In this activity you are to review the product liability case?below?and create a brief that summarizes its legal elements and holding. Instructions – Read?Estate of Simps
Overview – In this activity you are to review the product liability case below and create a brief that summarizes its legal elements and holding.
Instructions – Read Estate of Simpson v. GM, LLC.
Using the Week 3 Activity Template [DOCX], accurately summarize the following regarding design, manufacturing, and failure-to-warn causes of action in a brief that effectively lays out the following legal elements of the case:
- Case facts.
- Parties and their arguments.
- Proceedings of the court case – what happened in the court(s)?
- Applicable product liability defect law
- The holding of the court and its reason(s).
LEG500 – Format for all writing assignments:
- Include page numbers
- 1-inch margins, double spaced throughout assignment
- Times New Roman, 12-point type
- Title Page centered, first page should include: Assignment name, your name, professor name and date
- Cite credible, scholarly sources in the text of the paper that corresponds to the sources on the Source page. Type “Sources” centered on the last page of the assignment. Record sources that you used in the assignment in a numbered list as they appear in the paper, not alphabetically.
- For each resource you use in your coursework, there are two things you must do. First, add the resource to the Source list on the final page/slide. Second, insert an in-text citation to each sentence which quotes, paraphrases, or summarizes information from that resource. Make sure that each in-text citation has a match
Week 3 Activity Template
1. Summarize the facts of the case:
·
·
·
2. Summarize the arguments:
· Plaintiff:
·
·
·
· Defendant:
·
·
·
3. Describe the history of the proceedings.
4. Explain the law regarding product liability defect (1–2 paragraphs).
5. Provide the holding of the court and reasoning for the court’s decision.
[End of Document]
© 2020 Strayer University. All Rights Reserved. This document contains Strayer University Confidential and Proprietary information and may not be copied, further distributed, or otherwise disclosed in whole or in part, without the expressed written permission of Strayer University.
Page 1 of 1
,
Estate of Simpson v. GM, LLC, 2020 Mich. App. LEXIS 12
Export Citation
Court of Appeals of Michigan
January 2, 2020, Decided
No. 341961, No. 342291
THIS IS AN UNPUBLISHED OPINION. IN ACCORDANCE WITH MICHIGAN COURT OF APPEALS RULES, UNPUBLISHED OPINIONS ARE NOT PRECEDENTIALLY BINDING UNDER THE RULES OF STARE DECISIS.
Subsequent History: Leave to appeal denied by Simpson v. GM, LLC, 2021 Mich. LEXIS 95 (Mich., Feb. 2, 2021) Leave to appeal denied by Simpson v. GM, LLC, 2021 Mich. LEXIS 146 (Mich., Feb. 2, 2021) Prior History:
[*1] Genesee Circuit Court. LC No. 16-107103-NO.
Simpson v. GM LLC, 2018 Mich. App. LEXIS 1501 (Mich. Ct. App., Apr. 17, 2018)
Core Terms
spring, manufacturer, ball, rack, rivet, stud, summary disposition, misuse, foreseeable, express warranty, circuit court, warranty, overextension, cylinder, manufacturing defect, seller, proximate cause, no evidence, sidewall, product liability, component manufacturer, supporting evidence, piston, plaintiff's claim, discovery, email, breach of implied warranty, component part, design defect, proximate Judges: Before: M. J. Kelly, P.J., and Markey and Gleicher, JJ.
Opinion
Per Curiam.
This product liability action arises from the explosion of a gas spring. The spring was attached to the sidewall of a large metal rack owned by General Motors. GM used the rack to store and transport auto parts. Plaintiff Trask Simpson was severely injured when the gas spring violently separated as he raised the sidewall so that he could repair the rack's floor. The cylinder section of the spring penetrated Simpson's face, lodging in his sinus cavity and brain.
Simpson claims that a manufacturing defect caused his accident. A rivet inside the spring failed due to an inherent weakness, Simpson contends, resulting in the high-speed detonation of the device and his injury. Simpson sued the spring manufacturer (defendant Stabilus, Inc.), the manufacturer of the rack (defendant Keener Corporation), GM, and several other entities involved the rack's design and distribution.
All defendants brought motions for summary disposition. Some were granted, and some were denied. We granted leave to consider a host of legal issues raised in the motions. Simpson cross-appealed a ruling denying a [*2] discovery sanction, adding to the number of questions presented.
We affirm the circuit court's rulings as to defendant Stabilus and the discovery sanction, reverse as to defendants Keener and JWF, and remand for further proceedings consistent with this opinion.
I. BACKGROUND FACTS A. THE RACK AND GAS SPRING
Trask Simpson was employed by Dort Steel as a welder. Dort repaired or salvaged large metal racks in which GM stored and transported auto parts, such as bumpers. Dort employees either fixed broken racks delivered by GM, or disassembled them for reuse of their parts.
The rack involved in this case was a large metal container that was open in the front, had two lateral walls called sidewalls, and a rear wall called a T-bar. It arrived at Dort in a collapsed condition, with the three walls folded down to the rack's floor. The two sidewalls weighed approximately 90 pounds each. Gas springs manufactured by Stabilus assisted in lifting them into position. Once the two sidewalls were raised, the rear wall could be fastened in place.
Here is a photograph of the rack in the fully open position; the rear wall is in the foreground:
The inserts magnify the gas springs and the smaller red circles indicate [*3] their positions on the rack's sidewalls.
Gas springs are common, everyday products. They are found on the tailgates and hoods of cars, where they facilitate the upward movement of heavy metal. Underneath an office chair a gas spring dampens movement, preventing the seat from slamming down when someone sits on it. Gas springs have different sizes, strengths, and uses, but they all work by storing and releasing energy.
Gas springs consist of two primary components: a rod and a cylinder. The spring depicted on the left in the above photo is the spring that exploded; only the rod end remained in place. The spring on the right is fully extended, and both the rod and cylinder are intact.
A gas spring's function depends on a transfer of pressure within the spring itself. A metal tube, called the cylinder, holds pressurized nitrogen gas. A rod with a piston at the end fits into the cylinder. The rod end of the cylinder contains seals that glide along the rod and help guide it. As the spring is extended, motion of the piston along the rod allows the gas to flow from one end of the spring to the other. The pressure differential created by movement of the piston generates a force that helps raise [*4] a heavy object.
The piston's position on the rod is maintained by the seals and washers and, ultimately, by a single rivet. The rivet is at the center of plaintiff's claims in this case. According to plaintiff, the gas spring that injured Simpson separated because the rivet head failed. That failure, plaintiff posits, was due to a manufacturing defect. The rivet head in the spring that injured Simpson was a "bad apple," plaintiff maintains.
B. THE ACCIDENT
When the rack in the photograph was delivered to Dort, Simpson inspected it and decided to spot-weld a portion of the floor. As he started to raise the left side-wall, the gas spring blew apart. Propelled by the high-pressure nitrogen gas, the cylinder flew through the air and lodged in Simpson's face, penetrating his sinus and brain. The rod end of the spring remained attached to the rack. Here is a radiologic image obtained at the hospital where Simpson was taken, showing the cylinder embedded in his head:
Simpson died in August 2018, five years after the accident.
Before his death, Simpson sued a number of entities that he alleged were involved in the manufacture, distribution, and use of the gas spring. Pertinent here, the defendants [*5] were: GM; Gonzalez Contract Services (the designer of the rack); Keener Corporation (the manufacturer of the rack); JWF Technologies (the supplier of the gas spring), and Stabilus, Inc. (the manufacturer of the gas spring). Simpson's claims sounded in negligence and product liability.
The parties engaged in extensive discovery. More than two dozen depositions were taken. Jointly, the parties performed testing on the cylinder end of the spring and on exemplar springs. Dort apparently lost or destroyed the rod end of the spring that injured Simpson. A number of engineering experts provided depositions regarding the cause of the spring's separation.
The experts agreed (and Simpson does not contest) that the spring had been misused at GM before it arrived at Dort. Specifically, the evidence established that the spring had been overextended at least once, and possibly many times. According to several of the expert witnesses, overextension precipitated a failure of the rivet head. When Simpson began to raise the sidewall, the defective rivet head allowed an instantaneous transfer of high-pressure gas, violently pushing the two components of the spring apart. As Dr. Stephen Batzer, defendant [*6] Keener's engineering expert put it: "if the rivet fails and the other components of the piston assembly are then free on the . . . rod end, pressure inside of the cylinder will cause the cylinder and rod to separate under force, and if they're not captured by their mounting points there will be . . . a rocket."
All of the defendants brought motions for summary disposition under MCR 2.116(C)(10) . Simpson orally moved the court to impose a discovery sanction against JWF arising from JWF's alleged failure to timely supplement its discovery responses. The circuit court granted summary disposition to Keener, but denied summary disposition to GM, Gonzalez, Stabilus, and JWF. The court also denied Simpson's discovery sanction motion. GM and Gonzalez have settled with Simpson. Stabilus and JWF now appeal by leave granted; Simpson cross-appeals the dismissal of Keener and the denial of sanctions.
We turn to a deeper discussion of the evidence and the claims on appeal, which we address party-by-party. Our review of the evidence conforms to the rules governing summary disposition. We have considered the circuit court's summary disposition decisions de novo by familiarizing ourselves with the pleadings, admissions, [*7] affidavits, and other record documentary evidence "in the light most favorable to the nonmoving party to determine whether any genuine issue of material fact exists to warrant a trial." Walsh v Taylor , 263 Mich App 618, 621; 689 NW2d 506 (2004) . When the record has left open an issue on which reasonable minds could differ, we have concluded that a genuine issue of material fact exists, precluding summary disposition. West v Gen Motors Corp , 469 Mich. 177, 183; 665 N.W.2d 468 (2003) . Our review has also been guided by the principle that "[e]ven where the evidentiary facts are undisputed, it is improper to decide the matter as one of law if a jury could draw conflicting inferences from the evidentiary facts and thereby reach differing conclusions as to ultimate facts." Nichol v Billot , 406 Mich 284, 301-302, 279 NW2d 761 (1979) (citations omitted).
II. STABILUS
Stabilus manufactures a wide variety of gas springs of different lengths and pressures, and designed for use in diverse applications. Some are "off the shelf" products. Others, such as the spring involved in this case, are custom-made. According to James Kull, Stabilus's Director of Industrial Applications Engineering, the subject spring was "a custom product" manufactured for defendant JWF, with "a certain length, a certain stroke, a certain force, and end fitting connections."
Defendant Gonzalez designed the [*8] GM rack. The rack's design included two Stabilus springs, one mounted to each sidewall. A ball stud system (the "end fitting connections" referred to by Kull) attached the springs to the sidewalls. The springs selected for incorporation in the GM racks were manufactured with a ball cup, also called a "socket," at each end. The ball cup was intended to couple with the ball stud—a spherical head on a shank, affixed to the rack. The ball studs used on the GM racks were selected by defendant Gonzalez, and conformed to Stabilus's specifications. Here are photographs depicting the ball stud and a ball socket system. From left to right, the first two photos show the socket; the second depicts the clip, discussed below. The third photo is of a ball socket. The photo at the bottom of the display shows a spring's socket attached to a ball stud:
Clips on the ball sockets helped keep the balls and cups together. According to Stabilus's instructions, before freeing the spring from its attachment points, the clips would first be removed with a screwdriver. The evidence supports that when Simpson began working on the rack, the clip on the left spring's ball socket had already been removed. Simpson [*9] denied having removed the clip. Nevertheless, the ball apparently remained within the ball cup until the spring separated. 1
According to James Mattice, a forensic engineer retained by Dort, the spring blew apart due to a failure of the rivet head holding the piston components in place, likely precipitated by overextension of the spring: "I believe at some point the gas spring was loaded in tension or overextended which resulted in its failure. . . . I believe at some point, yes, the rivet failed." In Mattice's estimation, the rivet failure occurred before the rack arrived at Dort. Mattice tested four exemplar gas springs in his laboratory to determine the amount of force required to fail their rivet heads. His testing revealed that when extended in an axial direction, the rivet heads maintained their function until the load reached approximately 2,000 pounds. When the spring was overextended by .11 to .13 inches, its components would "start breaking up." C. Michael Dickinson, an engineer retained by GM, agreed that the spring separated because "[t]he rivet apparently failed."
Glenn Akhavein, an engineering expert retained by Simpson, concurred that the rivet head's failure caused the [*10] spring to separate:
This style of gas spring is held together by a rivet head, which had been damaged while at the GM facility due to over extension of the gas spring. When Mr. Simpson started lifting the left side rail the cylinder end of the gas spring (the end that rotates upwards while the side rail is lifted), came off of its ball stud and due to the damage that had taken place at GM it did not extend slowly but instead flew off with enough velocity to penetrate deeply into Mr. Simpson's head.
His testing of exemplar springs demonstrated that the rivet head held until at least 1,500 pounds of force were applied. To generate the force necessary to separate his exemplar springs, Akhavein pulled on them by attaching them to his Chevrolet Suburban vehicle.
James Kull, Stabilus's engineering representative, admitted that the evidence supported that the rivet head failed, and that this failure caused the spring to come apart. Kull explained that the rivet is the only part of the spring's inner workings that retains the piston components on the rod. According to Kull, the spring was designed so that the rivet head would withstand overextension. Kull testified that the ball stud is supposed [*11] to sheer before the rivet head fails, with the ball stud functioning as a "fuse." After examining a CT scan of the internal components of the failed spring, which displayed distortions of the washers holding the piston in place and an absence of the rivet head, Kull expounded:
A. [T]he way we designed this is the ball stud is designed to sheer at a force much lower than this. So to apply a longitudinal load through the ball stud, you're going to break the ball stud prior to that, you know, just by our strength of materials. So the ball stud will sheer before that in this type of connection. We have a 10-millimeter ball stud on that metal connection. That is the, say, like the fuse or what would break before I would expect to see, you know, piston . . . incident.
Q. Just for the record, there's a ball stud at the top of the gas spring and a ball stud at the bottom?
A. Yes.
Q. And if I understand what you're telling me is that, in the event that there's an excessive longitudinal force . . . like, force along the long axis of the spring.
A. Exactly. Yes.
Q. If we have excessive force on the long axis of the gas spring, the ball spring is intended to fail first?
A. That is correct, yes.
Q. And [*12] that would be where it's next down to the attachment point where you bolt it on to whatever you're attaching it to?
A. Exactly. Yes. [Emphasis added.]
In his 28 years with Stabilus, Kull asserted, he had never seen a gas spring separation like this one.
Dickinson, the engineer retained by GM, agreed that the ball stud was supposed to fail before the rivet head. In his view as well as Kull's, overextension of the spring should have tripped the ball stud connection. Had this happened, the spring would have fallen off the rack. "A 13-millimeter nominally grade-2 fastener [used in this case] is such that if you put a pure axial tensile load on the strut [spring], you will significantly deform and/or break the ball stud before you fail the internal components of the strut." He continued:
First let me say my understanding is it's Mr. Kull's testimony that says the ball studs are to act as a fuse and that they should break prior to a separation failure of the strut. I believe that that's correct and I believe that this was probably designed that way, which makes the failure of the strut through whichever mechanism or combination even more mysterious because we didn't fail these ball studs, and [*13] to my knowledge there's nothing magical about the ball studs on the accident rack. They're just grade 2 HS135's or whatever, right? That's just garden variety grade-2 steel.
If we had a high-load quasi-static potential load applied sufficient to fail the rack, the rivet head as it was done in the lab tests, . . . the ball studs would have failed or broken or bent before that.
He added, "So if you somehow put 1,000-pound highly dynamic load on that system, I would still expect the ball studs to go first."
Dickinson, too, tested exemplar springs and ball studs. His testing revealed that the ball studs began to exhibit signs of failure, including bending, when between 800 and 1,000 pounds of force was applied. Examination of photographs of the ball studs involved in Simpson's accident revealed no evidence of failure, however: "I would expect to see bending of that ball stud in those photos, and I don't. And you certainly don't see bending like that." He agreed that the rivet head in this case "would have failed below 800 pounds" if the overextension was purely axial "and all other things are out of play, there's no heating, there's no prior damage on the inside, there's no fatigue, crack [*14] growth that predated this . . . ." And based on his examination of the involved spring, Dickinson concluded that it was subjected to "primarily axial tension."
No evidence produced by any party suggested that the ball studs deformed or broke before the spring exploded. Instead, the evidence summarized above substantiates that the rivet head failed first. And according to Akhavein, "[i]f the rivet head doesn't fail you don't get separation between the two components." Had the rivet head continued to function despite the overextension, "then it's going to act just like it always does; the ball stud breaks and from whatever position this is compressed, it's going to slowly expand." Further questioning reinforced this point:
Q. Simply put, my question is this. What would have happened if the rivet head did not fail?
A. The gas spring would have extended to its full extent and then stopped.
Q. If the rivet head had not failed would there have been an injury to Trask?
A. I don't believe so.
In Akhavein's view, either the spring was not designed with a strong enough rivet head, or it was "manufactured in a manner that resulted in a product that didn't meet design intent." As discussed in more detail [*15] below, plaintiff has elected to confine his claim against Stabilus to a manufacturing defect.
When discovery concluded, Stabilus moved for summary disposition, presenting three arguments. Stabilus first contended that as the manufacturer of a component part, it bore no responsibility "for the use of the gas spring within the application in question." Further, Stabilus asserted, the gas spring was misused. Under MCL 600.2947(2) , Stabilus continued, it was not liable for the consequences of misuse unless the misuse was reasonably foreseeable. Here, Stabilus claimed, the misuse of the racks was unforeseeable. Stabilus also challenged plaintiff's defective design claim.
In response, plaintiff abandoned all previously pleaded design defect claims raised against Stabilus and limited his legal argument to "a manufacturing defect." The court denied Stabilus's initial motion. Following oral argument, the circuit court permitted Stabilus to refile its motion for summary disposition. In its renewed motion, Stabilus contended that no evidence supported that the gas spring was defectively manufactured.
At hearings conducted on the various defendants' motions for summary disposition, plaintiff's counsel declared: [*16]
This is a products liability action and they are talking about alternative design, underlying design. There is nothing wrong with the design of this gas spring. It is a manufacturing defect. The gas spring did not comply to the design of the gas spring itself. As the defense counsel for Stabilus indicated, there is a design criteria of the gas spring in which the rivet will be stronger than the ball stud. So in other words, if there is going to be an overextension, the overextension will break the ball stem, but the rivet will stay in place. The reason that's the distinction is, that prevents an explosion. So, the issue again is not alternative design . . . .
Plaintiff disputed that Stabilus supplied merely a "component," highlighting that the spring was a completed product used in conjunction with another product. Counsel analogized, "Stabilus'[s] claim of lacking responsibility for a component part is as if a manufacturer of a tire claims it has no liability for tire defects because it didn't know if it was going to be used on a Chevrolet or a Buick." Misuse of the spring was foreseeable, counsel urged.
The circuit court ruled that an issue of fact precluded summary disposition of plaintiff's [*17] defective manufacturing claim. As to the foreseeability of misuse of the spring, the court stated:
Plaintiff argues that this misuse was clearly foreseeable because Stabilus had accounted for overextension and excess force on the gas spring in their design criteria. And if this safety mechanism that was meant to prevent harm came out of – – coming out of misuse failed, then it seems clear that Stabilus foresaw the misuse of the spring and designed it accordingly. So, I'm going to let a jury decide that a
Collepals.com Plagiarism Free Papers
Are you looking for custom essay writing service or even dissertation writing services? Just request for our write my paper service, and we'll match you with the best essay writer in your subject! With an exceptional team of professional academic experts in a wide range of subjects, we can guarantee you an unrivaled quality of custom-written papers.
Get ZERO PLAGIARISM, HUMAN WRITTEN ESSAYS
Why Hire Collepals.com writers to do your paper?
Quality- We are experienced and have access to ample research materials.
We write plagiarism Free Content
Confidential- We never share or sell your personal information to third parties.
Support-Chat with us today! We are always waiting to answer all your questions.
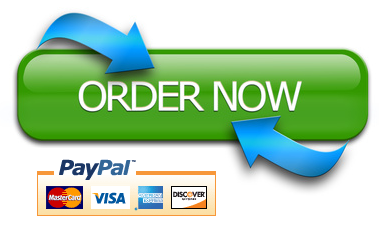