Does it matter what people wear to the office? You’ve never thought about that question before. When you first started at your architectural firm
Does it matter what people wear to the office? You’ve never thought about that question before. When you first started at your architectural firm—more than 40 years ago now—everyone dressed formally. And it wasn’t just to the office; you remember when families dressed in their best clothes to go to the movies, go out to dinner, and take an airplane flight. When you look around your office lately, it’s quite a different scene. There are interns wearing T-shirts and jeans and mail clerks wearing flip-flops. There are folks sitting at their desks wearing shorts and sneakers. Even most of your managers take advantage of the business casual look, preferring polos and khakis to the three-piece suit that you wear every day.
In the past, on most issues, you’ve given the employees whatever they wanted, so long as they produced good work. You always tried to keep them satisfied and happy in order to create a dynamic, creative environment that produced stunning, innovative building designs. You wonder, however, if things have gotten a bit too casual. It seemed okay when the men in your office wore a jacket and pants with no tie. But really—a T-shirt and jeans? A sweatshirt? A dress that basically looks like a muumuu? And it seems that casual clothing has led to a casual atmosphere. Sometimes you walk into the office to see all the people milling around, chatting, and laughing, and it looks more like a social hour than a place of business.
Apparently, other business owners and managers have similar concerns. According to research data, the number of companies that are allowing business casual throughout the week actually fell. Even the number of companies that are allowing casual Fridays fell by 5 percent. UBS, a Swiss bank, is taking things one step further. Not only did it institute a dress code, but it also gives every employee a 43-page guidebook that is filled with fashion and grooming tips. The guide even prescribes how employees should apply makeup, how often they should get their hair cut, and how to avoid having bad breath (Hint: no onions or garlic!).
Is it time to make a switchback? True, it’s not as if an architect needs to wear a suit and tie to do his or her work well. But at the same time, you’d like to remind your employees that the office needs to be more about work than comfort and fun.
Questions: What are the advantages and disadvantages of having an informal workplace? What are the advantages and disadvantages of having a formal workplace?
In your post please provide at least two APA references to support your answer (You can utilize the textbook). You can utilize the Purdue Online Writing Lab (OWL) (Links to an external site.)website for the correct way to reference the articles used.
DQ2 What Would You Do?
Prior to the completion of this discussion board post, please review:
Reading: Chapter 10 Managing Teams pg. 206
Chapter 10 Managing Teams PowerPoint Presentation Preview the document
Background: Cessna
The words “Cessna Skyhawk” have special meaning for anyone who has ever wanted to learn to fly. At 27 feet long and 8 feet tall, with a 36-foot wingspan, a 140 mph cruising speed, and room for two adults and their luggage, more people have learned to fly with a Cessna Skyhawk than with any other plane in aviation history. In fact, the Cessna Skyhawk is the best-selling plane of all time. Clyde Cessna built his first plane in 1911, and Cessna became a storied name in aviation. Cessna built 750 gliders for the army in World War II, introduced the Skyhawk in 1956, produced the first turbo-charged and cabin-pressurized single-engine planes in the 1960s, delivered its first business jet in the 1970s, topped $1 billion in sales in the 1980s, and then, in one of the worst downturns in the history of the aviation business, nearly went out of business over the next decade and a half.
Sales of general aviation aircraft, which had topped out at 17,000 planes per year, dropped to 12,000 planes within a year, and over the next decade finally hit rock bottom at 928 planes for the entire industry. During the same time, Cessna’s sales of piston-engine planes, like the Skyhawk, dropped from 8,000 per year to just 600. Cessna was forced to lay off 75 percent of the employees at its piston-engine plane factories (Cessna also makes business jets and larger planes) and eventually stopped making piston-engine planes altogether. However, after the economy improved and the U.S. government approved the General Aviation Revitalization Act (barring product liability lawsuits on any plane over 18 years old), Cessna decided to start building its legendary Skyhawks again.
This is where you come in. With nearly 20 years in the company, your first job with Cessna was teaching Cessna dealers how to service and maintain single-engine planes. But now, with profits flowing again and the company’s legal risk greatly reduced thanks to the Revitalization Act, you’ve been made the vice-president of Cessna’s “new” single-engine business. It’s your job to rebuild this part of the business from the ground up. And because pilots tend to remain loyal to the kind of airplane on which they learned to fly, much depends on your success or failure. If you can rebuild Cessna’s single-engine business, the pilots that learn to fly on today’s Cessna Skyhawks will be buying Cessna business jets 20 years from now.
One of the advantages of starting completely over is that you get to design the entire production facility, from its location to the new workers, to the suppliers, everything is up for grabs. For instance, Cessna does most of its production in Wichita, Kansas. But since it left the single-engine plane business, Wichita mostly produces a small number of highly customized jets each year, just the opposite of your business, which is a high number of standardized, single-engine planes. So, given the differences, you locate the new single-engine plane factory in Independence, Kansas, two hours away by car, and only 40 minutes away in one of Cessna’s small planes. Along with a new location, you’re debating taking a new approach to manufacturing planes by using production teams. This decision may strike some colleagues as radical, particularly at conservative-minded Cessna where, one of your fellow managers admitted, “we probably got into a mode of doing things for the future based on how we’d always done things in the past.” But the more you think about it, the more you are convinced that it is the right decision. Instead of using a standard production line where each worker does just one task, you are thinking about using teams to assemble Skyhawks and other single-engine planes. In an incredible departure from the engineering-based standards in which the motions of every worker on the assembly line are studied for a time, cost, and efficiency implications, production teams would be completely responsible for assembling the planes and for costs and quality.
You expect to see several benefits from a team-based approach, increased customer satisfaction from improved product quality, faster, more efficient production, and higher employee job satisfaction. A few things worry you, however. Despite all of their promise, teams and teamwork are also prone to significant disadvantages. They’re expensive to implement. They require significant training. And they only work about a third of the time they’re used. So, despite their promise, you can’t ignore the reality that using teams would be quite risky for Cessna.
Still, you can’t help thinking that teams could pay off and that there might be ways for you to minimize the risk of failure. For example, because the plant will be in a new location, Independence, Kansas, you get to start with a brand new workforce. What kinds of people should you hire for teamwork? What kinds of skills and experience will they need to succeed in a team environment? If you decide to take the plunge and use teams, how much authority and responsibility should you give them? Should they be limited to just advising management, or should you make them totally responsible for the quality, costs, and productivity? Finally, while you’re considering using teams on the assembly line, are there other places in which you might use teams? Not all teams are alike. Maybe there are other places in which teams could contribute to the success of Cessna’s “new” single-engine plane-manufacturing facility?
Question: If you were in charge of Cessna’s “new” single-engine factory, what would you do?
In your post please provide at least two APA references to support your answer (You can utilize the textbook). You can utilize the Purdue Online Writing Lab (OWL) (Links to an external site.)website for the correct way to reference the articles used.
Collepals.com Plagiarism Free Papers
Are you looking for custom essay writing service or even dissertation writing services? Just request for our write my paper service, and we'll match you with the best essay writer in your subject! With an exceptional team of professional academic experts in a wide range of subjects, we can guarantee you an unrivaled quality of custom-written papers.
Get ZERO PLAGIARISM, HUMAN WRITTEN ESSAYS
Why Hire Collepals.com writers to do your paper?
Quality- We are experienced and have access to ample research materials.
We write plagiarism Free Content
Confidential- We never share or sell your personal information to third parties.
Support-Chat with us today! We are always waiting to answer all your questions.
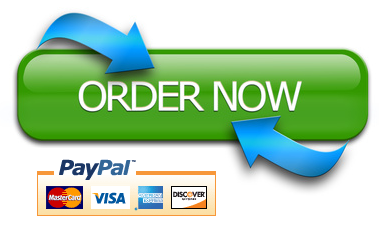