WA Furniture is a producer of high-quality home furniture Australia wide. It is a long-standing family business which prides itself on the quality and individuality of its pieces. T
Need demo and report of 2 pages.
My part is How the system supports the order fulfilment process.
Need to do the demo on oddo ERP. I will send you login of oddo ERP
Case Scenario
WA Furniture is a producer of high-quality home furniture Australia wide. It is a long-standing family
business which prides itself on the quality and individuality of its pieces. The company specializes in
WA timbers of Marri, Jarrah and Blackbutt, and has won several Furniture Industry Association of
Australia awards for its contemporary and timeless products.
Figure 1 shows the organizational structure for WA Furniture.
Figure 1: Organizational structure of WA Furniture
WA Furniture uses a few different software programs to support its operations, with heavy reliance
on Excel spreadsheets to share information between departments. As the company grow, the
number of spreadsheets grew, increasing the chances of error and misplaced information.
In Production, the company run a Materials Requirements Planning (MRP) system to help manage
the production process. This system schedules the production of all pieces required to make the
customer’s orders. Although outdated, it meets the manufacturing needs of the plant.
From the sales perspective, providing an accurate quotation to the customer is challenging. The
accuracy of quotations depends on information from previous orders. However, Production does not
capture costs by order at the point they were incurred and can only pass on “rough” estimations. As
such, it is not possible to provide an accurate quotation. There have been several occasions where the
company had to bear the losses because the orders were under quoted.
The accounting and finance activities are processed by a stand-alone package which has been in place
for several years. It relies to a large extent on input from paper-based output from the MRP system
and customer and supplier invoicing. While the system can handle the accounting processes in general,
there are frequently delays in processing of payments and invoices due to missing documentation.
As the company grows, it became obvious that the existing IT arrangement is not going to be sufficient.
WA Furniture is in the process of acquiring an ERP system. The company identified the following
business functions to be included in the scope of the implementation:
• Accounting
• Procurement
• Sales
• Production
• Inventory Management
The IT and Logistics Manager, Eddie Baker, has recommended that the company consider Odoo ERP,
an open-source system which has received raving reviews among SMEs in the recent years. You work
in the IT and Logistics department and have been assigned the task of creating a demo to show how
Odoo ERP may work for WA Furniture.
The management is particularly interested in understanding how Odoo ERP system can improve the
information flow in the company. In particular, the management want to understand:
• How the system supports the order fulfillment process
• How the system supports production process
• How the system supports processing of payments and invoices
• How the system supports the information flow between different departments
You should draw on information described in the following section to build and configure your
demo. For details that are not provided, reasonable assumptions are allowed. These should be
clearly listed in the accompanying report.
Company Operations
WA Furniture is a make-to-order business. The company has a range of designs from which
customers can choose but customers can also commission the company to design a unique piece to
suit their requirements. It has two main types of customers: consumers who are furnishing their
homes and businesses (eg. builders) furnishing houses for sale.
The order fulfillment process begins when Sales and Design team carries out an initial consultation
with customer to determine the specific requirements. For product selected from the company’s
existing range, customers may customize by choosing from the available options specific to the
selected piece. For instance, for a dining table, the customer is able to choose the type of timber (eg.
Jarrah, Tasmanian Oak, Marri, or Blackbutt), the size (eg. 1800w x 1050d X 760 h, 2100w X 1050d X
760h, 2400w X 1050d X 760h, 2700w X 1050 X 760h) and finish (eg. matt or gloss) of the final
product. For custom design pieces, the Sales and Design team works with the customer to produce a
design that satisfy the customer’s requirements.
A quotation is drawn up based on the customers’ requirements and presented to customers for
confirmation. A 30% deposit is typically required on acceptance of the quotation, with the final
payment upon delivery. Customers may choose to pick up the final product from WA Furniture or
they could utilize the delivery services provided. For deliveries within Perth metro, a standard of
$110 fee applies. The fees for outside Perth metro and interstate deliveries can range from $150 –
$350, depending on location.
The Sales and Design team has the discretion to apply 5-7% discount on the entire order for loyal
customers.
The figures below show examples of two quotations: 1) a quotation for a dining table and chairs
from the company’s existing range, and 2) a quotation for a custom design kitchen island for a
valued corporate customer.
Once the quotation has been confirmed by the customer, the design specifications will be forwarded
to the Production Team for production. The final product will take 6-8 weeks from order.
All furniture from the company’s existing range has an associated Bill of Materials (BOM). The
Production team modifies the BOM according to customer’s choice of timber, size and finish. These
BOMs are created when needed. For custom orders, the Production team relies on a standard BOM
designed to provide skeleton set of material, labour and machine requirements. This is created
based on past history of orders of similar type. This BOM is modified extensively by adding custom
components and routing steps to reflect the unique orders. This has resulted in many hundreds of
“dead” BOM in the MPR system due to one-time order.
WA Furniture maintains an inventory of components (eg. nuts, bolts, nails, fabric, timber etc.) that
enable them to fulfill orders from their existing range. The manager in Production has been working
in WA Furniture for many years and has developed a “sense” of how often different components
need to be restocked to avoid situations where sales order cannot be fulfilled because of out-of-
stock components. For customized furniture orders that require components that are not
maintained in the company, a call for tender may be raised from existing vendors and the vendor
that offers the lowest price will be selected. All purchase orders over $500 needs to be approved by
the manager. The company works closely with a few suppliers and has developed a good working
partnership over the years. Many of the company’s suppliers offer bulk discounts on purchases and
the management prefers to order from these suppliers.
The main steps in the production of a typical order are1:
1. Preparing material – eg. preparing the timber required for the production
2. Cutting the timber to required size
3. Size inspect and rubbing
4. Seasoning (providing chemical protection)
5. Making of joints and connected parts
6. First inspect (repair and trimming)
7. Colour and protective coating
8. Assembly
9. Final inspection.
1 Mehidi, S. and Haider, M. 2014. “Residue Reduction and Reuse in Wooden Furniture Manufacturing Industry” International Journal of Scientific and Engineering Research, October.
Figure 2: Quotation Example 1
Figure 3: Quotation Example 2
Collepals.com Plagiarism Free Papers
Are you looking for custom essay writing service or even dissertation writing services? Just request for our write my paper service, and we'll match you with the best essay writer in your subject! With an exceptional team of professional academic experts in a wide range of subjects, we can guarantee you an unrivaled quality of custom-written papers.
Get ZERO PLAGIARISM, HUMAN WRITTEN ESSAYS
Why Hire Collepals.com writers to do your paper?
Quality- We are experienced and have access to ample research materials.
We write plagiarism Free Content
Confidential- We never share or sell your personal information to third parties.
Support-Chat with us today! We are always waiting to answer all your questions.
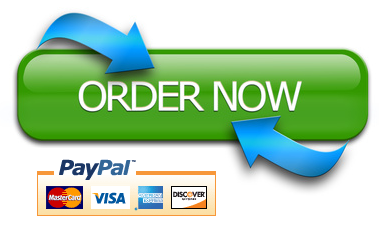