problems that the companies face in the execution of a reverse logistics is the scarcity of good information systems. To work well, a flexible reverse logistics information system is required.
The system should create a database at store level so that the retailer can begin tracking returned product and follow it all the way back through the supply chain.
The information system should also include detailed information programs about important reverse logistics measurements, such as returns rates, recovery rates, and returns inventory turnover.
Useful tools such as radio frequency (RF) are helpful. New innovations such as two-dimensional bar code and radio frequency identification license plates (RFID) may soon be in use extensively.
Centralized Return Centers (CRC)
Having centralized return centers (CRC) can offer many benefits to an organization, including:
Consistency in disposition decisions and minimizes errors.
A space saving advantage for retailers who want to dedicate as much of the shop floor to salable merchandise as possible
Labor cost reductions due to their specialization, as CRC employees can typically handle returns more efficiently than retail clerks can.
Transportation cost reductions as empty truckloads returning from store deliveries are used to pick up return merchandise.
A convenient selling tool for the easy disposition of returned items. This can be an appealing service to retailers, and may be a deal-maker for obtaining or retaining customers.
Faster disposition times allow the company to obtain higher credits and refunds, as items stay idle for smaller periods of time, thus losing less value.
Easier to identify trends in returns, which is an advantage to manufacturer who can detect and fix quality problems sooner than if these returns were handled entirely by customer service personnel.
Zero Returns
A company may have a program that does not accept returns from its customers. Rather, it gives the retailer an allowable return rate, and proposes guidelines as to the proper disposition of the items. Such policies are usually accompanied by discounts for the retailer.
This type of policy passes the returns responsibility onto the retailer, while reducing costs for the manufacturer or distributor.
The drawback is that the manufacturer loses some control over its merchandise.
Remanufacture and Refurbishment
The advantage of remanufacturing and refurbishment is using reworked parts resulting in a cost savings.
There are five categories of remanufacture and refurbishment:
Make the product reusable for its intended purpose:
1) Repair
2) Refurbishing
3) Remanufacturing
Retrieve reusable parts from old or broken products:
4) Cannibalization
Reuse parts of products for different purpose:
5) Recycling
Asset Recovery
Asset recovery is the classification and disposition of returned goods, surplus, obsolete, scrap, waste and excess material products, and other assets. It tries to maximize returns to the owner, while minimizing costs and liabilities for the dispositions.
The objective of asset recovery is to recover as much of the economic (and ecological) value as is possible, thus reducing the final quantities of waste.
This can be a good cash generating opportunity for companies who can sell these goods that would be otherwise end up in landfills.
Negotiation
Negotiation is a key element for all parties of the reverse logistics process. Because of the inherent lack of expertise on product returns, negotiations usually are informal and approached without formal pricing gu
Collepals.com Plagiarism Free Papers
Are you looking for custom essay writing service or even dissertation writing services? Just request for our write my paper service, and we'll match you with the best essay writer in your subject! With an exceptional team of professional academic experts in a wide range of subjects, we can guarantee you an unrivaled quality of custom-written papers.
Get ZERO PLAGIARISM, HUMAN WRITTEN ESSAYS
Why Hire Collepals.com writers to do your paper?
Quality- We are experienced and have access to ample research materials.
We write plagiarism Free Content
Confidential- We never share or sell your personal information to third parties.
Support-Chat with us today! We are always waiting to answer all your questions.
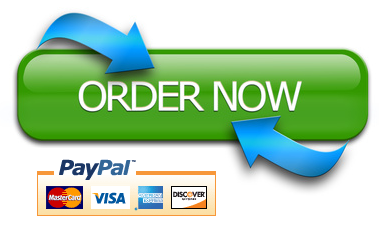