This assignment is intended to help you use leadership skills to gather project members from cross-functional departments and skill sets and lead them in the fulfillment
This assignment is intended to help you use leadership skills to gather project members from cross-functional departments and skill sets and lead them in the fulfillment and implementation of a mock project.
Discover the various responsibilities of a project manager by organizing a project. See Chapter 19, sections 19.9 and Cases.
Apply project management tools and a PM outline type of your choice to structure and plan the project by defining, planning, and controlling. The project will be a continuation of how to improve the process you chose in Weeks 1 and 2.
Create a 10- to 12-slide PowerPoint presentation (supported by Excel and Word as needed), with detailed speaker notes, that includes the following:
- Project description
- Project Management Charts (Critical Path, Gant Chart, etc.)
- Improved Process Flowchart from Week 1
- Meeting cadence/rhythm and timing
- Metrics to measure the project’s success
- Financial and budgetary considerations
- Description of the project reporting structure
Cite references to support your assignment.
Format your assignment according to APA guidelines.
Running head: Process improvement flowchart 1
Process improvement flowchart 4
Process improvement flowchart
David Leonard
University of Phoenix
OPS/574
17 June 2022
Amazon fulfillment system process flow chart
Outbound shipping
SLAM
Loading
Outbound sorting
Packing
Customer orders online
Picking
Pick tower
Stowing
Unloading and unboxing
Inbound shipping
The current fulfillment system process used by Amazon can be evaluated based on the total quality management (TQM). This technique aims at continuous improvement over time. Based on the approach, there the current system engages the customer only when making orders and receiving the product or services ordered. The entire process is well-designed and developed to accommodate necessary variables towards safe and convenient delivery of purchased products.
Process improvement flowchart
As outlined the customer initiates the process of making online orders. However, using the customer-focus of the TQM technique, there is a need to maximize the engagement of customers in the fulfilment process in maximizing customer experience when making purchases from the Amazon ecommerce platform. Customer-focus aimed can be measured based on the levels of engagement of the customer between the points of making online orders and when the delivery of the products or services is done (Kaur et al, 2019). The flow chart represents the Amazon fulfillment system after improvements.
Outbound shipping
SLAM
Loading
Outbound sorting
Packing
Customer orders online
Picking
Pick tower
Stowing
Unloading and unboxing
Inbound shipping
P1
P2
Summary
Amazon’s fulfilment system is a process that allows the company to grow through providing access to Amazon logistic networks. The company has a wide network of suppliers who supply various commodities offered by the company to the customers. According to the current fulfillment system, the company is able to secure supplies even before the customer makes an order. This involves the highly demanded products which are kept in the company’s warehouses. The reason for maintaining the stock is to ensure there is a faster delivery process. This also entails the products that are manufactured within the company. When a customer makes an online order, the pick tower picks the products from the stores and is ready for picking and packing. The products are prepared and packed on branded packets and ready for shipping to the customer based on the location details provided by the customer.
Based on the total quality management (TQM) technique used in evaluating the process flowchart, a weakness is identified in that the customer has a lower level of engagement and tracking of the product before it is delivered. This is because the customer is only able to monitor the product at the selection stage when the products are displayed at the store or warehouse. However, given that the purchases are made online, there is a need to engage the customer by enabling the customers to see the selected products before they are packed and shipped.
It is for this reason that there should be more instances of engagement with the customer which can be introduced at the points marked P1 and P2 respectively. At these points, the customer can trace the product and assess whether it meets the expectations before it is packed and delivered to the location provided by the customer.
Introducing the two check-points would enhance customer focus as it increases the levels of engagement of the customer with the company in assessing the quality standards of the product. Therefore, there will be a better performance in ability to engage customer in the purchase process compared to the current level of customer engagement (Yudiansyah et al, 2020).
Increasing the level of engagement as illustrated in the improved process flowchart helps Amazon in realizing the main organizational goal of customer-centrism. This in turn enhance customer loyalty to the company which can boost the performance of the company in relation to sales maximization and expanding customer base.
Reference
Kaur, M., Singh, K., & Singh, D. (2019). Synergetic success factors of total quality management (TQM) and supply chain management (SCM): A literature review. International Journal of Quality & Reliability Management.
Yudiansyah, A., Keke, Y., & Veronica, V. (2020). Can the mobile robot be a future order-picking solution?: A case study at Amazon fulfillment center. Advances in Transportation and Logistics Research, 3, 800-806.
,
OPS/574 v1
Statistical Process Control Methods
OPS/574 v1
Page 2 of 2
Statistical Process Control Methods
Process Evaluation
Evaluate your process using 1 of the following:
· Use the lean concept to find ways to eliminate waste and improve the process
· SPC or Six Sigma to reduce defects or variances in the process
Amazon has been able to create a more customer-centric approach by concentrating solely on items that are directly relevant to its customers' needs. So, when it comes to choosing a mode of transportation for a cargo, the promised delivery date to the client is the most important factor. Calculation of on-time delivery must be based on the odds of lower-cost choices being as likely to deliver as the high-cost ones. Here's an example of how the Lean Principle is applied. As evidence of this managerial approach to lean management, Amazon's fulfillment and customer service centers employ more people than its computer science departments. Providing the necessary customer service via phone, chat, and e-mail, as well as receiving, storing, choosing, packing, and shipping products, required the full participation of the Gemba (the frontline physical location of "value labor"). |
Evaluation of Control Chart and Process Metrics
Complete the following in Excel:
· Calculate the defined process metrics including variation and process capability.
· Develop and display a control chart for the process.
Evaluate the control chart and process metrics using Statistical Process Control (SPC) methods. Determine whether the process could benefit from the use of Six Sigma, Lean, or other tools. (Include all calculation and charts.)
For Amazon, automation needed to be reinvented around a lean philosophy of "autonomy" – keeping the people for the most complex, high-value jobs and using robots to assist them. Rather than doing repetitive, easy tasks, machines can handle them, allowing humans to focus on the more important tasks. By doing this, Amazon's employees are provided with an excellent work environment. The use of autonomation enables humans to complete their tasks safely and without errors by automating routine, low-value tasks. To achieve the perfect 99.996 percent level of effectiveness, it is imperative that a human and a machine work together. A second aspect of standard work enforced by Amazon is the implementation of an efficient sequence and elimination of waste, to maximize the output of a task. The Continuous Improvement philosophy adopted by Amazon aimed to eliminate all non-value-added processes and reduce waste. |
Executive Summary
Write a 700-word executive summary that includes the following:
· A summary of the Process Evaluation (using either Lean or SPC or Six Sigma)
· A summary of the Evaluation of Control Chart and Process metrics based on SPC methods
· A summary of your evaluation of whether the process would benefit from the use of Six Sigma, Lean, or other tools
· A description of the SPC project and recommendations for improvements
With the help of the internet, Amazon has evolved from a retail store to a one-stop shop with a wide range of goods. This technology was not widely available in the 1990s. I think Amazon is the corporation that stood out at the end of the day as the one that did the right thing to implement this new technology to capitalize on its potential. In order to achieve this goal, the "working backwards" method is particularly useful. Identifiying a target and moving backwards through the process to achieve that goal, as described by Amazon, is the process of identifying a target and achieving it. It is very common for companies to write a press release announcing the launch of a new product before any actual work has begun on the product, and this practice is maintained for other products as well. In the department of customer service, the company used the andon-cord model. If a product is having trouble on the internet, the company may remove it until the issue is resolved. Recurring problems can be detected in the returns process. In this case, the customer may be told that the product was sent to the lab for testing, and they can choose to have it replaced or refunded. Otherwise known as "halting the process." Waste doesn't cost customers anything. As discussed recently in an Innovation Excellence piece, Amazon's lean innovation policy prioritizes waste minimization. As a result of the understanding Jeff Bezos, the CEO and founder of Amazon, has incorporated lean principles into many parts of the business, including shipping and returns. No matter how small the improvements are, when they're added up, they add up to a significant gain. Further, Amazon reorganized the stowing of merchandise at its workstations to make the process more efficient. We've always aimed to stow items within a set time frame and with a specific number of frontline employees at fulfillment centers due to the fact that stowing costs about 20% of the budgets. The adoption of lean principles by Amazon makes it possible to pause development when a bug is found and fix it immediately. Amazon is definitely the most effective company at applying lean principles to today's business challenges. Amazon had a tough time stowing the carts because their output was so erratic since stowing a computer screen takes longer. To cut down on stowing times, Kaizen was employed, so that the front-line workers would ask for assistance from the bottom up in order to meet the company's overall bottom-up production objectives. If you want to achieve the best possible results, it is best to mix staff members from various departments, engineers, and a few executives who are willing to ask questions and come up with new ideas. In order for us to fix this problem, these groups have been brought together, so that this is a priority. Kaizen teams should be held to deliver firm-wide benefits over the long-term.sults for the company. Amazon's customer service responded to the cord-on-cord idea. A year later, Bezos joined the system, and the project had been up and running for over a year. A consumer starts the process when they contact customer service regarding a new product they just received. The customer-service agent may remove the item from sale until the problem has been fixed as long as there is a reoccurring issue. In order to restart the production line after this has been resolved, the issue should be fixed first. They were able to detect, monitor, and fix these problems with a high degree of precision after applying detailed methodology. In fact, thousands of faulty items are avoided every year by the andon cord. By empowering the employees on the front line, the andon cord has also improved quality. When customer care representatives are able to end a telephone call, it's a huge mark of trust for them, as they often have little ability to assist consumers over the phone. As a result, the consumers were informed that the goods were being tested in the lab for quality issues before they could be made available to consumers. The cord, however, made it possible for them to do this. There is also the option to offer a refund or a new product to the paying customers. On the company's website, customers can see recalls in real-time as they occur. We have seen the impact of this on our frontline staff and they are now motivated to perform their best for their clients as a result of it. |
Copyright 2020 by University of Phoenix. All rights reserved.
Copyright 2020 by University of Phoenix. All rights reserved.
Collepals.com Plagiarism Free Papers
Are you looking for custom essay writing service or even dissertation writing services? Just request for our write my paper service, and we'll match you with the best essay writer in your subject! With an exceptional team of professional academic experts in a wide range of subjects, we can guarantee you an unrivaled quality of custom-written papers.
Get ZERO PLAGIARISM, HUMAN WRITTEN ESSAYS
Why Hire Collepals.com writers to do your paper?
Quality- We are experienced and have access to ample research materials.
We write plagiarism Free Content
Confidential- We never share or sell your personal information to third parties.
Support-Chat with us today! We are always waiting to answer all your questions.
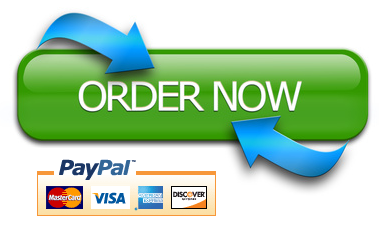