Read ‘It all Ties Together’: Define the key steps in their improvement project including key steps and tools. What is the purpose of each step? Specifically, how does CSX monetize their sustai
1. Read "It all Ties Together": Define the key steps in their improvement project including key steps and tools. What is the purpose of each step? Specifically, how does CSX monetize their sustainability improvements (i.e. not simply reduced fuel consumption, what operational changes were necessary)?
2. Read "TTR Presentation": Define the key steps in their improvement project including key steps and tools. What is the purpose of each step? Specifically, how does TTR monetize their sustainability improvements (i.e. not simply reduced energy consumption, what operational changes were necessary)?
Citation back to the article, around 400 words each question
1
��������� �� ����������
Project Duration: Aug 03 – Aug 04
2
3
• Joint Venture between Partners Tata Auto Components (TACO): 51% Toyo of Japan: 40.25% Mitsubishi Non Ferrous of Japan: 8.75%
• Equity Base US $ 6.95 million
• Initial Project Cost US $ 11.3 million
• Integrated Plant Facility • Equivalent Capacity
625,000 Heat Exchangers • No. of Employees: 221 • Land : 7 Acres • Plant : 100,000 sq.ft.
� � � � �� � �� ��� � �� � � ���� � ������ ����
Tata Toyo Radiators today is one of the largest manufacturers of
Heat Exchangers in India.
4
• Integrated Plant Facility
Press, Tube Mill, Fin Forming, Degreasing,
Core Assembly, Brazing Oven, Tank Clinching &
Leak Testing
• Products
Aluminum Brazed Radiator, Intercooler,
Heater Core, Condenser
��� � � �� �� ��� ����� ���
5
Acknowledgements ����� �� ��
This report presents the work done by the team for reducing energy consumption and improving brazing oven productivity.
Energy conservation has been an integral effort for Tata Toyo Radiators (TTR) since its inception in 1998. This Six Sigma project, undertaken in 2003-04, assisted in channeling the efforts of team members through a structured and systematic data driven approach for enhancing productivity, planning, and energy planning.
We would like thank our management champion, Mr. R. Sundar, CEO, for providing us guidance and support for moving this project forward. We would also like to express our thanks to Mr. A. Alur & Mr. R. Shete. Our special thanks to the technical advisors of Toyo Radiators, Japan, and also to the management and the board members of Tata Auto Comp Systems (TACO), the parent company of TTR, for supporting the Six Sigma movement in TTR.
6
Summary of Project Achievements � ��� � !������ �� ��
28 % reduction in energy consumption levels. Energy levels were reduced from about 9.87 kwh / equivalent heat exchanger between April 02 and July 03 (16 months data) to about 7.05 kwh / equivalent heat exchanger between Jan 04 and Aug 04 (8 months data).
Hard savings of Rs 5.5 million / year or US $ 122,200 / year are achieved based on 2004 – 05 actual volumes.
The “Actual” energy cost per equivalent heat exchanger paid by TTR’s finance department to the electric power company dropped from about Rs 48 per heat exchanger between April 02 and July 03 (16 month data) to about Rs 30 per heat exchanger between Jan 04 and Aug 04 (8 months data) – tremendous achievement.
7
Summary of Project Achievements
Productivity Improvement:
Brazing oven productivity increased 42 % from 76 equivalent heat exchangers in July / Aug 03 to 108 equivalent heat exchangers in Jan to Aug 04.
� ��� � !������ �� ��
8
��������� �" � � ��
Project Statement : – The present energy consumption for “Entire
TTR Factory” is about 4577318 kilo watt hour (kwh) while producing 463729 equivalent heat exchangers. This gives us an energy consumption level per radiator of 9.87 kwh / heat exchanger.
This is based on 16 months of data (April 02 to July 03)
Note
� ��� � !�# � �" ����$!%�
9
��������� �" � � ��&&&
• Project Objective: – To reduce the plant energy consumption level by about 2 kwh /
equivalent heat exchanger, i.e., reduce current levels from about 9.87 to 7.9 kwh / rad by 31 Dec 03. This will result in hard recurring energy savings of about Rs 4 Million / year (US $ 88,800) based on 2004 annual volumes.
Equivalent Heat Exchangers = 1*Radiator volumes + 1.5 * Intercooler volumes + 1/6 * Heat Core Volumes
� �" ����$!%�
Concept of Equivalent Heat Exchanger: Intercoolers are about 1.5 times the size of radiators and heater cores are about 1/6 times the size of radiators. The following equivalent heat exchanger formula was used for this project:
10
��������� �" � � ����' �!% ����$!%��
02-03 Apr-Jul 03
9.82 9.9
Kwh /eq heat exchanger
9.0
9.5
10.0
8.5
8.0
7.5
Aug Sept Oct Nov Dec Jan 04 Feb Mar
Target: 7.9 Target: 7.9 KwhKwh / / radrad
Expected Savings of
RsRs. 4 . 4 Million / yrMillion / yr
Before Project Data Energy Consumption between Apr 02 to Jul 03 is 9.87 Kwh / rad
11
��������� �" � � ��&&&
•• Expected Date to complete DMAI Phases: Expected Date to complete DMAI Phases: On / before 30 Nov 2003 On / before 30 Nov 2003
•• Expected Date to complete Control Phase: Expected Date to complete Control Phase: On / before 31 March 2004On / before 31 March 2004
A Team Commitment
� �" ����$!%�
12
Tube Mill Machine
Press 1 Press 2 Press 3
Fin Forming Machine
Plastic Tank & O Ring
( �!�����$!�����' !� "!�� � ��������%%��)�* ��$!��
Testing
Tube weld Tube mill Cut to size
Degrease
Clinching
Fitment of drain plug, pressure
cap etc
Packaging and Dispatch
Leak Testing
Fin Forming Cut to size
Core Assembly
Brazing Area
Header Plate Core Support
� �" ����$!%�
13
�������� !�!���))��� ���+��� ��!%��� ,� )�# – )��./�
Brazing FDV
612000
123000
Kwh
600,000
Air Comp
Others
500,000
400,000
300,000
200,000
100,000
119700
Tube Mill
70320
Pump House
48180
Admin Bldg
27820
Fin Forming
26240
Press
20000
Pareto Analysis
� ��� � !�' �!% ����$!%�
Main Focus Area:
Brazing Area
Secondary Focus Areas:
FDV (Ventilation System), Air Comp (Air Compressor), and Pump House
�!) +�!�� �������� ����%�* ���� �%�!))� � !��0!� � %����% ,� ���,� ��%��%���+�)�* �� !� � �!% �� ���%�* �����!1���+��* ���� � ,� )�!� �- )��./
14
����������� %
Tata Toyo Radiators (TTR)
Brazing Area
Force Draft Ventilation
(FDV)
Air Compressor (Air Comp)
Tube Mill
Pump House
Admin Bldg Fin Forming Press
Tank Clinching and Leak Testing
IC
' ! ������������% ,� ���� ��!%�"���� � �
Based on Pareto Analysis, project will focus primarily on ‘Brazing Area’ and secondarily on areas like FDV, Air Comp, Tube Mill and Pump House
15
' �!% ����$!%�
� , !�� ���������� +���� 0�
� %�%����"�� ��$���!������ �!)�% %2��$����! �%�!��� �"�� %% ��� ����$��+�!3 ���!��!2�!%� �����% � �!) �%��4.�5 ��"����!)�,)!��6% ������&
� $ %�)� �����$����! � �� ��� "� ���+�!3 ����0���,�� �� 0 ���!% �����"��$��1���"!����%� ���� � ����������)�0�)%&
��� �� 0 ���� �!% �� � ���7 0!)����$�!�����$!����%�,���$� �� �$�� �$��$��+�!3 ���!��!�� ��- )��# � � %��./�* !%� �!% �� � !�� � �89&�� $����! � �� � ���� ����!%���$ %�" � ������!�� � � :.��7 0!)�����! !���%�,���$� ��+��� ���./&��"�* ���� ) � !�$ �0���$ %2��$��1* $ ;�$�!�����$!�����* � ) ��� �� �* �2�!%�* �� �� ) ���* �,����%%� ����,�� ����$�� �$��$��+�!3 ���!��!� ��!� %$������� ��%,!�2��$���+���� � �������������% ,� ���,��� $�!�����$!����&�
16
' �!% ����$!%� <=�"���>���������� !�!�
Plant Energy Levels
July – Aug 03
76
90
100
110
80
70
60
Target = 90
Brazing Area Productivity Levels
Productivity figures include change over times, however, exclude planned shut downs
02-03 Apr to July 03
9.82
Kwh / Equivalent Heat Exchangers
8.5
9.0
9.5
8.0
7.5
7.0
Target = 7.9
10.0 9.9
Kwh / Equivalent Heat Exchangers
17
=�!3 ���� ��!��)�* �� !��!
Burn Off Fluxing Dry Off 1 Dry Off 2
Brazing Oven Cooling Section
7.5 kw blower motor
12 heater, 10 kw each. Total = 120 kw load (t Deg C)
7.5 kw blower motor 7.5 kw blower motor
12 heater, 10 kw each. Total = 120 kw load
9 heater, 9 kw each. Total = 81 kw load
8 top and bottom zones. 8 Heaters = 360 kw. Varying from t1 to t2 Deg C
Product must reach T +/- T1 Deg C for minimum ‘x’ minutes
7.5 kw blower motor
7.5 kw exhaust system blower
� �!)�3���$!%�
The ‘Brazing Oven’ is the biggest source of energy consumption in the Brazing Area.
18
� ���� !)�? �* ��"��$��=�!3 ���� ��! � �!)�3���$!%�
Temp Zone 1
Temp Zone 2
Temp Zone 3
Brazing Oven Cooling Section
Burn Off, Fluxing and Dry Off
Start to Finish Length of the Brazing Area: 46 meters
19
� %� ����! %�%��@ %� • After many brainstorming sessions the team identified the
following causes for “High Energy Consumption” for the areas highlighted in the Pareto Analysis. Causes for “Lower Productivity in Brazing Area” were also brainstormed.
Wherever possible, the team attempted to quantify financial losses per individual causes. Simultaneously, counteractions for the causes were also brainstormed. Approximate costs for implementing counteractions were also discussed for management to take immediate decision.
� �!)�3���$!%�
20
� %���"�A����! %�%�!� ��� ����!�� ��% Area Causes & Losses in Rs
Million per yr Counteractions
Burnoff • Burnoff ‘ON’ during heater core brazing (Rs 0.314 M/yr)
• Inadequate utilization due to frequent temp / speed changes (Rs 0.214 M/yr)
• Shut off burnoff as last radiator exits before HC starts
• See “Brazing Oven” section
Fluxer • Fluxer ‘ON’ during heater core brazing (Rs 0.011 M/yr)
• Inadequate utilization due to frequent temp / speed changes (Rs 0.015 M/yr)
• Fluxer Breakdown (Rs 0.2 M/yr)
• Fluxer nozzle setting problem
(Rs 0.15 M/yr)
• Shut off burnoff as last radiator exits before HC starts
• See “Brazing Oven” section • Keep spare fluxer balls. Spare kit for
fluxer pump • Procure and install video camera in
the fluxer area to assist the loading operator
� ��� � !�# � �!)�3��;�� ,��0���$!%�
Detailed calculations for ‘financial losses’ are available
Note
21
Area Causes & Losses in Rs Million per yr
Counteractions
Dry Off • Inadequate utilization due to frequent temp / speed changes (Rs 0.4 M/yr)
• Air Blower not functioning properly (Rs 0.075 M/yr)
See “Brazing Oven” section • Procure bearing and other motor spares
Cooling Section
• Muffle between oven and cooling section has no insulation, causing heat loss
• Air blower remains
‘on’ during idle condition changes (Rs 0.03 M/yr)
• Insulate muffle • Modify current circuit
� �!)�3��;�� ,��0���$!%�
� %���"�A����! %�%�!� ��� ����!�� ��%
22
Area Causes & Losses in Rs Million per
yr
Counteractions
Brazing
Oven
Production Schedule
• Inadequate utilization of brazing oven due to frequent speed and temperature changes (~ Rs 2 M / yr)
• Pitch not
optimized, leading to lower radiator output per hour
• No systematic
plan for feeding the clinching line, leading to higher number of changes for the brazing oven
• Commonization of temp for at least 80 % of all products. • Commonization of s1 brazing conveyor speed and speed
increase for double row cores up to truck model • Commonization of conveyor speed for 43 mm and 65 mm
intercoolers at s2 mm/min • Zig zag loading of Sumo / Safari intercoolers, hereby increasing
output for different mm radiator cores • Increase conveyor speed for18 mm cores from s3 to s4 mm/min
and heater core speed from s5 to s6 mm/min • Decrease product pitch on conveyor for Sumo and Indica type
radiators. Decrease Sumo pitch from p1 to p2 mm and Indica pitch from p3 to p4 mm; helped increase output by about ‘x’ eq heat exchangers / hr
• Daily production schedule indicating sequence of production
was developed by the team • Adhering to the scheduled plan would lead to reduction in
number of changes in the brazing oven, leading to better utilization of the brazing oven
� �!)�3��;�� ,��0���$!%� � %���"�A����! %�%�!� ��� ����!�� ��%
23
Area Causes & Losses in Rs Million per yr
Counteractions
Brazing Area
• Brazing conveyor running at Sx mm/min during idle condition
• Core Band Shortages (Rs
0.49 M / yr)
• Reduced conveyor speed to Sy for idle condition reducing heat loss and switched off blower during non-brazing time (by introducing new electrical logic)
• Procured new core bands
Force Draft
Ventilation System (FDV)
• FDV does not have a cut off timer, thus many times FDV keeps running during the night also (when not actually needed) (Rs 0.16 M / yr)
• Exhaust fans do not start automatically after power failure
• Install 6 timers on FDV • Circuit modification
Employees • Employees’ involvement and awareness for energy conversation
• Generated operator awareness for energy / utility cost. Mr. Purandhare, an energy conservation expert, conducted “Energy Conservation Awareness” program for the factory on 15 Nov 03.
• Also the team initiated a poster campaign in TTR.
� �!)�3��;�� ,��0���$!%� � %���"�A����! %�%�!� ��� ����!�� ��%
24
Area Causes & Losses in Rs Million per yr
Counteractions
Air Comp • Press drop due to leakages in air comp line
• Due to inadequate brazing oven utilization, more use of comp air
• Fix leakages • Reduced brazing oven running hours. This
reduced load on air compressor, saving money
Core Assy & Clinching
Admin Building
• Hydraulic power packs remain “ON” during lunch and changeovers (Rs 0.17 M / yr)
• Electrical heating elements are
used to heat food in cafeteria
• Completed work instructions and conduct operator awareness session for shutting power packs during lunch, tea breaks, and dinner
• Install solar heating system
(payback period is about 8 months)
Pump House • Pumps operate continuously during no-production time as the pump switches are located far away from production area (for example tube mill area)
• Provided remote switches for tube mill pumps (near machine control board)
� �!)�3��;�� ,��0���$!%�
� %���"�A����! %�%�!� ��� ����!�� ��%
25
For improving brazing oven utilization, around 25 planned experiments were conducted over a period of about a month. Heat Exchanger cores with temperature loggers (profilers) connected to cores were passed through the brazing oven for recording the temperatures that the cores were actually attaining when the cores were actually passing through the various heating and cooling zones in the brazing oven. Brazing zone temperatures, speeds, and pitch were systematically varied and the actual core temperatures (on three places on the radiator core) were measured and analyzed.
Through these experiments, we successfully commonized temperatures, speeds, and optimized pitch for about 80 % of heat exchangers manufactured by us. This, along with other improvement actions, led to a 42 % improvement in brazing oven output, thereby reducing energy cost per heat exchanger core.
� �!)�3��;�� ,��0���$!%�
���0������ ,�� 2�=�!3 ���� � ,��!� ��2�!� �� ��$�� � ,� 3!� �����,�� ���%
26
=�!3 ���� � ,2����0������ ,�� 2�!� �� ��$�� ,� 3!� ��� ��,�� ���%
Radiator cores moving on the brazing oven conveyor just before entering the brazing oven
Speed of ConveyorRadiator Core
� ,��0���$!%�
Pitch
27
=�!3 ���� � ,2����0������ ,�� 2�!� �� ��$�� ,� 3!� ��� ��,�� 
Collepals.com Plagiarism Free Papers
Are you looking for custom essay writing service or even dissertation writing services? Just request for our write my paper service, and we'll match you with the best essay writer in your subject! With an exceptional team of professional academic experts in a wide range of subjects, we can guarantee you an unrivaled quality of custom-written papers.
Get ZERO PLAGIARISM, HUMAN WRITTEN ESSAYS
Why Hire Collepals.com writers to do your paper?
Quality- We are experienced and have access to ample research materials.
We write plagiarism Free Content
Confidential- We never share or sell your personal information to third parties.
Support-Chat with us today! We are always waiting to answer all your questions.
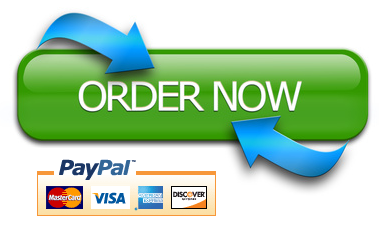