Write a 3.5-page to 4.5-page paper that highlights your reflections about relevant operations lessons from the Boeing tour a
Write a 3.5-page to 4.5-page paper that highlights your reflections about relevant operations lessons from the Boeing tour and our course time studying Lean. The paper should address what you observed and learned at Boeing, and tie that to what you read in All I Need to Know About Manufacturing I Learned in Joe’s Garage, what we discussed in class and you read in the course textbook and other readings regarding Lean concepts, and your experience in the various in-class simulations pertaining to Lean. The paper should not merely report what happened but should display critical thinking and personal insight.
here's some more details:
Lean Reflection Paper(10%). Each student will write a 4-page paper that highlights his/her reflections about relevant operations lessons from the Boeing tour and our course time studying Lean. The paper should address what you observed and learned at Boeing, and tie that to what you read in All I Need to Know About Manufacturing I Learned in Joe’s Garage, what we discussed in class and you read in the course textbook and other readings regarding Lean concepts, and your experience in the various in-class simulations pertaining to Lean. The paper should not merely report what happened but should display critical thinking and personal insight. Additional details for this assignment will be posted on Canvas.
NOTE:THE ATTACHED video shows you what I similarly experience in Boeing tour but please do not mention anything about Toyota
VIDEO: https://youtu.be/k4-eJsFdxaU
Operations and Project Management ELCBUS 340 16 April 2018
1
Today’s Agenda
Class Administration – Littlefield Launch, Team Projects
Quality
Types of Variation
Control Charting
Process Capability Ratio (Cp)
Process Capability Index (Cpk)
Statistical Process Control
Continuous
Discrete
Process Capability Studies
2
50,000 Feet Overview of OPM
Managing Processes
Process Strategy
Process Performance & Quality
Constraint Management
Process Layout
Lean Systems
Process Analysis
Using Operations to Compete
Operations As a
Competitive Weapon
Operations Strategy
Project Management
Managing Value Chains
Supply Chain Strategy
Inventory Management
Location
Forecasting
Sales & Operations Planning
Scheduling
Resource Planning
Process Analysis
3
Service vs. Manufacturing
Small vs. Medium vs. Large Firms
Industry type: hightech, healthcare, aerospace, IT, etc ….
Quality
A term used by customers to describe their general satisfaction with a service or product.
Costs of Quality
Four major categories:
Prevention Costs
Appraisal Costs
Internal Failure Costs
External Failure Costs
Many companies spend significant time, effort, and expense on systems, training, and organizational changes to improve quality and performance of their processes. It is estimated that COQ ranges from 20 to 30 percent of gross sales.
Costs of Quality
Prevention Costs are associated with preventing defects before they happen
Appraisal Costs are incurred when a firm assesses the level of performance of its processes
Internal Failure Costs result from defects that are discovered during the production of a service or product
External Failure Costs arise when a defect is discovered after the customer receives the product or service
Ethical Failure Costs are the societal and monetary costs associated with passing defective services or products to customers
TQM & Six Sigma
What is Total Quality Management?
Total Quality Management (TQM)
Is a quality strategy that focuses on achieving high levels of process performance and quality by stressing three principles:
Customer Satisfaction
Employee Involvement
Continuous Improvement
Customer Satisfaction
Conformance to Specifications
Value
Fitness for Use
Support
Psychological Impressions
Total Quality Management
Principles
Customer satisfaction (internal or external): when customers’ expectations have been met or exceeded.
Conformance to specifications
It is the processes that produced the service or product that are really being judged.
Specifications may relate to consistent quality, on-time delivery, or delivery speed.
Value
How well the service or product serves its intended purpose at a price customers are willing to pay.
Fitness for use: customer may consider the convenience of a service or the mechanical features of a product.
Support: the service or product support may be as important to the customer as the service or product itself.
Psychological impressions: atmosphere, image, or aesthetics
9
Employee Involvement
Cultural Change
Quality at the Source
Teams
Employee Empowerment
Problem-solving teams
Special-purpose teams
Self-managed teams
Total Quality Management
Principles
Employee involvement
Cultural change
Challenge is to define customer for each employee
External customers buy the service or product.
Internal customers are employees in the firm who rely on output of other employees. An assembly line is a chain of internal customer-supplier relationships, with an external customer purchasing the finished goods.
Top management must motivate cultural change.
Everyone is expected to contribute and share the view that quality control is an end to itself
Quality at the source
Teams
Employee involvement is a key tactic for improving processes and quality
Small groups of people
Common purpose.
Set their own performance goals and approaches
Hold themselves accountable for success
Three employee-empowerment approaches to teamwork
Problem-solving teams (also called quality circles)
Special-purpose teams
Self-managing teams, the highest level of worker participation
10
Continuous Improvement
Kaizen
Problem-solving tools
Plan-Do-Study-Act Cycle
Total Quality Management
Principles
Based on the Japanese concept, kaizen
The philosophy of continually seeking ways to improve processes.
Not unique to quality. Applies to process improvement as well.
Getting started
SPC training
Make SPC a normal aspect of daily operations.
Build work teams and employee involvement.
Utilize problem-solving tools within the work teams.
Develop operator ownership in the process.
11
Plan-Do-Study-Act Cycle
Total Quality Management
Principles
Problem-solving process: The Deming Wheel
Plan—select a process needing improvement, document process, analyze data, set improvement goals, discuss alternatives, assess benefits and costs, develop a plan and improvement measures.
Do—implement plan, monitor improvements.
Study—analyze data to evaluate effectiveness of the plan.
Act—document and disseminate improved process as a standard procedure.
12
What is Six Sigma?
Six Sigma
A comprehensive and flexible system for achieving, sustaining, and maximizing business success by minimizing defects and reducing variation in processes.
Six Sigma Project Frameworks
DMAIC
DFSS (Define for Six Sigma)
DMADV
IDOV
DMAIC
5 – 15
Control
An improvement system for existing processes falling below specification and looking for incremental improvement
Define
Measure
Analyze
Improve
DMADV
Verify
An improvement system used to develop new processes or products at Six Sigma quality levels
Define
Measure
Analyze
Design
IDOV
Used for designing a completely new product or business process to meet customer needs and specifications or to achieve Six Sigma quality levels
Identify
Design
Optimize
Verify
The Tools
Six Sigma Tools
[Introduce the Tools]
Standard Work
The best combination of machines and people working together to produce a product or service at a particular point in time.
5S
5S is a workplace organization method used to assure work can be done effectively and efficiently.
SIPOC
SIPOC is a tool that summarizes the inputs, outputs and steps of one or more processes in table form.
RACI
RACI is a method to identify the roles and responsibilities of participants in a cross organizational team.
5Ys
Statistics
Waste
Worker Realignment
Workplace Reorganization
DIG
CAPA
Affinity
Fishbone
Setup Reduction
Visual Controls
Small Lots
Kanban
A3
1-Piece Flow
SPC
Kaizen
Cycle Time Reduction
TPM
FMEA
DOE
Project Management
Reengineering
Six Sigma Project
Balanced Scorecard
QFD
Hoshin Planning
VOC
18
Six Sigma Certifications
Master Black Belt
Black Belt
Green Belt
Yellow Belt
Certifying Organizations?
Acceptance Sampling
Acceptance Sampling
The application of statistical techniques to determine if a quantity of material from a supplier should be accepted or rejected based on the inspection or test of one or more samples.
Acceptable Quality Level
The quality level desired by the consumer.
Acceptance Sampling
Acceptance Sampling
Firm A uses TQM or Six Sigma to achieve internal process performance
Supplier uses TQM or Six Sigma to achieve internal process performance
Yes
No
Yes
No
Fan motors
Fan blades
Accept blades?
Supplier
Manufactures fan blades
TARGET: Firm A’s specs
Accept motors?
Motor sampling
Blade sampling
Firm A
Manufacturers furnace fan motors
TARGET: Buyer’s specs
Buyer
Manufactures furnaces
Six Sigma Approach
X
X
X
X
X
X
X
X
X
X
X
X
X
X
X
X
X
Process average OK; too much variation
Process variability OK; process off target
Process on target with low variability
Reduce spread
Center process
X
X
X
X
X
X
X
X
X
Statistical Process Control
Statistical Process Control (SPC)
SPC
The application of statistical techniques to determine whether a process is delivering what the customer wants.
Performance Measurements
Variables (Continuous) – Characteristics that can be measured.
Attributes (Discrete) – Characteristics that can be counted.
Statistical Process Control (SPC)
A process that is in statistical control:
Is stable and predictable
Variation will be limited to an expected range
But still may not be capable
A process that is out of statistical control:
Is unstable and unpredictable
Variation will not be limited to the expected range
Variation may be extreme
Types of Variation
Common cause
Variation that is random, unidentifiable and unavoidable
Special cause
Variation that can be identified and eliminated
Effects of Special Cause Variation on the Process Distribution
Control Charts
Time-ordered diagram used to determine whether observed variations are abnormal
Control Charting
A control chart always has a central line for the average, an upper line for the upper control limit and a lower line for the lower control limit.
By comparing current data to these lines, one can make conclusions about whether the process variation is in control or out of control (special cause variation)
Variable data control charts use two charts with attribute data using one chart
[Explain]
Describe the anatomy of a control chart – use the bullets as a guideline for your explanation.
[Draw this on the Board]
[Insert graphic from supplemental PPT, slide 7]
Remember the Galton box?
If you turn the SPC on its end and shook all of the points to the bottom, you would be a Probability Density Function (PDF) that would appear to be a normal distribution.
[Next Slide]
Control charting process
29
Types of Control Charts
Variable Data Control Charts
X-bar Chart – Measures whether the process is generating output consistent with a target value.
R Chart – Measures the variability of the process.
S Chart – Measures the Standard Deviation of the process.
Attribute Data Control Charts
p-chart – Measures the proportion of defective services of products in a process.
c-chart – Measures the proportion of defects in one service or product.
Continuous Control Charts Charts R Charts S Charts
[Explain]
Describe the anatomy of a control chart – use the bullets as a guideline for your explanation.
[Draw this on the Board]
[Insert graphic from supplemental PPT, slide 7]
Remember the Galton box?
If you turn the SPC on its end and shook all of the points to the bottom, you would be a Probability Density Function (PDF) that would appear to be a normal distribution.
[Next Slide]
Control charting process
31
– Chart
Data are collected in a face-and-plunge operation done on a lathe. The dimension being measured is the groove inside diameter (ID), which has a tolerance of 7.125 ± 0.010. Four parts are measured every hour. These values have been entered in the table below.
Chart Control Limits
=
=
Where:
= the central line of the chart
= a constant to provide three-sigma limits for the sample mean
Calculating Control Chart Factors
Chart Control Limits
=
=
Plot data over time
Centerline =
Upper and Lower Control Limits
LCL
UCL
=
=
Where:
= average of several R values and the central line of the R control chart
, = constants that provide three standard deviation limits for the given sample size
R-Chart
Control Limits
Calculating Control Chart Factors
R-Chart
Control Limits
=
= 2.282(0.0037) = 0.008443
=
= 0(0.0037) = 0
Plot the Range of each subgroup overtime, the calculated value is the centerline.
R-Chart
Variation and out of control data points
Common Cause Variation
Out-of-control point (Special Cause)
Time plot of sequential process measurements
Sample Number | 1 | 2 | 3 | 4 | 5 | ||
1 | 0.5014 | 0.5022 | 0.5009 | 0.5027 | 0.5045 | ||
2 | 0.5021 | 0.5041 | 0.5024 | 0.5020 | 0.5062 | ||
3 | 0.5018 | 0.5026 | 0.5035 | 0.5023 | 0.5054 | ||
4 | 0.5008 | 0.5034 | 0.5024 | 0.5015 | 0.5047 | ||
5 | 0.5041 | 0.5056 | 0.5034 | 0.5047 | 0.5043 | ||
0.50204 | 0.50358 | 0.50252 | 0.50264 | 0.50502 | 0.50316 | ||
R | 0.0033 | 0.0034 | 0.0026 | 0.0032 | 0.0019 | 0.00288 |
Example
The management of West Allis Industries is concerned about the production of a special metal screw used by several of the company’s largest customers. The diameter of the screw is critical to the customers. Data from five samples appear in the accompanying table. The sample size is 5. Is the process in statistical control?
=
0.5032 + 0.577(0.0029) = 0.5048
=
0.5032 – 0.577(0.0029) = 0.5015
Example
Compute the mean for each sample and the control limits.
Process average is NOT in statistical control.
Example
05- 46
Compute the range for each sample and the control limits
= = 2.114(0.0029) = 0.0061
= = 0(0.0029) = 0
Example
Process variability is in statistical control.
Example
=
=
Where:
= average of several Stdev values and the central line of the S control chart
, = constants that provide three standard deviation limits for the given sample size
S-Chart
Control Limits
S – Chart
Subgroup | Obs 1 | Obs 2 | Obs 3 | Obs 4 | Obs 5 | Obs 6 | Obs 7 | Obs 8 | Obs 9 | Obs 10 | |
1 | 46.8204 | 58.8572 | 67.7175 | 51.3078 | 53.3025 | 51.3258 | 59.0268 | 49.9933 | 47.086 | 60.4783 | |
2 | 53.9847 | 47.4005 | 59.1598 | 57.2251 | 57.3207 | 50.4045 | 54.8046 | 55.7574 | 58.8662 | 59.2083 | |
3 | 52.4315 | 63.2146 | 61.4096 | 59.342 | 57.4605 | 53.7083 | 57.0489 | 58.4325 | 48.5544 | 61.4105 | |
4 | 50.9712 | 53.4314 | 52.9449 | 66.827 | 43.9849 | 67.8154 | 57.4312 | 44.3194 | 60.5493 | 59.6383 | |
5 | 62.0421 | 57.1784 | 60.1955 | 56.4687 | 64.9641 | 52.9195 | 48.6739 | 56.3773 | 60.3216 | 58.9171 | |
6 | 53.1269 | 58.374 | 63.7938 | 50.8965 | 52.4253 | 52.696 | 64.2078 | 65.9364 | 55.8426 | 54.478 | |
7 | 55.0507 | 53.8931 | 51.8424 | 68.7073 | 50.173 | 58.0991 | 59.3456 | 57.9232 | 69.2396 | 60.2033 | |
8 | 54.3315 | 52.3679 | 65.2346 | 62.6795 | 61.5929 | 54.0084 | 61.4465 | 58.4423 | 55.7608 | 54.1888 | |
9 | 59.9584 | 59.1762 | 51.5629 | 63.0753 | 59.4856 | 63.2215 | 50.8982 | 62.4343 | 49.4303 | 48.9902 | |
10 | 54.0402 | 56.3253 | 53.3773 | 54.7368 | 59.8292 | 54.6631 | 62.2161 | 61.5533 | 66.2283 | 63.0929 | |
11 | 57.2273 | 65.8816 | 67.9839 | 51.7812 | 63.3054 | 56.5156 | 54.5318 | 54.4049 | 54.6459 | 52.6297 | |
12 | 51.5133 | 61.0216 | 61.2776 | 62.1072 | 56.1983 | 54.805 | 59.083 | 58.8301 | 51.2939 | 54.9033 | |
13 | 41.6784 | 46.7246 | 90.9593 | 57.7698 | 57.6619 | 53.9903 | 47.1248 | 50.2183 | 52.0052 | 57.2942 | |
14 | 52.8303 | 42.4179 | 58.0054 | 60.1385 | 59.9954 | 60.5936 | 49.6827 | 68.2645 | 53.5693 | 60.6435 | |
15 | 58.1128 | 53.4343 | 49.8567 | 53.3065 | 48.6588 | 53.4726 | 61.1457 | 61.6733 | 54.4246 | 51.8054 | |
16 | 59.4674 | 66.2816 | 71.1186 | 63.6602 | 65.4012 | 53.2372 | 55.0633 | 46.6954 | 57.0477 | 61.8819 | |
17 | 63.6288 | 47.3453 | 45.6509 | 40.2198 | 51.7382 | 51.0804 | 56.4197 | 57.7979 | 65.3047 | 66.539 | |
18 | 59.5853 | 50.9825 | 56.2445 | 103.441 | 52.6224 | 63.7297 | 43.3771 | 58.7982 | 59.8339 | 57.9202 | |
19 | 57.8042 | 49.2275 | 56.9069 | 55.4057 | 60.342 | 62.0972 | 57.2 | 38.6509 | 61.459 | 59.144 | |
20 | 53.2788 | 62.1238 | 48.7058 | 58.0984 | 52.3153 | 56.8277 | 53.3615 | 64.6894 | 56.0133 | 56.9455 | |
21 | 61.0891 | 52.2114 | 55.0061 | 50.2427 | 55.6495 | 53.7419 | 63.6856 | 56.5452 | 55.6084 | 67.2915 | |
22 | 47.6385 | 62.0744 | 71.2102 | 64.6661 | 58.1218 | 56.8151 | 62.913 | 53.8949 | 64.6937 | 53.5819 | |
23 | 46.1471 | 57.2321 | 60.0446 | 59.5476 | 54.4676 | 48.8446 | 57.6602 | 58.5467 | 65.4449 | 50.6271 | |
24 | 53.1199 | 52.4063 | 53.1227 | 52.1897 | 56.6952 | 53.0823 | 61.1469 | 50.5565 | 56.9315 | 60.0423 | |
25 | 55.3156 | 60.7648 | 55.0855 | 56.2381 | 60.3981 | 61.7266 | 69.0841 | 51.4446 | 58.1248 | 50.136 | |
54.44778 | 55.61393 | 59.53668 | 59.20314 | 56.56439 | 55.97686 | 57.06316 | 56.08721 | 57.5312 | 57.67965 | 56.9704 | |
Stdev | 5.286458 | 6.28949 | 9.49476 | 11.10656 | 5.147585 | 4.750668 | 5.9335 | 6.835565 | 5.76572 | 4.830527 | 6.544084 |
Calculating Control Chart Factors
Chart Control Limits when using large sample sizes (S Chart)
=
=
S-Chart
Control Limits
=
= 1.436(6.5441) = 9.3973
=
= 0.564(6.5441) = 3.6909
56.970398800000012 56.970398800000012 56.970398800000012 56.970398800000012 56.97039880000001 2 56.970398800000012 56.970398800000012 56.970398800000012 56.970398800000012 56.970398800000012
53.002844821727074 53.002844821727074 53.002844821727074 53.002844821727074 53.002844821727074 53.002844821727074 53.002844821727074 53.002844821727074 53.002844821727074 53.002844821727074
60.937952778272951 60.937952778272951 60.937952778272951 60.937952778272951 60.937952778272951 60.937952778272951 60.937952778272951 60.937952778272951 60.937952778272951 60.937952778272951
X-Bar: Stacked Data (Y)
5.2864584810532644 6.2894901987177159 9.4947599494406294 11.106561756232184 5.1475848615248676 4.7506682219522194 5.9335003652986451 6.8355648020676014 5.7657197453628175 4.8305269359839684
6.5440835317633903 6.5440835317633903 6.5440835317633903 6.5440835317633903 6.5440835317633903 6.5440835317633903 6.5440835317633903 6.5440835317633903 6.5440835317633903 6.5440835317633903
3.6959524205845296 3.6959524205845296 3.6959524205845296 3.6959524205845296 3.6959524205845296 3.6959524205845296 3.6959524205845296 3.6959524205845296 3.6959524205845296 3.6959524205845296
9.3922146429422515 9.3922146429422515 9.3922146429422515 9.3922146429422515 9.3922146429422515 9.3922146429422515 9.3922146429422515 9.3922146429422515 9.392214642942251 5 9.3922146429422515
S: Stacked Data (Y)
Control Chart Evaluation
Control Chart Rules
Rule Name | Out of Control Condition | Chart Type | |
Variables | Attributes | ||
Beyond Limits | One or more points beyond the control limits | X | X |
Zone C | 9 or more consecutive points on one side of the average (in Zone C or beyond) | X | X |
Trend | 7 consecutive points trending up or trending down | X | X |
Over-control | 14 consecutive points alternating up and down | X | X |
Zone A | 2 out of 3 consecutive points in Zone A or beyond | X | |
Zone B | 4 out of 5 consecutive points in Zone B or beyond | X | |
Stratification | 15 consecutive points in Zone C | X | |
Mixture | 8 consecutive points with no points in Zone C | X |
Discrete Control Charts c-charts np-charts
56
Control Charts for Attributes Data c-chart
c-charts count the number of defects per unit of service encounter
The underlying distribution is the Poisson distribution
The mean of the distribution is and the standard deviation is .
c-chart example
The Woodland Paper Company produces paper for the newspaper industry. As a final step in the process, the paper passes through a machine that measures various product quality characteristics. When the paper production process is in control, it averages 20 defects per roll.
a. Set up a control chart for the number of defects per roll. For this example, use two-sigma control limits.
b. Five rolls had the following number of defects: 16, 21, 17, 22, and 24, respectively. The sixth roll, using pulp from a different supplier, had 5 defects. Is the paper production process in control?
a. The average number of defects per roll is 20. Therefore:
c-chart example
Example 5.4
The process is out of control due to Sample 6.
c-chart example
However, sample 6 is from a new supplier and results in a better product.
20 20 20 20 20 20
11.06 11.06 11.06 11.06 11.06 11.06
28.94 28.94 28.94 28.94 28.94 28.94
C – Defects
np-chart
np-charts are used to control the proportion defective
Sampling involves yes/no decisions so the underlying distribution is the binomial distribution
np-chart
np-chart example
A Test was conducted to determine the presence of the Rh factor in 13 samples of donated blood. The results of the test are given in the table on the next slide.
Using three-sigma control limits, is the accuracy of the blood testing process in statistical control?
np-chart example
Example 5.3
189
1614
= = 0.1171
p =
Total defectives
Total number of observations
Calculate the sample proportion defective and plot each sample proportion defective on the chart.
np-chart example
np-chart example
np-chart example
The process is in statistical control.
Control Chart Evaluation
Control Chart Rules
Rule Name | Out of Control Condition | Chart Type | |
Variables | Attributes | ||
Beyond Limits | One or more points beyond the control limits | X | X |
Zone C | 9 or more consecutive points on one side of the average (in Zone C or beyond) | X | X |
Trend | 7 consecutive points trending up or trending down | X | X |
Over-control | 14 consecutive points alternating up and down | X | X |
Zone A | 2 out of 3 consecutive points in Zone A or beyond | X | |
Zone B | 4 out of 5 consecutive points in Zone B or beyond | X | |
Stratification | 15 consecutive points in Zone C | X | |
Mixture | 8 consecutive points with no points in Zone C | X |
Continuous
Discrete
n = 1 n = 2 to 9 n = 10+
I-MR
chart
Xbar-R chart
Xbar-S chart
Defects
Defectives
Yes No
c chart
u chart
Yes
Collepals.com Plagiarism Free Papers
Are you looking for custom essay writing service or even dissertation writing services? Just request for our write my paper service, and we'll match you with the best essay writer in your subject! With an exceptional team of professional academic experts in a wide range of subjects, we can guarantee you an unrivaled quality of custom-written papers.
Get ZERO PLAGIARISM, HUMAN WRITTEN ESSAYS
Why Hire Collepals.com writers to do your paper?
Quality- We are experienced and have access to ample research materials.
We write plagiarism Free Content
Confidential- We never share or sell your personal information to third parties.
Support-Chat with us today! We are always waiting to answer all your questions.
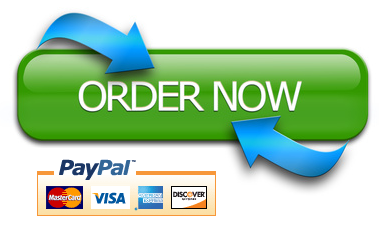
All Rights Reserved Terms and Conditions
College pals.com Privacy Policy 2010-2018