Review job leads with client. What process metrics are used in this process??Process metrics used in this process include assessing time (applicant-to-new hire conversion and applica
Welcome to Week 3! Below is my (1) value stream map from a project conducted in Austin, Texas, and (2) Week 3 DQ responses. My focus will be on Process Block 3 – Review job leads with client.
- What process metrics are used in this process? Process metrics used in this process include assessing time (applicant-to-new hire conversion and applicant-to-new hire).
- Describe any shortcomings such as delays, bottlenecks, or quality issues in the process. Within Process Block 3 - Review job leads with client, the issues are (1) delays due to juggling other priorities, (2).rework due to lack of clarity from the business, and (3) rework due to outdated jobs. Other issues include no standard approach in finding job leads and difficulty with finding jobs that match the individual's skills, background, and ability.
Post your initial response by Wednesday, midnight of your time zone, and reply to at least 2 of your classmates' initial posts by Sunday, midnight of your time zone.
Have a wonderful week!
All the best,
Professor Chin
References
1. JWI550 Operational Excellence Lecture Notes. www.blackboard.strayer.edu
2. K. Martin et al. 2014. Value Stream Mapping.
1st person to respond to is Faith
Hello Professor and class on my journey through operational value stream used to serve customers using performance metrics, I would use the system known as KPIs (key performance indicators) to measure how a task is performed and if the goals are being meet. By using this system, it will give me relevant and attainable information. Tracking performance metrics provides a way for me to measure growth and development. Tracking performance metrics can drive planning for improvements, adjustments and changes to a business's process to meet goals. Employee performance methods determine the employees’ productivity and efficiency in reaching established benchmarks that contribute to the overall growth of a business. Tracking employee performance metrics helps managers can influence adjustments or make necessary improvements to help employees reach their work goals. Using this method there will be different things I would be tracking quality to measure the quality of the employee performance to make sure great customer service is given, efficiency, and productivity. One of the shortcomings I think this plan would have been not always acting on it. KPIs can shape strategy and inform fact-based decision making inside businesses but only if those inside the business put the plan in motion. We as leaders always have the great ideas, but often time we do not fully go through with the plan, so then it becomes a waste of the people time and the company’s money. We also need to make sure that we challenge and always update the KPIs. Once the right KPIs have been designed, they are often never questioned or challenged in terms of whether they remain relevant, linked to strategy or continue to help the business be successful. It is important to make sure that you are always collecting the right information, collecting it often enough and are using what you collect. We need to make sure we always utilize the information that we have found.
www.indeed.com/career-advice/career-development/key-performance-indicators
JWI 550: Operational Excellence Week Three Lecture Notes
LinkedIn Learning: Value Stream Analysis
2nd person to respond to is Katrina
Hello Professor Chin and class
What process metrics are used in this process?
The process metrics used in this process are the assessment of time and how long it takes to complete the inspection and how long it takes to get the necessary parts from the supply.
Describe any shortcomings, such as delays, bottlenecks, or quality issues in the process.
Some of the shortcomings are bottlenecks, manning issues, and supply challenges. We tend to find ourselves with more aircraft to fit in the inspection process than we have space and manning allocated. On top of this, we face supply issues that hinder the inspection lead times and give a higher number of work-in-process (WIP) aircraft than we are allowed. All these delays create a bottleneck of aircraft within different stages of work.
- Roy D. Shapiro. September 12, 2013. Process Analysis.
Regards
Katrina
© Strayer University. All Rights Reserved. This document contains Strayer University Confidential and Proprietary information and may not be copied, further distributed, or otherwise disclosed in whole or in part, without the expressed written permission of Strayer University.
JWI 550 (1208) Page 1 of 14
JWI 550: Operational Excellence
Week Three Lecture Notes
© Strayer University. All Rights Reserved. This document contains Strayer University Confidential and Proprietary information and may not be copied, further distributed, or otherwise disclosed in whole or in part, without the expressed written permission of Strayer University.
JWI 550 (1208) Page 2 of 14
HOW WORK GETS DONE What It Means In operations, the term process refers to how work flows from a specific input to a specific output. Process mapping, like value stream mapping, utilizes diagramming techniques to support three objectives that are part of any pursuit of operational excellence: (1) defining the beginnings and ends of the processes for which you and your team are responsible, (2) clarifying all the steps that take place between the starts and ends of those processes, and (3) identifying opportunities to improve processes within the value stream. Why It Matters
• You and your team need to define exactly what you are responsible for delivering and at what stage each deliverable gets handed off to the next team.
• It forces you to document and validate exactly what is currently happening in each process and not make assumptions about specific tasks in the work flow.
• It provides a clear visual tool to begin exploring individual discrete processes to test for weaknesses, and it is the basis from which you will establish baseline metrics to gauge future improvements.
“Assume you get a new job, whether it is in sales or manufacturing or anywhere, the
best thing you can do for yourself is to get a good handle on how what you are
responsible for works…and the best way to do that is to process map.”
Jack Welch
© Strayer University. All Rights Reserved. This document contains Strayer University Confidential and Proprietary information and may not be copied, further distributed, or otherwise disclosed in whole or in part, without the expressed written permission of Strayer University.
JWI 550 (1208) Page 3 of 14
THE CHALLENGE AND OPPORTUNITY FOR MANAGERS
Our course is designed to balance two types of analysis that are critical in the pursuit of operational excellence:
1. The big-picture, customer-centric view developed through value stream mapping
2. The tools of operations management that can be applied to improve specific processes Operational leaders must be able to leverage both while not compromising either. As discussed last week, it is not expected that management understand the minutiae of each process in a value stream. Still, they must apply their operational and leadership talents to involve the right people in the analysis. They must use the tools of OM to get far enough “into the weeds” to uncover barriers to performance. This requires the input of front-line workers who have detailed knowledge about how the work really gets done and who are excited about an improved future state – the topic of our readings for next week. Great operators must be both big-picture thinkers and detail-oriented analysts. They must be able to step back and consider the mission of the organization and how it delivers value to customers in ways that create a sustainable competitive advantage. And they must be able to dive deep and figure out what’s really going on. This balance is not always easy to sustain, but it is necessary. If there is too much focus on the big picture, the root causes of dysfunction may never come to light. If there is too much focus on process details, you risk putting lots of time and energy into individual tasks that have little impact on the organization’s overall performance and competitive advantage.
© Strayer University. All Rights Reserved. This document contains Strayer University Confidential and Proprietary information and may not be copied, further distributed, or otherwise disclosed in whole or in part, without the expressed written permission of Strayer University.
JWI 550 (1208) Page 4 of 14
YOUR STARTING POINT
1. Do you know exactly where your team’s responsibilities begin and where they end? In other
words, do you know the exact point at which the input is received and ready to be worked on, and where the final output is handed off to another team?
2. How well do you understand each and every step in the current processes being used?
3. Do you know the difference between a step in a process where a value is added and a step where work is held and no value is added?
4. Do you understand not only how work flows from one step to the next, but where projects and products encounter capacity issues that result in bottlenecks that slow down everything?
5. If you were to ask the people performing the tasks in a process what currently works well and what doesn’t, what would you expect to hear?
6. Do you have any knowledge about how the processes your organization uses to produce an output compare to those used by your competitors?
© Strayer University. All Rights Reserved. This document contains Strayer University Confidential and Proprietary information and may not be copied, further distributed, or otherwise disclosed in whole or in part, without the expressed written permission of Strayer University.
JWI 550 (1208) Page 5 of 14
HOW WORK REALLY GETS DONE
We have mentioned the term process several times. Now, we are ready to dig deeper into what we mean by that term and how we can evaluate whether discrete processes are performing well or not. From Input to Output Every organization has processes to get work done. Through these processes, inputs (e.g., a partially finished product or service) are transformed into outputs (e.g., a more finished product or service, or one that is housed in a location more accessible to the consumer) that add value. But to understand exactly how this happens, and to document it for others’ use, organizations must map out what their work teams are doing and how they do it. Process mapping does not just document an organization’s product strategy and processes. It also facilitates both analysis of the processes to identify areas of improvement and measurement of the organization’s success in achieving its goals. This is critical information. Without it, it is much more difficult to identify the best opportunities for improvement. You cannot accurately judge how to scale your success or fix the problem unless you understand what you are already doing. You cannot evaluate how well the organization is operating unless you have some way to measure the results it produces. This requires process mapping and process metrics.
WHAT IS A PROCESS?
Before we go any further, let’s define the term:
“A process is a set of tasks to be performed in a defined sequence and uses inputs (such as labor, capital, knowledge, raw materials, purchased components, and energy) to create outputs that are of great value to customers and therefore to the organization itself. While it may be easier for many of us to visualize an automobile assembly process or a steel-making process, every organization – manufacturing or service, public or private, for-profit or not-for-profit – organizes its work through its operating processes.”
“Process Analysis,” p. 3 Regardless of sector, every organization’s operating processes are meant to fulfill two goals:
1. Deliver the “customer promise” 2. Create value for stakeholders
As Shapiro notes, “Organizations without the means to improve rarely can keep up with competition, and improvement requires a deep understanding of underlying operating processes and an ability to assess their performance” (p. 4). And so, we have two questions to answer:
1. How is each particular process doing? 2. How might we do it better?
© Strayer University. All Rights Reserved. This document contains Strayer University Confidential and Proprietary information and may not be copied, further distributed, or otherwise disclosed in whole or in part, without the expressed written permission of Strayer University.
JWI 550 (1208) Page 6 of 14
The first question is the focus of this week’s reading, and the second question will be our focus next week. While a process is a more granular and internally focused segment of the work flow than a value stream, mapping processes and mapping value streams have a similar purpose.
“Process flow diagrams are useful in many different ways. One use… is as a communications tool that allows a team of people to share a common view of the work they are performing. When a team has such a shared view of what activities (tasks) are being performed and in what sequence, as well as how products and information flow, they can more easily discuss the pros and the cons of changes and improvements to the process.”
“Process Analysis,” p. 7
TYPES OF PROCESS MAPS
As mentioned earlier, a process takes an input and transforms it through an action into an output. When a sawmill transforms a log into a stack of two-by-fours, the log is the input and the two-by-fours are the output. The sawing, planning, and other actions employed by the sawmill personnel to produce the two- by-fours are the process. One way to understand the process is to create a graphic representation of what happens between input and output. This graphic depiction is called a process map. A process map shows the logical flow or sequence of steps and activities that an item undergoes when it is transformed by the process from an input to an output. The four most common types of maps are:
• Value stream map (VSM)
• High-level process map and SIPOC
• Swim lane process map (also called deployment or cross-functional maps)
• Detailed (low-level) process map
1. VALUE STREAM MAP (VSM) As a reminder from our previous readings, a value stream map is a diagram depicting all the actions required to bring a product from concept to launch, and from order to delivery. This includes processing the customer’s information, transforming inputs to produce the product, and delivering the final product to the consumer. The map captures all the key flows of work, information, and materials in a process. A value stream map also includes important process metrics, such as setup times, processing times, units in queue, wait times, and total lead time. Value stream maps are widely used in “lean” projects, which emphasize carrying as little inventory as possible, to map the order to delivery cycle.
© Strayer University. All Rights Reserved. This document contains Strayer University Confidential and Proprietary information and may not be copied, further distributed, or otherwise disclosed in whole or in part, without the expressed written permission of Strayer University.
JWI 550 (1208) Page 7 of 14
2. HIGH-LEVEL PROCESS MAP A high-level process map provides an overview of the process that captures the main inputs and outputs of the process, but which may leave out small details in an effort to represent the process overall. A high- level process map typically represents the process in 4 to 9 process steps. For example:
• A manufacturing plant’s process may be represented on a high-level process map as raw materials storage progressing to processing of a finished product, to storage of the finished product, and finally to shipment of the product to the customer.
• A distribution center can be mapped out as materials coming into the distribution center, staged in a storage location, picked and packaged to fulfill the customer order, shipped to the customer, and invoiced.
• A medical office could map out the flow of their operations, including the reception area, patient rooms, and medical storage, and could also include billing and clerical functions.
SIPOC SIPOC is a popular tool used to provide a high-level overview of the process. This includes the elements of the acronym — the suppliers, inputs, process, outputs, and customers. A SIPOC diagram shows the process steps at a high level in one column, while other columns list:
• The suppliers and the inputs they provide to the process
• The outputs and customers who receive the outputs of the process
When mapping a process, it’s helpful to first map the high-level, major steps in the process. From there, we can “decompose” the key steps into lower-level, detailed process maps. The process of completing this breakdown is called process decomposition. We start with an overview (the “forest”) and then drill down (to the “trees”). You need to define the overview first so you don’t lose sight of the process’s overall flow. 3. SWIM LANE PROCESS MAP (DEPLOYMENT OR CROSS FUNCTIONAL MAPS) A swim lane process map, also called a deployment or cross-functional map, is similar to a detailed process map. The difference is that in a swim lane map, the depiction of the process steps is overlaid with “swim lanes” representing the departments, functions, or teams responsible for each of the process steps. The advantage of using a swim lane process map is that it shows, not just who performs a given step in the process, but also the hand-offs among departments. Hand-offs among departments are possible points of process failure where errors or miscommunications can result in the process not working as it is supposed to.
© Strayer University. All Rights Reserved. This document contains Strayer University Confidential and Proprietary information and may not be copied, further distributed, or otherwise disclosed in whole or in part, without the expressed written permission of Strayer University.
JWI 550 (1208) Page 8 of 14
Swim lane process maps would be applicable in situations such as the following:
• In a problem resolution process, an operator may identify a problem and communicate this to a supervisor. The supervisor works with the maintenance department to solve the problem, while maintenance personnel may work with engineering personnel to design the fix. Engineering may in turn work with outside vendors and purchasers to buy and install a solution. Production planning may also be involved to schedule downtime at the facility in order to halt the process and install the solution.
• The process of purchasing and financing a loan is also a good example. This starts with selection of the home and continues through contract negotiation, loan origination, inspection, loan closing, and transfer of ownership. Each of these steps requires the interaction of the buyer, agent, seller, bank, home inspector, attorney, and movers, all of whom perform different functions independently and relative to each other.
4. DETAILED (LOW-LEVEL) PROCESS MAPS A detailed or low-level process map is essentially the detail of each of the individual steps of the process or processes depicted in the high-level process map. Detailed process maps show the linkages, decisions, inspections, feedback, and rework loops of the process. They explain the “if this, then that” types of decisions that take place for the process to transform its inputs into outputs. The detail provided by a low-level process map allows you to analyze the map and identify opportunities for improvement. You can use a detailed, “as-is” map of an actual process to identify, study, document, and analyze delays, points of failure, rework, and bottlenecks in the process (points where the process is too slow or inefficient). A detailed process map could range from 10 to 30 or more steps. Some examples include…
• The receiving of raw materials, storage of those raw materials, and the retrieval of raw materials to be used in processing
• The pass, fail, rework, and retest feedback loops of a product testing process
• The script flow used by a customer service agent in a call center, who reads through various “if this, then that” queries and responses in handling customer calls
© Strayer University. All Rights Reserved. This document contains Strayer University Confidential and Proprietary information and may not be copied, further distributed, or otherwise disclosed in whole or in part, without the expressed written permission of Strayer University.
JWI 550 (1208) Page 9 of 14
PROCESS METRICS AND RELATED TERMINOLOGY
Some important process metrics and related terminology are capacity, utilization, efficiency, bottlenecks, processing rates, and throughput time. The first step in measuring process performance is measuring task times (p. 7):
“The standard time of a task is defined as the average time that an employee (or customer in many service processes) with average skills will take to complete that task, under ordinary circumstances, and working at a sustainable pace. “One important measure of any process is labor content, the total time that is spent by the firm’s employees on the product or service. Labor cost is, of course, greater than labor content multiplied by the wage rate, because the firm needs to pay employees for any idle time that they incur because of imbalances in the process structure.”
“Process Analysis,” pp. 7-8 These considerations require that we expand our notion of task times. A task in a batch process, or in any process, may require the following:
1. Setup time, the amount of time required to get ready for the task (to load the riders on a Disney World ride, for example, or to prepare the settings on the machine that mixes the dumpling filling) and, if necessary, clean up afterward. Formally, setup time is any time taken to perform a task that is independent of the number of products or customers being processed.
2. Run time, the time it takes to process each unit. Formally, run time is the time taken to perform a
task that varies with the number of products or customers being processed.
“Process Analysis,” p. 8 Bottleneck This term refers to the limiting factor or constraint in the system, the point at which the process takes the longest time to complete a step compared to other steps. Identifying bottlenecks and determining how to address them is one way to make the process more efficient.
“[T]he bottleneck of any process is the task that causes all other tasks to have idle time (there may be two or more bottlenecks in any process). In other words, a bottleneck constrains product flow.”
“Process Analysis,” p. 10
“Capacity and bottleneck analysis are important because capacity limits output and output (as well as price) determines revenue, but neither capacity nor bottleneck analysis tells us much about other key measures of process performance. In particular, most operations managers are quite concerned with the efficiency of their processes—the cost of the inputs, and, often as important, how well these processes make use of those inputs.”
“Process Analysis,” p. 16
© Strayer University. All Rights Reserved. This document contains Strayer University Confidential and Proprietary information and may not be copied, further distributed, or otherwise disclosed in whole or in part, without the expressed written permission of Strayer University.
JWI 550 (1208) Page 10 of 14
Capacity This term refers to the maximum rate of output for a process, measured in units of output per unit of time. Capacity is not “load” (the actual rate of output) and should not be stated as “maximum capacity” because that would be redundant. Capacity is itself the maximum possible output.
“Formally, we have defined capacity as the maximum output, in terms of units produced or customers served, in a specified time period (e.g., units manufactured per hour or customers served per day). This is a critical measure of process performance because it constrains revenue. You can’t sell more than you can make—a firm’s maximum revenue is limited by its capacity.”
“Process Analysis,” p. 13 “Clearly, making a process more efficient means decreasing idle times as much as possible. This requires redefining tasks, wherever possible, to balance the process—that is, to make cycle times as nearly equal as possible and capacity utilization at each task as high as possible. However, because many tasks are not easily divisible it is rarely possible to balance a process fully.”
“Process Analysis,” p. 13
There are two types of capacity. The first is design capacity, the theoretical maximum output of a system in a given period under ideal conditions. Design capacity may be greater than actual capacity because “ideal conditions” are rarely encountered in real life. The second is effective capacity, the capacity a firm can expect to achieve, given its product mix, scheduling, maintenance, and quality. Cycle Times “The system’s cycle time is the average time between the completion of successive units of product or, in the case of a service process, the average time between the departures of successive customers” (p.11).
Efficiency and Effectiveness “[P]rocess performance is a matter of efficiency (how well a process turns its inputs into outputs), and effectiveness (how well a process delivers its customer promise)” (pp. 15-16). Flexibility This term refers to “the ability to change or react with little penalty in time, effort, cost or performance” (p. 20).
© Strayer University. All Rights Reserved. This document contains Strayer University Confidential and Proprietary information and may not be copied, further distributed, or otherwise disclosed in whole or in part, without the expressed written permission of Strayer University.
JWI 550 (1208) Page 11 of 14
Labor Utilization
“[W]e define labor utilization as useful time (namely, time actually working on a product or delivering a service) spent by workers as a percentage of the total time for which they are available (and being paid).” “We need to be careful as to how we use the labor utilization calculation to make decisions. Some managers, thinking that efficiency is reflected in ‘workers being busy,’ exhort their workers to increase their utilization by making more product. However, at non-bottleneck steps, greater labor utilization translates into more inventory, not more saleable product. Rather than increasing labor utilization itself, emphasis should be placed on breaking bottlenecks. Reducing a bottleneck’s time will automatically raise labor utilization, but in a useful way, namely one that results in more saleable product and increased revenues.”
“Process Analysis,” pp. 16, 17 Processing Rate The processing rate of a step in the process is the rate at which units come off that specific step or workstation (for example, 2 units/minute). The process or cycle time of the workstation is the time between units coming off that workstation (in our example, 30 seconds/unit). For example, if the cashier at a grocery store takes an average of 6 minutes to check out a customer, the process (or cycle) time at the checkout station is 6 minutes. If there are 3 cashiers working, then the checkout station (combined) can complete checking out 3 customers every 6 minutes. The checkout process functions at the processing rate of 3 customers every 6 minutes, or 0.5 customers per minute. The process or cycle time is the reciprocal of the processing rate. In this example, the process or cycle time at the checkout station is 6/3 or 2 minutes. Quality
“Quality is the ability of a product or service to meet or exceed customers’ expectations… We define quality in two different ways:
• Performance quality
• Conformance quality” “Process Analysis,” pp. 17-18
“A firm that competes on performance quality produces goods and services that deliver a high level of some set of performance dimensions… In contrast, a product or service with high conformance quality delivers on its specifications, whether that means a high level of performance or not.”
“Process Analysis,” p. 18
© Strayer University. All Rights Reserved. This document contains Strayer University Confidential and Proprietary information and may not be copied, further distributed, or otherwise disclosed in whole or in part, without the expressed written permission of Strayer University.
JWI 550 (1208) Page 12 of 14
“Performance quality is primarily the realm of designers and product developers. Operations is responsible for developing processes that meet design specifications. A product that does not meet its design specifications is typically called a defect.”
“Process Analysis,” p. 18 Speed
“A second aspect of effectiveness that is important to many firms is how quickly (and reliably) they can produce and deliver a product to customers, or, in a service context, how quickly a customer can be served.”
“Process Analysis,” p. 18 Throughput Time Throughput time is the time it takes for a product to go through the production process with no waiting. It is the longest path through the system.
“We define throughput time (TPT) as the start-to-finish time of a process, namely the total elapsed time between the time when a customer walks in the door and the time when the customer leaves, or the time from when the raw materials and components begin to be gathered and the time the finished product is completed.”
“Process Analysis,” p. 19
Utilization Utilization refers to the actual output as a percent of design capacity.
© Strayer University. All Rights Reserved. This document contains Strayer University Confidential and Proprietary information and may not be copied, further distributed, or otherwise disclosed in whole or in part, without the expressed written permission of Strayer University.
JWI 550 (1208) Page 13 of 14
SUCCEEDING BEYOND THE COURSE
As you read the materials and participate in class activities, stay focused on the key learning outcomes for the week and how they can be applied to your job.
• Understand the importance of process analysis in any organization As the saying goes, “The devil is in the details.” Even the simplest of businesses has dozens, if not hundreds, of processes that are part of its regular operations. Weaknesses in any one of these can have a cascading effect that undermines the performance of upstream or downstream processes. Just as you did with mapping a value stream, select one particular process that you and your team are regularly responsible for, and develop a detailed diagram of the exact steps in that process needed to transform an input to an output. Clearly identify the hand-off from task to task, including those stages where the work is sitting idle, waiting for additional input(s), or can’t be moved on because of capacity limitations at the next step.
• Calculate process metrics to explain operational outcomes After you have created your process map, perform at least 3 calculations for operational outcomes. To get started, you should calculate the throughput time, the time spent idle where no work is being done and no value is being added, and the labor utilization. You may select additional or other metrics, of cour
Collepals.com Plagiarism Free Papers
Are you looking for custom essay writing service or even dissertation writing services? Just request for our write my paper service, and we'll match you with the best essay writer in your subject! With an exceptional team of professional academic experts in a wide range of subjects, we can guarantee you an unrivaled quality of custom-written papers.
Get ZERO PLAGIARISM, HUMAN WRITTEN ESSAYS
Why Hire Collepals.com writers to do your paper?
Quality- We are experienced and have access to ample research materials.
We write plagiarism Free Content
Confidential- We never share or sell your personal information to third parties.
Support-Chat with us today! We are always waiting to answer all your questions.
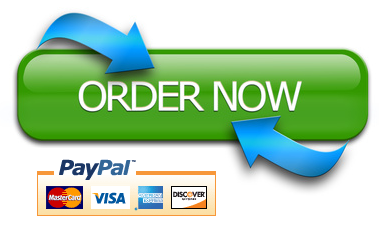