The drug loaded within the bead is the source for mass transfer, whereas the fluid surrounding the bead is the sink for mass transfer. This is
I have a serie of problems due next week but I dont think I can finnish all in time, so i need help with at least two of these problems. They are process problems, some of them already have solution but the task is about making a complete understanding of the problem and the solutions. The main task of each problem are: 1. A quick statment about the problem 2. A quick graphic representation 3. List of the simplification in the problem 4. Math model that represent the problem 5. Solution method 6.Simulation that show the influence of the main variables Some of these are already in the paper but without all the steps. This is not my main language so if I write something wrong or dont explain it correctly let me know.
Ao. The drug loaded
within the bead is the source for mass transfer, whereas the fluid surrounding the bead is the sink for
mass transfer.This is an unsteady-state process, as the source formass transfer is contained within the
diffusion control volume itself.
Consider a limiting case where the resistance to film mass transfer of the drug through the liquid
boundary layer surrounding the capsule surface to the bulk surrounding the fluid is negligible.
Furthermore, assume that the drug is immediately consumed or swept away once it reaches the bulk
solution so that in essence the surrounding fluid is an infinite sink. In this particular limiting case, cAs is equal to zero, so at a long time the entire amount of drug initially loaded into the bead will be
depleted. If radial symmetry is assumed, then the concentration profile is only a function of the r
direction (Figure 27.4).
It is desired to design a spherical capsule for the timed release of the drug dimenhydrinate,
commonly called Dramamine, which is used to treat motion sickness. A conservative total dosage for
one capsule is 10 mg, where 50% of the drug must be released to the body within 3 h. Determine the
size of the bead and the initial concentration of Dramamine in the bead necessary to achieve this
dosage. The diffusion coefficient of Dramamine (species A) in the gel matrix (species B) is 3 � 10�7 cm2/s at a body temperature of 378C. The solubility limit of Dramamine in the gel is 100 mg/cm3, whereas the solubility of Dramamine in water is only 3 mg/cm3.
The model must predict the amount of drug released vs. time, bead diameter, initial concentra-
tion of the drug within the bead, and the diffusion coefficient of the drug within the gel matrix. The
physical system possesses spherical geometry. The development of the differential material balance
model and the assumptions associated with it follow the approach presented in Section 25.4.
One way to deliver a timed dosage of a drug within the human body is to ingest a capsule and allow it to settle in the gastrointestinal system. Once inside the body, the capsule slowly releases the drug by a
diffusion-limited process. A suitable drug carrier is a spherical bead of a nontoxic gelatinous material
that can pass through the gastrointestinal system without disintegrating. A water-soluble drug
(solute A) is uniformly dissolved within the gel and has an initial concentrationC
The general differential equation for mass transfer reduces to the following partial differential
equation for the one-dimensional unsteady-state concentration profile cA(r; t):
@cA @t
¼ DAB @2cA @r2
þ 2 r
@cA @r
� � (27-18)
Key assumptions include radial symmetry, dilute solution of the drug dissolved in the gel matrix, and
no degradation of the drug inside the bead (RA ¼ 0). The boundary conditions at the center (r ¼ 0) and the surface (r ¼ R) of the bead are
r ¼ 0; @cA @r
¼ 0; t � 0 r ¼ R; cA ¼ cAs ¼ 0; t > 0
At the center of the bead, we note the condition of symmetry where the flux NA(0; t) is equal to zero. The initial condition is
t ¼ 0; cA ¼ cAo; 0 � r � R The analytical solution for the unsteady-state concentration profile cA(r; t) is obtained by separation- of-variables technique described earlier. The details of the analytical solution in spherical coordi-
nates are provided by Crank. The result is
Y ¼ cA � cAo cAs � cAo
¼ 1 þ 2R pr
X1 n¼1
ð�1Þn n
sin npr
R
� � e�DABn
2p2t=R2; r 6¼ 0; n ¼ 1; 2; 3; : : : (27-19)
At the center of the spherical bead (r ¼ 0), the concentration is
Y ¼ cA � cAo cAs � cAo
¼ 1 þ 2 X1 n¼1
(� 1)ne�DABn2p2t=R2; r ¼ 0; n ¼ 1; 2; 3; : : : (27-20)
Once the analytical solution for the concentration profile is known, calculations of engineering
interest can be performed, including the rate of drug release and the cumulative amount of drug
release over time. The rate of drug release, WA, is the product of the flux at the surface of the bead
(r ¼ R) and the surface area of the spherical bead
WA(t) ¼ 4pR2NAr ¼ 4pR2 �DAB @cA(R, t)
@r
� � (27-21)
It is not so difficult to differentiate the concentration profile, cA(r; t), with respect to radial coordinate r, set r ¼ R, and then insert back into the above expression for WA(t) to ultimately obtain
WA(t) ¼ 8pRcAoDAB X1 n¼1
e�DABn 2p2t=R2 (27-22)
r = 0
r
cA(r, 0) = cAo
∂cA ∂r
Bulk fluid
cA = 0
NA(R, t)
t = 0
= 0
Drug in gel bead
r = R cA⎯ = 0
r
cA(r, 0) cAo
Bulk fluid
cA = 0
t > 0
∞∞
Figure 27.4 Drug release from a spherical gel bead.
The above equation shows that the rate of drug release will decrease as time increases until all of the
drug initially loaded into the bead is depleted, at which point WA will go to zero. Initially, the drug is
uniformly loaded into the bead. The initial amount of drug loaded in the bead is the product of the
initial concentration and the volume of the spherical bead
mAo ¼ cAoV ¼ cAo 4
3 pR3
The cumulative amount of drug release from the bead over time is the integral of the drug release rate
over time
mAo � mAðtÞ ¼ Zt 0
WA(t) dt
After some effort, the result is
mA(t)
mAo ¼ 6
p2
X1 n¼1
1
n2 e�DABn
2p2t=R2 (27-23)
The analytical solution is expressed as an infinite series summation that converges as ‘‘n’’ goes
to infinity. In practice, convergence to a single numerical value can be attained by carrying the series
summation out to only a few terms, especially if the dimensionless parameter DAB t/R 2 is relatively
large. It is a straightforward task to implement the infinite series summation on a spreadsheet
program such as Excel (Microsoft Corporation).
Table 27.1 Excel spreadsheet for drug�release profile, Example 2 mAo ¼ 10 mg DAB ¼ 3:00E � 07 cm2/s
R ¼ 0:326 cm CAo ¼ 68:9 mg/cm3
Time, t (s) 0.0 18 180 1800 3600 7200 10800 14400 18000 21600
Time, t (h) 0.0 0.005 0.05 0.50 1.00 2.00 3.00 4.00 5.00 6.00
mA(t)/mAo 1 � mA(t)/mAo
1.0 0.964 0.925 0.774 0.689 0.578 0.500 0.439 0.389 0.347
0.0 0.036 0.075 0.226 0.311 0.422 0.500 0.561 0.611 0.653
Series term n ¼ 1 9.99E�01 9.95E�01 9.51E�01 9.05E�01 8.18E�01 7.40E�01 6.70E�01 6.06E�01 5.48E�01 2 2.49E�01 2.45E�01 2.05E�01 1.67E�01 1.12E�01 7.50E�02 5.02E�02 3.36E�02 2.25E�02 3 1.11E�01 1.06E�01 7.08E�02 4.51E�02 1.83E�02 7.41E�03 3.00E�03 1.22E�03 4.94E�04 4 6.20E�02 5.77E�02 2.80E�02 1.26E�02 2.52E�03 5.07E�04 1.02E�04 2.05E�05 4.11E�06 5 3.95E�02 3.53E�02 1.14E�02 3.26E�03 2.66E�04 2.16E�05 1.76E�06 1.44E�07 1.17E�08 6 2.73E�02 2.32E�02 4.57E�03 7.51E�04 2.03E�05 5.49E�07 1.48E�08 4.01E�10 1.08E�11 7 1.99E�02 1.60E�02 1.75E�03 1.50E�04 1.10E�06 8.07E�09 5.92E�11 4.34E�13 3.19E�15 8 1.51E�02 1.13E�02 6.31E�04 2.55E�05 4.15E�08 6.77E�11 1.10E�13 1.80E�16 2.93E�19 9 1.19E�02 8.22E�03 2.13E�04 3.66E�06 1.08E�09 3.21E�13 9.52E�17 2.82E�20 8.36E�24 10 9.51E�03 6.06E�03 6.64E�05 4.41E�07 1.94E�11 8.56E�16 3.77E�20 1.66E�24 7.33E�29 11 7.78E�03 4.50E�03 1.91E�05 4.43E�08 2.38E�13 1.27E�18 6.84E�24 3.67E�29 1.97E�34 12 6.46E�03 3.37E�03 5.07E�06 3.71E�09 1.98E�15 1.06E�21 5.65E�28 3.02E�34 1.61E�40 13 5.44E�03 2.54E�03 1.23E�06 2.57E�10 1.12E�17 4.87E�25 2.12E�32 9.23E�40 4.02E�47 14 4.62E�03 1.91E�03 2.75E�07 1.48E�11 4.29E�20 1.25E�28 3.61E�37 1.05E�45 3.04E�54 15 3.97E�03 1.44E�03 5.59E�08 7.03E�13 1.11E�22 1.76E�32 2.79E�42 4.41E�52 6.98E�62 16 3.44E�03 1.08E�03 1.04E�08 2.76E�14 1.95E�25 1.38E�36 9.72E�48 6.87E�59 4.85E�70 17 2.99E�03 8.12E�04 1.76E�09 8.93E�16 2.30E�28 5.94E�41 1.53E�53 3.95E�66 1.02E�78 18 2.62E�03 6.08E�04 2.71E�10 2.38E�17 1.83E�31 1.41E�45 1.09E�59 8.41E�74 6.48E�88 19 2.31E�03 4.53E�04 3.80E�11 5.22E�19 9.85E�35 1.86E�50 3.50E�66 6.60E�82 1.24E�97 20 2.05E�03 3.36E�04 4.86E�12 9.43E�21 3.56E�38 1.34E�55 5.06E�73 1.91E�90 7.20E�108
A representative spreadsheet solution is provided in Table 27.1. Note that in Table 27.1 the terms
within the series summation rapidly decay to zero after a few terms. The cumulative drug release vs.
time profile is shown in Figure 27.5. The drug-release profile is affected by the dimensionless
parameter DAB t=R 2. If the diffusion coefficient DAB is fixed for a given drug and gel matrix, then the
critical engineering-design parameter we can manipulate is the bead radius R. As R increases, the rate
of drug release decreases; if it is desired to release 50% of Dramamine from a gel bead within 3 h, a
bead radius of 0.326 cm (3.26 mm) is required, as shown in Figure 27.5. Once the bead radius R is
specified, the initial concentration of Dramamine required in the bead can be backed out
cAo ¼ mAo
V ¼ 3mAo
4pR3 ¼ 3ð10 mgÞ
4p(0:326 cm)3 ¼ 68:9 mg
cm3
In summary, a 6.52-mm-diameter bead with an initial concentration of 68:9 mg=cm3 will dose out the required 5 mg of Dramamine within 3 h. The concentration profile along the r direction
at different points in time is provided in Figure 27.6. The concentration profile was calculated by
spreadsheet similar to the format given in Table 27.1. The concentration profile decreases as time
increases and then flattens out to zero after the drug is completely released from the bead.
0.00 0.05 0.10 0.15 0.20 0.25 0.30 0.35
D ru
g c
o n ce
n tr
a tio
n ,
c A (r
, t)
( m
g /c
m 3 )
Radial position, r (cm)
3 h 12 h 24 h
0
20
40
60
80
100
Figure 27.6 Concentration
profile of a 0.326-cm-radius
bead after 3, 12, and 24 h.
0
F ra
ct io
n o
f d ru
g r
e le
a se
d , 1 –
m A (t
)/ m
A O
Time, t (h) 1 2
0.326 cm 0.163 cm
3 4 5 6 0
0.2
0.4
0.6
0.8
1.0
Figure 27.5 Fractional drug
release vs. time profiles.
- Preface
- Contents
- 1: Introduction to Momentum Transfer
- Fluids and the Continuum
- Properties at a Point
- Point-to-Point Variation of Properties in a Fluid
- Units
- Compressibility
- Surface Tension
- 2: Fluid Statics
- Pressure Variation in a Static Fluid
- Uniform Rectilinear Acceleration
- Forces on Submerged Surfaces
- Buoyancy
- Closure
- 3: Description of a Fluid in Motion
- Fundamental Physical Laws
- Fluid-Flow Fields: Lagrangian and Eulerian Representations
- Steady and Unsteady Flows
- Streamlines
- Systems and Control Volumes
- 4: Conservation of Mass: Control-Volume Approach
- Integral Relation
- Specific Forms of the Integral Expression
- Closure
- 5: Newton’s Second Law of Motion: Control-Volume Approach
- Integral Relation for Linear Momentum
- Applications of the Integral Expression for Linear Momentum
- Integral Relation for Moment of Momentum
- Applications to Pumps and Turbines
- Closure
- 6: Conservation of Energy: Control-Volume Approach
- Integral Relation for the Conservation of Energy
- Applications of the Integral Expression
- The Bernoulli Equation
- Closure
- 7: Shear Stress in Laminar Flow
- Newton’s Viscosity Relation
- Non-Newtonian Fluids
- Viscosity
- Shear Stress in Multidimensional Laminar Flows of a Newtonian Fluid
- Closure
- 8: Analysis of a Differential Fluid Element in Laminar Flow
- Fully Developed Laminar Flow in a Circular Conduit of Constant Cross Section
- Laminar Flow of a Newtonian Fluid Down an Inclined-Plane Surface
- Closure
- 9: Differential Equations of Fluid Flow
- The Differential Continuity Equation
- Navier-Stokes Equations
- Bernoulli’s Equation
- Closure
- 10: Inviscid Fluid Flow
- Fluid Rotation at a Point
- The Stream Function
- Inviscid, Irrotational Flow about an Infinite Cylinder
- Irrotational Flow, the Velocity Potential
- Total Head in Irrotational Flow
- Utilization of Potential Flow
- Potential Flow Analysis—Simple Plane Flow Cases
- Potential Flow Analysis—Superposition
- Closure
- 11: Dimensional Analysis and Similitude
- Dimensions
- Dimensional Analysis of Governing Differential Equations
- The Buckingham Method
- Geometric, Kinematic, and Dynamic Similarity
- Model Theory
- Closure
- 12: Viscous Flow
- Reynolds’s Experiment
- Drag
- The Boundary-Layer Concept
- The Boundary-Layer Equations
- Blasius’s Solution for the Laminar Boundary Layer on a Flat Plate
- Flow with a Pressure Gradient
- von Kármán Momentum Integral Analysis
- Description of Turbulence
- Turbulent Shearing Stresses
- The Mixing-Length Hypothesis
- Velocity Distribution from the Mixing-Length Theory
- The Universal Velocity Distribution
- Further Empirical Relations for Turbulent Flow
- The Turbulent Boundary Layer on a Flat Plate
- Factors Affecting the Transition From Laminar to Turbulent Flow
- Closure
- 13: Flow in Closed Conduits
- Dimensional Analysis of Conduit Flow
- Friction Factors for Fully Developed Laminar, Turbulent, and Transition Flow in Circular Conduits
- Friction Factor and Head-Loss Determination for Pipe Flow
- Pipe-Flow Analysis
- Friction Factors for Flow in the Entrance to a Circular Conduit
- Closure
- 14: Fluid Machinery
- Centrifugal Pumps
- Scaling Laws for Pumps and Fans
- Axial and Mixed Flow Pump Configurations
- Turbines
- Closure
- 15: Fundamentals of Heat Transfer
- Conduction
- Thermal Conductivity
- Convection
- Radiation
- Combined Mechanisms of Heat Transfer
- Closure
- 16: Differential Equations of Heat Transfer
- The General Differential Equation for Energy Transfer
- Special Forms of the Differential Energy Equation
- Commonly Encountered Boundary Conditions
- Closure
- 17: Steady-State Conduction
- One-Dimensional Conduction
- One-Dimensional Conduction with Internal Generation of Energy
- Heat Transfer from Extended Surfaces
- Two- and Three-Dimensional Systems
- Closure
- 18: Unsteady-State Conduction
- Analytical Solutions
- Temperature-Time Charts for Simple Geometric Shapes
- Numerical Methods for Transient Conduction Analysis
- An Integral Method for One-Dimensional Unsteady Conduction
- Closure
- 19: Convective Heat Transfer
- Fundamental Considerations in Convective Heat Transfer
- Significant Parameters in Convective Heat Transfer
- Dimensional Analysis of Convective Energy Transfer
- Exact Analysis of the Laminar Boundary Layer
- Approximate Integral Analysis of the Thermal Boundary Layer
- Energy- and Momentum-Transfer Analogies
- Turbulent Flow Considerations
- Closure
- 20: Convective Heat-Transfer Correlations
- Natural Convection
- Forced Convection for Internal Flow
- Forced Convection for External Flow
- Closure
- 21: Boiling and Condensation
- Boiling
- Condensation
- Closure
- 22: Heat-Transfer Equipment
- Types of Heat Exchangers
- Single-Pass Heat-Exchanger Analysis: The Log-Mean Temperature Difference
- Crossflow and Shell-and-Tube Heat-Exchanger Analysis
- The Number-of-Transfer-Units (NTU) Method of Heat-Exchanger Analysis and Design
- Additional Considerations in Heat-Exchanger Design
- Closure
- 23: Radiation Heat Transfer
- Nature of Radiation
- Thermal Radiation
- The Intensity of Radiation
- Planck’s Law of Radiation
- Stefan-Boltzmann Law
- Emissivity and Absorptivity of Solid Surfaces
- Radiant Heat Transfer Between Black Bodies
- Radiant Exchange in Black Enclosures
- Radiant Exchange in Reradiating Surfaces Present
- Radiant Heat Transfer Between Gray Surfaces
- Radiation from Gases
- The Radiation Heat-Transfer Coefficient
- Closure
- 24: Fundamentals of Mass Transfer
- Molecular Mass Transfer
- The Diffusion Coefficient
- Convective Mass Transfer
- Closure
- 25: Differential Equations of Mass Transfer
- The Differential Equation for Mass Transfer
- Special Forms of the Differential Mass-Transfer Equation
- Commonly Encountered Boundary Conditions
- Steps for Modeling Processes Involving Molecular Diffusion
- Closure
- 26: Steady-State Molecular Diffusion
- One-Dimensional Mass Transfer Independent of Chemical Reaction
- One-Dimensional Systems Associated with Chemical Reaction
- Two- and Three-Dimensional Systems
- Simultaneous Momentum, Heat, and Mass Transfer
- Closure
- 27: Unsteady-State Molecular Diffusion
- Unsteady-State Diffusion and Fick’s Second Law
- Transient Diffusion in a Semi-Infinite Medium
- Transient Diffusion in a Finite-Dimensional Medium Under Conditions of Negligible Surface Resistance
- Concentration-Time Charts for Simple Geometric Shapes
- Closure
- 28: Convective Mass Transfer
- Fundamental Considerations in Convective Mass Transfer
- Significant Parameters in Convective Mass Transfer
- Dimensional Analysis of Convective Mass Transfer
- Exact Analysis of the Laminar Concentration Boundary Layer
- Approximate Analysis of the Concentration Boundary Layer
- Mass, Energy, and Momentum-Transfer Analogies
- Models for Convective Mass-Transfer Coefficients
- Closure
- 29: Convective Mass Transfer Between Phases
- Equilibrium
- Two-Resistance Theory
- Closure
- 30: Convective Mass-Transfer Correlations
- Mass Transfer to Plates, Spheres, and Cylinders
- Mass Transfer Involving Flow Through Pipes
- Mass Transfer in Wetted-Wall Columns
- Mass Transfer in Packed and Fluidized Beds
- Gas-Liquid Mass Transfer in Stirred Tanks
- Capacity Coefficients for Packed Towers
- Steps for Modeling Mass-Transfer Processes Involving Convection
- Closure
- 31: Mass-Transfer Equipment
- Types of Mass-Transfer Equipment
- Gas-Liquid Mass-Transfer Operations in Well-Mixed Tanks
- Mass Balances for Continuous Contact Towers: Operating-Line Equations
- Enthalpy Balances for Continuous-Contact Towers
- Mass-Transfer Capacity Coefficients
- Continuous-Contact Equipment Analysis
- Closure
- Nomenclature
- APPENDIXES
- Appendix A: Transformations of the Operators ∇ and ∇2 to Cylindrical Coordinates
- Appendix B: Summary of Differential Vector Operations in Various Coordinate Systems
- Appendix C: Symmetry of the Stress Tensor
- Appendix D: The Viscous Contribution to the Normal Stress
- Appendix E: The Navier–Stokes Equations for Constant ρ and μ in Cartesian, Cylindrical, and Spherical Coordinates
- Appendix F: Charts for Solution of Unsteady Transport Problems
- Appendix G: Properties of the Standard Atmosphere
- Appendix H: Physical Properties of Solids
- Appendix I: Physical Properties of Gases and Liquids
- Appendix J: Mass-Transfer Diffusion Coefficients in Binary Systems
- Appendix K: Lennard–Jones Constants
- Appendix L: The Error Function
- Appendix M: Standard Pipe Sizes
- Appendix N: Standard Tubing Gages
- Author Index
- Subject Index
- TrUe LiAr
,
Chemical Engineering Journal 104 (2004) 35–43
Modeling of counter current moving bed gas-solid reactor used in direct reduction of iron ore
Daniel R. Parisi∗, Miguel A. Laborde Departamento de Ingenier´ıa Quı́mica, Facultad de Ingenier´ıa, Universidad de Buenos Aires, Pabell´on de Industrias,
Ciudad Universitaria, 1428 Buenos Aires, Argentina
Received 11 November 2003; received in revised form 6 August 2004; accepted 9 August 2004
Abstract
In this work, the shaft furnace reactor of the MIDREX® process is simulated. This is a counter current gas-solid reactor, which transforms iron ore pellets into sponge iron.
Simultaneous mass and energy balance along the reactor leads to a set of ordinary differential equation with two points boundary conditions. The iron ore reduction kinetics was modelated with the unreacted shrinking core model. Solving the ODE system allows to know the c
tion ( e used for d ©
K
1
g t f n o f
w [ a m v p
m
dy- lance dy-
tor same nking
but
ctor d the oth
. c- he nsfer con- olid is tive
1 d
oncentration and temperature profiles of all species within the reactor. The model was able to satisfactorily reproduce the data of two MIDREX® plants: Siderca (ARGENTINA) and Gilmore Steel Corpora
U.S.A.). Also, it was used to explore the performance of the reactor under different operating conditions. This capacity could b esign and control purpose. 2004 Elsevier B.V. All rights reserved.
eywords: Shaft furnace simulation; Gas-solid reactor; Moving bed; Direct reduction.
. Introduction
Direct reduction of iron ore is today’s major process for enerating metallic iron, necessary in the iron and steel indus-
ry. World production of direct reduce iron (DRI) has grown rom near zero in 1970 to 45.1 Mt in 2002. MIDREX® Tech- ology is the most important one, responsible for the 66.6% f the world total DRI production. Its main reactor (the shaft
urnace) is a moving bed reactor. The first studies related to moving bed solid-gas reactors
ere performed by Munro and Amundson[1], Amundson 2] and Siegmund et al.[3]. In these works, the authors used linear function of the solid temperature in order to approxi- ate the reaction rate and to obtain analytical solutions. The
alidity of this solution is limited to a narrow range of tem- eratures.
∗ Corresponding author. Tel.: +54 11 4576 3240; fax: +54 11 4576 3241. E-mail addresses:[email protected] (D.R. Parisi),
[email protected] (M.A. Laborde).
Schaefer et al.[4] studied the heat generation in a stea state reactor. They used a step function for the heat ba and the results show the existence of multiplicity of stea states.
Yoon et al.[5] developed a model for a Lurgi type reac used in the carbon gasification. They considered the temperature in both phases (solid and gas) and the shri unreacted core model for the solid particle.
Amundson and Arri[6] analyzed the same system considering different temperatures in both phases.
Arce et al.[7] studied a countercurrent moving bed rea using a heterogeneous model for the reactor design an shrinking core model for the solid particle. They applied b models to an irreversible first order exothermic reaction
Rao and Pichestapong[8] developed a model for a rea tor in which the reduction of iron mineral is carried out. T model considers that the controlling step is the mass tra of the gaseous reactants in the product solid layer. The centration of the gaseous species on the interface gas-s that of the equilibrium and it was evaluated using an itera
385-8947/$ – see front matter © 2004 Elsevier B.V. All rights reserved. oi:10.1016/j.cej.2004.08.001
36 D.R. Parisi, M.A. Laborde / Chemical Engineering Journal 104 (2004) 35–43
Nomenclature
Ap pellet external area (cm 2)
C reactor gas concentration (mol/cm3) D effective diffusion coefficient (cm2/s) Gm molar flow (mol/cm
2 s) H reaction enthalpy (cal/mol) h global heat transfer coefficient (pellets/gas)
(cal/s/cm2/K) k kinetics constant of the surface reaction (cm/s) kg external mass transfer coefficient (cm/s) L reduction zone length (cm) Mw molecular weight np number of pellets per unit volume (1/cm
3) R reaction rate (mol/cm3s) R̂ reaction rate per pellet (mol/s) r0 external radius of the pellet (cm) rc radius of the unreacted core (cm) T temperature (◦C) u gas velocity (cm/s) X extent of reaction/extent of reactant conversion
(mol/cm3) z space variable inside the reactor (cm)
Subscripts atm atmosphere i ith reaction in reactor inlet j jth reactant (gas or solid) n gaseous reactant rs reactive solid (Fe2O3) ps product solid (Fe) sol solid g gas
Greek letters α stoichiometric coefficient ρ density of the solid reactant (g/cm3)
method. As a consequence, the problem cannot be solved in terms of differential equations system. In this paper, the heat balance is avoided since the authors assumed a linear function of the temperature with the reactor length.
The aim of this work is to model and simulate a solid-gas countercurrent moving bed reactor in which the reduction of iron ore pellets is performed using CO and H2 as reducing gases.
In order to do that, mass and energy balance are taken into account simultaneously. This leads to a set of ordinary differential equation with two point boundary conditions.
The model is validated with data from two industrial plants. Also, it is used to explore the performance of the reactor under different operating conditions.
Fig. 1. Shaft furnace geometry.
1.1. Shaft furnace of the MIDREX® process
The main function of the shaft furnace is to generate sponge iron from iron ore. The solids flow downwards by gravity and the reducing gases flow upwards in counter cur- rent, while the corresponding chemical transformations oc- cur. Fig. 1 shows a scheme of the reactor.
As it can be observed, the furnace consists of a vertical cylindrical container, with a conic lower zone. The inner wall is covered with insulating materials resistant to erosion.
The reducing gases enter by the middle zone of the reactor through the bustle, which consists of a channel with approx- imately 70 nozzles that direct the gas towards the center of the solid bed.
Immediately underneath, the upper burdenfeeders are lo- cated. Following in descendent order one can found: the wind boxes (which take the cooling gas that circulates around the lower conical zone of the reactor), cooling gas distrib- utor or (“inverted Christmas tree”), which besides to inject cooling gases has the function to support most of the bed weight.
Gases going out from the shaft furnace are recycled into another reactor: the Reformer. This is a fixed bed catalytic reactor, which transforms the process gas (with addition of natural gas) into reducing gas again.
2
l- l
nre- ade
( film ith
. The model
In order to model the MIDREX® shaft furnace, the fo owing approximations are considered:
(a) The iron ore pellet consumption is governed by the u acted shrinking core model. This aproximation was m by several authors, see for instance[8,9].
b) Mass and heat transfer resistances through the around the solid particle are negligible comparing w
D.R. Parisi, M.A. Laborde / Chemical Engineering Journal 104 (2004) 35–43 37
diffusional resistance inside the porous solid (kg � D/2/r0).
(c) Only steady-state operating conditions will be consid- ered.
(d) Plug flow is assumed for gas and solid phase.
Due to high gas flow rate in the reactor, turbulence regime is reached. Under this situation, inertial effects are predom- inanant. So it will not be considered neither axial nor radial dispersion[10].
For the solid phase this hypothesis was verified through a previous work[11]. Distinct element method simulations (DEM) were performed in order to study the granular bed dynamics of a typical MIDREX® shaft furnace.
Only the global direct reduction reactions are taken into account. The area of interest
Collepals.com Plagiarism Free Papers
Are you looking for custom essay writing service or even dissertation writing services? Just request for our write my paper service, and we'll match you with the best essay writer in your subject! With an exceptional team of professional academic experts in a wide range of subjects, we can guarantee you an unrivaled quality of custom-written papers.
Get ZERO PLAGIARISM, HUMAN WRITTEN ESSAYS
Why Hire Collepals.com writers to do your paper?
Quality- We are experienced and have access to ample research materials.
We write plagiarism Free Content
Confidential- We never share or sell your personal information to third parties.
Support-Chat with us today! We are always waiting to answer all your questions.
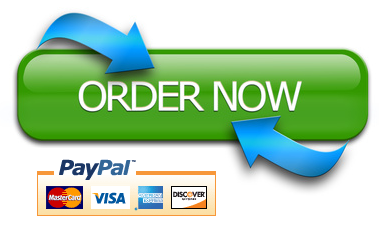